- お役立ち記事
- How to Provide High-Performance Electronic Components with Diode OEM Manufacturing
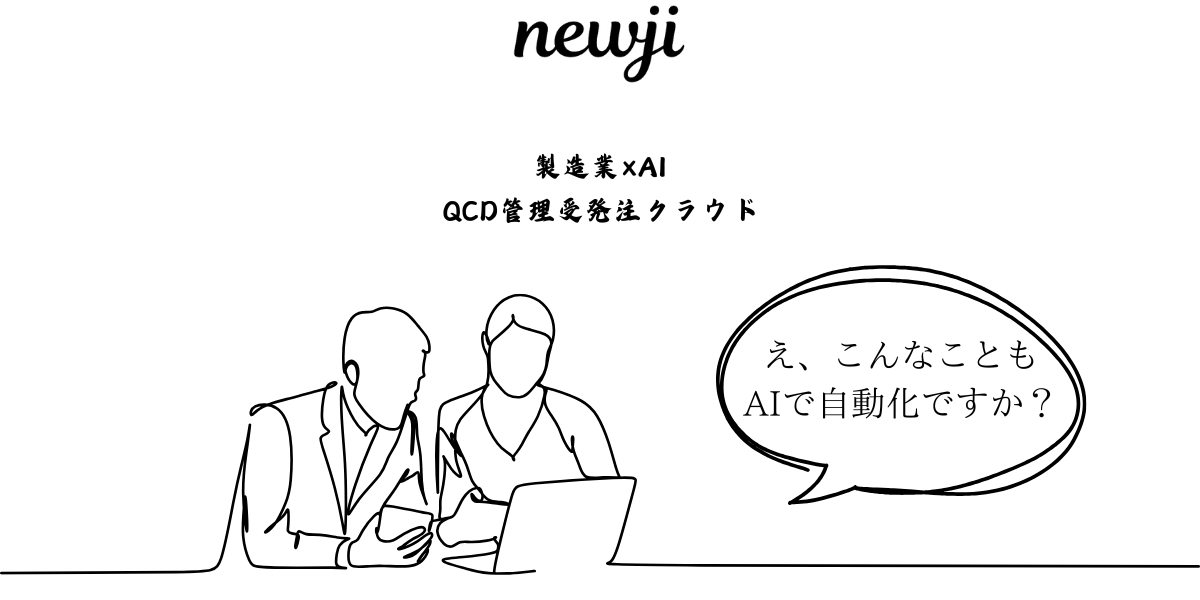
How to Provide High-Performance Electronic Components with Diode OEM Manufacturing
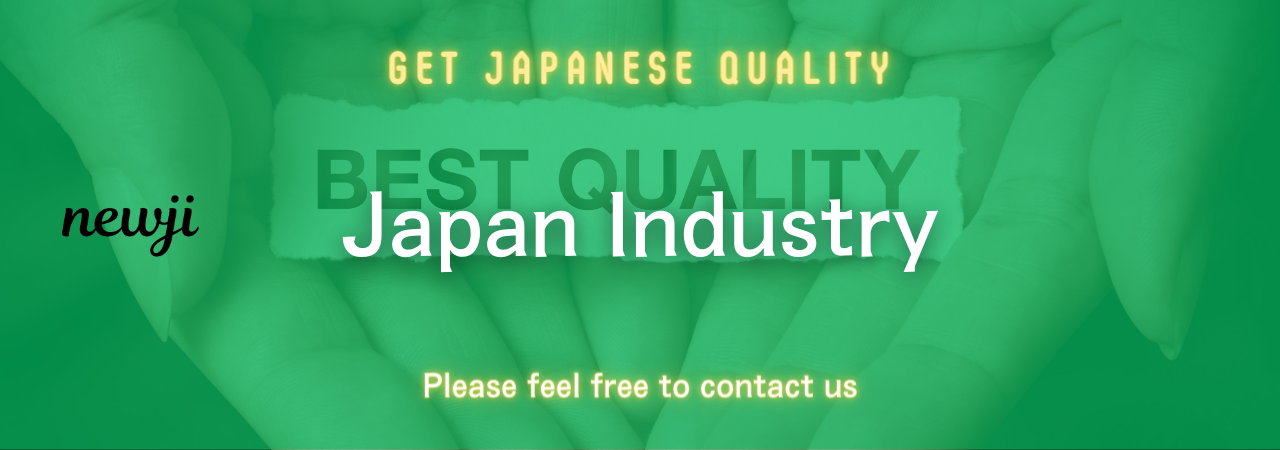
Understanding the Basics of Diode OEM Manufacturing
To deliver high-performance electronic components, it is essential first to grasp the fundamentals of diode OEM manufacturing.
An Original Equipment Manufacturer (OEM) leverages their expertise to craft electronic parts, which include diodes, that get supplied to other companies.
These diodes then get integrated into larger systems or products.
Understanding these basic concepts is crucial as we delve deeper into the different aspects of providing top-notch components.
目次
What Makes a Diode High-Performance?
Diodes are integral parts of many electronic devices.
They allow current to flow in one direction while blocking it in the opposite direction.
High-performance diodes are characterized by low power loss, fast switching capabilities, and high reliability.
Factors such as breakdown voltage, forward voltage drop, and maximum current rating play essential roles in determining the performance of a diode.
Breakdown Voltage
The breakdown voltage of a diode is the maximum reverse voltage a diode can handle before it starts conducting in the reverse direction.
High-performance diodes usually have a higher breakdown voltage.
This ensures that the diode can withstand significant electrical stress without failing.
Forward Voltage Drop
The forward voltage drop is the voltage loss experienced when current passes through the diode in the intended direction.
Lower forward voltage drops are desirable in high-performance diodes because they indicate lower energy loss.
Maximum Current Rating
This specifies the maximum current the diode can carry without damage.
Higher current ratings are generally associated with high-performance diodes as they can operate reliably under more demanding conditions.
The Importance of Quality in Diode OEM Manufacturing
Quality is a critical aspect of diode OEM manufacturing.
When dealing with electronic components, even a small defect can result in a device’s malfunction.
To ensure high performance, diodes must undergo rigorous quality control at various stages of production.
Material Selection
High-quality materials contribute significantly to the performance and reliability of diodes.
Manufacturers often select materials like silicon or gallium arsenide, which offer desirable electrical properties.
Manufacturing Precision
Precision during the manufacturing process ensures that the diodes perform as expected.
Employing advanced manufacturing techniques ensures that each diode meets the stringent specifications required for high-performance applications.
Testing and Validation
Before diodes reach the market, they must undergo extensive testing.
These tests ensure that the diodes meet all specified parameters and can perform under various conditions.
Validation helps in identifying any potential issues before the product reaches the end customer.
Steps to Improve Diode OEM Manufacturing Performance
Invest in Research and Development
Continual research and development can lead to innovative solutions and improvements in diode technology.
Investing in R&D allows manufacturers to stay ahead of industry trends and develop advanced high-performance diodes.
Upgrade Manufacturing Equipment
Employing state-of-the-art manufacturing equipment ensures high precision and better control over the production process.
Modern equipment can also lead to higher efficiency and reduced production costs.
Implement Robust Quality Control Systems
A robust quality control system detects anomalies early in the production process.
It ensures that defective products do not proceed to later stages, thus reducing waste and improving overall product quality.
The Role of Customization in High-Performance Diode OEM Manufacturing
Customization plays a significant role in meeting specific industry requirements.
Different applications may have unique needs, which can be addressed through tailored diode solutions.
Understanding Client Needs
Establishing clear communication with clients helps in understanding their specific requirements.
This information helps in designing and manufacturing diodes that meet the exact needs of their applications.
Prototyping and Feedback
Before full-scale production, creating prototypes and seeking client feedback can lead to better end products.
This iterative process helps in refining the design and manufacturing process.
Flexibility in Production
Being flexible in production allows manufacturers to accommodate custom orders efficiently.
This includes adjusting production schedules and techniques to meet the client’s demands without compromising on quality.
Sustainability in Diode OEM Manufacturing
Sustainability is becoming increasingly crucial in manufacturing industries.
Implementing eco-friendly practices not only benefits the environment but also can lead to cost savings and a better brand image.
Energy-Efficient Processes
Utilizing energy-efficient manufacturing processes reduces the overall environmental impact and lowers costs.
This can include optimizing machinery to consume less energy or implementing renewable energy sources within the production facility.
Material Recycling
Recycling materials wherever possible reduces waste and conserves resources.
Implementing a closed-loop system ensures that as much material as possible gets reused in the production process.
Compliance with Regulations
Adhering to environmental regulations is non-negotiable.
Ensuring compliance with local and international standards helps in maintaining a good reputation and avoiding legal repercussions.
The Future of Diode OEM Manufacturing
The future of diode OEM manufacturing holds promise with advancements in technology and materials.
As industries evolve, the demand for more efficient, reliable, and customized diodes will continue to grow.
Emerging Technologies
Technological advancements such as quantum computing and artificial intelligence offer new opportunities for diode applications and manufacturing processes.
Staying at the forefront of these technologies can give manufacturers a competitive edge.
Industry Collaboration
Collaborating with other industry players and academic institutions can lead to innovative solutions and advancements.
Pooling resources and knowledge can speed up the development of next-generation diodes.
Continuous Improvement
Commitment to continuous improvement ensures that manufacturers do not become complacent.
Regularly assessing processes, technologies, and market trends can lead to ongoing enhancements in product quality and performance.
In conclusion, providing high-performance electronic components through diode OEM manufacturing involves a meticulous focus on quality, innovation, and customization.
By understanding the fundamentals and constantly improving processes, manufacturers can meet the ever-increasing demands of the modern electronics industry.
資料ダウンロード
QCD調達購買管理クラウド「newji」は、調達購買部門で必要なQCD管理全てを備えた、現場特化型兼クラウド型の今世紀最高の購買管理システムとなります。
ユーザー登録
調達購買業務の効率化だけでなく、システムを導入することで、コスト削減や製品・資材のステータス可視化のほか、属人化していた購買情報の共有化による内部不正防止や統制にも役立ちます。
NEWJI DX
製造業に特化したデジタルトランスフォーメーション(DX)の実現を目指す請負開発型のコンサルティングサービスです。AI、iPaaS、および先端の技術を駆使して、製造プロセスの効率化、業務効率化、チームワーク強化、コスト削減、品質向上を実現します。このサービスは、製造業の課題を深く理解し、それに対する最適なデジタルソリューションを提供することで、企業が持続的な成長とイノベーションを達成できるようサポートします。
オンライン講座
製造業、主に購買・調達部門にお勤めの方々に向けた情報を配信しております。
新任の方やベテランの方、管理職を対象とした幅広いコンテンツをご用意しております。
お問い合わせ
コストダウンが利益に直結する術だと理解していても、なかなか前に進めることができない状況。そんな時は、newjiのコストダウン自動化機能で大きく利益貢献しよう!
(Β版非公開)