- お役立ち記事
- How to proceed with why-why analysis and how to effectively use it to prevent recurrence of quality defects
月間77,185名の
製造業ご担当者様が閲覧しています*
*2025年2月28日現在のGoogle Analyticsのデータより
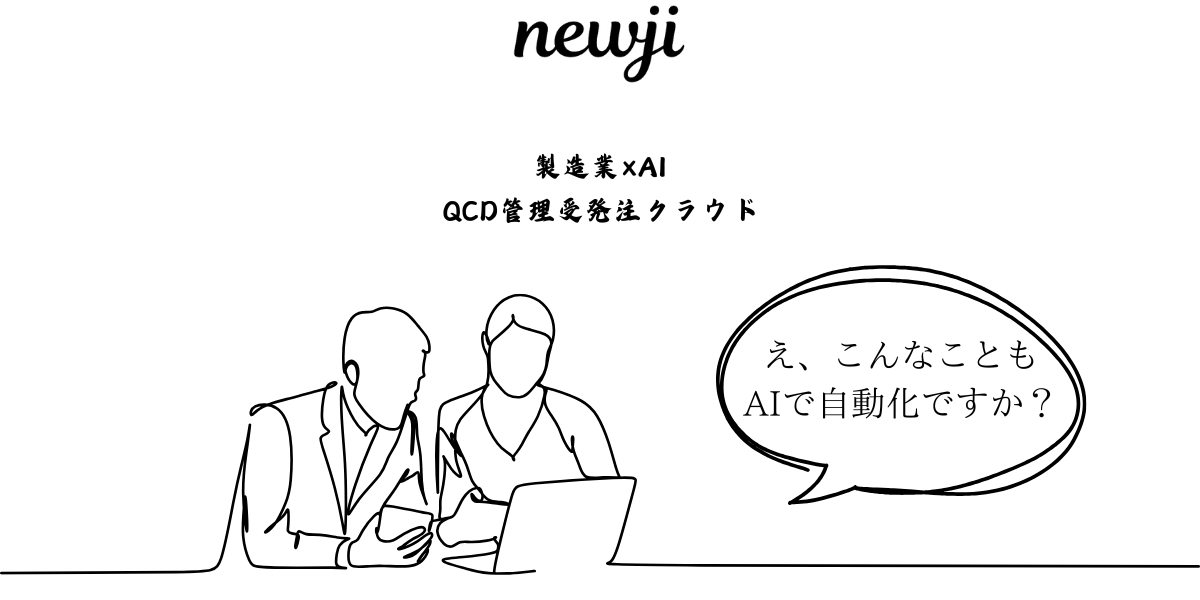
How to proceed with why-why analysis and how to effectively use it to prevent recurrence of quality defects
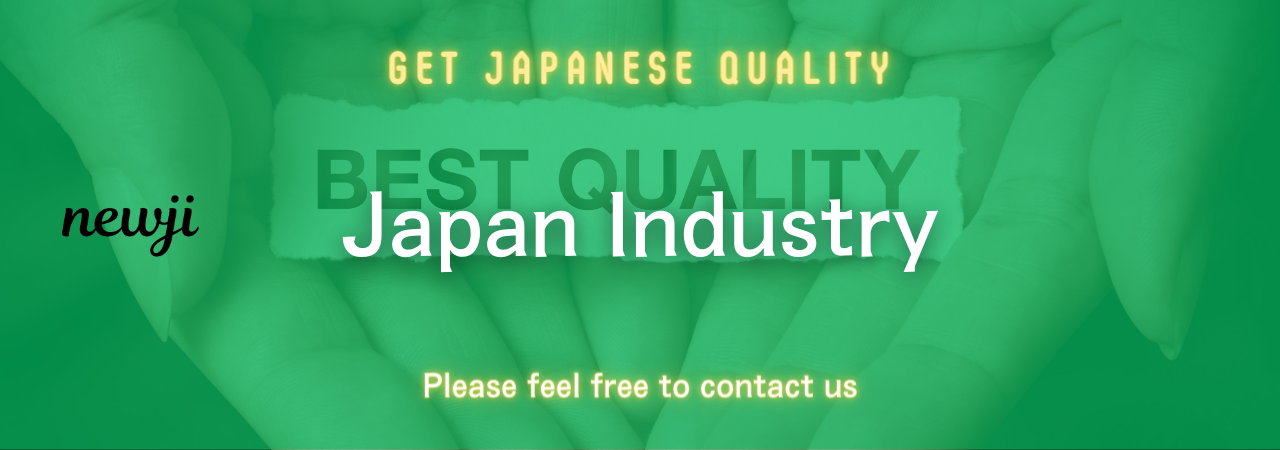
目次
Understanding Why-Why Analysis
The Why-Why Analysis is a simple yet powerful tool used to explore the cause-and-effect relationships underlying a particular problem.
It’s designed to root out the fundamental cause of a defect or issue, rather than simply addressing its symptoms.
By repeatedly asking “why” something has occurred, a deeper understanding is achieved, leading to effective resolution and prevention of problem recurrence.
Originating from the world of quality management, the Why-Why Analysis has found applications in various industries.
It’s a part of Toyota’s production system methods, renowned for its efficiency and effectiveness.
Five Steps to Conduct a Why-Why Analysis
To perform a Why-Why Analysis, one must follow a structured process.
The steps are easy to follow, making it accessible to anyone within an organization.
Step 1: Assemble a Team
Gather a team with diverse expertise and perspectives related to the problem.
This diversity aids in thorough examination and understanding of the issues.
Step 2: Define the Problem
Clearly define the problem at hand.
Describe it precisely, focusing on what is happening and how it impacts your process or product.
A well-defined problem is a critical starting point for an effective analysis.
Step 3: Ask “Why”
Begin with the problem statement and ask “why” it occurred.
Record the response and treat it like a new problem.
Ask “why” again to dig deeper.
Repeat this questioning process as often as needed.
Five iterations are common, but more may be necessary to uncover the root cause.
Step 4: Identify the Root Cause
When the line of questioning no longer yields further responses, you’ve likely reached the root cause.
This is the fundamental issue that needs resolution to prevent recurrence.
It’s crucial to ensure that the root cause is within your control to manage or fix.
Step 5: Develop and Implement a Solution
Formulate a strategy to address the root cause.
The solution must be actionable and designed to prevent the problem from resurfacing.
Post-implementation, monitor the situation to ensure the problem does not reappear and tweak the solution if necessary.
Benefits of Employing Why-Why Analysis
Utilizing Why-Why Analysis brings several benefits to an organization.
Identifying Root Causes
It helps in accurately identifying the underlying causes of problems, ensuring solutions are effective rather than merely band-aid fixes.
Preventing Problem Recurrence
Since it addresses the root cause, the chances of the issue recurring are significantly minimized.
This proactive approach leads to long-term process improvements.
Improved Decision-Making
The clarity offered by Why-Why Analysis supports better decision-making.
With a solid understanding of causes, strategies can be more effectively designed and implemented.
Facilitates Team Collaboration
The analysis encourages collaboration and participatory efforts among team members.
Diverse perspectives foster a comprehensive understanding of issues, facilitating more robust solutions.
Common Pitfalls and How to Avoid Them
While Why-Why Analysis is straightforward, certain pitfalls can undermine its effectiveness.
Vague Problem Statements
It is crucial to articulate the problem concisely at the outset.
A vague problem results in unclear analysis and ineffective solutions.
Neglecting Necessary Expertise
Ensure your team encompasses individuals with relevant knowledge sectors.
Inadequate expertise can lead to incomplete analysis, failing to pinpoint the root cause.
Stopping Too Soon
Do not stop asking “why” prematurely.
If the root cause is not identified, the exercise does not achieve its purpose.
Continue questioning until you’re satisfied with the thoroughness.
Attributing the Cause to Human Error
Avoid the trap of simply blaming human error as the root cause.
Looking deeper often reveals systemic issues that need addressing, rather than placing blame on individuals.
Effective Use of Why-Why Analysis in Quality Management
To effectively leverage Why-Why Analysis for preventing quality defects, integrate it into your quality management practices.
Create a Supportive Culture
Build an organizational culture that values continuous improvement and sees mistakes as learning opportunities.
Encourage open communication and collective problem-solving.
Train Your Workforce
Equip your employees with the skills to perform Why-Why Analysis through regular training sessions.
Ensure they understand the importance of identifying and addressing root causes.
Incorporate into Routine Procedures
Make Why-Why Analysis part of routine procedures whenever defects are detected.
Regular application strengthens processes and quality standards.
Document and Share Findings
Keep a record of each analysis conducted along with the solutions implemented.
Share these learnings across departments to foster organizational learning and improvement.
By diligently applying the Why-Why Analysis method and integrating it into your quality management systems, organizations can significantly reduce the recurrence of quality defects and improve their processes.
The result is a more robust, efficient, and competitive operation.
資料ダウンロード
QCD管理受発注クラウド「newji」は、受発注部門で必要なQCD管理全てを備えた、現場特化型兼クラウド型の今世紀最高の受発注管理システムとなります。
ユーザー登録
受発注業務の効率化だけでなく、システムを導入することで、コスト削減や製品・資材のステータス可視化のほか、属人化していた受発注情報の共有化による内部不正防止や統制にも役立ちます。
NEWJI DX
製造業に特化したデジタルトランスフォーメーション(DX)の実現を目指す請負開発型のコンサルティングサービスです。AI、iPaaS、および先端の技術を駆使して、製造プロセスの効率化、業務効率化、チームワーク強化、コスト削減、品質向上を実現します。このサービスは、製造業の課題を深く理解し、それに対する最適なデジタルソリューションを提供することで、企業が持続的な成長とイノベーションを達成できるようサポートします。
製造業ニュース解説
製造業、主に購買・調達部門にお勤めの方々に向けた情報を配信しております。
新任の方やベテランの方、管理職を対象とした幅広いコンテンツをご用意しております。
お問い合わせ
コストダウンが利益に直結する術だと理解していても、なかなか前に進めることができない状況。そんな時は、newjiのコストダウン自動化機能で大きく利益貢献しよう!
(β版非公開)