- お役立ち記事
- How to promote kaizen activities and best practices in quality control in manufacturing
月間77,185名の
製造業ご担当者様が閲覧しています*
*2025年2月28日現在のGoogle Analyticsのデータより
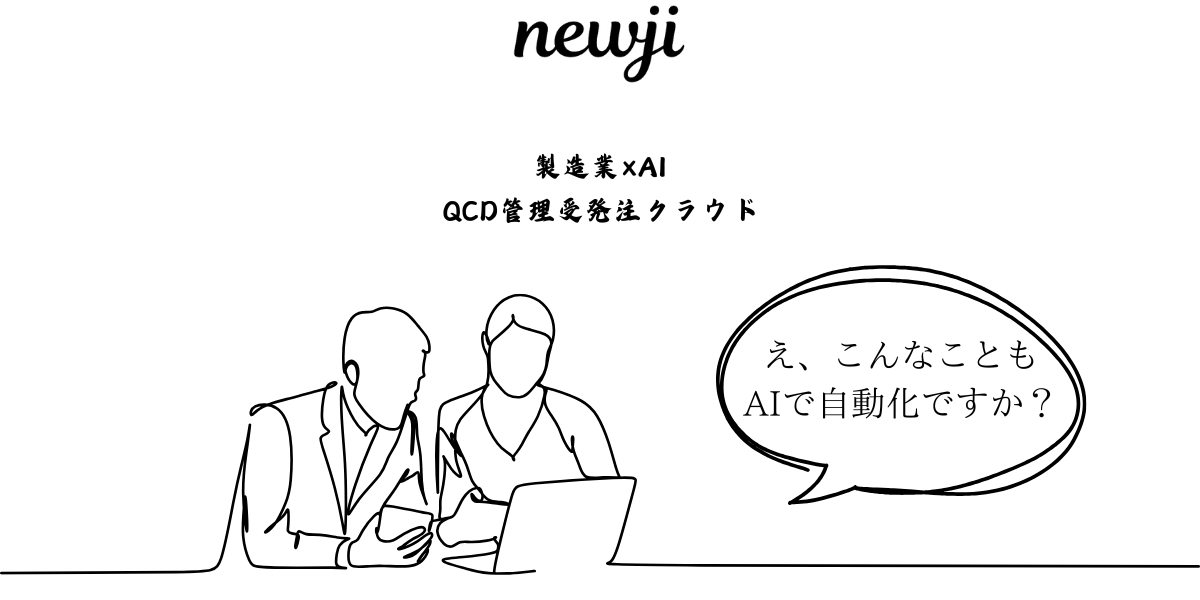
How to promote kaizen activities and best practices in quality control in manufacturing
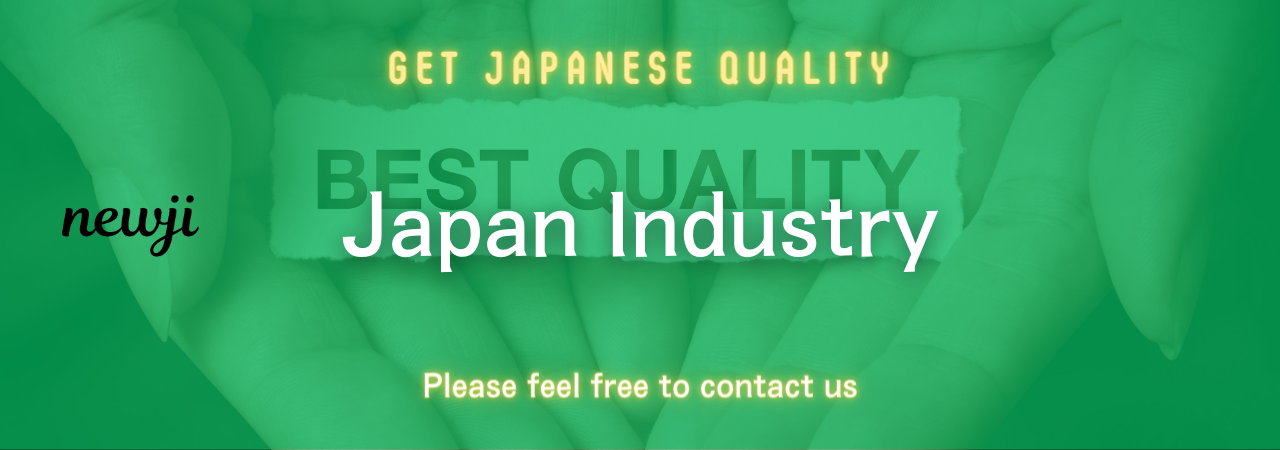
Kaizen, a Japanese term meaning “continuous improvement,” has become a cornerstone for quality control in manufacturing industries worldwide. This philosophy focuses on small, incremental changes that lead to big improvements over time. By integrating Kaizen activities, manufacturers can enhance efficiency, reduce waste, and elevate product quality. Here’s how to promote Kaizen activities and follow best practices in quality control in the manufacturing sector.
目次
Understanding the Principle of Kaizen
Kaizen is built on five foundational elements: teamwork, personal discipline, improved morale, quality circles, and suggestions for improvement. The goal is not to make dramatic changes all at once but to continuously make small improvements. This leads to sustainable, long-term benefits.
Steps to Promote Kaizen Activities
Develop a Kaizen Mindset
Creating a culture that embraces continuous improvement starts at the top. Leadership should openly support Kaizen principles and emphasize their importance. By setting an example, managers can foster an environment where employees feel encouraged to seek out small changes continually.
Employee Training
Employees need to understand how to implement Kaizen effectively. Providing regular training sessions can equip them with the tools and knowledge necessary to identify areas for improvement. Consider adopting workshops, seminars, and even online courses. Provide examples of successful Kaizen initiatives to inspire and illustrate its practical applications.
Establish Quality Circles
Quality circles are small groups of employees who meet regularly to discuss and solve workplace issues. These circles empower employees to be part of the decision-making process and contribute their unique perspectives. This collaborative approach often leads to more innovative solutions and encourages team-building.
Create an Open Communication Environment
For Kaizen to thrive, communication must be transparent and open. Encourage employees to speak up if they identify any inefficiencies or areas for improvement. Establishing suggestion boxes or digital platforms for feedback can also facilitate open communication. Recognize and reward valuable contributions to keep the momentum going.
Measure and Analyze
Consistently track and measure the outcomes of your Kaizen activities. Use metrics and key performance indicators (KPIs) to assess the effectiveness of implemented changes. This data-driven approach can help in fine-tuning processes and ensuring that improvements are aligned with overarching business goals.
Best Practices for Quality Control
Implement a Robust Quality Management System (QMS)
A Quality Management System, or QMS, serves as the backbone of quality control in manufacturing. It outlines the policies, procedures, and responsibilities needed to achieve quality objectives. Popular schemes like ISO 9001 offer a framework that manufacturing plants can tailor to their specific needs.
Regular Audits and Inspections
Frequent audits and inspections play a vital role in maintaining high-quality standards. Schedule both internal and external audits to ensure adherence to quality protocols. These assessments can identify weaknesses in your processes, providing opportunities for further Kaizen activities.
Employee Involvement
Similar to Kaizen, quality control thrives on employee involvement. Ensure employees understand the importance of quality and their role in maintaining it. Regularly update them on quality metrics and goals. Employee involvement in quality assessments can provide fresh insights and enhance overall performance.
Utilize Advanced Technologies
Technology can significantly augment quality control measures. From automated inspection systems to real-time data analytics, modern tools can provide precise and timely information. Investing in technologies like AI and IoT can offer a competitive edge in maintaining high-quality standards.
Supplier Quality Management
Suppliers play a crucial role in the quality of the final product. Implement a supplier quality management program to ensure they adhere to your quality standards. Regularly evaluate their performance through scorecards and audits. Building strong, mutually beneficial relationships with suppliers can lead to consistent quality and reduced risk of defects.
Integrating Kaizen with Quality Control
Continuous Improvement Programs
Marrying Kaizen with your QMS can create a powerful, continuous improvement program. Use quality control data to inform Kaizen activities. For instance, if a metric reveals a drop in product quality, initiate a Kaizen event focused on that specific area to investigate and resolve the issue.
Routine Problem-Solving
Develop a habit of routine problem-solving meetings. These sessions should involve team members from various departments. The diverse expertise can lead to more holistic solutions. Utilize tools like the Plan-Do-Check-Act (PDCA) cycle to monitor the effectiveness of implemented changes.
Documentation and Standardization
Documenting Kaizen activities and outcomes helps in standardizing successful practices. This can then be shared across departments and even different plant locations. Standardization ensures that improvements are uniformly implemented, maximizing their benefits.
Feedback Loops
Feedback loops are crucial for both Kaizen and quality control. Regularly collect feedback on both implemented changes and existing processes. This ongoing dialogue can highlight new areas for improvement and validate the effectiveness of past initiatives.
Case Studies: Successful Kaizen in Manufacturing
Toyota
Toyota is a prime example of Kaizen in action. The company’s renowned “Toyota Production System” incorporates Kaizen as a core element. Employees at all levels are encouraged to suggest improvements, leading to innovations such as Just-In-Time manufacturing and Jidoka, which enhances automation without compromising quality.
Nissan
Another great example is Nissan. The automaker employs quality circles and Kaizen events to continuously refine its manufacturing processes. This has resulted in reduced production times, lower costs, and significantly improved vehicle quality.
Conclusion
Embracing Kaizen and adhering to best practices in quality control can transform your manufacturing operations. By fostering a culture of continuous improvement, involving employees in the process, and leveraging modern technologies, you can achieve sustainable growth and superior product quality. Start small, stay consistent, and witness the remarkable changes that Kaizen can bring to your manufacturing processes.
資料ダウンロード
QCD管理受発注クラウド「newji」は、受発注部門で必要なQCD管理全てを備えた、現場特化型兼クラウド型の今世紀最高の受発注管理システムとなります。
ユーザー登録
受発注業務の効率化だけでなく、システムを導入することで、コスト削減や製品・資材のステータス可視化のほか、属人化していた受発注情報の共有化による内部不正防止や統制にも役立ちます。
NEWJI DX
製造業に特化したデジタルトランスフォーメーション(DX)の実現を目指す請負開発型のコンサルティングサービスです。AI、iPaaS、および先端の技術を駆使して、製造プロセスの効率化、業務効率化、チームワーク強化、コスト削減、品質向上を実現します。このサービスは、製造業の課題を深く理解し、それに対する最適なデジタルソリューションを提供することで、企業が持続的な成長とイノベーションを達成できるようサポートします。
製造業ニュース解説
製造業、主に購買・調達部門にお勤めの方々に向けた情報を配信しております。
新任の方やベテランの方、管理職を対象とした幅広いコンテンツをご用意しております。
お問い合わせ
コストダウンが利益に直結する術だと理解していても、なかなか前に進めることができない状況。そんな時は、newjiのコストダウン自動化機能で大きく利益貢献しよう!
(β版非公開)