- お役立ち記事
- How to select and manage multiple suppliers to reduce risks in material supply
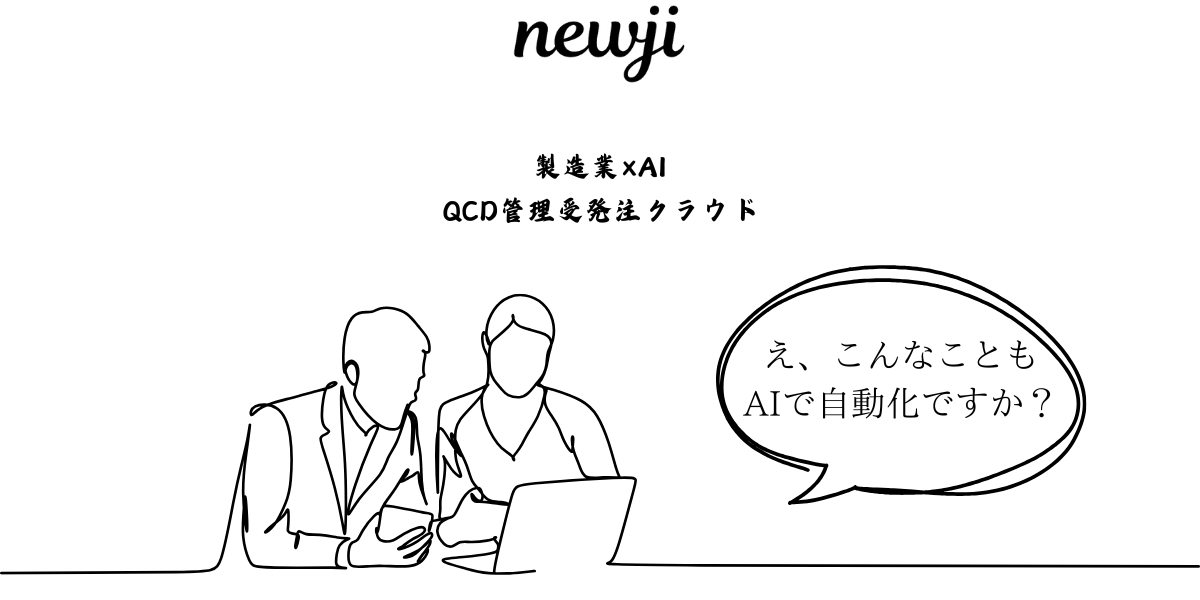
How to select and manage multiple suppliers to reduce risks in material supply
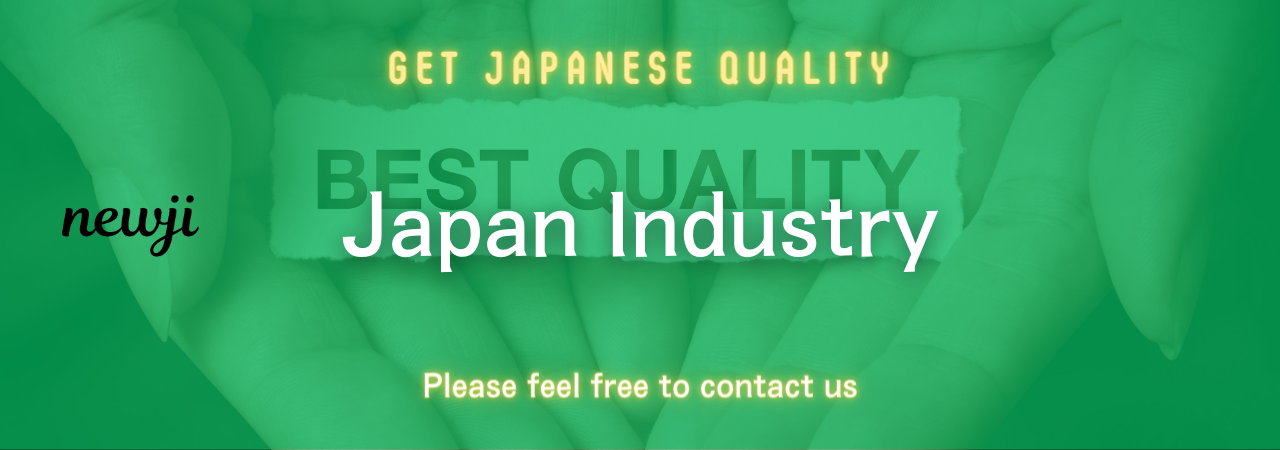
目次
Understanding the Importance of Multiple Suppliers
In today’s fast-paced and ever-changing business environment, relying on a single supplier for materials can pose significant risks.
Issues such as supply chain disruptions, natural disasters, political instability, and financial instability can arise unexpectedly, impacting your operations negatively if you don’t have a backup plan.
It’s essential to have a diverse supplier base to safeguard your business.
This strategy not only helps in mitigating risks but also fosters competitive pricing and innovation.
The Benefits of Working with Multiple Suppliers
When you engage with multiple suppliers, you ensure a steady supply of materials, even if one supplier faces unforeseen challenges.
This redundancy allows you to continue operations without disruptions.
Moreover, different suppliers can offer varied pricing and payment terms which gives your business flexibility in managing costs effectively.
It also opens avenues for innovation as suppliers often bring in new ideas that can improve your products or services.
In addition, having multiple suppliers increases your negotiation power, allowing you to secure better deals and terms based on market conditions.
Criteria for Selecting Suppliers
Choosing the right suppliers is critical when you’re considering working with multiple vendors.
Begin by evaluating potential suppliers based on their reliability, quality of materials, and their ability to meet your delivery timelines consistently.
Supplier reputation is another factor; you want to work with those who are known for their dependable services.
Financial stability is also crucial to ensure they can withstand economic fluctuations.
Additionally, assess their level of customer service, communication ability, and responsiveness to resolve issues promptly.
Consider Geographical Diversification
When selecting suppliers, consider their geographical locations.
Diversifying geographically minimizes risks related to regional disruptions like natural disasters or political instability.
This strategy ensures a broader safety net for your supply chain.
For instance, a flood or earthquake might impact suppliers from one region but having alternatives in other areas reduces impact significantly on your material supply.
Assess Technology and Innovation Capabilities
In today’s technology-driven environment, a supplier’s technological capability can be a competitive advantage.
Suppliers using advanced technology often provide better quality control, faster production times, and innovative solutions.
Additionally, their investment in technology ensures they are poised to adapt to future industrial developments and demands.
Building Strong Relationships with Suppliers
To manage multiple suppliers effectively, it is essential to build strong and collaborative relationships with each.
Openness and frequent communication are vital in this process.
Share your business goals and expectations clearly with your suppliers, fostering a transparent environment.
Regularly review performance together to ensure alignment and address any issues that might arise.
Strong relationships often lead to suppliers being willing to prioritize your orders and offer you better terms.
Establish a Supplier Evaluation System
Implementing a supplier evaluation system is a proactive step for managing multiple suppliers.
Regular assessments help identify issues early, allowing you to take corrective actions promptly.
Key metrics can include delivery performance, quality of materials, service levels, and contract compliance.
Supplier evaluations also provide insights on potential areas for improvement and innovation.
Effective Management Strategies
Managing multiple suppliers requires strategic oversight and planning.
Create a centralized database to track all your suppliers and their contracts, ensuring easy access to information.
Use software solutions to streamline procurement processes, integrating supplier management to improve efficiency.
This approach should include order tracking, invoice management, and supply chain analytics.
Always maintain consistent documentation; this ensures contractual obligations and expectations are met while offering a reference for any future issues.
Develop a Contingency Plan
An effective contingency plan is essential to mitigate risks related to material supply.
Anticipate potential supply chain disruptions and prepare strategies accordingly.
This planning should involve identifying critical materials, evaluating their suppliers, and determining alternative supply sources.
Contingency plans should be tested periodically to ensure their effectiveness in realistic scenarios.
Emphasizing Sustainability and Ethical Sourcing
Incorporate sustainability into your supply chain by selecting suppliers that adhere to ethical sourcing and environmental standards.
Sustainability not only aligns your practices with broader environmental goals but also enhances your brand image and competitiveness.
Engage with suppliers about their sustainability practices and work together to improve these practices over time.
This collaboration can lead to innovative solutions that are both effective and environmentally friendly.
Conclusion
Selecting and managing multiple suppliers is a strategic approach to reducing risks in material supply.
This involves thorough evaluation, diversification, and robust management systems to ensure a reliable supply chain.
Building strong relationships and focusing on sustainability further enhance your business resilience and adaptability.
By following these practices, businesses can safeguard their operations and position themselves well in competitive markets.
資料ダウンロード
QCD調達購買管理クラウド「newji」は、調達購買部門で必要なQCD管理全てを備えた、現場特化型兼クラウド型の今世紀最高の購買管理システムとなります。
ユーザー登録
調達購買業務の効率化だけでなく、システムを導入することで、コスト削減や製品・資材のステータス可視化のほか、属人化していた購買情報の共有化による内部不正防止や統制にも役立ちます。
NEWJI DX
製造業に特化したデジタルトランスフォーメーション(DX)の実現を目指す請負開発型のコンサルティングサービスです。AI、iPaaS、および先端の技術を駆使して、製造プロセスの効率化、業務効率化、チームワーク強化、コスト削減、品質向上を実現します。このサービスは、製造業の課題を深く理解し、それに対する最適なデジタルソリューションを提供することで、企業が持続的な成長とイノベーションを達成できるようサポートします。
オンライン講座
製造業、主に購買・調達部門にお勤めの方々に向けた情報を配信しております。
新任の方やベテランの方、管理職を対象とした幅広いコンテンツをご用意しております。
お問い合わせ
コストダウンが利益に直結する術だと理解していても、なかなか前に進めることができない状況。そんな時は、newjiのコストダウン自動化機能で大きく利益貢献しよう!
(Β版非公開)