- お役立ち記事
- How to proceed with parts and materials procurement and key points for quality assurance, cost reduction, and supplier management
月間76,176名の
製造業ご担当者様が閲覧しています*
*2025年3月31日現在のGoogle Analyticsのデータより
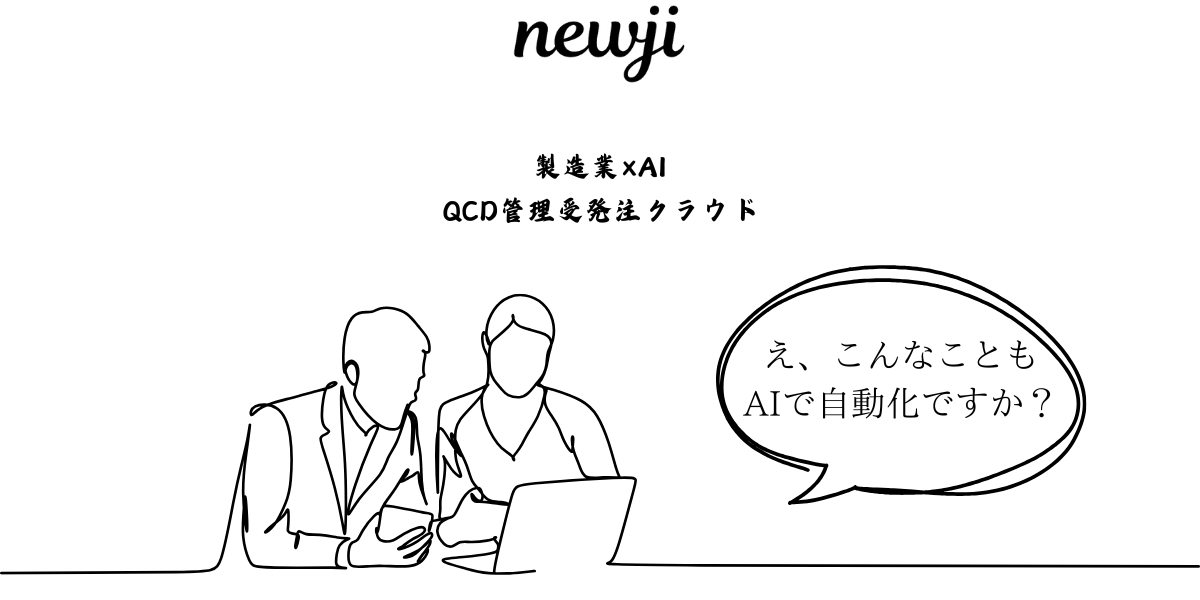
How to proceed with parts and materials procurement and key points for quality assurance, cost reduction, and supplier management
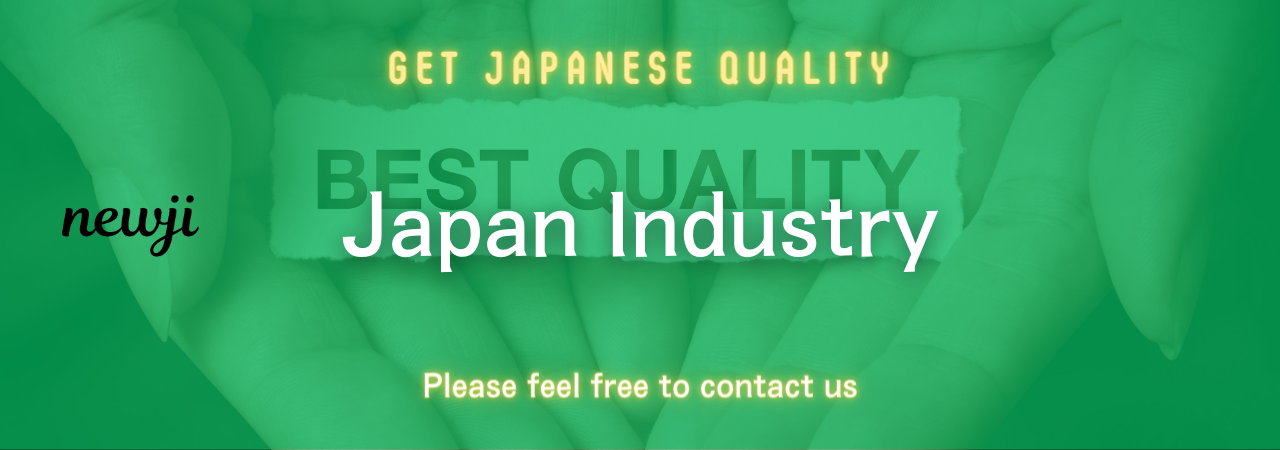
目次
Understanding Parts and Materials Procurement
Parts and materials procurement is a pivotal process in any manufacturing or production-related industry.
It involves acquiring the necessary components and raw materials needed to create finished goods.
This process must be handled with precision because it directly impacts the production timeline, cost-effectiveness, and the overall quality of the final product.
To ensure that procurement is conducted efficiently, businesses need to understand the significance of selecting the right suppliers, maintaining quality standards, and managing costs.
Quality Assurance: A Crucial Aspect
Quality assurance in procurement is about ensuring that the parts and materials obtained meet the necessary standards and specifications.
It is important to establish stringent quality checks at various stages of the procurement process.
This starts from the initial evaluation of potential suppliers to the final inspection of received materials.
To achieve effective quality assurance, businesses should conduct thorough inspections and assessments of incoming materials.
This includes verifying the materials against set quality standards and production requirements.
Additionally, implementing a robust supplier evaluation system can help in maintaining a consistent quality level.
The Importance of Cost Reduction
Cost reduction plays a critical role in parts and materials procurement as it directly impacts a company’s profitability.
One effective way to achieve cost reduction is through strategic sourcing, which involves negotiating better terms with suppliers and seeking alternative sources that offer competitive pricing without compromising on quality.
Additionally, implementing a Just-In-Time (JIT) inventory system can significantly reduce costs associated with storage and inventory management.
By only ordering materials as needed, businesses can minimize excess inventory, reduce holding costs, and improve cash flow.
Supplier Management for Optimal Collaboration
Effective supplier management is key to success in procurement.
It involves building strong relationships with suppliers to ensure timely delivery and consistent quality of materials.
Establishing clear communication channels and setting expectations from the outset can lead to a more collaborative relationship.
Engaging suppliers in long-term contracts, offering feedback, and regularly reviewing their performance can help in reinforcing these relationships.
Moreover, having contingency plans with multiple suppliers reduces the risk associated with dependency on a single source.
Steps to Effective Parts and Materials Procurement
Understanding the step-by-step process involved in procurement can significantly enhance efficiency and outcomes.
Step 1: Identification of Needs
The first step in parts and materials procurement is identifying the required goods based on the production needs.
This involves determining the specifications, quantity, and timelines for the required materials.
It is essential to have a clear understanding of the production schedules and requirements to ensure that procurement aligns with the overall production plan.
Step 2: Supplier Evaluation and Selection
Once the needs are identified, the next step is to evaluate potential suppliers.
This involves assessing suppliers based on their ability to meet quality standards, delivery timelines, and cost parameters.
Conducting supplier audits and visiting their facilities can provide better insight into their operational capabilities and reliability.
Step 3: Price Negotiation and Agreement
Negotiating favorable terms with the selected suppliers is a crucial step in procurement.
During this phase, it is important to discuss and finalize the pricing, payment terms, delivery schedule, and any other critical aspects.
Having a formal agreement or contract in place can protect both parties and serve as a reference if disputes arise.
Step 4: Ordering and Payment Process
Once terms are finalized, orders can be placed with the suppliers.
It is essential to establish an efficient ordering process that ensures clarity and prevention of errors.
Implementing a streamlined payment system can also enhance this step by ensuring timely payments and maintaining a good relationship with the suppliers.
Step 5: Receiving and Quality Inspection
Upon receiving the materials, conducting a thorough inspection is vital to verify that they meet the agreed-upon quality standards.
This involves checking for any discrepancies in quantity, specifications, and condition of the materials.
Any issues identified during this inspection should be promptly addressed with the supplier.
Key Points to Remember
To maintain an efficient procurement process, businesses should focus on three main factors: quality, cost, and supplier relationships.
Here are some key points to remember:
Regularly Evaluate Suppliers
Continuously monitor and assess supplier performance to ensure they consistently meet the required standards.
This can involve regular audits, performance reviews, and feedback sessions.
Focus on Long-term Partnerships
Developing long-term relationships with key suppliers can lead to better terms and collaboration.
It encourages suppliers to prioritize your business’s needs and contribute to mutual growth.
Adapt to Market Changes
Stay informed about market trends and price fluctuations to make informed procurement decisions.
Adapting quickly to market changes can help in securing favorable deals and maintaining the cost-effectiveness of the procurement process.
In conclusion, parts and materials procurement is a fundamental aspect of manufacturing that requires careful planning and management.
By focusing on quality assurance, cost reduction, and robust supplier management, businesses can establish a seamless procurement process that enhances production efficiency and supports strategic goals.
資料ダウンロード
QCD管理受発注クラウド「newji」は、受発注部門で必要なQCD管理全てを備えた、現場特化型兼クラウド型の今世紀最高の受発注管理システムとなります。
ユーザー登録
受発注業務の効率化だけでなく、システムを導入することで、コスト削減や製品・資材のステータス可視化のほか、属人化していた受発注情報の共有化による内部不正防止や統制にも役立ちます。
NEWJI DX
製造業に特化したデジタルトランスフォーメーション(DX)の実現を目指す請負開発型のコンサルティングサービスです。AI、iPaaS、および先端の技術を駆使して、製造プロセスの効率化、業務効率化、チームワーク強化、コスト削減、品質向上を実現します。このサービスは、製造業の課題を深く理解し、それに対する最適なデジタルソリューションを提供することで、企業が持続的な成長とイノベーションを達成できるようサポートします。
製造業ニュース解説
製造業、主に購買・調達部門にお勤めの方々に向けた情報を配信しております。
新任の方やベテランの方、管理職を対象とした幅広いコンテンツをご用意しております。
お問い合わせ
コストダウンが利益に直結する術だと理解していても、なかなか前に進めることができない状況。そんな時は、newjiのコストダウン自動化機能で大きく利益貢献しよう!
(β版非公開)