- お役立ち記事
- How to reduce the risk of delivery delays managed by the purchasing department
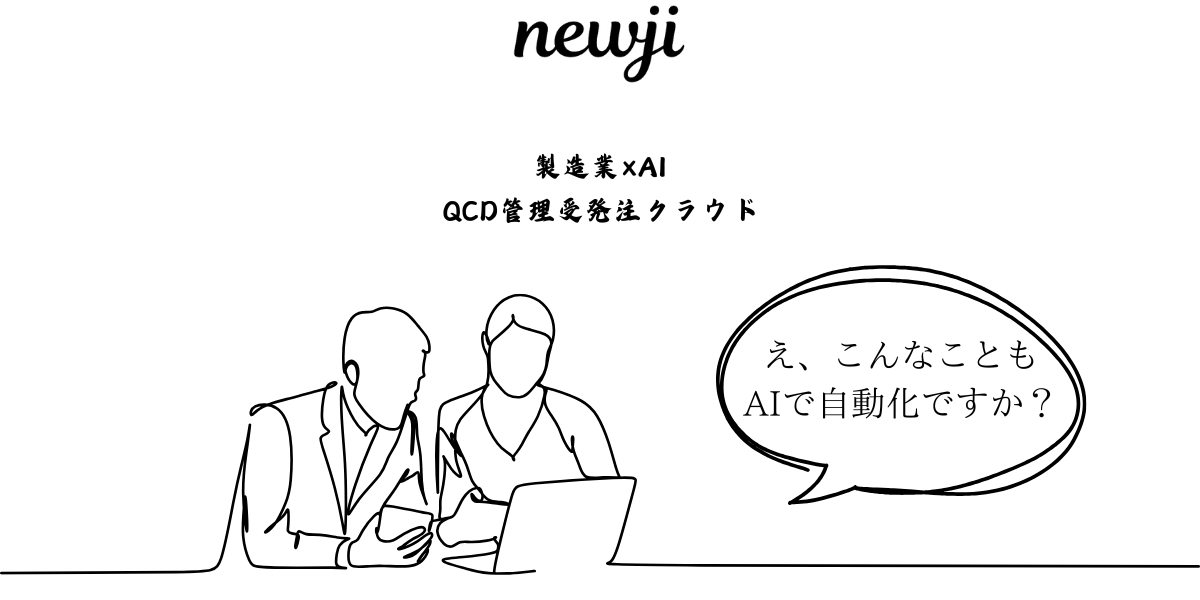
How to reduce the risk of delivery delays managed by the purchasing department
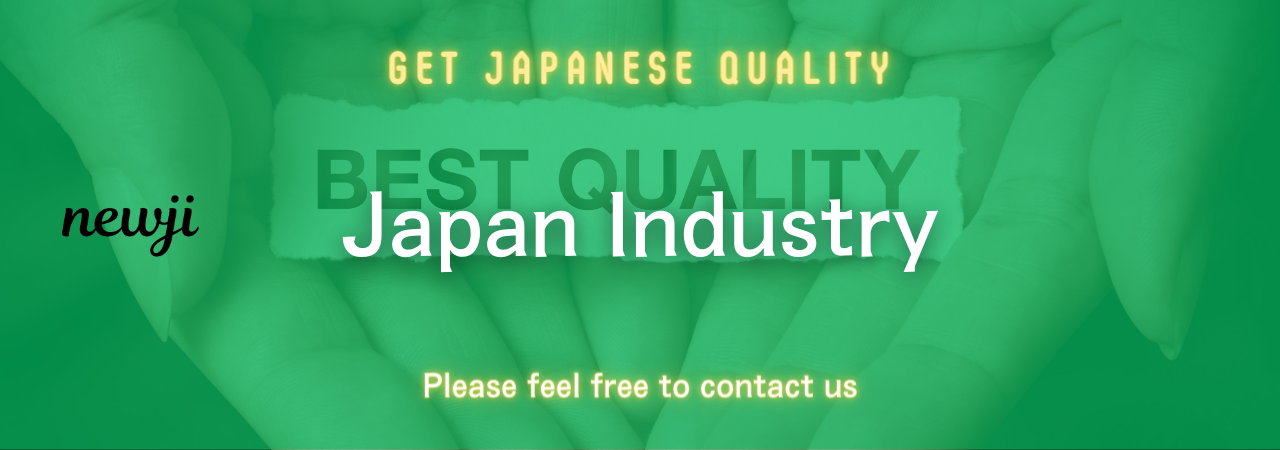
目次
Understanding Delivery Delays
Delivery delays can be a significant issue in supply chain management, causing a ripple effect of problems throughout the business.
These delays can disrupt production schedules, lead to increased costs, and ultimately impact customer satisfaction.
Understanding the nature of delivery delays is the first step to mitigating their effects.
Various factors contribute to delivery delays, including supplier issues, logistical challenges, and unexpected demand changes.
By identifying these factors, the purchasing department can develop strategies to reduce the risk of delays.
Importance of the Purchasing Department
The purchasing department plays a crucial role in managing delivery schedules.
It is responsible for sourcing the right suppliers, negotiating contracts, and ensuring that goods are delivered on time.
By effectively managing these tasks, the purchasing department can greatly reduce the risk of delivery delays.
This involves building strong relationships with suppliers, employing strategic negotiation tactics, and implementing robust tracking systems.
The more efficient the purchasing department, the smoother the entire supply chain will run.
Strategies for Reducing Delivery Delays
1. Build Strong Supplier Relationships
Strong supplier relationships are key to preventing delivery delays.
Reliable suppliers are more likely to deliver on time and communicate promptly about potential issues.
Regular communication and collaboration can help in anticipating and solving problems before they occur.
It’s important to maintain an open line of communication and establish trust with suppliers.
This can be achieved through regular meetings, performance reviews, and by providing feedback on their service.
2. Implement Strategic Sourcing
Strategic sourcing involves selecting suppliers based on a comprehensive evaluation of their capabilities, reliability, and delivery performance.
By choosing the right suppliers, the purchasing department can minimize the risk of delays.
This strategy requires an analysis of supplier performance metrics such as lead times, quality rates, and historical reliability.
Additionally, considering alternative suppliers can provide options if a primary supplier encounters problems.
Technology can be instrumental in reducing delivery delays.
Implementing supply chain management software can provide visibility into the entire supply process.
Real-time tracking allows the purchasing department to monitor shipments and identify any potential delays immediately.
Moreover, automated communication tools can send alerts and updates to all parties involved, ensuring quick responses to any issues.
4. Forecast Demand Accurately
Accurate demand forecasting helps in aligning supply with market needs.
The purchasing department should work closely with the sales and marketing teams to use market analysis tools effectively.
This collaboration ensures that the right amount of inventory is ordered and reduces the risk of shortages or overstock.
Regularly reviewing and adjusting forecasts based on the latest market trends will further enhance accuracy and minimize delays.
5. Create Contingency Plans
Despite best efforts, unexpected issues can still cause delivery delays.
Therefore, having a contingency plan is crucial.
The purchasing department should develop backup plans for scenarios like supplier failures or transportation disruptions.
These plans might include having secondary suppliers, adjusting inventory levels, or shifting production schedules.
By being prepared, the department can reduce the impact of delays on operations.
The Benefits of Reducing Delivery Delays
Reducing delivery delays leads to several benefits for the company.
Firstly, it enhances customer satisfaction as products arrive on time, increasing the likelihood of repeat business.
Secondly, it lowers operational costs since less money is spent on expedited shipping or corrective actions.
Additionally, it improves overall supply chain efficiency, allowing the company to respond more swiftly to market demands.
Ultimately, achieving timely deliveries gives the business a competitive edge in the marketplace.
Conclusion
In conclusion, the risk of delivery delays can be significantly reduced by the purchasing department through strategic initiatives and proactive measures.
By building strong supplier relationships, using technology, and preparing for unforeseen circumstances, they can ensure smoother operations.
The benefits of these efforts extend beyond avoiding delays and include enhanced customer satisfaction, reduced costs, and increased efficiency.
Thus, a well-functioning purchasing department is vital to the success of any business seeking to maintain a competitive edge.
資料ダウンロード
QCD調達購買管理クラウド「newji」は、調達購買部門で必要なQCD管理全てを備えた、現場特化型兼クラウド型の今世紀最高の購買管理システムとなります。
ユーザー登録
調達購買業務の効率化だけでなく、システムを導入することで、コスト削減や製品・資材のステータス可視化のほか、属人化していた購買情報の共有化による内部不正防止や統制にも役立ちます。
NEWJI DX
製造業に特化したデジタルトランスフォーメーション(DX)の実現を目指す請負開発型のコンサルティングサービスです。AI、iPaaS、および先端の技術を駆使して、製造プロセスの効率化、業務効率化、チームワーク強化、コスト削減、品質向上を実現します。このサービスは、製造業の課題を深く理解し、それに対する最適なデジタルソリューションを提供することで、企業が持続的な成長とイノベーションを達成できるようサポートします。
オンライン講座
製造業、主に購買・調達部門にお勤めの方々に向けた情報を配信しております。
新任の方やベテランの方、管理職を対象とした幅広いコンテンツをご用意しております。
お問い合わせ
コストダウンが利益に直結する術だと理解していても、なかなか前に進めることができない状況。そんな時は、newjiのコストダウン自動化機能で大きく利益貢献しよう!
(Β版非公開)