- お役立ち記事
- How to promote collaboration between purchasing and logistics departments to reduce transportation costs
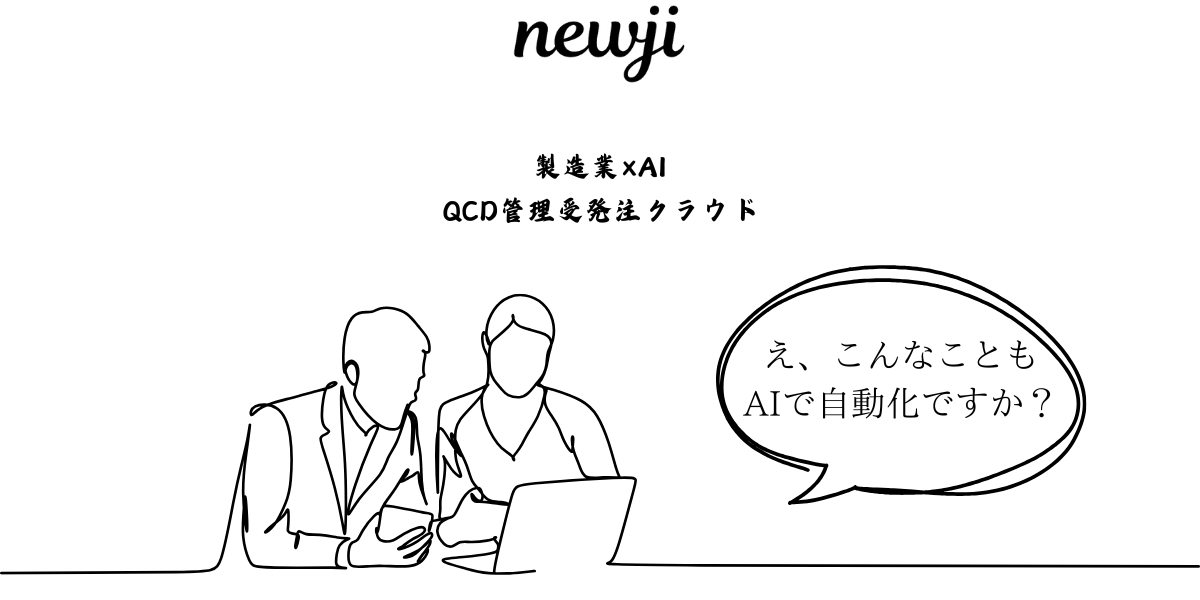
How to promote collaboration between purchasing and logistics departments to reduce transportation costs
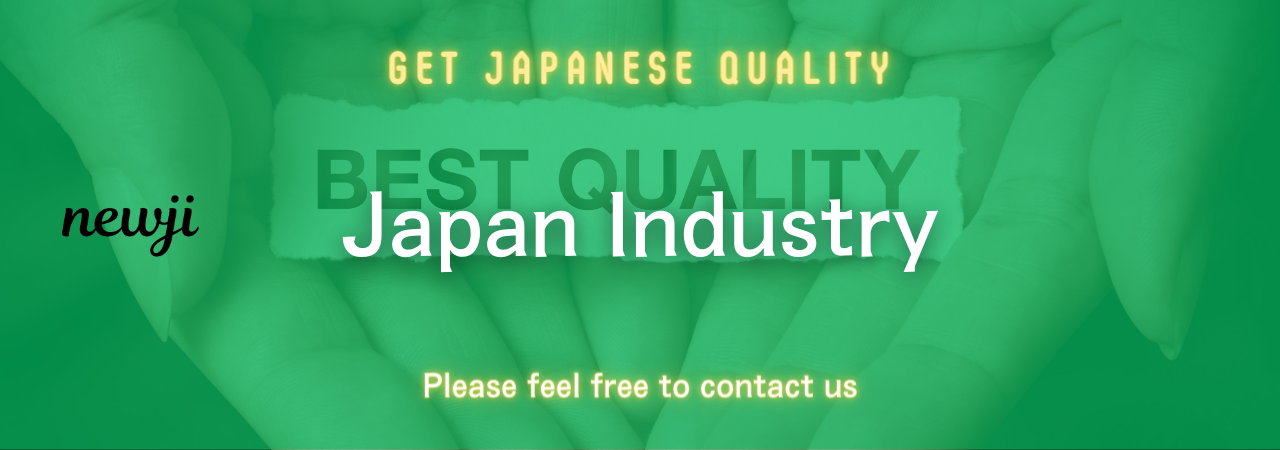
目次
Understanding the Importance of Collaboration
Collaborating between purchasing and logistics departments is crucial for any organization aiming to reduce transportation costs effectively.
Both departments play a vital role in resource management, cost efficiency, and ensuring that goods move smoothly from suppliers to customers.
While purchasing focuses on acquiring quality products at the best prices, logistics handles the movement, warehousing, and delivery of these products.
When these two departments work in sync, they can significantly reduce transportation costs.
This cooperation can lead to better supplier relationships, efficient inventory management, and streamlined shipping processes.
Identifying Common Goals
The first step in fostering collaboration is identifying and establishing common goals.
Both departments should aim to improve efficiency, reduce costs, and enhance customer satisfaction.
By aligning their objectives, purchasing and logistics teams can work towards a shared vision that benefits the entire organization.
Regular meetings should be held to discuss these goals and the strategies required to achieve them.
Clear communication opens the door for ideas and solutions that might not have been considered otherwise.
Streamlining Communication
Effective collaboration depends on clear and open communication channels between departments.
Both purchasing and logistics staff should have access to the same information and updates at all times.
This ensures that everyone is on the same page when making decisions that impact transportation costs.
Utilizing technology can greatly enhance communication.
Implementing a centralized system where both departments can access and share important information will prevent delays and misunderstandings.
Joint Meetings and Planning Sessions
Scheduling joint meetings and planning sessions helps in exchanging ideas and information.
These sessions create a forum where purchasing and logistics teams can discuss upcoming projects, potential challenges, and brainstorm solutions.
Collaborative decision-making processes enable both teams to consider each other’s insights and expertise.
Leveraging Technology and Data
In the modern business environment, data plays a significant role in decision-making.
Purchasing and logistics departments can use data to identify inefficiencies and find cost-saving opportunities.
Analytical tools can help forecast demand, optimize delivery routes, and plan purchase orders to coincide with optimal shipping schedules.
By leveraging technology, both departments can reduce transportation costs through informed planning and execution.
Using Integrated Software Solutions
Implementing integrated software solutions that tie together purchasing and logistics functions is crucial.
Such tools can help automate processes, reduce errors, and provide real-time insights into supply chain activities.
An integrated system ensures that all relevant data is available in one place and that both departments have a holistic view of operations.
Negotiating with Suppliers and Carriers
Another aspect of reducing transportation costs is negotiating effectively with suppliers and carriers.
Both purchasing and logistics teams must collaborate to establish favorable terms and seek alliances with suppliers who offer reliable, cost-effective shipping solutions.
Work together to create a standardized process for evaluating and selecting suppliers and carriers based on their performance, reliability, and cost-effectiveness.
This collaborative approach ensures that both departments maximize savings and enhance service quality.
Long-term Agreements and Strategic Partnerships
Building long-term agreements and strategic partnerships with key suppliers and carriers can result in substantial cost savings.
By consolidating shipment volumes and ensuring steady business for carriers, companies can negotiate better terms and receive prioritized services.
This strategy can also contribute to fostering strong relationships and increased leverage in future negotiations.
Enhancing Inventory Management
Efficient inventory management is key to controlling transportation costs.
Both purchasing and logistics must coordinate closely to balance inventory levels that minimize storage costs without causing stockouts or excess.
Strategies such as Just-In-Time (JIT) inventory systems can be explored to optimize inventory levels.
This collaboration requires both departments to accurately forecast demand, streamline order cycles, and arrange timely shipments to maintain the right amount of stock.
Minimizing Expedited Shipments
Expedited shipments are often a significant source of increased transportation costs.
When inventory is not managed correctly, companies may need to rush orders to meet delivery deadlines, leading to higher shipping expenses.
Collaborative inventory management helps avoid these situations by planning adequately and maintaining optimal inventory levels.
Performance Evaluation and Adjustments
Finally, continuous evaluation of collaborative efforts is necessary for long-term success.
Both departments should regularly review key performance indicators (KPIs), such as transportation cost per unit, order fulfillment rates, and supplier performance metrics.
Using KPI data, cross-functional teams can identify areas for improvement and make necessary adjustments to strategies and operations.
This iterative process of evaluation and enhancement ensures that transportation cost-cutting measures remain effective in the long term.
Celebrating Successes and Learning from Failures
Recognizing and celebrating achievements is important in maintaining motivation and continued collaboration between departments.
When set goals are met, acknowledging the teamwork and effort involved fosters an atmosphere of cooperation and a shared sense of accomplishment.
Conversely, analyzing failures or challenges encountered along the way provides learning opportunities.
Identifying what went wrong helps both departments adjust tactics and prevents future issues.
By maintaining a spirit of learning and collaboration, purchasing and logistics teams can continue to develop innovative solutions to minimize transportation costs.
資料ダウンロード
QCD調達購買管理クラウド「newji」は、調達購買部門で必要なQCD管理全てを備えた、現場特化型兼クラウド型の今世紀最高の購買管理システムとなります。
ユーザー登録
調達購買業務の効率化だけでなく、システムを導入することで、コスト削減や製品・資材のステータス可視化のほか、属人化していた購買情報の共有化による内部不正防止や統制にも役立ちます。
NEWJI DX
製造業に特化したデジタルトランスフォーメーション(DX)の実現を目指す請負開発型のコンサルティングサービスです。AI、iPaaS、および先端の技術を駆使して、製造プロセスの効率化、業務効率化、チームワーク強化、コスト削減、品質向上を実現します。このサービスは、製造業の課題を深く理解し、それに対する最適なデジタルソリューションを提供することで、企業が持続的な成長とイノベーションを達成できるようサポートします。
オンライン講座
製造業、主に購買・調達部門にお勤めの方々に向けた情報を配信しております。
新任の方やベテランの方、管理職を対象とした幅広いコンテンツをご用意しております。
お問い合わせ
コストダウンが利益に直結する術だと理解していても、なかなか前に進めることができない状況。そんな時は、newjiのコストダウン自動化機能で大きく利益貢献しよう!
(Β版非公開)