- お役立ち記事
- How to select standardized parts that support improved production line flexibility
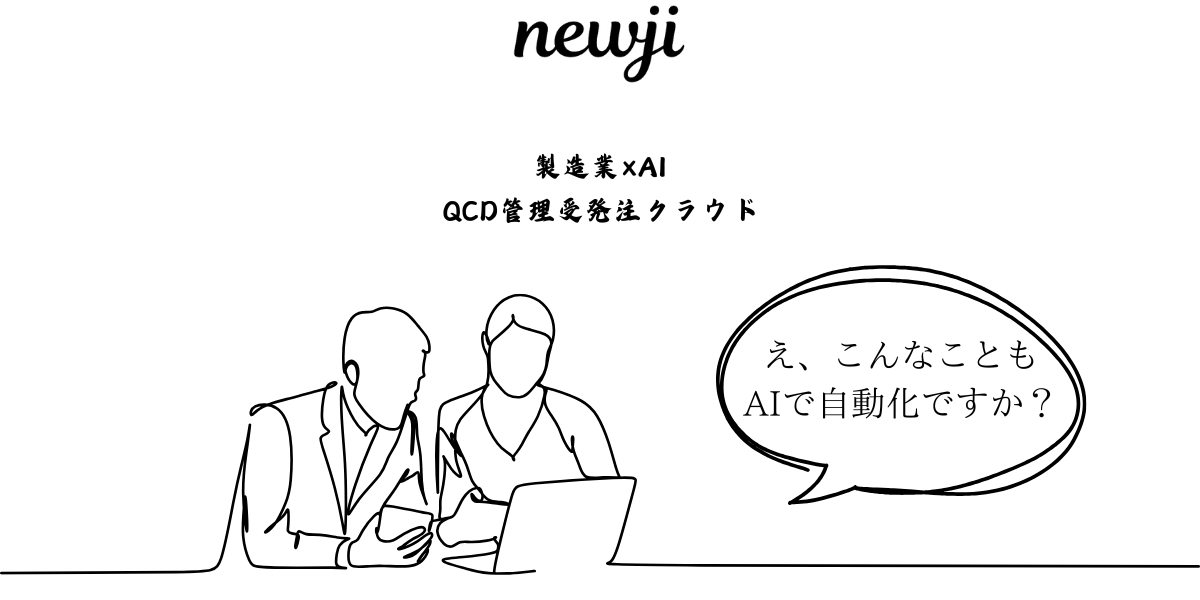
How to select standardized parts that support improved production line flexibility
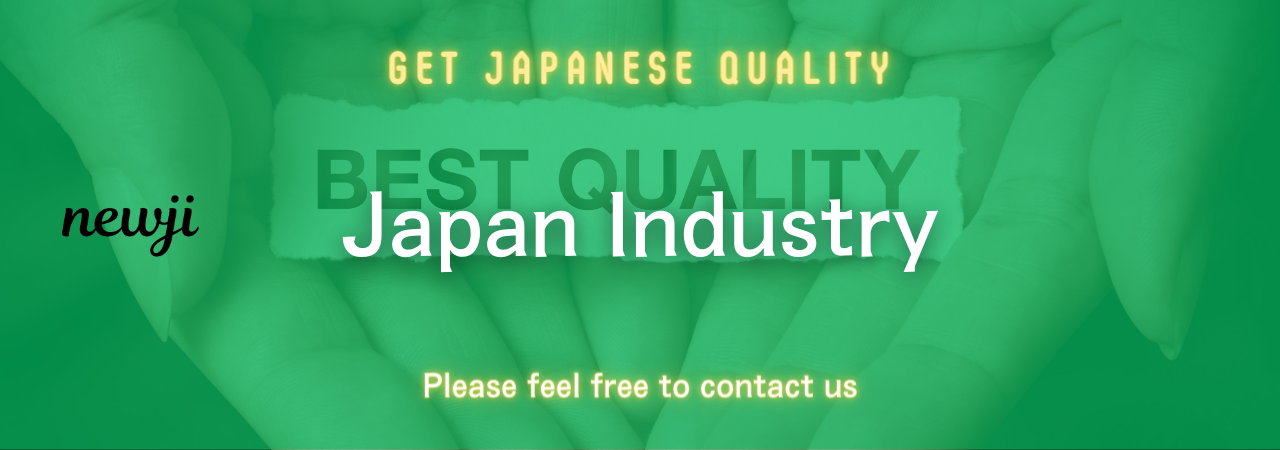
目次
Introduction to Standardized Parts
In today’s rapidly evolving manufacturing landscape, flexibility and efficiency are more critical than ever for production lines.
Standardized parts play a crucial role in achieving these goals by streamlining processes and reducing costs.
These components are pre-engineered and mass-produced, allowing different systems to utilize them across various applications.
In this article, we will explore how to select standardized parts that support improved production line flexibility.
Understanding the Importance of Flexibility
Before diving into the specifics of standardized parts, it’s essential to appreciate why flexibility is vital for modern production lines.
With the growing demand for customized products and shorter lead times, manufacturers must adapt quickly to changing requirements.
This adaptiveness reduces downtime and facilitates quick adjustments in production schedules.
By incorporating flexibility into the production line, companies can respond efficiently to shifts in market demand or unforeseen disruptions.
Minimizing Costs and Complexity
Standardized parts help in minimizing costs and reducing the complexity of operations.
By using interchangeable components, companies can limit the variety of parts in their inventory, leading to a more manageable supply chain.
This reduction in complexity also translates into simpler employee training and maintenance procedures.
Enabling Quick Adjustments
Standardized parts allow for faster adjustments in production lines, such as implementing new designs or making modifications to existing ones.
This capability ensures that production can swiftly pivot without encountering significant delays or additional costs.
Identifying the Right Standardized Parts
Selecting the appropriate standardized parts for a production line requires a strategic approach.
It’s not just about picking parts; it’s about ensuring that these components meet the specific needs of your manufacturing processes.
Assessing Compatibility
The first step in selecting standardized parts is assessing compatibility with your existing systems and processes.
Parts must fit seamlessly with your machinery and assembly line requirements.
Evaluate whether the parts align with your current technology and production methodology to avoid costly retrofits or adjustments.
Evaluating Quality and Durability
Quality is paramount when selecting standardized parts.
The durability and reliability of these components directly impact production efficiency and product quality.
Research different manufacturers and suppliers to ensure they adhere to industry standards and provide parts that will withstand the rigors of daily use.
Considering Cost-Effectiveness
While it’s tempting to opt for the cheapest options, it’s essential to consider the long-term implications of your choice.
Balance cost with quality and performance to ensure the parts offer good value over time.
Factor in potential savings from reduced downtime and maintenance when evaluating cost-effectiveness.
Checking for Vendor Support and Availability
Ensure that the chosen parts have robust vendor support and are readily available.
Reliable vendors should offer customer service and technical support to assist with any issues that may arise.
Additionally, parts should be readily available to prevent production delays due to inventory shortages.
Integrating Standardized Parts into Your Production Line
Once you’ve selected the appropriate standardized parts, the next step is their integration into the production line.
This process involves careful planning and execution to maximize the benefits.
Planning the Integration
Start by creating a detailed plan outlining how the standardized parts will be incorporated into the existing system.
This plan should include timelines, personnel responsibilities, and any necessary adjustments to machinery.
A comprehensive approach ensures a smooth transition with minimal disruption.
Training Personnel
Ensure that all employees involved understand the new components and their role in the production line.
Conduct training sessions to educate staff about the new processes and address any questions or concerns they may have.
Proper training ensures that employees can operate and maintain the new components effectively.
Monitoring and Adjusting
Once the parts are integrated, continuous monitoring is key to identifying any issues or areas for improvement.
Gather feedback from employees and supervisors to assess the impact on production efficiency and flexibility.
Use this information to make any necessary adjustments for optimal performance.
Case Study: Successful Implementation
To illustrate the importance and impact of standardized parts, let’s consider a case study of a manufacturing firm that successfully integrated these components.
Company XYZ, a leading automotive parts manufacturer, faced challenges with their fluctuating production demands and variations in product sizes.
By incorporating standardized parts into their assembly line, they reduced downtime by 30% and improved overall production efficiency by 25%.
Their employees required less training as the parts were interchangeable across different models.
This adaptability allowed Company XYZ to meet varying customer demands promptly, enhancing their market competitiveness.
Conclusion
Selecting and integrating standardized parts is a strategic move toward enhancing production line flexibility.
By focusing on compatibility, quality, cost-effectiveness, and vendor support, manufacturers can build resilient and adaptable systems.
As demonstrated by the case study, the right choice of standardized parts leads to significant improvements in efficiency and responsiveness.
In a fast-paced manufacturing environment, leveraging these components ensures that companies remain agile and ready to meet the challenges of tomorrow.
資料ダウンロード
QCD調達購買管理クラウド「newji」は、調達購買部門で必要なQCD管理全てを備えた、現場特化型兼クラウド型の今世紀最高の購買管理システムとなります。
ユーザー登録
調達購買業務の効率化だけでなく、システムを導入することで、コスト削減や製品・資材のステータス可視化のほか、属人化していた購買情報の共有化による内部不正防止や統制にも役立ちます。
NEWJI DX
製造業に特化したデジタルトランスフォーメーション(DX)の実現を目指す請負開発型のコンサルティングサービスです。AI、iPaaS、および先端の技術を駆使して、製造プロセスの効率化、業務効率化、チームワーク強化、コスト削減、品質向上を実現します。このサービスは、製造業の課題を深く理解し、それに対する最適なデジタルソリューションを提供することで、企業が持続的な成長とイノベーションを達成できるようサポートします。
オンライン講座
製造業、主に購買・調達部門にお勤めの方々に向けた情報を配信しております。
新任の方やベテランの方、管理職を対象とした幅広いコンテンツをご用意しております。
お問い合わせ
コストダウンが利益に直結する術だと理解していても、なかなか前に進めることができない状況。そんな時は、newjiのコストダウン自動化機能で大きく利益貢献しよう!
(Β版非公開)