- お役立ち記事
- How to set safety stock and its impact on costs: The optimal balance that purchasing departments should consider
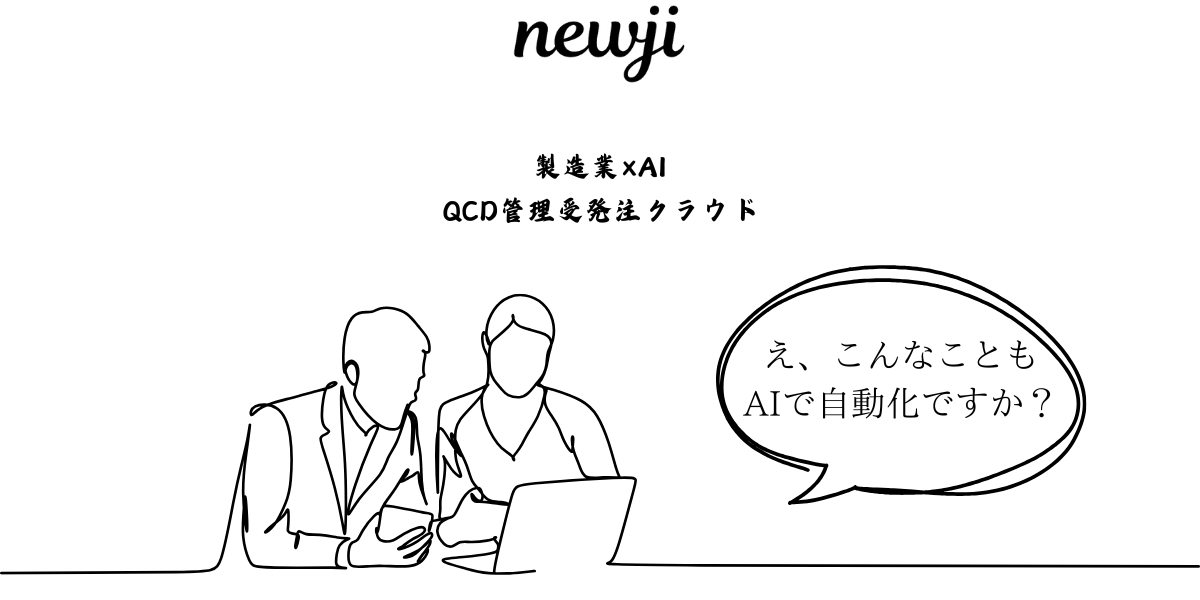
How to set safety stock and its impact on costs: The optimal balance that purchasing departments should consider
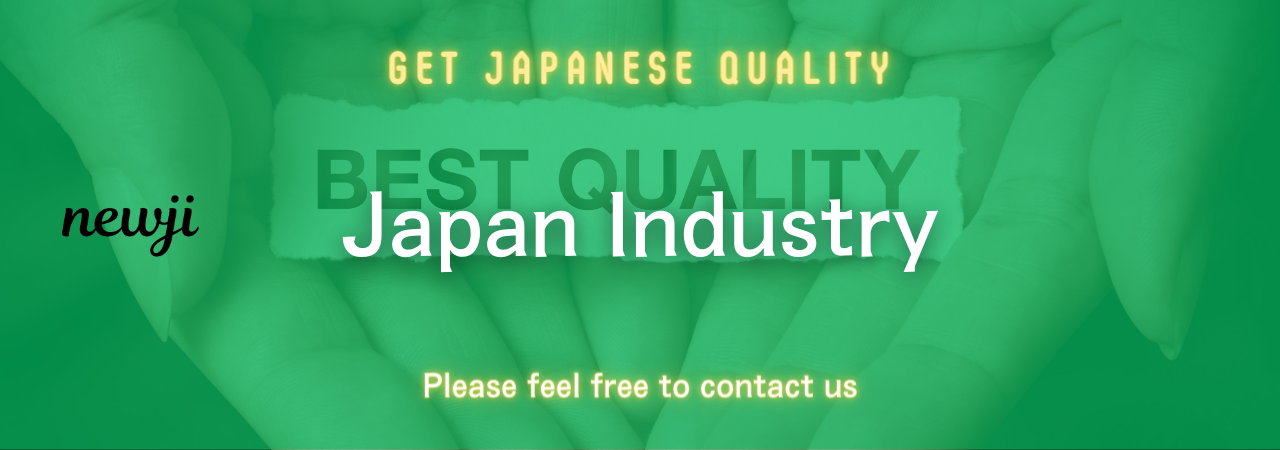
目次
Understanding Safety Stock
Safety stock is an essential concept in inventory management that serves as a buffer to prevent stockouts and ensure smooth operations.
It acts as a cushion against uncertainties in demand and supply, helping companies avoid delays in fulfilling customer orders.
Determining the right amount of safety stock is crucial as it directly impacts both service levels and holding costs.
Striking the optimal balance between these factors is vital for maintaining efficient purchasing operations.
Why Safety Stock Matters
Safety stock plays a critical role in enhancing customer satisfaction by ensuring that products are available when needed.
It helps companies avoid the pitfalls associated with stockouts, such as losing customers to competitors or facing costly expedited shipping fees.
Without adequate safety stock, businesses may struggle to meet demand fluctuations or unforeseen delivery delays from suppliers.
Having the right amount of safety stock is also key to optimizing supply chain efficiency.
An optimal level of safety stock can effectively absorb minor disruptions, such as a sudden increase in customer demand or a supplier’s shipment delay.
This reduces the risk of halting production lines or service interruptions, ultimately contributing to a robust and responsive supply chain.
Calculating Safety Stock
To effectively manage safety stock, companies must use accurate calculations tailored to their specific needs and conditions.
One common method for calculating safety stock is based on statistical techniques that consider lead time variability and demand fluctuations.
The basic formula for calculating safety stock is:
Safety Stock = Z-score x Standard deviation of demand x Square root of lead time
In this formula, the Z-score represents the desired service level, which corresponds to the probability of not facing a stockout.
The choice of Z-score will depend on the company’s tolerance for risk, with higher scores indicating a greater emphasis on avoiding stockouts.
The standard deviation of demand reflects the variability in customer demand during the lead time, while the square root of lead time accounts for fluctuations in the time it takes to receive replenishment orders.
These factors are critical in determining an appropriate safety stock level.
Factors Affecting Safety Stock
Several variables can influence the calculation of safety stock, making tailored assessments essential for effective inventory management.
1. **Demand Variability**: High variability in customer demand necessitates more safety stock to mitigate the risk of stockouts.
Seasonal trends, market dynamics, and promotions can all impact demand variability.
2. **Lead Time Variability**: Lead time is the interval between placing an order and receiving it.
Uncertainties in supplier performance can cause fluctuations in lead time, requiring increased safety stock to maintain service levels.
3. **Service Level Targets**: Companies must determine their acceptable level of service, or the probability of not experiencing a stockout.
Higher service levels lead to increased safety stock, weighing service performance against inventory carrying costs.
4. **Supplier Reliability**: Reliable suppliers with consistent lead times enable businesses to maintain lower safety stock levels.
Conversely, less predictable suppliers may require higher safety stock to compensate for delivery inconsistencies.
5. **Order and Holding Costs**: Balancing the trade-off between ordering costs and holding costs is critical.
While safety stock reduces ordering frequency, excessive inventory increases holding costs, prompting a need for optimization.
The Impact of Safety Stock on Costs
Safety stock levels directly impact various inventory-related costs, highlighting the importance of establishing the appropriate balance.
Holding Costs
Holding costs encompass expenses incurred from storing inventory, such as warehousing, insurance, and obsolescence.
Excessive safety stock leads to higher holding costs, which can significantly impact a company’s bottom line.
However, keeping safety stock too low can result in missed sales opportunities and decrease customer satisfaction.
Ordering Costs
Optimizing safety stock can influence ordering costs, as lower stock levels may necessitate more frequent replenishment orders.
Ordering costs include administrative expenses, shipping, and receiving overhead, which accumulate with each transaction.
By managing safety stock levels effectively, businesses can strike a balance between these costs and achieve cost efficiency.
Potential Lost Sales
Inadequate safety stock can lead to stockouts, resulting in lost sales opportunities and dissatisfied customers.
This not only affects current revenue but can also damage long-term customer relationships and brand reputation.
By maintaining sufficient safety stock, businesses can ensure consistent product availability, fostering customer loyalty and enhancing competitive advantage.
Strategies for Optimizing Safety Stock
To achieve the optimal balance of safety stock, purchasing departments can employ various strategies tailored to their operational requirements.
Data-Driven Analysis
Utilizing historical data and demand forecasting can provide insights into patterns and trends, enabling more accurate safety stock calculations.
Advanced analytics tools can help predict demand fluctuations and assess supplier performance to facilitate informed decision-making.
Collaborative Planning
Collaborating with suppliers on lead time transparency and demand forecasting fosters a more resilient supply chain.
Open communication and shared data help synchronize inventory strategies and reduce uncertainties.
Regular Review and Adjustment
Periodic evaluation of safety stock levels ensures alignment with changing market conditions and business objectives.
Regularly updating calculations based on the latest data ensures that inventory levels remain optimal over time.
In conclusion, setting the right safety stock level is a critical component of effective inventory management.
While it is essential to protect against stockouts, it is equally important to manage costs associated with excessive inventory.
By understanding the variables influencing safety stock and employing strategic approaches, purchasing departments can achieve an optimal balance that supports operational efficiency and minimizes costs.
資料ダウンロード
QCD調達購買管理クラウド「newji」は、調達購買部門で必要なQCD管理全てを備えた、現場特化型兼クラウド型の今世紀最高の購買管理システムとなります。
ユーザー登録
調達購買業務の効率化だけでなく、システムを導入することで、コスト削減や製品・資材のステータス可視化のほか、属人化していた購買情報の共有化による内部不正防止や統制にも役立ちます。
NEWJI DX
製造業に特化したデジタルトランスフォーメーション(DX)の実現を目指す請負開発型のコンサルティングサービスです。AI、iPaaS、および先端の技術を駆使して、製造プロセスの効率化、業務効率化、チームワーク強化、コスト削減、品質向上を実現します。このサービスは、製造業の課題を深く理解し、それに対する最適なデジタルソリューションを提供することで、企業が持続的な成長とイノベーションを達成できるようサポートします。
オンライン講座
製造業、主に購買・調達部門にお勤めの方々に向けた情報を配信しております。
新任の方やベテランの方、管理職を対象とした幅広いコンテンツをご用意しております。
お問い合わせ
コストダウンが利益に直結する術だと理解していても、なかなか前に進めることができない状況。そんな時は、newjiのコストダウン自動化機能で大きく利益貢献しよう!
(Β版非公開)