- お役立ち記事
- How to solve global procurement issues tackled by mid-level manufacturing employees
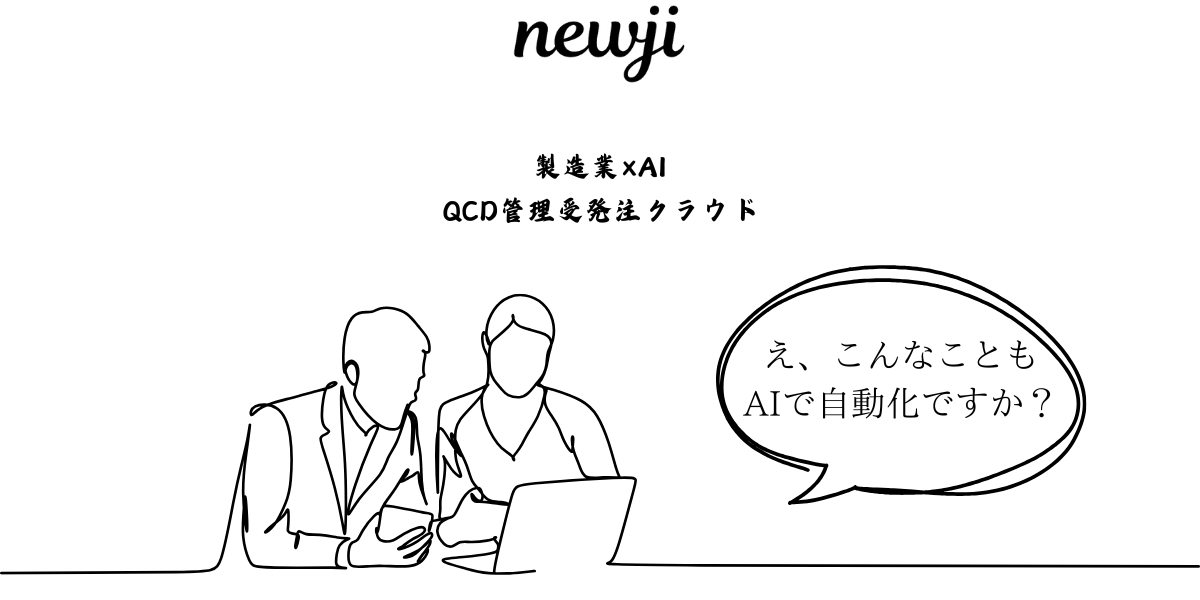
How to solve global procurement issues tackled by mid-level manufacturing employees
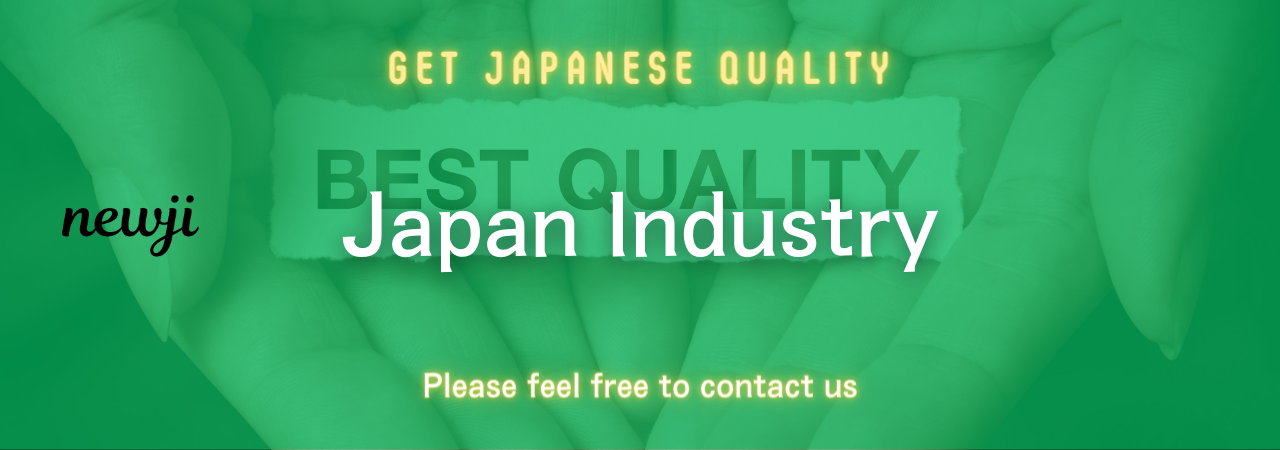
目次
Understanding Global Procurement Challenges
Mid-level manufacturing employees often face a variety of challenges in global procurement.
These challenges range from dealing with complex supply chains to managing international regulations and market volatility.
Understanding these issues is the first step toward finding effective solutions.
Global procurement involves sourcing goods and services from suppliers located all over the world.
While it offers numerous benefits such as cost savings, access to unique resources, and diversified risk, it also introduces several complications.
These include communication barriers, logistical issues, currency fluctuations, and compliance with international trade laws.
For mid-level manufacturing employees, navigating these complexities can be daunting yet essential for maintaining smooth operations and competitive advantage.
Communication Barriers and Cultural Differences
Effective communication is crucial in managing global procurement.
Language differences can lead to misunderstandings, impacting everything from contract negotiations to everyday interactions.
For mid-level employees, it’s important to both develop language skills and leverage translation tools to minimize misunderstandings.
Cultural differences also play a significant role in global procurement.
Different countries have varying business etiquettes and negotiation styles.
Manufacturing employees should undergo cultural awareness training to better understand and respect these differences.
Building strong relationships with international suppliers requires sensitivity and adaptability to these cultural nuances.
Managing Supply Chain Complexity
Global supply chains are inherently complex due to the numerous moving parts that span across borders.
Mid-level manufacturing employees must keep track of multiple suppliers, transportation routes, and regulatory requirements, all of which can result in delays and increased costs if not managed efficiently.
One effective solution is the integration of advanced supply chain management systems.
These systems provide real-time data and analytics that help employees monitor and predict potential disruptions.
By using technology to gain visibility into every aspect of the supply chain, employees can make informed decisions and quickly address problems as they arise.
Dealing with Currency Fluctuations
Currency fluctuations are another challenge in global procurement.
Exchange rates can vary significantly, affecting the cost of imported goods.
Mid-level employees must develop strategies to mitigate the risk of these fluctuations.
One approach is to use financial hedging techniques, such as forward contracts or options, to lock in exchange rates for future transactions.
Partnering with financial experts or consultants can also help employees understand and implement these strategies effectively.
Additionally, maintaining a diversified supplier base can provide flexibility and options in case of adverse currency movements.
Navigating Regulatory and Compliance Issues
Compliance with international trade laws is critical for successful global procurement.
Regulations can vary widely from country to country and can include tariffs, import quotas, and safety standards.
Mid-level manufacturing employees must stay informed about these regulations to avoid legal complications and fines.
Developing a robust compliance management system is essential.
This system should keep track of all the relevant legislation in each country and ensure that procurement activities adhere to these regulations.
Regular training and updates for employees can also go a long way in maintaining compliance.
Strengthening Supplier Relationships
Strong, reliable relationships with suppliers are the backbone of successful global procurement.
Beyond transactional interactions, mid-level manufacturing employees should focus on building partnerships based on trust and mutual benefit.
Regular communication, performance evaluations, and collaboration on process improvements can lead to enhanced supplier relationships.
Creating a supplier relationship management program can be beneficial, allowing employees to systematically track and enhance these relationships over time.
Solutions for Improving Global Procurement
While there are many challenges associated with global procurement, there are also numerous strategies that mid-level manufacturing employees can employ to overcome these obstacles and enhance their procurement processes.
Investing in Technology
Technology plays an integral role in streamlining global procurement processes.
Advanced software solutions can automate routine tasks, provide data analytics, and improve supply chain visibility.
Investing in such technology enables mid-level employees to free up valuable time, allowing them to focus on strategic decision-making rather than administrative duties.
Furthermore, technology can enhance communication across different regions and languages.
Collaboration platforms and digital communication tools help maintain seamless interaction with global suppliers regardless of location or time zone.
Developing Cross-Functional Teams
Global procurement is not a siloed activity but rather one that involves multiple departments such as finance, logistics, and legal.
Developing cross-functional teams within the organization ensures that all aspects of procurement are covered, and diverse perspectives are included in problem-solving efforts.
Mid-level manufacturing employees should foster an environment where knowledge sharing is encouraged, and team members are motivated to contribute.
Cross-functional collaboration helps identify potential issues early and improve overall procurement efficiency.
Continuous Learning and Adaptation
The global market is ever-changing, with new challenges emerging regularly.
Continuous learning and adaptation are crucial for staying ahead.
Mid-level manufacturing employees should pursue ongoing education and training opportunities in global procurement trends, technologies, and best practices.
Participating in industry conferences, workshops, and webinars provides fresh insights and potential solutions for current procurement challenges.
Establishing a culture of lifelong learning within the manufacturing organization can enhance innovation and agility.
Conclusion
Global procurement presents several challenges for mid-level manufacturing employees, from navigating complex supply chains to managing regulatory compliance.
However, with a proactive approach and strategic implementation of technology and collaboration, these challenges can be effectively addressed.
Through cultural awareness, cross-functional teamwork, and continuous learning, employees can enhance their global procurement processes, ensuring supply chain reliability and fostering a competitive edge in the market.
Ultimately, by solving procurement issues, manufacturers can achieve not only operational efficiency but also enhance their global standing and profitability.
資料ダウンロード
QCD調達購買管理クラウド「newji」は、調達購買部門で必要なQCD管理全てを備えた、現場特化型兼クラウド型の今世紀最高の購買管理システムとなります。
ユーザー登録
調達購買業務の効率化だけでなく、システムを導入することで、コスト削減や製品・資材のステータス可視化のほか、属人化していた購買情報の共有化による内部不正防止や統制にも役立ちます。
NEWJI DX
製造業に特化したデジタルトランスフォーメーション(DX)の実現を目指す請負開発型のコンサルティングサービスです。AI、iPaaS、および先端の技術を駆使して、製造プロセスの効率化、業務効率化、チームワーク強化、コスト削減、品質向上を実現します。このサービスは、製造業の課題を深く理解し、それに対する最適なデジタルソリューションを提供することで、企業が持続的な成長とイノベーションを達成できるようサポートします。
オンライン講座
製造業、主に購買・調達部門にお勤めの方々に向けた情報を配信しております。
新任の方やベテランの方、管理職を対象とした幅広いコンテンツをご用意しております。
お問い合わせ
コストダウンが利益に直結する術だと理解していても、なかなか前に進めることができない状況。そんな時は、newjiのコストダウン自動化機能で大きく利益貢献しよう!
(Β版非公開)