- お役立ち記事
- How to proceed with why-why analysis and practice to prevent recurrence of quality defects
月間76,176名の
製造業ご担当者様が閲覧しています*
*2025年3月31日現在のGoogle Analyticsのデータより
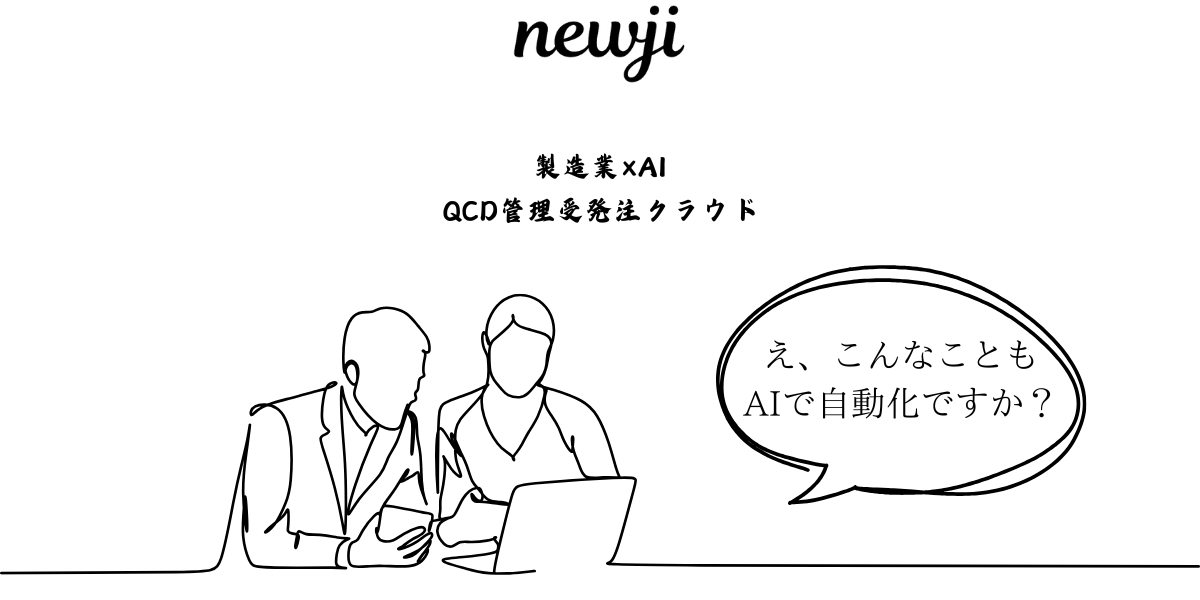
How to proceed with why-why analysis and practice to prevent recurrence of quality defects
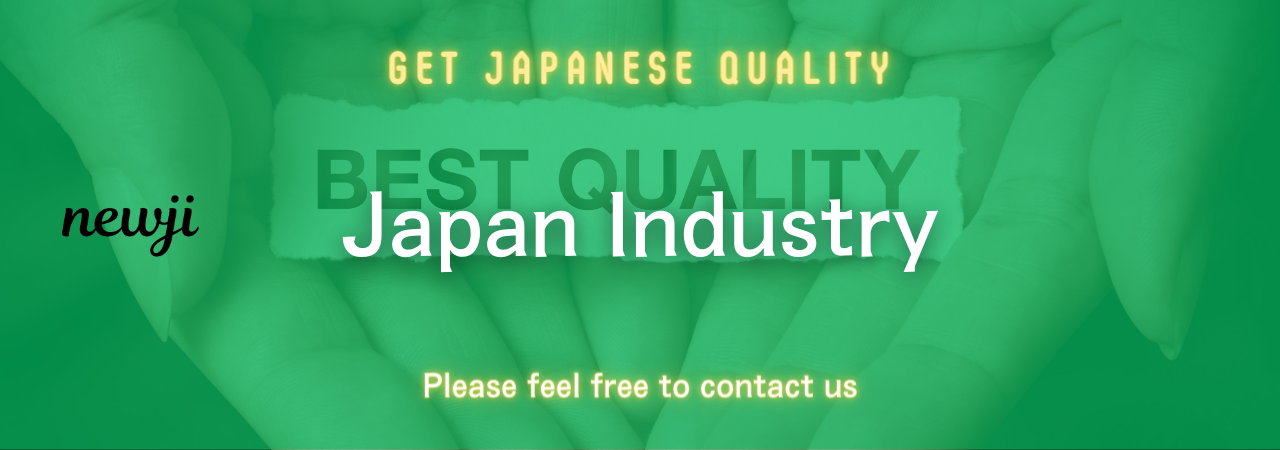
目次
Understanding Why-Why Analysis
Why-why analysis is a method used to identify the root cause of a problem, especially quality defects, by asking “why” multiple times until the fundamental issue is uncovered.
This analysis is a simple yet powerful tool that helps organizations prevent defects from reoccurring by eliminating the root cause.
The need for why-why analysis often arises when a quality defect is discovered in a product or service.
The immediate reaction might be to address the symptoms and not the root problem.
However, without understanding and addressing the root cause, a company might find itself dealing with the same issue repeatedly.
This not only incurs costs but also affects customer satisfaction and trust.
Steps to Implement Why-Why Analysis
The process of conducting a why-why analysis can be broken down into several steps.
Each step requires careful consideration and input from team members who understand the situation and processes involved.
1. Identify the Problem
The first step in a why-why analysis is to clearly define the problem or defect.
It is important to express the issue in detail so that everyone involved understands what needs to be solved.
For example, if a manufacturing defect is causing a high rate of product returns, describe the nature of the defect, how often it occurs, and its impact on the business.
2. Gather the Team
Involve a team that is knowledgeable about the processes involved with the defect.
This team can include managers, operators, engineers, or any other personnel involved in the production or delivery process.
The diversity in the team’s expertise can lead to a more comprehensive view of the problem and more effective brainstorming of potential causes.
3. Begin with the First “Why”
Ask why the problem occurred.
This step involves looking at immediate causes or factors that led to the defect.
The answer should not be superficial but should reflect real reasons that can be substantiated by evidence.
4. Ask “Why” Again
For every answer given, ask why it happened.
Continue asking “why” until the team agrees that the root cause has been identified.
The aim is to push beyond symptoms and reach the core issue.
Generally, this may take anywhere from three to five iterations of asking “why,” depending on the complexity of the problem.
5. Identify the Root Cause
Once the root cause is reached, review if there is enough evidence or data that supports this finding.
The identified root cause should explain the defect fully and align with recorded observations.
6. Develop Solutions
With the root cause identified, brainstorm practical solutions that will address the issue and prevent it from recurring.
Solutions might include process changes, additional training for staff, or new quality control procedures.
Ensure these solutions are sustainable and feasible within the organization’s resources and capacity.
7. Implement Changes
Carry out the solutions identified.
It’s important to monitor the implementation to ensure that the changes are being followed as planned.
Documentation is key at this stage to capture what changes were made and any immediate effects observed.
8. Monitor and Review
After implementation, continuously monitor the situation to ensure that the solutions have effectively addressed the root cause.
Regular reviews and follow-ups can help detect any signs of the problem reoccurring and assess the effectiveness of the new processes in place.
Benefits of Why-Why Analysis
Using why-why analysis allows organizations to dive deep into problem-solving, focusing on prevention rather than reaction.
Long-term Solutions
By finding the root cause rather than treating symptoms, companies can implement changes that offer long-term solutions instead of quick fixes.
Efficiency and Cost-Effective
Preventing issues reduces the need for emergency fixes, which can be time-consuming and costly.
Improved Quality
By understanding and mitigating the root causes of defects, the overall quality of products and services is enhanced, leading to higher customer satisfaction.
Enhanced Team Collaboration
Involving a cross-functional team fosters communication and collaboration within the organization, encouraging diverse thinking and engagement in problem-solving.
Best Practices for Conducting Why-Why Analysis
While why-why analysis is a straightforward concept, there are some best practices to ensure it is most effective.
Be Thorough and Honest
Ensure that the answers reflect true causes rather than pointing fingers at individuals.
Honesty is crucial to uncovering real issues.
Stay Focused
Keep the analysis centered on one specific problem at a time to avoid confusion and ensure that the results are meaningful and applicable.
Ensure Consistency
Apply the same structured approach each time you conduct a why-why analysis to ensure consistent results and that team members are familiar with the process.
Document Findings
Always document the process and findings.
This documentation is useful for reference in future analyses and helps to evaluate the effectiveness of implemented solutions.
Conclusion
Why-why analysis is a critical tool for uncovering the root causes of quality defects and preventing their recurrence.
By following the structured process of asking “why” repeatedly and involving a knowledgeable team, organizations can effectively identify and solve underlying issues.
Implementing this analysis leads to long-term improvements in quality and operational efficiency.
Ultimately, it helps build a stronger and more resilient organization that is capable of consistently delivering high-quality products and services.
資料ダウンロード
QCD管理受発注クラウド「newji」は、受発注部門で必要なQCD管理全てを備えた、現場特化型兼クラウド型の今世紀最高の受発注管理システムとなります。
ユーザー登録
受発注業務の効率化だけでなく、システムを導入することで、コスト削減や製品・資材のステータス可視化のほか、属人化していた受発注情報の共有化による内部不正防止や統制にも役立ちます。
NEWJI DX
製造業に特化したデジタルトランスフォーメーション(DX)の実現を目指す請負開発型のコンサルティングサービスです。AI、iPaaS、および先端の技術を駆使して、製造プロセスの効率化、業務効率化、チームワーク強化、コスト削減、品質向上を実現します。このサービスは、製造業の課題を深く理解し、それに対する最適なデジタルソリューションを提供することで、企業が持続的な成長とイノベーションを達成できるようサポートします。
製造業ニュース解説
製造業、主に購買・調達部門にお勤めの方々に向けた情報を配信しております。
新任の方やベテランの方、管理職を対象とした幅広いコンテンツをご用意しております。
お問い合わせ
コストダウンが利益に直結する術だと理解していても、なかなか前に進めることができない状況。そんな時は、newjiのコストダウン自動化機能で大きく利益貢献しよう!
(β版非公開)