- お役立ち記事
- How to proceed with overseas procurement to avoid problems and countermeasures for quality, delivery dates, and transportation issues
月間77,185名の
製造業ご担当者様が閲覧しています*
*2025年2月28日現在のGoogle Analyticsのデータより
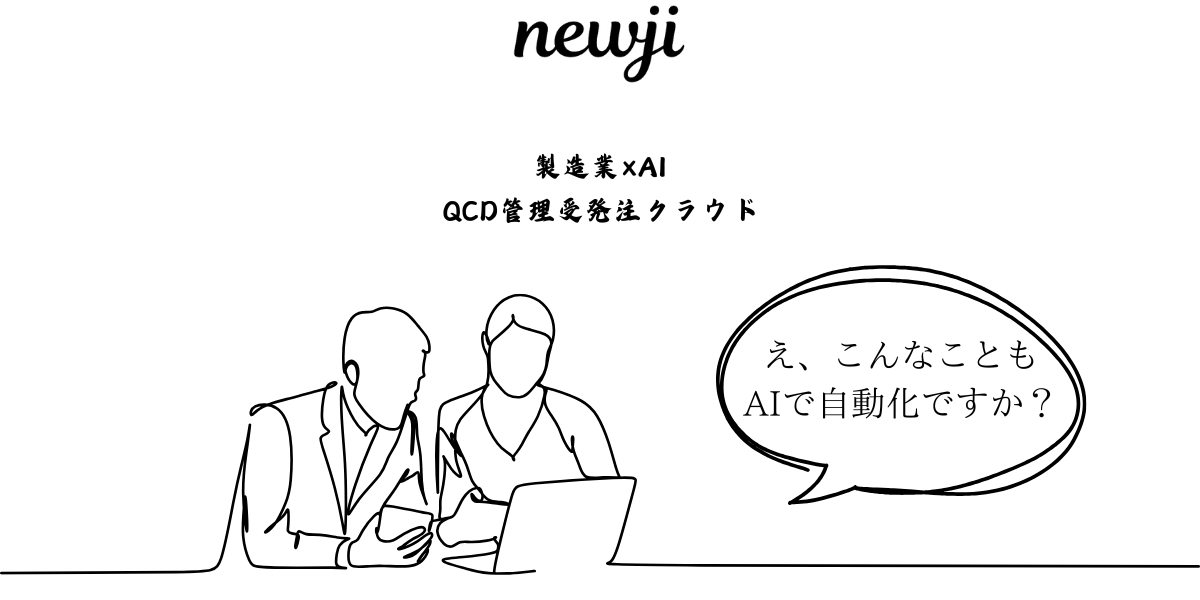
How to proceed with overseas procurement to avoid problems and countermeasures for quality, delivery dates, and transportation issues
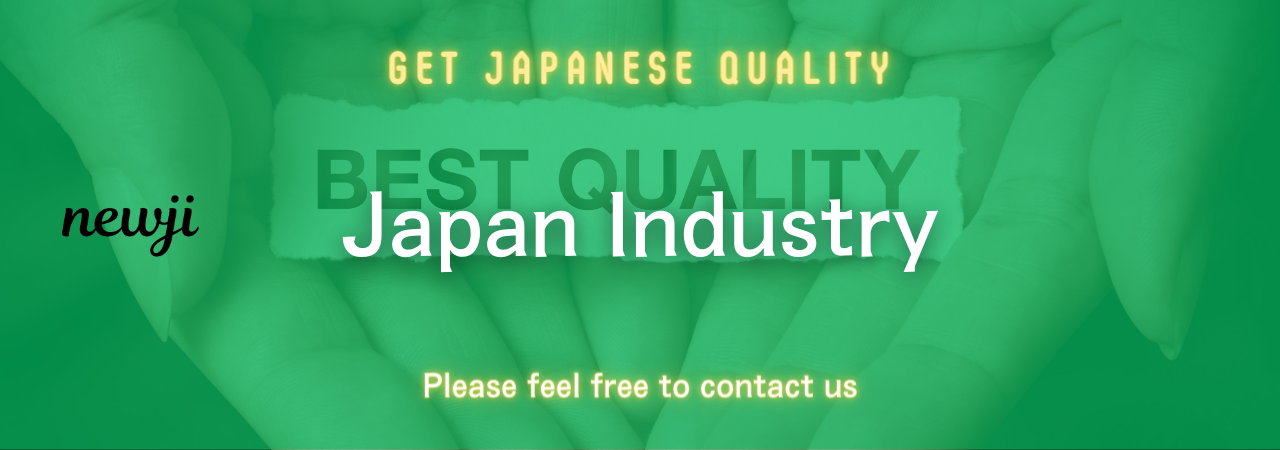
目次
Understanding Overseas Procurement
Overseas procurement is the process of sourcing goods, services, or raw materials from another country to meet business needs.
This practice is increasingly common as businesses look to reduce costs, access unique products, or tap into specialized expertise that may not be available locally.
However, engaging in overseas procurement isn’t without its challenges.
Understanding these challenges and knowing how to overcome them is key to a successful procurement strategy.
Key Challenges in Overseas Procurement
One of the main issues companies face with overseas procurement is ensuring product quality.
When purchasing from foreign suppliers, direct inspection may not always be feasible, making it difficult to assess the quality of goods before they arrive.
Differences in quality standards and manufacturing processes in other countries can further complicate matters.
Delivery dates can also present a challenge.
When procuring goods from overseas, shipping times can be unpredictable due to various factors such as customs clearance, delays at ports, or unforeseen logistical issues.
This uncertainty can disrupt supply chains and affect overall business operations.
Transportation issues, including shipping costs and logistical hurdles, are another common problem.
Long distances mean higher transportation costs and increased risks of damage or loss during transit.
Additionally, navigating international shipping regulations and documentation can be complex.
Steps to Efficient Overseas Procurement
To tackle these challenges, it is important to have a well-thought-out strategy in place.
Here are some steps you can take to ensure efficient overseas procurement:
1. Research and Choose the Right Supplier
The first step in overseas procurement is conducting thorough research to identify potential suppliers.
Look for suppliers who have a good reputation and a track record of delivering quality products on time.
Check for certifications or accreditations that demonstrate their adherence to international standards.
Engage in conversations with them and consider visiting their facilities if possible, to get a sense of their capabilities.
2. Establish Clear Communication
Effective communication is critical when dealing with overseas suppliers.
Language barriers and time zone differences can hinder communication, so it’s essential to establish clear channels of communication.
Use written communication to avoid misunderstandings and ensure that all specifications, timelines, and expectations are agreed upon by both parties.
3. Implement Quality Control Measures
To address quality concerns, implement a robust quality control process.
This may involve setting clear quality standards and specifications for the products you’re sourcing.
Consider hiring third-party inspection agencies to verify that products meet your quality requirements before they are shipped.
4. Plan for Delays
Being prepared for potential delays is crucial in overseas procurement.
Build in buffer times to accommodate any unforeseen delays in delivery.
Keep a flexible inventory management system that can adapt to fluctuations in supply.
Additionally, maintain open lines of communication with your suppliers to stay informed about any issues that may arise.
5. Optimize Transportation and Logistics
To avoid transportation issues, choose the right logistics partner with expertise in international shipping.
They can help navigate the complexities of customs regulations and ensure that all necessary documentation is in order.
Evaluate different transportation options and consider consolidating shipments to reduce costs.
Moreover, invest in insurance to protect against damage or loss during transit.
Countermeasures for Common Overseas Procurement Problems
Addressing Quality Concerns
Quality issues can lead to customer dissatisfaction and increased costs due to returns or replacements.
To mitigate quality concerns, establish key performance indicators (KPIs) with your suppliers to track quality over time.
Regularly review performance data and provide feedback to ensure continuous improvement.
Building long-term relationships with trusted suppliers can also encourage them to prioritize your quality requirements.
Overcoming Delivery Challenges
To overcome delivery challenges, utilize technology to improve visibility along your supply chain.
Implement a robust tracking system to monitor the status of shipments and anticipate delays.
Develop contingency plans that can be activated when delivery schedules are compromised.
Additionally, maintaining a reliable network of alternate suppliers can help you meet demands when primary suppliers experience delays.
Managing Transportation and Logistics
When managing transportation and logistics, stay informed about changes in international trade policies that might impact your procurement strategy.
Engage with logistics experts who can provide insights into optimizing routes and managing costs effectively.
When shipping goods, prioritize modes of transport that offer both reliability and cost-efficiency.
Encourage your logistics partners to adopt technology solutions that enhance transparency and communication throughout the shipping process.
Conclusion
Overseas procurement is a valuable strategy for businesses looking to enhance their competitive edge, but it requires careful planning and execution to avoid potential pitfalls.
By understanding the common challenges of quality, delivery, and transportation, and implementing effective countermeasures, you can streamline your overseas procurement efforts.
Building strong relationships with reliable suppliers and logistics partners, maintaining open communication, and leveraging technology can all contribute to building a successful overseas procurement strategy.
With these measures in place, businesses can navigate the complexities of international sourcing, ensure consistent supply, and ultimately achieve their strategic goals.
資料ダウンロード
QCD管理受発注クラウド「newji」は、受発注部門で必要なQCD管理全てを備えた、現場特化型兼クラウド型の今世紀最高の受発注管理システムとなります。
ユーザー登録
受発注業務の効率化だけでなく、システムを導入することで、コスト削減や製品・資材のステータス可視化のほか、属人化していた受発注情報の共有化による内部不正防止や統制にも役立ちます。
NEWJI DX
製造業に特化したデジタルトランスフォーメーション(DX)の実現を目指す請負開発型のコンサルティングサービスです。AI、iPaaS、および先端の技術を駆使して、製造プロセスの効率化、業務効率化、チームワーク強化、コスト削減、品質向上を実現します。このサービスは、製造業の課題を深く理解し、それに対する最適なデジタルソリューションを提供することで、企業が持続的な成長とイノベーションを達成できるようサポートします。
製造業ニュース解説
製造業、主に購買・調達部門にお勤めの方々に向けた情報を配信しております。
新任の方やベテランの方、管理職を対象とした幅広いコンテンツをご用意しております。
お問い合わせ
コストダウンが利益に直結する術だと理解していても、なかなか前に進めることができない状況。そんな時は、newjiのコストダウン自動化機能で大きく利益貢献しよう!
(β版非公開)