- お役立ち記事
- How to proceed with why-why analysis and how to utilize it to prevent problems from recurring
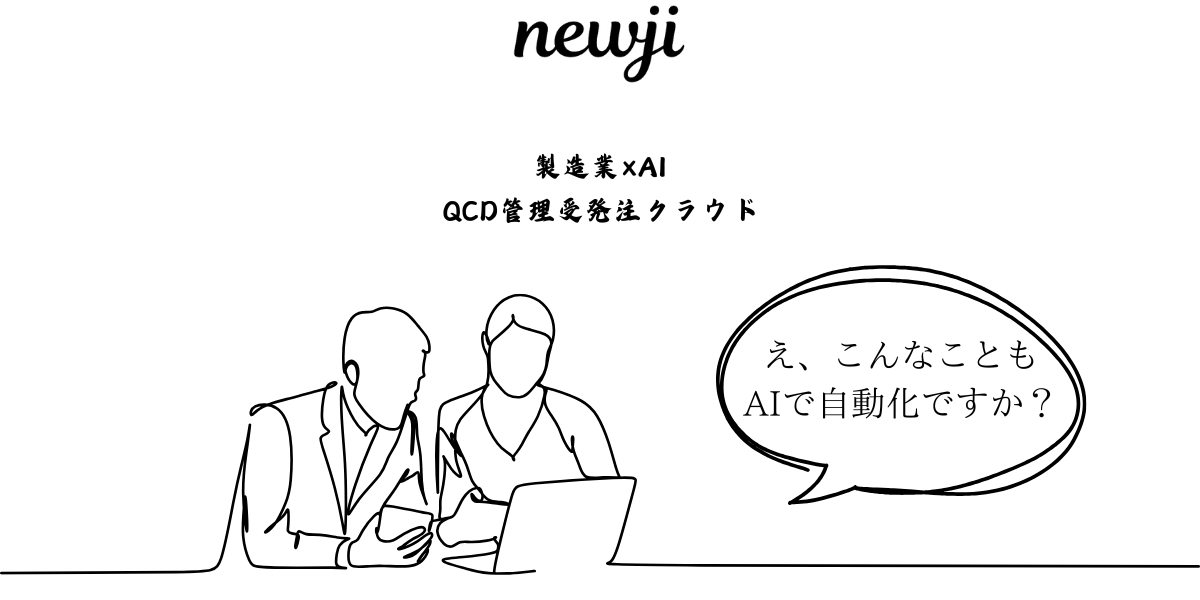
How to proceed with why-why analysis and how to utilize it to prevent problems from recurring
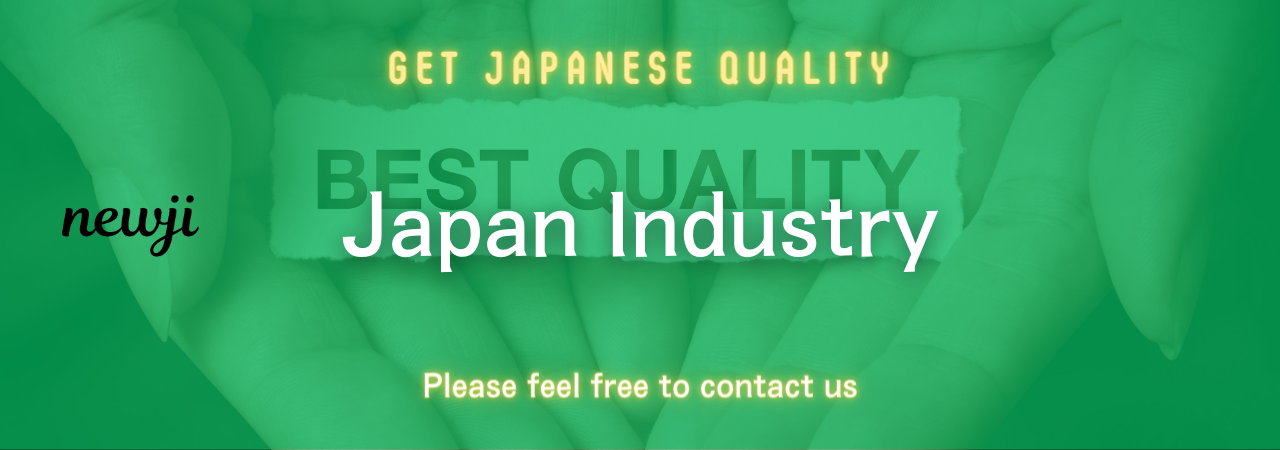
目次
Understanding Why-Why Analysis
Why-Why Analysis is a powerful problem-solving tool that aims to identify the root cause of an issue by repeatedly asking the question “Why?”.
This method is intuitive and relies on successive questioning to drill down into the depths of the problem.
The goal is to unravel the complexities of why a particular problem occurred, rather than just treating symptoms.
The Why-Why Analysis is key in fields like manufacturing, healthcare, software development, and any other industry where root cause identification plays a critical role in strategy and operations.
Origin and Importance
Originally part of the Toyota Production System, the Why-Why Analysis was designed to improve processes and systems by addressing the core reasons for defects or issues.
Its simplicity and effectiveness make it popular across multiple disciplines.
Understanding and implementing this tool can greatly reduce the chances of problems recurring, thereby ensuring a higher task efficiency and reduced resource wastage.
Steps to Conduct a Why-Why Analysis
The Why-Why Analysis can be broken down into several easy-to-follow steps.
Step 1: Identify the Problem
Clearly define the problem you are trying to solve.
Ensure that all stakeholders involved agree on the exact nature of the problem.
The problem statement should be specific and precise so that the right questions can be asked.
Step 2: Assemble a Team
Gather a team of individuals who are knowledgeable about the process or system in which the problem has occurred.
Their insights will provide diverse perspectives, aiding in identifying potential root causes.
A collaborative approach often yields more robust analyses.
Step 3: Start Asking “Why?”
Begin with the problem and ask “Why did this happen?” to identify the first causal layer.
Continue this process with each subsequent answer, quizzing deeper each time.
Typically, five rounds of questioning are recommended, but it can be more or fewer based on the complexity of the issue.
Step 4: Identify the Root Cause
Keep digging until you reach a fundamental issue that can be resolved or improved upon to prevent a recurrence of the problem.
The identified root cause should be actionable, specific, and within the team’s sphere of influence to address.
Step 5: Develop a Plan
Once the root cause is identified, develop an action plan to eliminate or mitigate the risk of the problem occurring again.
This plan should detail the steps necessary to implement changes, assign responsibilities, and set deadlines.
Ensure the plan is communicated effectively to all relevant parties to promote responsibility and accountability.
Utilizing Why-Why Analysis to Prevent Recurrence
Merely completing a Why-Why Analysis is not enough: without proper utilization, efforts might go wasted.
Implement the Action Plan
Executing the developed action plan is crucial for the process to result in tangible improvements.
Track progress closely, ensuring that all aspects of the plan are enacted with diligence.
Promptly address any resistance or obstacles that may surface.
Monitor and Measure Results
After implementation, it is vital to monitor the outcomes to ensure the problem has been effectively addressed.
Use relevant KPIs and metrics to gauge the efficacy.
Compare these to previous data to assess improvements and confirm if the root cause was accurately targeted.
Document the Process
Document each stage of the Why-Why Analysis, detailing the questions asked, responses given, and the root cause determined.
This documentation acts as an invaluable reference for future issues and fosters a culture of transparency and accountability.
Review and Reflect
Regularly review the analysis and subsequent results to reflect on what has been learned.
Adjust processes and strategies based on these insights to further refine problem-solving skills within your organization.
Promote a Continuous Improvement Culture
Publicize successful outcomes from the Why-Why Analysis to build momentum for continuous improvement initiatives.
Encourage an environment where team members continuously look for ways to enhance processes and freely communicate potential issues before they escalate.
Challenges and Considerations
While Why-Why Analysis is a powerful tool, it does come with certain challenges.
Risk of Assumptions
When asking “Why?” insist on data-driven and factual responses as opposed to assumptions or gut feelings.
Assumptions can divert focus away from the true root cause, leading to ineffective solutions.
Complex Problems
The Why-Why Analysis is more suited to simple to moderate complexity problems.
For more complex issues, additional tools and analyses may need to be employed alongside the Why-Why Analysis for a more comprehensive solution.
Poor Implementation
Despite identifying a root cause, poorly implemented action plans can cause the issue to persist.
It’s crucial to ensure proper resources, commitment, and follow-through for effective implementation.
Conclusion
Why-Why Analysis is an indispensable method for identifying the root causes of problems and preventing their recurrence.
By following the outlined steps, and utilizing the results effectively, organizations can enhance their problem-solving capabilities, ensuring robust solutions that safeguard against future issues.
With consistent application and organizational buy-in, the Why-Why Analysis can significantly contribute to the cultivation of a responsive and agile enterprise.
資料ダウンロード
QCD調達購買管理クラウド「newji」は、調達購買部門で必要なQCD管理全てを備えた、現場特化型兼クラウド型の今世紀最高の購買管理システムとなります。
ユーザー登録
調達購買業務の効率化だけでなく、システムを導入することで、コスト削減や製品・資材のステータス可視化のほか、属人化していた購買情報の共有化による内部不正防止や統制にも役立ちます。
NEWJI DX
製造業に特化したデジタルトランスフォーメーション(DX)の実現を目指す請負開発型のコンサルティングサービスです。AI、iPaaS、および先端の技術を駆使して、製造プロセスの効率化、業務効率化、チームワーク強化、コスト削減、品質向上を実現します。このサービスは、製造業の課題を深く理解し、それに対する最適なデジタルソリューションを提供することで、企業が持続的な成長とイノベーションを達成できるようサポートします。
オンライン講座
製造業、主に購買・調達部門にお勤めの方々に向けた情報を配信しております。
新任の方やベテランの方、管理職を対象とした幅広いコンテンツをご用意しております。
お問い合わせ
コストダウンが利益に直結する術だと理解していても、なかなか前に進めることができない状況。そんな時は、newjiのコストダウン自動化機能で大きく利益貢献しよう!
(Β版非公開)