- お役立ち記事
- How to Provide High-Precision Casting Parts with Die Casting Mold OEM Manufacturing
How to Provide High-Precision Casting Parts with Die Casting Mold OEM Manufacturing
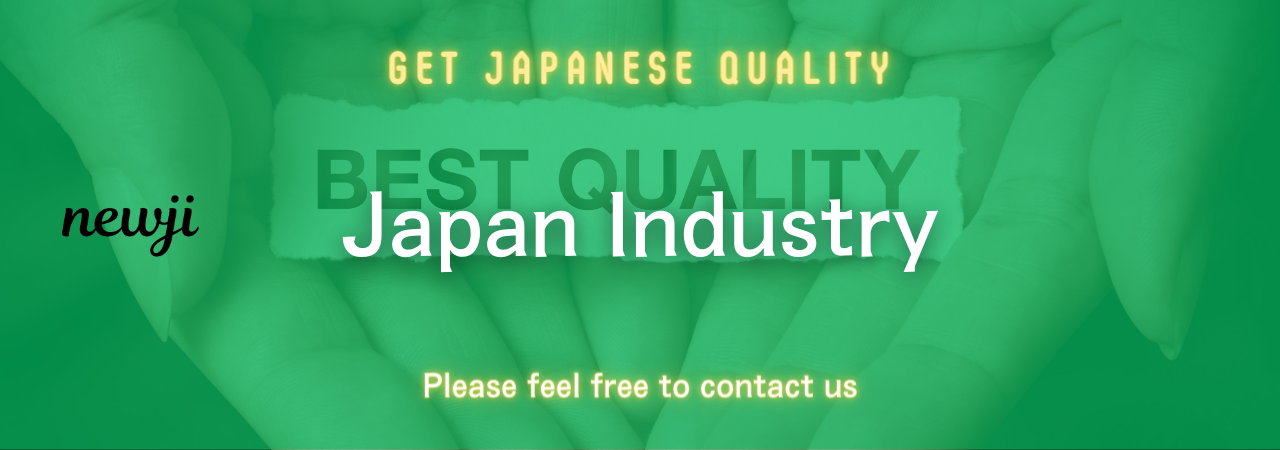
Die casting is a popular manufacturing process, known for its ability to produce high-precision parts. These parts are critical components in many industries, ranging from automotive to electronics. In this article, we’ll delve into how to provide high-precision casting parts using die casting mold OEM manufacturing.
目次
Understanding Die Casting
Die casting is a metal casting process wherein molten metal is forced under high pressure into a mold cavity. The molds, known as dies, are reusable and can produce intricate parts with superb detail. The process is highly efficient and produces parts that require little to no machining.
Types of Die Casting
There are primarily two types of die casting methods: hot-chamber and cold-chamber die casting.
Hot-chamber die casting is ideal for metals with low melting points, such as zinc.
Cold-chamber die casting is used for metals with higher melting points, like aluminum and magnesium.
Understanding the differences between these methods is crucial in selecting the appropriate process for manufacturing high-precision parts.
The Role of Die Casting Mold OEM Manufacturing
OEM (Original Equipment Manufacturer) die casting mold manufacturing involves creating custom molds tailored to specific parts. The precision and quality of the molds are paramount to the final product’s accuracy and durability.
Designing the Mold
The first step in providing high-precision casting parts is designing the mold. Engineers utilize advanced CAD (Computer-Aided Design) software to create detailed mold designs.
The design process involves several considerations:
1. **Material Selection**: Different metals have varying properties, such as melting points and thermal conductivity. Choosing the right metal for both the mold and the casting is crucial.
2. **Tolerance Levels**: High-precision parts require dies designed to very tight tolerances. This ensures that the parts produced are accurate and consistent in their dimensions.
3. **Cooling Channels**: Efficient cooling is vital in die casting. Properly designed cooling channels reduce cycle time and prevent defects like warping.
4. **Ejection Mechanisms**: These mechanisms ensure that the cast parts are ejected smoothly without damage.
Prototype Testing
Before mass production, it’s essential to create prototypes and test them rigorously. This step helps identify potential issues early on.
Engineers can make any necessary adjustments to the mold design and the casting process based on these tests.
Quality Control
Quality control is vital to ensure that the high-precision casting parts meet the required standards.
Optimizing the Die Casting Process
For high-precision casting parts, optimizing every stage of the die casting process is essential.
Maintaining Uniform Temperature
Uniform temperature control during the process helps in achieving consistency.
Temperature variations can lead to defects like shrinkage, so it’s critical to maintain the appropriate and uniform temperature.
Using Advanced Materials
Advances in metallurgy have introduced high-strength materials that enhance the quality of the casting parts.
These materials provide better resistance to wear and tear, ensuring longer mold life and higher-quality parts.
Automation and Monitoring
Modern die casting facilities use automation to enhance precision and efficiency.
Automated systems ensure consistent metal injection, reducing human error. Continuous monitoring of the casting parameters helps in early detection of any deviations, allowing for immediate corrections.
Post-Production Processes
Once the parts are cast, several post-production processes ensure that they meet the necessary specifications.
Trimming
After casting, excess material, known as flash, needs to be trimmed off. Trimming is done using trimming presses or other cutting tools to ensure clean and accurate edges.
Machining
In some instances, machining is necessary to achieve the final dimensions and surface finish. CNC (Computer Numerical Control) machines are often utilized for this purpose, as they provide high precision and repeatability.
Surface Treatment
Surface treatments, such as polishing, painting, or coating, enhance the appearance and functionality of the casting parts. These treatments can also provide additional protection against corrosion and wear.
Ensuring High-Precision in Mass Production
When moving to mass production, maintaining consistency and precision for every part is a challenge.
Strict Process Controls
Implementing strict process controls helps in maintaining the integrity of the casting parts. Regular inspections and audits of the casting process ensure that it remains within the specified parameters.
Employee Training
Well-trained employees are essential to the success of a die casting operation. Continuous training programs ensure that workers are knowledgeable about the latest techniques and quality standards.
Investing in Technology
Investing in the latest technology is crucial for maintaining high precision in mass production. Advanced die casting machines with real-time monitoring and feedback systems enhance accuracy and efficiency.
Benefits of High-Precision Die Casting Parts
High-precision casting parts offer numerous benefits across various industries.
Enhanced Performance
Precision parts fit better and function more efficiently in assemblies. This leads to better overall performance of the final product.
Cost Savings
Although high-precision molds and processes might have higher initial costs, they lead to significant savings in the long run. These savings come from reduced wastage, lesser need for rework, and fewer defects.
Increased Reliability
Products made with high-precision parts are generally more reliable and have longer lifespans. This is particularly important in industries like automotive and aerospace, where reliability is critical.
Providing high-precision casting parts with die casting mold OEM manufacturing involves a meticulous design process, rigorous testing, and strict quality control. By optimizing every stage of the process and investing in advanced technologies, manufacturers can achieve the high levels of precision required for modern applications. This not only enhances the performance and reliability of the final products but also offers significant cost benefits.
資料ダウンロード
QCD調達購買管理クラウド「newji」は、調達購買部門で必要なQCD管理全てを備えた、現場特化型兼クラウド型の今世紀最高の購買管理システムとなります。
ユーザー登録
調達購買業務の効率化だけでなく、システムを導入することで、コスト削減や製品・資材のステータス可視化のほか、属人化していた購買情報の共有化による内部不正防止や統制にも役立ちます。
NEWJI DX
製造業に特化したデジタルトランスフォーメーション(DX)の実現を目指す請負開発型のコンサルティングサービスです。AI、iPaaS、および先端の技術を駆使して、製造プロセスの効率化、業務効率化、チームワーク強化、コスト削減、品質向上を実現します。このサービスは、製造業の課題を深く理解し、それに対する最適なデジタルソリューションを提供することで、企業が持続的な成長とイノベーションを達成できるようサポートします。
オンライン講座
製造業、主に購買・調達部門にお勤めの方々に向けた情報を配信しております。
新任の方やベテランの方、管理職を対象とした幅広いコンテンツをご用意しております。
お問い合わせ
コストダウンが利益に直結する術だと理解していても、なかなか前に進めることができない状況。そんな時は、newjiのコストダウン自動化機能で大きく利益貢献しよう!
(Β版非公開)