- お役立ち記事
- How to share information with suppliers necessary for quality control of imported procured products
月間76,176名の
製造業ご担当者様が閲覧しています*
*2025年3月31日現在のGoogle Analyticsのデータより
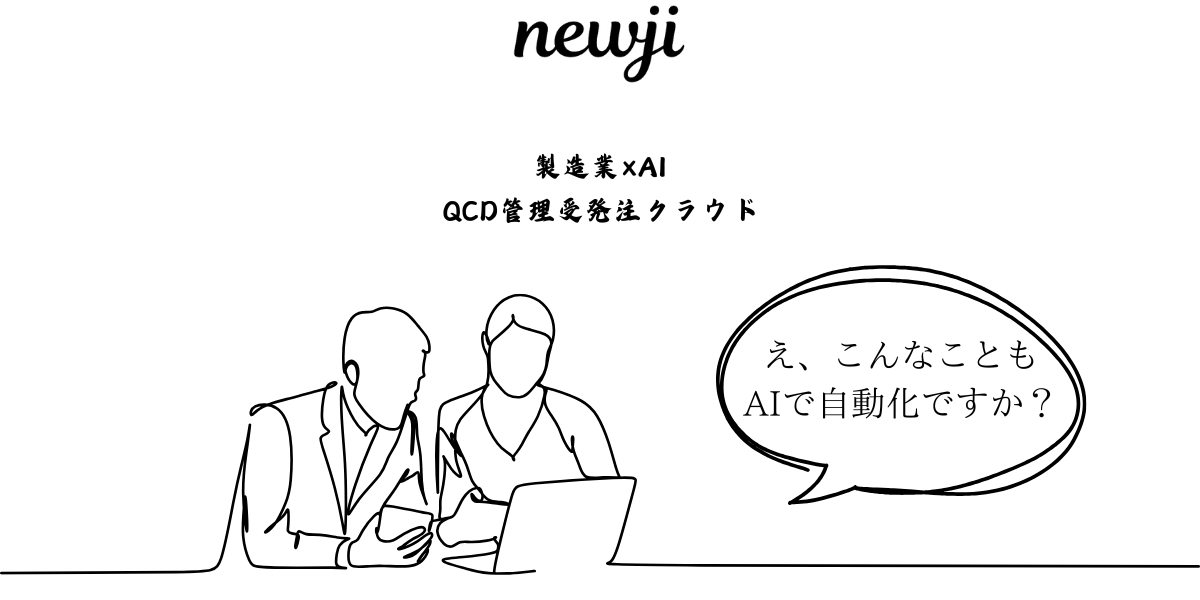
How to share information with suppliers necessary for quality control of imported procured products
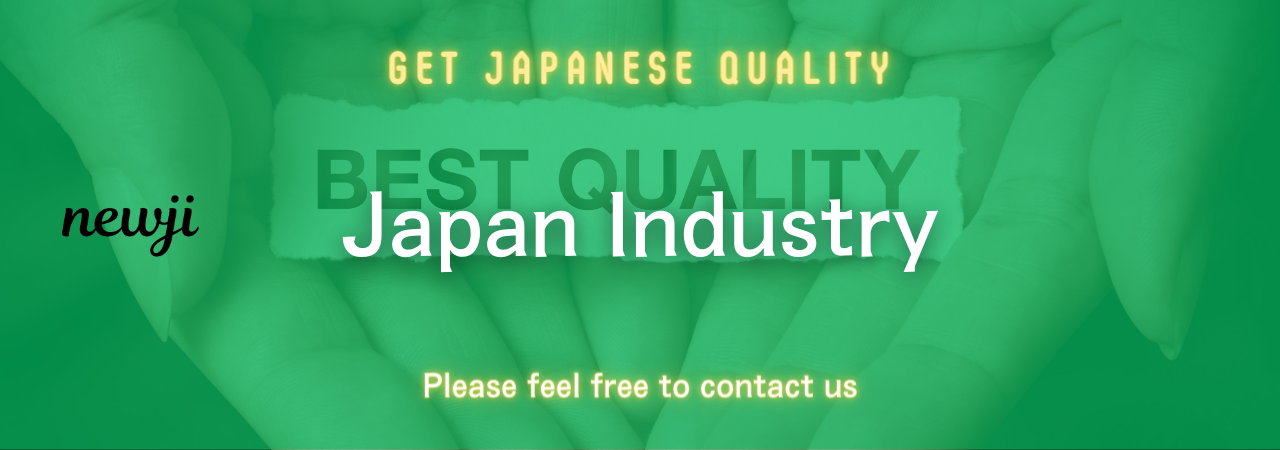
Understanding the Importance of Quality Control
Quality control is a crucial aspect of any business that deals with imported procured products.
It ensures that the products meet the required standards and specifications before they reach the end-user.
Having a robust quality control process minimizes risks, reduces costs associated with returns and complaints, and enhances customer satisfaction.
Sharing information with suppliers is a vital part of maintaining high-quality standards.
Establishing Clear Communication Channels
The first step in sharing information with suppliers for quality control is establishing clear communication channels.
This can be achieved by setting up regular meetings, using reliable communication tools, and maintaining a shared documentation system.
Regular meetings can help in discussing quality standards, addressing any issues, and making necessary adjustments in the processes.
Using communication tools like email, instant messaging, and collaborative platforms can streamline information sharing.
These tools should be accessible to both parties and provide a reliable way to convey messages swiftly and accurately.
Moreover, using a shared documentation system like cloud storage allows both suppliers and buyers to have real-time access to important documents, specifications, and changes.
Defining Quality Standards and Specifications
It is essential to define clear quality standards and specifications before the procurement process begins.
These should be based on customer expectations, industry standards, and regulatory requirements.
Sharing these specifications with suppliers ensures they know exactly what is expected in terms of product quality.
Quality standards might include dimensions, materials, functionality, and appearance, among other factors.
Providing detailed specifications will help suppliers understand the exact requirements and minimize the risk of errors.
This can be supplemented by providing samples or prototypes to give suppliers a clearer understanding of the expected outcome.
Regularly Updating Suppliers on Quality Requirements
Quality requirements may change over time due to various factors like changes in market demands or regulatory updates.
Keeping suppliers informed about these changes is crucial for maintaining quality standards.
Regular updates ensure suppliers can implement necessary adjustments in their production processes.
Using newsletters or updates via the chosen communication channels can be an effective way to keep suppliers informed.
This approach ensures they are always up-to-date with any changes and can respond promptly to new requirements.
Implementing Supplier Audits and Assessments
Conducting regular supplier audits and assessments is an effective way to ensure compliance with quality standards.
These audits can be scheduled periodically or conducted randomly to assess the supplier’s processes and product quality.
The audit can include a review of the supplier’s production processes, quality control measures, and their compliance with agreed standards.
Providing the supplier with feedback from audits allows them to improve and correct any issues identified.
This not only maintains product quality but also strengthens the supplier-buyer relationship.
Encouraging Open Feedback from Suppliers
Feedback is a two-way street.
While providing feedback to suppliers is essential, encouraging open feedback from them is equally important.
Suppliers might have insights that can lead to improved processes or practices.
By creating an environment where suppliers feel comfortable sharing their thoughts, you promote collaboration and continuous improvement.
This open dialogue can help identify potential issues before they become significant problems and can lead to innovations that benefit both parties.
Utilizing Technology for Quality Control
Technology plays a pivotal role in modern quality control processes.
Utilizing advanced technology like data analytics, AI, and machine learning can enhance the accuracy and efficiency of quality control.
Implementing software that automates quality checks and monitors the production process can provide real-time data and insights.
These tools can help identify patterns and predict potential quality issues before they arise, allowing for proactive measures.
Additionally, employing digital platforms for documentation and reporting ensures all parties have access to the most current information, facilitating better decision-making and coordination.
Training and Development Programs for Suppliers
Investing in training and development programs for suppliers is a strategic move for ensuring quality.
These programs should focus on sharing the latest industry best practices, quality control techniques, and standards compliance.
By equipping suppliers with the necessary knowledge and skills, you ensure they are capable of delivering products that meet the desired quality standards.
Training sessions can be conducted on-site or virtually, depending on the logistics and availability.
Providing certifications or acknowledgments upon completion of these programs can also incentivize suppliers to participate and continue focusing on quality enhancement.
Establishing a Strong Partnership
Finally, building a strong partnership with suppliers is fundamental for effective information sharing and quality control.
This partnership should be based on trust, mutual respect, and shared goals.
By treating suppliers as partners rather than mere vendors, you foster an environment of collaboration and communication.
This leads to a better understanding of each other’s needs and challenges, ultimately resulting in improved quality and efficiency.
In conclusion, sharing information with suppliers is pivotal for the quality control of imported procured products.
By establishing clear communication, defining and updating quality standards, conducting supplier audits, utilizing technology, and fostering a strong partnership, businesses can ensure high-quality imports that meet or exceed customer expectations.
資料ダウンロード
QCD管理受発注クラウド「newji」は、受発注部門で必要なQCD管理全てを備えた、現場特化型兼クラウド型の今世紀最高の受発注管理システムとなります。
ユーザー登録
受発注業務の効率化だけでなく、システムを導入することで、コスト削減や製品・資材のステータス可視化のほか、属人化していた受発注情報の共有化による内部不正防止や統制にも役立ちます。
NEWJI DX
製造業に特化したデジタルトランスフォーメーション(DX)の実現を目指す請負開発型のコンサルティングサービスです。AI、iPaaS、および先端の技術を駆使して、製造プロセスの効率化、業務効率化、チームワーク強化、コスト削減、品質向上を実現します。このサービスは、製造業の課題を深く理解し、それに対する最適なデジタルソリューションを提供することで、企業が持続的な成長とイノベーションを達成できるようサポートします。
製造業ニュース解説
製造業、主に購買・調達部門にお勤めの方々に向けた情報を配信しております。
新任の方やベテランの方、管理職を対象とした幅広いコンテンツをご用意しております。
お問い合わせ
コストダウンが利益に直結する術だと理解していても、なかなか前に進めることができない状況。そんな時は、newjiのコストダウン自動化機能で大きく利益貢献しよう!
(β版非公開)