- お役立ち記事
- How to proceed with why-why analysis and how to effectively use it to prevent recurrence of quality defects
How to proceed with why-why analysis and how to effectively use it to prevent recurrence of quality defects
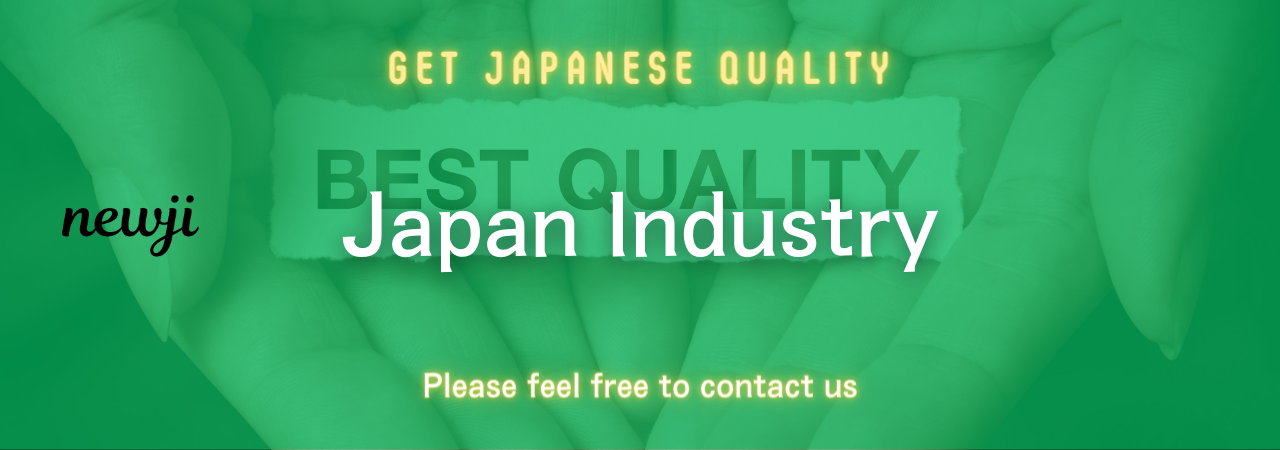
目次
What is Why-Why Analysis?
Why-why analysis is a problem-solving method used to identify the root causes of issues or defects.
By repeatedly asking the question “why,” businesses are able to drill down from the observed problem to its underlying causes.
This technique is especially useful in quality management processes within manufacturing, service industries, and even in daily life.
The rationale behind why-why analysis is that most problems don’t originate from a single cause.
Instead, they arise due to a combination of factors that may not be immediately obvious.
Steps to Conduct a Why-Why Analysis
1. Define the Problem
The first step in performing a why-why analysis is to clearly define the problem at hand.
Make sure to describe it in detailed and specific terms.
For example, instead of stating “The machine stopped,” specify “The machine stopped due to overheating.”
2. Assemble a Team
Gather a cross-functional team of people who have knowledge about the processes involved.
Include team members from different departments to gain various perspectives and insights into the problem.
3. Start Asking “Why?”
Begin with the problem statement and ask why it happened.
Then, continue to ask why for each subsequent answer.
Typically, this process is repeated about five times, but it can vary depending on the complexity of the issue.
4. Identify Root Causes
Once you have drilled down through the layers of causes, identify the root cause(s) among them.
These root causes are the underlying issues that need to be addressed to prevent recurrence of the defect.
5. Develop Action Plans
After identifying root causes, brainstorm actionable solutions.
These plans should be focused on eliminating or addressing the identified root causes.
For each action, allocate responsibility and set a timeline for implementation.
6. Validate the Solutions
Evaluate the effectiveness of the solutions implemented.
This may involve monitoring specific metrics to determine if the recurrence of defects is prevented or significantly reduced.
Importance of Why-Why Analysis in Preventing Quality Defects
Why-why analysis is a powerful tool in quality management for several reasons.
Firstly, it helps to avoid assumptions and jump to conclusions.
By deeply understanding the root of a problem, a business can prevent similar issues from occurring in the future.
Moreover, it encourages a proactive approach by addressing potential defects at their origin rather than just treating symptoms.
Additionally, the structured nature of why-why analysis promotes better communication within teams.
Collaboration in identifying root causes brings diverse perspectives, improving both the problem-solving process and fostering a culture of continuous improvement.
Finally, implementing why-why analysis can lead to significant cost savings.
By effectively correcting root causes, businesses can reduce waste, rework, and the associated financial implications of recurring quality defects.
Best Practices for Effective Why-Why Analysis
Encourage Open Communication
Foster an environment where team members feel comfortable sharing insights and observations.
This openness ensures all relevant factors are considered during the analysis.
Avoid Blame
When conducting a why-why analysis, focus on processes, not people.
Assigning blame can stifle creativity and honest discussion needed to identify root causes.
Use Visual Aids
Incorporating tools such as flowcharts, diagrams, and fishbone diagrams can help visualize the relationship between causes and effects.
These tools can aid in maintaining clarity during the analysis.
Be Flexible
If a valid reason arises for a deviation, accept it.
Not every problem will require exactly five “whys,” and the process should adapt to the complexity of the issue.
Document Everything
Record the entire analysis process, from problem definition to root cause identification and action plan development.
Documentation serves as a reference for future analyses and helps track the progress and effectiveness of implemented solutions.
Conclusion: Using Why-Why Analysis for Long-term Improvements
Why-why analysis is more than a technique for addressing immediate quality defects.
It is a strategic approach that leads to long-term improvements in processes and systems.
By identifying and tackling root causes, businesses can not only prevent the recurrence of defects but also enhance overall operational efficiency and product quality.
To maximize the benefits of why-why analysis, its practice should become a standard part of problem-solving within an organization.
When coupled with a commitment to continuous learning and improvement, why-why analysis is an essential tool in a company’s arsenal for maintaining high quality standards and achieving sustainable growth.
資料ダウンロード
QCD調達購買管理クラウド「newji」は、調達購買部門で必要なQCD管理全てを備えた、現場特化型兼クラウド型の今世紀最高の購買管理システムとなります。
ユーザー登録
調達購買業務の効率化だけでなく、システムを導入することで、コスト削減や製品・資材のステータス可視化のほか、属人化していた購買情報の共有化による内部不正防止や統制にも役立ちます。
NEWJI DX
製造業に特化したデジタルトランスフォーメーション(DX)の実現を目指す請負開発型のコンサルティングサービスです。AI、iPaaS、および先端の技術を駆使して、製造プロセスの効率化、業務効率化、チームワーク強化、コスト削減、品質向上を実現します。このサービスは、製造業の課題を深く理解し、それに対する最適なデジタルソリューションを提供することで、企業が持続的な成長とイノベーションを達成できるようサポートします。
オンライン講座
製造業、主に購買・調達部門にお勤めの方々に向けた情報を配信しております。
新任の方やベテランの方、管理職を対象とした幅広いコンテンツをご用意しております。
お問い合わせ
コストダウンが利益に直結する術だと理解していても、なかなか前に進めることができない状況。そんな時は、newjiのコストダウン自動化機能で大きく利益貢献しよう!
(Β版非公開)