- お役立ち記事
- How to review processes to shorten procurement lead time in purchasing department
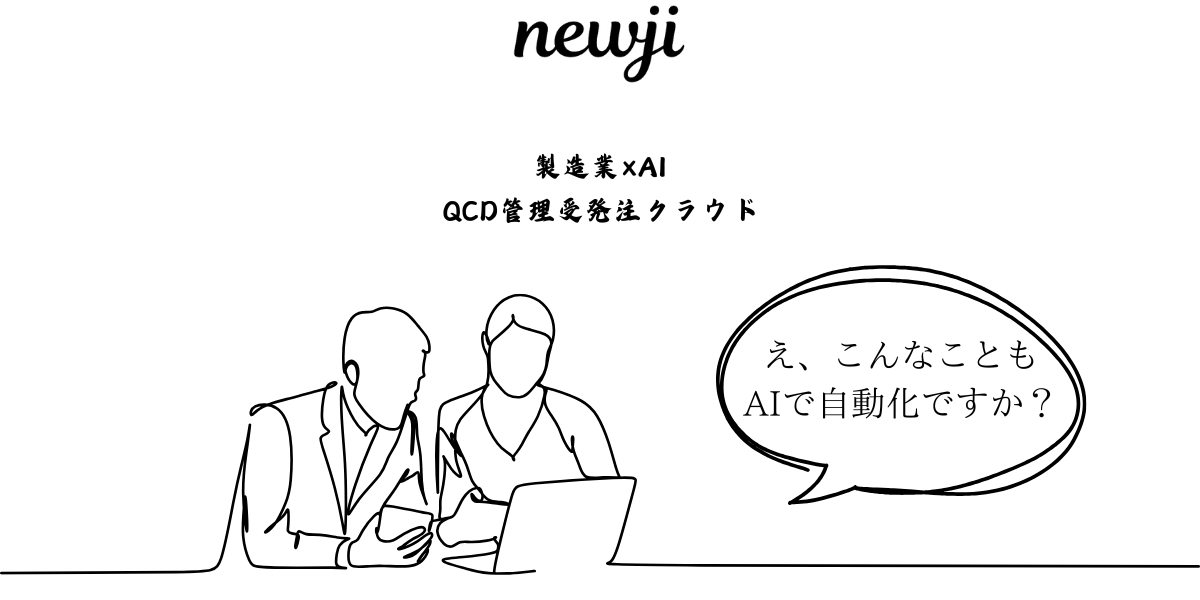
How to review processes to shorten procurement lead time in purchasing department
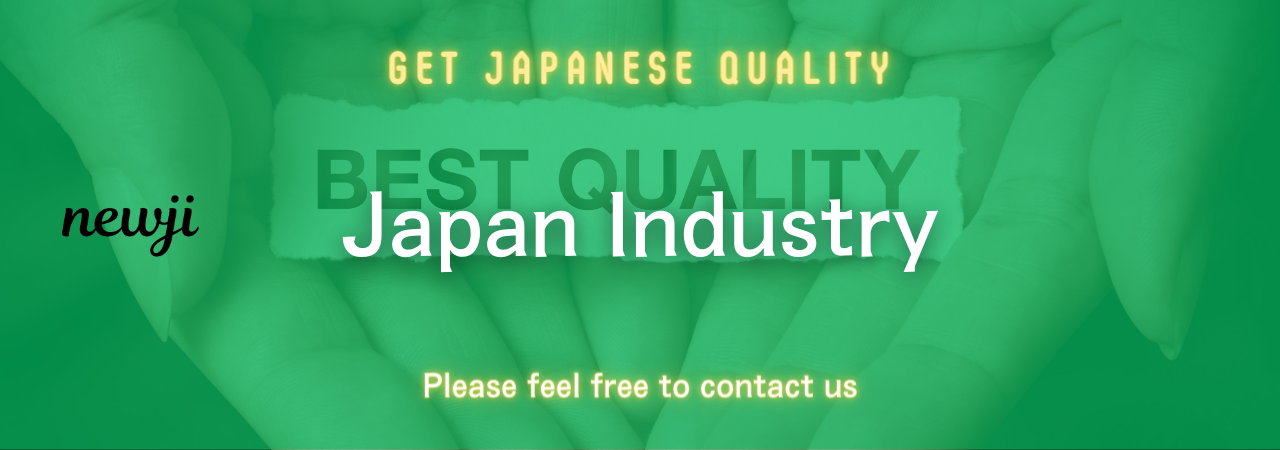
目次
Understanding Procurement Lead Time
Procurement lead time is the duration it takes from identifying a need for a product or service to having it delivered and ready for use.
Reducing this time enhances efficiency and responsiveness, allowing companies to react swiftly to market demands and opportunities.
The first step in reducing procurement lead time is understanding the process thoroughly.
The Importance of Reviewing Processes
Reviewing processes is crucial for identifying bottlenecks and inefficiencies that contribute to long lead times.
Every step in the procurement process – from requisition, supplier selection, negotiation, order placement, to delivery – needs to be scrutinized.
By closely examining each stage, companies can pinpoint exactly where delays occur and take corrective action.
Strategies to Shorten Procurement Lead Time
Streamline Documentation
One of the most common causes of delays in procurement is excessive paperwork and manual processing.
Automating these processes can significantly reduce lead times.
Implementing electronic procurement systems can eliminate unnecessary documentation and facilitate faster approvals and sign-offs.
These systems enable quick sharing of information, reducing waiting times typically associated with manual interventions.
Enhance Supplier Relationships
Maintaining strong relationships with suppliers can lead to more efficient procurement processes.
Suppliers who value their partnerships are often more flexible and responsive to urgent requests.
Regular communication with suppliers ensures a better understanding of each other’s capabilities and constraints.
This understanding can lead to negotiations for better terms, including faster delivery times.
Adopt Just-in-Time Purchasing
Just-in-time (JIT) purchasing helps minimize inventory holding costs and reduce lead times by ordering goods only when needed.
By aligning procurement schedules with production needs, companies can avoid unnecessary delays and costs associated with overstocking.
However, JIT requires accurate demand forecasting and reliable suppliers to avoid disruptions.
Optimize Supplier Selection and Evaluation
Choosing the right supplier is critical to reducing lead times.
Procurement teams should evaluate suppliers based on their ability to deliver promptly and reliably.
Creating a preferred supplier list based on previous performance helps ensure that orders are placed with vendors who have a track record of meeting deadlines.
Continuous evaluation of suppliers’ performance is necessary to maintain high standards in delivery times.
Implement Predictive Analytics
Leveraging data analytics can significantly shorten procurement lead times.
Predictive analytics tools can forecast demand more accurately, helping organizations to procure materials in line with actual needs.
This reduces the risk of overordering and underordering, both of which contribute to longer lead times.
Data-driven insights enable better planning, ensuring that procurement processes run smoothly.
Improve Internal Collaboration
Cross-departmental collaboration is essential in reducing procurement lead times.
Seamless communication between different departments, such as sales, production, and procurement, ensures that everyone is aware of forecasts and materials needed.
This alignment eliminates the delays caused by miscommunication or lack of information, allowing for more efficient order processing.
Monitoring and Continuous Improvement
Track Key Performance Indicators (KPIs)
Tracking KPIs is vital in assessing the effectiveness of efforts to reduce procurement lead times.
Metrics such as order cycle time, supplier lead time, and on-time delivery rates provide insights into procurement efficiency.
Regular analysis of these KPIs helps identify areas for improvement and ensures that strategies are working effectively.
Encourage Feedback and Adaptation
Encourage stakeholders involved in the procurement process to provide feedback on what works and what doesn’t.
This feedback is invaluable for refining processes and implementing necessary changes.
Adapting based on real-world challenges and insights ensures that the procurement process remains efficient and responsive to changing needs.
Training and Development
Investing in the training and development of procurement staff ensures they are up-to-date with the latest trends and technologies.
Understanding modern procurement techniques and systems enables staff to perform their roles more effectively, reducing lead times.
Continuous learning fosters a culture of innovation and improvement, which is crucial for maintaining a competitive edge.
Concluding Thoughts
Procurement is a critical function that directly impacts a company’s ability to meet customer demands and adapt to market changes.
By reviewing and optimizing procurement processes, businesses can significantly reduce lead times, enhancing overall operational efficiency.
This requires a comprehensive approach that includes leveraging technology, fostering supplier relationships, and promoting internal collaboration.
With commitment and strategic focus, reducing procurement lead time becomes an attainable objective that drives value and growth.
資料ダウンロード
QCD調達購買管理クラウド「newji」は、調達購買部門で必要なQCD管理全てを備えた、現場特化型兼クラウド型の今世紀最高の購買管理システムとなります。
ユーザー登録
調達購買業務の効率化だけでなく、システムを導入することで、コスト削減や製品・資材のステータス可視化のほか、属人化していた購買情報の共有化による内部不正防止や統制にも役立ちます。
NEWJI DX
製造業に特化したデジタルトランスフォーメーション(DX)の実現を目指す請負開発型のコンサルティングサービスです。AI、iPaaS、および先端の技術を駆使して、製造プロセスの効率化、業務効率化、チームワーク強化、コスト削減、品質向上を実現します。このサービスは、製造業の課題を深く理解し、それに対する最適なデジタルソリューションを提供することで、企業が持続的な成長とイノベーションを達成できるようサポートします。
オンライン講座
製造業、主に購買・調達部門にお勤めの方々に向けた情報を配信しております。
新任の方やベテランの方、管理職を対象とした幅広いコンテンツをご用意しております。
お問い合わせ
コストダウンが利益に直結する術だと理解していても、なかなか前に進めることができない状況。そんな時は、newjiのコストダウン自動化機能で大きく利益貢献しよう!
(Β版非公開)