- お役立ち記事
- How to select process technology to improve sinterability of metal powder
月間77,185名の
製造業ご担当者様が閲覧しています*
*2025年2月28日現在のGoogle Analyticsのデータより
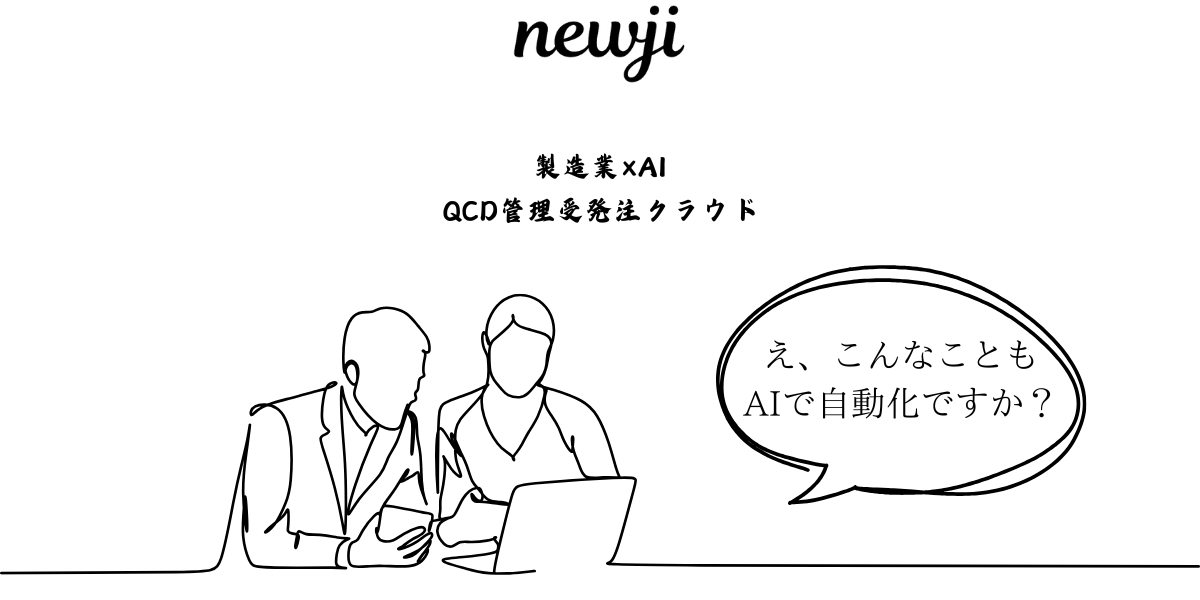
How to select process technology to improve sinterability of metal powder
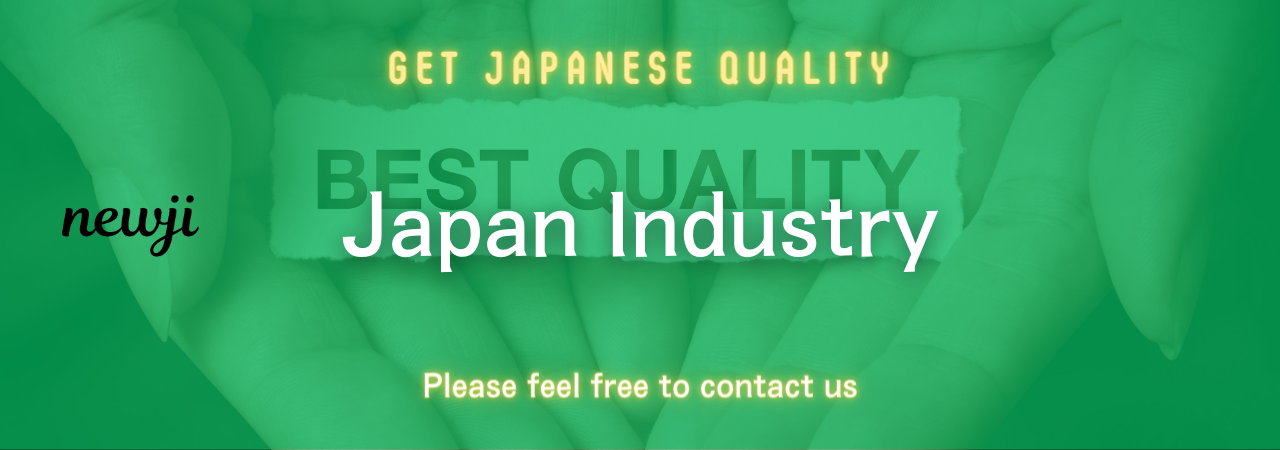
目次
Understanding Sinterability of Metal Powder
Sinterability is a key factor in the field of powder metallurgy.
It describes the capability of metal powders to bond at the particle surfaces and form a solid structure when subjected to heat and pressure.
The sintering process enhances properties such as strength, hardness, and thermal resistance.
Choosing the right process technology is essential for optimizing the sinterability of metal powders.
This article will guide you through the factors to consider and steps to take to improve sinterability using appropriate process technology.
Factors Influencing Sinterability
Particle Size and Shape
The size and shape of metal powder particles significantly affect sinterability.
Fine particles with a high surface area promote better diffusion, enhancing the bonding process during sintering.
Additionally, spherical particles tend to pack more efficiently, reducing porosity.
This results in a denser final product.
Material Composition
The composition of the metal powder plays an important role in sintering.
Different materials require specific conditions such as temperature and atmosphere to achieve optimal bonding.
Alloys, for instance, can be designed to have certain elements that promote better sintering characteristics.
Temperature and Time
Proper control of sintering temperature and time is crucial.
An optimal temperature allows for sufficient diffusion at the particle boundaries without causing excessive grain growth.
Similarly, the duration of the heating process should be adequate to allow for full densification while avoiding prolonged exposure that could degrade material properties.
Pressure Application
In many sintering techniques, applying pressure can significantly enhance the densification process.
Methods such as hot pressing and hot isostatic pressing utilize pressure in tandem with heat to improve particle bonding.
The applied pressure helps eliminate voids, enhancing the overall strength of the material.
Selecting the Right Process Technology
Conventional Sintering
Conventional sintering is the most common and straightforward method.
It involves heating the metal powder compact in a furnace at a temperature below its melting point.
While simple, it may not always provide sufficient density and mechanical properties for advanced applications.
Hot Pressing
Hot pressing involves the simultaneous application of heat and uniaxial pressure on the powder compact.
This method is effective for achieving high density and enhanced mechanical properties.
Hot pressing is ideal for components that need to withstand high stress and temperature conditions.
Spark Plasma Sintering (SPS)
Spark Plasma Sintering, also known as Field Assisted Sintering Technique (FAST), is a relatively modern technology that applies pulsed direct electrical current along with pressure to the powder compact.
SPS significantly reduces the sintering time and can fully densify powders without excessive grain growth.
This method is particularly suitable for ceramics and composite materials.
Hot Isostatic Pressing (HIP)
HIP is a process where the metal powder compact is placed in a high-pressure, high-temperature environment.
This technique uses an inert gas, like argon, to apply pressure uniformly in all directions.
HIP is incredibly effective for complex shapes and high-performance materials, ensuring thorough elimination of porosity.
Steps to Improve Sinterability
Optimize Material Selection
Choosing the correct powder composition is the first step.
Consider powders with finer particles and uniform shapes.
Select alloy compositions that support easier sintering based on the intended application.
Tune Process Parameters
Experiment with different temperatures, times, and pressures to determine the optimum sintering conditions.
Control the atmosphere in the sintering chamber to prevent oxidation or other undesirable reactions.
Conduct small-scale tests to study the effects of varying these parameters on the final product.
Utilize Advanced Sintering Techniques
Adopt advanced sintering technologies like SPS or HIP for more demanding applications.
These methods provide greater control over the sintering environment, resulting in superior material properties.
Conduct Post-Sintering Treatments
Post-sintering processes such as annealing, machining, or surface treatments can enhance the properties of the sintered components.
These treatments can improve characteristics like toughness, wear resistance, and dimensional accuracy.
Conclusion
Selecting the right process technology to improve the sinterability of metal powder is crucial for achieving desired mechanical and physical properties in final products.
By considering factors such as particle size, composition, temperature, and pressure, and by utilizing advanced sintering techniques, manufacturers can optimize their processes.
Continual experimentation and adjustments to process parameters can further enhance the quality and performance of metal parts produced through powder metallurgy.
Armed with this knowledge, manufacturers can ensure their products meet stringent industry standards and applications.
資料ダウンロード
QCD管理受発注クラウド「newji」は、受発注部門で必要なQCD管理全てを備えた、現場特化型兼クラウド型の今世紀最高の受発注管理システムとなります。
ユーザー登録
受発注業務の効率化だけでなく、システムを導入することで、コスト削減や製品・資材のステータス可視化のほか、属人化していた受発注情報の共有化による内部不正防止や統制にも役立ちます。
NEWJI DX
製造業に特化したデジタルトランスフォーメーション(DX)の実現を目指す請負開発型のコンサルティングサービスです。AI、iPaaS、および先端の技術を駆使して、製造プロセスの効率化、業務効率化、チームワーク強化、コスト削減、品質向上を実現します。このサービスは、製造業の課題を深く理解し、それに対する最適なデジタルソリューションを提供することで、企業が持続的な成長とイノベーションを達成できるようサポートします。
製造業ニュース解説
製造業、主に購買・調達部門にお勤めの方々に向けた情報を配信しております。
新任の方やベテランの方、管理職を対象とした幅広いコンテンツをご用意しております。
お問い合わせ
コストダウンが利益に直結する術だと理解していても、なかなか前に進めることができない状況。そんな時は、newjiのコストダウン自動化機能で大きく利益貢献しよう!
(β版非公開)