- お役立ち記事
- How to Provide High-Quality Pulse Oximeters in OEM Manufacturing
月間76,176名の
製造業ご担当者様が閲覧しています*
*2025年3月31日現在のGoogle Analyticsのデータより
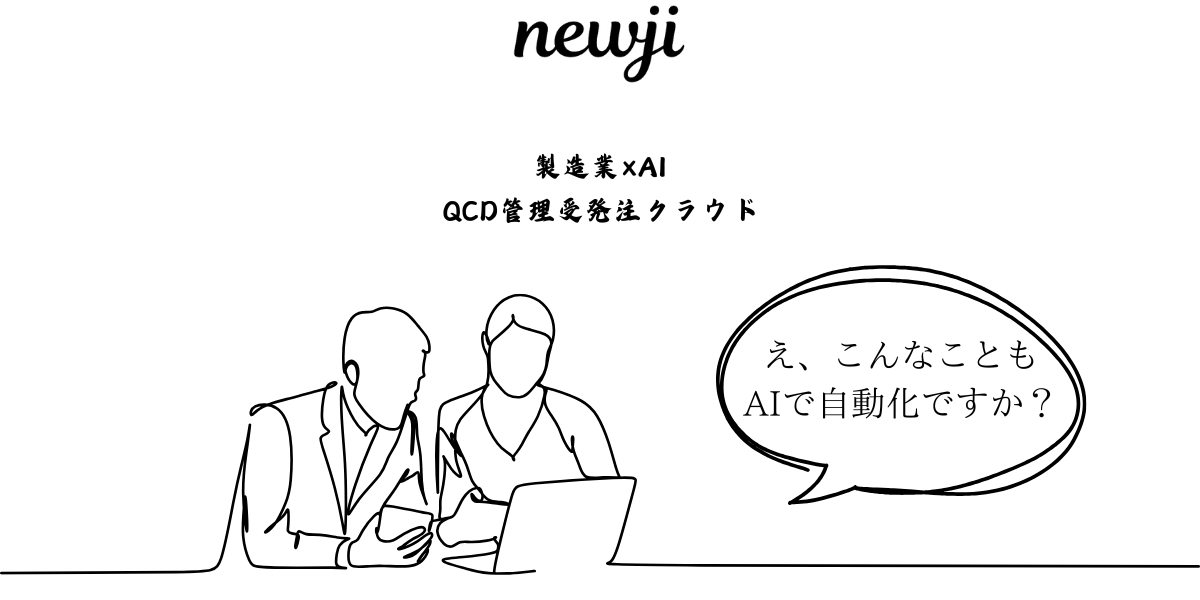
How to Provide High-Quality Pulse Oximeters in OEM Manufacturing
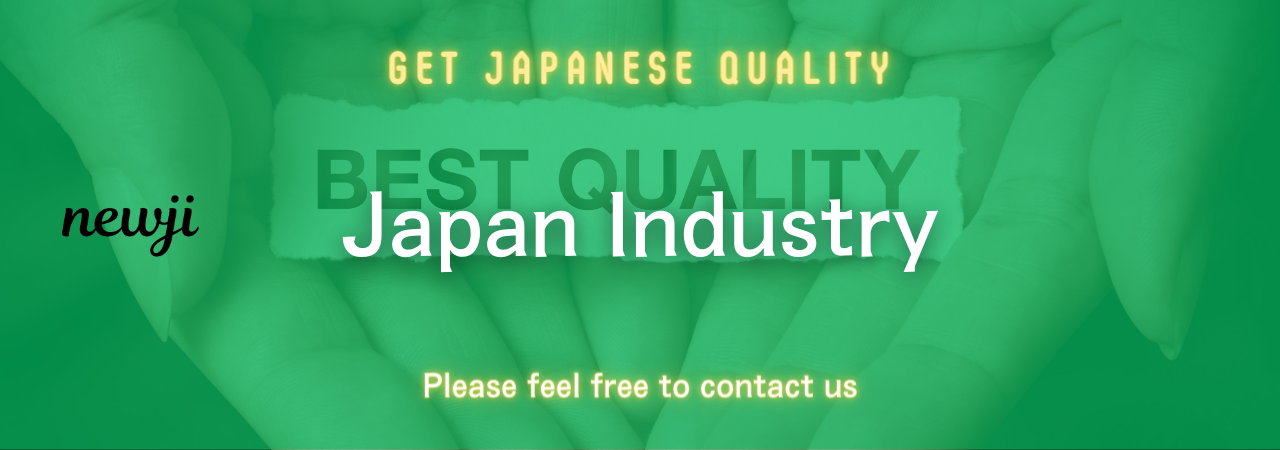
Providing high-quality pulse oximeters in OEM manufacturing involves several critical steps, ranging from design and development to quality control and customer service.
Each step in this comprehensive process plays a crucial role in ensuring the end product’s reliability and efficiency.
Here’s a detailed look into how you can achieve this:
目次
Understanding the Basics of Pulse Oximeters
Pulse oximeters are medical devices that measure the oxygen saturation level in a person’s blood.
They are crucial in various medical settings, helping to monitor the health of patients with conditions affecting oxygen levels.
Understanding the basic functionality and importance of these devices is the first step in manufacturing high-quality products.
Components of a Pulse Oximeter
A typical pulse oximeter consists of a sensor, a display unit, and a processor.
The sensor uses light to detect the oxygen level, while the processor analyzes this data and the display unit presents it to the user.
Each component needs to be chosen and integrated carefully to ensure the device’s accuracy and reliability.
Design and Development
The design and development phase is critical in OEM manufacturing of pulse oximeters.
Starting with a clear blueprint that outlines all specifications and requirements is essential.
Prototyping and Testing
Developing a prototype allows manufacturers to test the design and functionality before mass production begins.
It’s crucial to conduct rigorous testing at this stage to identify and rectify any potential issues.
Compliance with Regulations
Pulse oximeters must comply with various medical regulations and standards.
Ensuring that the design meets these standards is vital.
This includes certifications from relevant authorities, such as the FDA (Food and Drug Administration) in the United States or CE marking in Europe.
Material Selection
Choosing the right materials for the components is another key aspect.
Materials should not only meet safety and quality standards but also contribute to the durability and efficiency of the device.
Safe and Non-Toxic Materials
Materials used must be safe and non-toxic, as they come in direct contact with the human body.
Using biocompatible materials minimizes the risk of allergic reactions or other adverse effects.
Durable and Reliable Materials
Durability is crucial in medical devices.
Selecting materials that are robust and can withstand regular use without deteriorating ensures the longevity and reliability of the pulse oximeter.
Quality Control
Consistent quality control measures are fundamental in manufacturing high-quality pulse oximeters.
Implementing stringent quality control processes at every stage of production helps maintain high standards.
In-Process Quality Checks
Conducting quality checks during various stages of production helps identify defects early.
This minimizes waste and ensures that only high-quality products proceed to the next stage.
Final Product Testing
Before the pulse oximeters are dispatched, final product testing is essential.
This includes testing the sensors, processors, and display units to ensure they function correctly and meet the required standards.
Technology Integration
Incorporating advanced technology enhances the functionality and user experience of pulse oximeters.
Investing in the latest technology not only improves the product but also gives you a competitive edge.
Advanced Sensors
Using advanced sensors that offer higher accuracy and reliability ensures that the pulse oximeters provide precise readings.
It’s also beneficial to invest in sensors that are less prone to interference.
Wireless Connectivity
Incorporating wireless connectivity options, such as Bluetooth or Wi-Fi, allows pulse oximeters to connect with other medical devices or smartphones.
This feature enhances monitoring and data management capabilities.
Customer Service and Support
Beyond manufacturing, providing exceptional customer service and support is essential.
Offering assistance and addressing any issues customers may face helps build trust and ensures customer satisfaction.
User Manuals and Training
Providing comprehensive user manuals and training ensures that users can operate the pulse oximeters correctly.
This minimizes misuse and enhances the effectiveness of the device.
After-Sales Support
Offering reliable after-sales support, including warranties and repair services, helps maintain customer trust.
Being responsive to customer needs and resolving any issues promptly enhances the overall user experience.
Conclusion
Successfully providing high-quality pulse oximeters in OEM manufacturing involves a meticulous and integrated approach.
From understanding the basics and focusing on design and development, to ensuring stringent quality control and providing exceptional customer service, each step is interconnected.
By paying attention to every detail and continuously improving the process, manufacturers can deliver reliable and efficient pulse oximeters that meet high standards and satisfy customer needs.
資料ダウンロード
QCD管理受発注クラウド「newji」は、受発注部門で必要なQCD管理全てを備えた、現場特化型兼クラウド型の今世紀最高の受発注管理システムとなります。
ユーザー登録
受発注業務の効率化だけでなく、システムを導入することで、コスト削減や製品・資材のステータス可視化のほか、属人化していた受発注情報の共有化による内部不正防止や統制にも役立ちます。
NEWJI DX
製造業に特化したデジタルトランスフォーメーション(DX)の実現を目指す請負開発型のコンサルティングサービスです。AI、iPaaS、および先端の技術を駆使して、製造プロセスの効率化、業務効率化、チームワーク強化、コスト削減、品質向上を実現します。このサービスは、製造業の課題を深く理解し、それに対する最適なデジタルソリューションを提供することで、企業が持続的な成長とイノベーションを達成できるようサポートします。
製造業ニュース解説
製造業、主に購買・調達部門にお勤めの方々に向けた情報を配信しております。
新任の方やベテランの方、管理職を対象とした幅広いコンテンツをご用意しております。
お問い合わせ
コストダウンが利益に直結する術だと理解していても、なかなか前に進めることができない状況。そんな時は、newjiのコストダウン自動化機能で大きく利益貢献しよう!
(β版非公開)