- お役立ち記事
- How to Provide High-Performance Ceramic Parts with Ceramic OEM Manufacturing
How to Provide High-Performance Ceramic Parts with Ceramic OEM Manufacturing
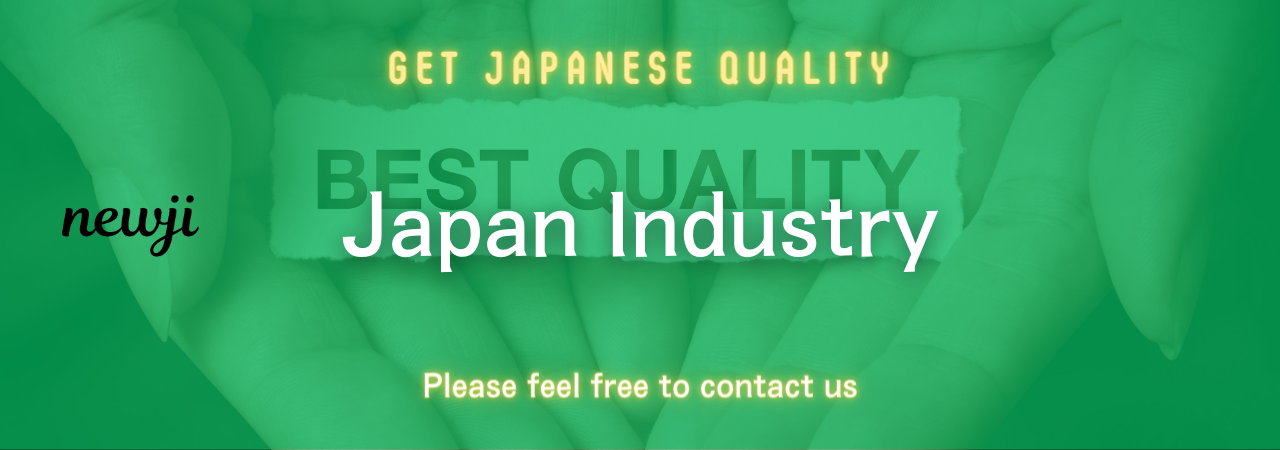
Ceramic parts have transformed the landscape of manufacturing, offering remarkable benefits such as high durability, thermal resistance, and exceptional strength.
In this article, we explore how to achieve high-performance ceramic parts through Ceramic OEM (Original Equipment Manufacturer) manufacturing.
目次
Understanding Ceramic OEM Manufacturing
Ceramic OEM manufacturing involves producing ceramic components tailored to the specifications and requirements of different industries.
This process ensures that the end product meets the highest standards of quality and performance.
But what exactly does it entail?
Let’s break it down!
Material Selection
The first step in Ceramic OEM manufacturing revolves around selecting the right type of ceramic material.
Common materials include alumina, zirconia, silicon carbide, and silicon nitride.
Each material offers unique properties suitable for specific applications.
For example, alumina is known for its electrical insulation properties, while silicon carbide boasts high thermal conductivity.
Design and Prototyping
Once the material is selected, the next phase is design and prototyping.
Engineers and designers work together to create a blueprint of the desired ceramic part.
CAD (Computer-Aided Design) software is commonly used to develop detailed designs.
Once the design is finalized, prototypes are manufactured for testing.
This step is crucial to ensure the part meets all required specifications and functions correctly.
Manufacturing Techniques
Ceramic parts can be manufactured using various techniques, each suited to different types of ceramics and applications.
Common techniques include:
Powder Processing
This method involves grinding ceramic materials into fine powder.
The powder is then shaped and sintered at high temperatures to produce dense, high-strength ceramic parts.
Injection Molding
In this technique, ceramic powder is mixed with a binder to create a feedstock.
The feedstock is then injected into molds under high pressure to form the desired shape.
Hot Pressing
Hot pressing combines high pressure and high temperature to shape the ceramic material.
This technique is effective in producing ceramic parts with superior density and strength.
Isostatic Pressing
Isostatic pressing uses uniform pressure applied from all directions to form ceramic parts.
This method is ideal for creating complex shapes and ensuring consistent density throughout the material.
Quality Control and Testing
Quality control is a critical aspect of Ceramic OEM manufacturing.
Rigorous testing ensures that each ceramic part meets the required standards.
Dimensional Inspection
Dimensional inspection involves measuring the physical dimensions of the ceramic part to ensure it matches the design specifications.
Tools like calipers, micrometers, and CMM (Coordinate Measuring Machine) are commonly used.
Material Testing
Material testing assesses the properties of the ceramic material, such as hardness, density, and thermal conductivity.
These tests ensure the material meets the required quality standards for the intended application.
Performance Testing
Performance testing involves assessing the ceramic part under simulated operational conditions.
This may include tests for wear resistance, thermal stability, and mechanical strength.
Applications of High-Performance Ceramic Parts
High-performance ceramic parts play a crucial role in numerous industries.
Here are some common applications:
Aerospace and Defense
In the aerospace and defense industries, ceramic parts are used in components like heat shields, engine parts, and armor.
Their high thermal resistance and strength make them ideal for extreme conditions.
Electronics and Semiconductors
Ceramic materials are excellent electrical insulators.
They are often used in electronic components like circuit boards, capacitors, and resistors to ensure reliable performance.
Medical Devices
Ceramic materials are biocompatible, making them suitable for medical implants, dental crowns, and prosthetics.
Their durability and compatibility with human tissue are significant advantages.
Automotive Industry
In the automotive industry, ceramic parts are used in components like brake pads, spark plugs, and catalytic converters.
Their ability to withstand high temperatures and reduce wear is essential for automotive applications.
Benefits of Ceramic OEM Manufacturing
Ceramic OEM manufacturing offers several benefits that contribute to the production of high-performance parts.
Customization
One of the most significant benefits of Ceramic OEM manufacturing is the ability to customize parts to meet specific requirements.
This ensures that each component is designed and manufactured to fit its intended application perfectly.
High Precision
Ceramic OEM manufacturing techniques allow for high precision and accuracy, ensuring that each part meets the exact design specifications.
This level of precision is critical, especially for applications that require tight tolerances.
Cost-Effectiveness
While ceramic materials can be expensive, Ceramic OEM manufacturing can be cost-effective in the long run.
The durability and longevity of ceramic parts mean fewer replacements and maintenance, leading to cost savings.
Performance and Reliability
Ceramic parts manufactured through Ceramic OEM processes offer superior performance and reliability.
Their unique properties, such as high thermal resistance, electrical insulation, and mechanical strength, make them ideal for demanding applications.
Conclusion
Ceramic OEM manufacturing is a complex yet efficient process that ensures the production of high-performance ceramic parts.
From material selection to quality control and testing, each step is crucial in delivering top-notch components.
As we have seen, these parts find applications across a range of industries, owing to their exceptional properties and reliability.
If you are looking to leverage the benefits of high-performance ceramic parts, understanding and utilizing Ceramic OEM manufacturing is the key.
資料ダウンロード
QCD調達購買管理クラウド「newji」は、調達購買部門で必要なQCD管理全てを備えた、現場特化型兼クラウド型の今世紀最高の購買管理システムとなります。
ユーザー登録
調達購買業務の効率化だけでなく、システムを導入することで、コスト削減や製品・資材のステータス可視化のほか、属人化していた購買情報の共有化による内部不正防止や統制にも役立ちます。
NEWJI DX
製造業に特化したデジタルトランスフォーメーション(DX)の実現を目指す請負開発型のコンサルティングサービスです。AI、iPaaS、および先端の技術を駆使して、製造プロセスの効率化、業務効率化、チームワーク強化、コスト削減、品質向上を実現します。このサービスは、製造業の課題を深く理解し、それに対する最適なデジタルソリューションを提供することで、企業が持続的な成長とイノベーションを達成できるようサポートします。
オンライン講座
製造業、主に購買・調達部門にお勤めの方々に向けた情報を配信しております。
新任の方やベテランの方、管理職を対象とした幅広いコンテンツをご用意しております。
お問い合わせ
コストダウンが利益に直結する術だと理解していても、なかなか前に進めることができない状況。そんな時は、newjiのコストダウン自動化機能で大きく利益貢献しよう!
(Β版非公開)