- お役立ち記事
- How to Reduce Production Costs Through Effective Tool Management
How to Reduce Production Costs Through Effective Tool Management
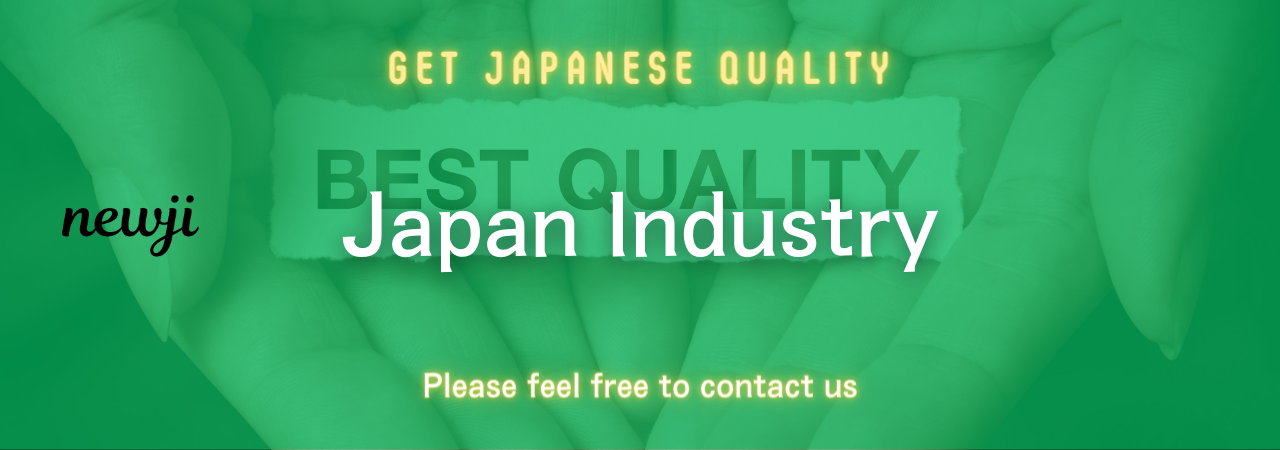
Efficient tool management is a critical aspect of reducing production costs in any manufacturing setting.
By focusing on the effective use and maintenance of tools, businesses can significantly cut down expenses and ensure smooth operation.
In this article, we will explore various strategies for achieving cost reductions through proper tool management.
目次
Understanding Tool Management
Tool management involves the systematic control and maintenance of tools used in the production process.
It encompasses everything from tool selection, storage, and usage to regular maintenance and replacement.
When these aspects are handled efficiently, it translates to reduced downtime, lower repair costs, and optimal tool performance.
Benefits of Effective Tool Management
Implementing a robust tool management strategy offers several advantages:
– Prolongs tool lifespan
– Reduces downtime due to tool failure
– Enhances production efficiency
– Lowers overall production costs
Let’s delve deeper into specific tactics for improving tool management.
Proper Tool Selection
Choosing the right tools for the job is the first step toward effective tool management.
The selected tools should be appropriate for the specific manufacturing tasks and compatible with the materials being used.
Investing in high-quality tools, although higher in initial cost, typically results in better performance and longevity.
Assessing Tool Requirements
Before purchasing tools, assess your production requirements thoroughly.
Consider the type of tasks, frequency of use, and the precision needed.
This evaluation helps in selecting tools that meet your needs without overspending on unnecessary features.
Regular Maintenance and Inspection
Routine maintenance and inspection of tools can prevent unexpected breakdowns and extend their lifespan.
Schedule regular intervals for detailed inspections and upkeep.
Lubrication, sharpening, and calibration are crucial aspects of tool maintenance.
Creating a Maintenance Schedule
Develop a maintenance schedule that aligns with the usage patterns of your tools.
For instance, high-use tools may need more frequent attention compared to those used less often.
A well-planned schedule ensures that no tool is neglected, reducing the risk of sudden failures.
Organized Tool Storage
An organized storage system for tools is vital for quick access and preventing damage.
Poor storage conditions can lead to misplacement, wear, and tear, effectively shortening the tool’s life.
Implement a system where each tool has a designated storage space.
Labeling and Inventory Management
Labeling tools and maintaining an inventory system help keep track of all tools in use.
This system minimizes the chances of tools getting lost and ensures that replacements are available when needed.
Training Employees
Ensure that all employees are trained in the correct use and handling of tools.
Proper usage techniques can prevent damage and enhance the efficiency of production processes.
Regular training sessions keep employees updated on the latest tool management practices.
Encouraging Responsible Tool Use
Instill a sense of responsibility among employees for the tools they handle.
Encourage them to report any tool issues immediately and take part in maintenance activities.
This involvement fosters a proactive approach to tool care.
Utilizing Tool Management Software
Leveraging technology can significantly streamline tool management processes.
Tool management software helps in tracking tool usage, scheduling maintenance, and managing inventory.
These systems offer real-time insights that can lead to more informed decision-making.
Choosing the Right Software
Select software that is tailored to your specific industrial needs.
Factors to consider include ease of use, integration capabilities with existing systems, and the level of customer support offered.
Cost-Benefit Analysis
Regularly perform a cost-benefit analysis of your tool management practices.
Evaluate the costs associated with tool purchase, maintenance, and replacement against the benefits gained through enhanced production efficiency.
This analysis can highlight areas where further cost reductions can be made.
Identifying Improvement Areas
Identify specific areas of your tool management process that can be optimized.
Whether it’s upgrading certain tools, improving storage solutions, or enhancing maintenance protocols, targeted improvements can lead to substantial cost savings.
Conclusion
Effective tool management is a strategic approach that can lead to significant reductions in production costs.
By focusing on proper tool selection, regular maintenance, organized storage, employee training, and utilizing management software, businesses can ensure their production processes run smoothly and efficiently.
Implement these strategies, and witness marked improvements in both tool longevity and overall productivity, ultimately leading to cost savings and better resource utilization.
資料ダウンロード
QCD調達購買管理クラウド「newji」は、調達購買部門で必要なQCD管理全てを備えた、現場特化型兼クラウド型の今世紀最高の購買管理システムとなります。
ユーザー登録
調達購買業務の効率化だけでなく、システムを導入することで、コスト削減や製品・資材のステータス可視化のほか、属人化していた購買情報の共有化による内部不正防止や統制にも役立ちます。
NEWJI DX
製造業に特化したデジタルトランスフォーメーション(DX)の実現を目指す請負開発型のコンサルティングサービスです。AI、iPaaS、および先端の技術を駆使して、製造プロセスの効率化、業務効率化、チームワーク強化、コスト削減、品質向上を実現します。このサービスは、製造業の課題を深く理解し、それに対する最適なデジタルソリューションを提供することで、企業が持続的な成長とイノベーションを達成できるようサポートします。
オンライン講座
製造業、主に購買・調達部門にお勤めの方々に向けた情報を配信しております。
新任の方やベテランの方、管理職を対象とした幅広いコンテンツをご用意しております。
お問い合わせ
コストダウンが利益に直結する術だと理解していても、なかなか前に進めることができない状況。そんな時は、newjiのコストダウン自動化機能で大きく利益貢献しよう!
(Β版非公開)