- お役立ち記事
- How to proceed with material procurement and efficiency using MRP that the production planning department should practice
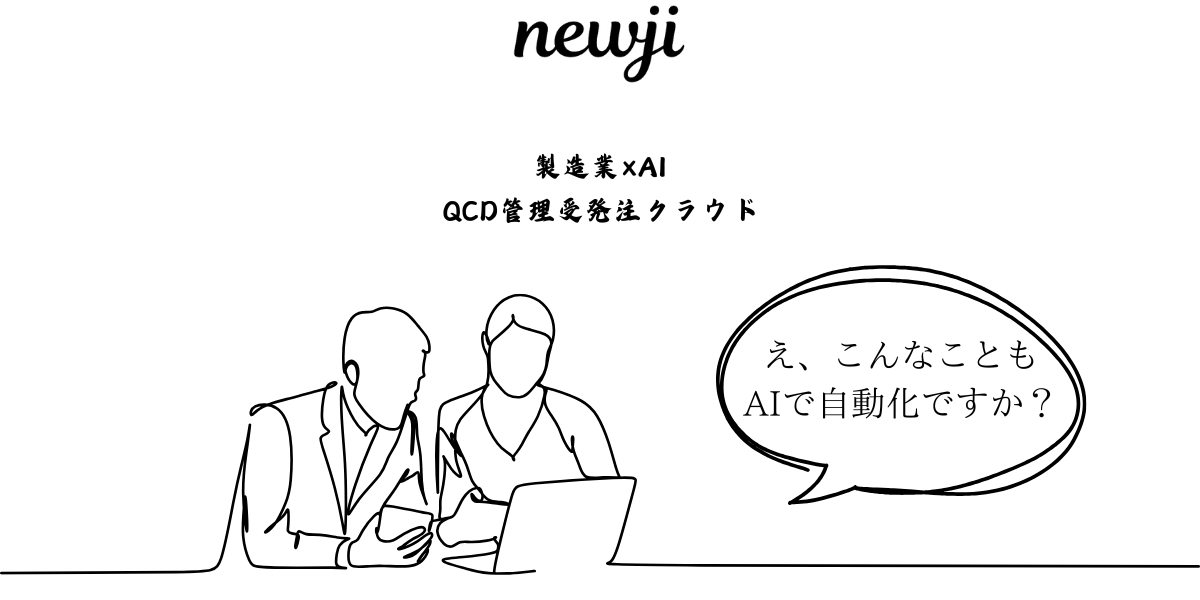
How to proceed with material procurement and efficiency using MRP that the production planning department should practice
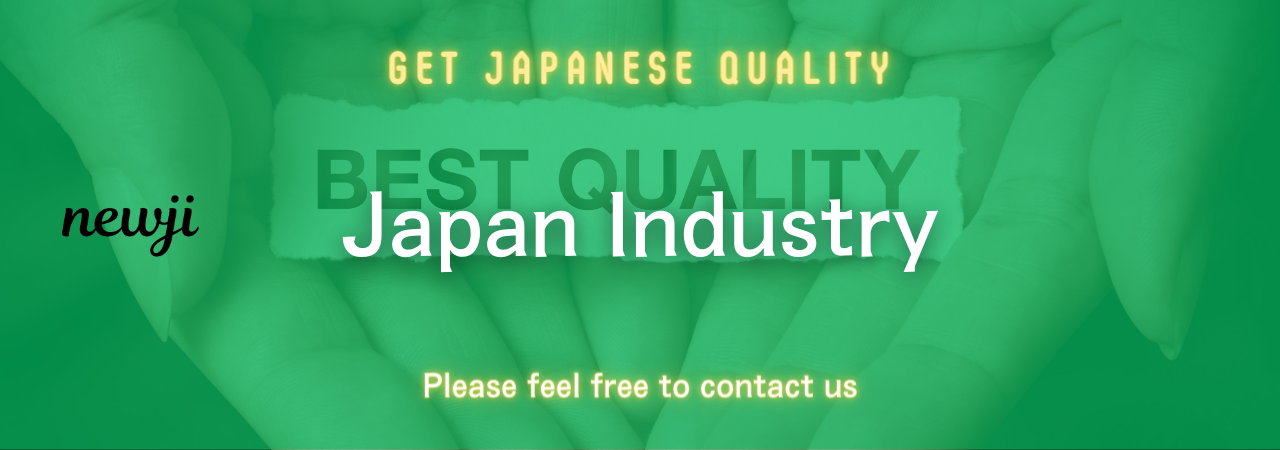
目次
Understanding MRP: A Key to Efficient Material Procurement
Material Requirements Planning, commonly known as MRP, is a crucial part of the production planning process.
It is essential for the production planning department to understand how to proceed with material procurement using MRP to enhance overall efficiency.
MRP helps determine what materials are needed, in what quantities, and at what time, ensuring a smooth production process.
MRP operates through a systematic approach.
It uses data from inventory records, the master production schedule, and the bill of materials to calculate the quantities of each component needed for production.
By doing so, it helps in reducing excess inventory and minimizing shortages.
The Components of MRP
To effectively utilize MRP, it’s important to grasp its core components:
1. **Inventory Records**: This component tracks the status of the current inventory, including information on materials already available, expected receipts, and supplier lead times.
2. **Master Production Schedule (MPS)**: This outlines the production plan and indicates the quantity of each product to be produced and the timeline for their completion.
3. **Bill of Materials (BOM)**: A detailed list of raw materials, parts, and sub-assemblies required to produce a product.
It provides the relationship between finished goods and the components needed to create them.
Steps in Implementing MRP for Material Procurement
Implementing MRP for efficient material procurement involves several steps:
Step 1: Data Collection and Input
The first step involves collecting accurate data about inventory levels, customer orders, and production schedules.
This data serves as the foundation for MRP calculations.
It’s important to ensure the data is up-to-date and accurate to prevent discrepancies in material planning.
Step 2: Bill of Materials (BOM) Analysis
Analyzing the BOM is critical, as it lists all the components required to manufacture a product.
This step helps identify what materials need to be procured and the sequence in which they are needed.
Step 3: Master Production Schedule Development
Develop a Master Production Schedule that aligns with the demand forecast.
The MPS should carefully outline production schedules to ensure timely product delivery.
This step aids in determining the right quantities and timing for material procurement.
Step 4: MRP Calculation
The MRP system processes the data from the inventory records, BOM, and MPS to calculate the net requirements for each material.
This calculation considers existing inventory and scheduled receipts to determine the exact quantities needed.
Step 5: Procurement and Ordering
Based on the MRP calculations, the procurement team can generate purchase orders for materials.
Ensuring timely communication and collaboration with suppliers is critical in this step for timely material delivery.
Benefits of MRP in Material Procurement Efficiency
Using MRP in material procurement offers numerous benefits:
Improved Inventory Management
One of the most significant advantages of MRP is improved inventory management.
By accurately forecasting material requirements, companies can maintain optimal inventory levels, reducing carrying costs and minimizing the risk of stockouts.
Enhanced Production Efficiency
MRP ensures that materials are available when needed, avoiding production delays due to material shortages.
This leads to an increase in production efficiency and helps maintain a steady production flow.
Cost Reduction
Efficient procurement through MRP can lead to cost reductions.
By minimizing unnecessary inventory costs and optimizing material orders, companies can achieve significant savings.
Better Supplier Relationships
MRP facilitates improved communication and collaboration with suppliers.
By providing clear and accurate material requirements, companies can build stronger relationships with suppliers, leading to better negotiation terms and more reliable deliveries.
Challenges in Implementing MRP
While MRP offers numerous benefits, its implementation can present some challenges:
Data Accuracy
The effectiveness of MRP relies heavily on the accuracy of data input.
Inaccurate data can lead to incorrect material requirements and disrupt production schedules.
System Complexity
MRP systems can be complex to implement and require significant time and resources.
Training staff to operate the system effectively is crucial to maximize its benefits.
Change Management
Implementing MRP involves changes in the way a company manages its production and procurement processes.
Change management strategies are essential to ensure a smooth transition and acceptance among staff.
Best Practices for Successful MRP Implementation
To overcome challenges and ensure successful MRP implementation, consider the following best practices:
Continuous Staff Training
Regular training sessions ensure that employees stay up-to-date with MRP processes and are equipped to handle any changes in systems or practices.
Invest in Reliable Software
Choosing reliable MRP software that integrates seamlessly with existing systems can make a significant difference in its effectiveness.
Evaluate available options to find software that best suits the company’s needs.
Foster Supplier Communication
Maintain open lines of communication with suppliers to ensure timely deliveries and minimize disruptions.
Strong supplier relationships are key to the smooth operation of the MRP system.
Regularly Review and Update Data
Regular audits and updates of inventory data, BOM, and production schedules will help maintain the accuracy of the MRP system and prevent potential issues.
In conclusion, the production planning department can greatly benefit from implementing MRP for material procurement.
By understanding the components, processes, and best practices, companies can enhance efficiency, reduce costs, and improve production planning overall.
資料ダウンロード
QCD調達購買管理クラウド「newji」は、調達購買部門で必要なQCD管理全てを備えた、現場特化型兼クラウド型の今世紀最高の購買管理システムとなります。
ユーザー登録
調達購買業務の効率化だけでなく、システムを導入することで、コスト削減や製品・資材のステータス可視化のほか、属人化していた購買情報の共有化による内部不正防止や統制にも役立ちます。
NEWJI DX
製造業に特化したデジタルトランスフォーメーション(DX)の実現を目指す請負開発型のコンサルティングサービスです。AI、iPaaS、および先端の技術を駆使して、製造プロセスの効率化、業務効率化、チームワーク強化、コスト削減、品質向上を実現します。このサービスは、製造業の課題を深く理解し、それに対する最適なデジタルソリューションを提供することで、企業が持続的な成長とイノベーションを達成できるようサポートします。
オンライン講座
製造業、主に購買・調達部門にお勤めの方々に向けた情報を配信しております。
新任の方やベテランの方、管理職を対象とした幅広いコンテンツをご用意しております。
お問い合わせ
コストダウンが利益に直結する術だと理解していても、なかなか前に進めることができない状況。そんな時は、newjiのコストダウン自動化機能で大きく利益貢献しよう!
(Β版非公開)