- お役立ち記事
- How to streamline custom parts procurement in the machinery industry
How to streamline custom parts procurement in the machinery industry
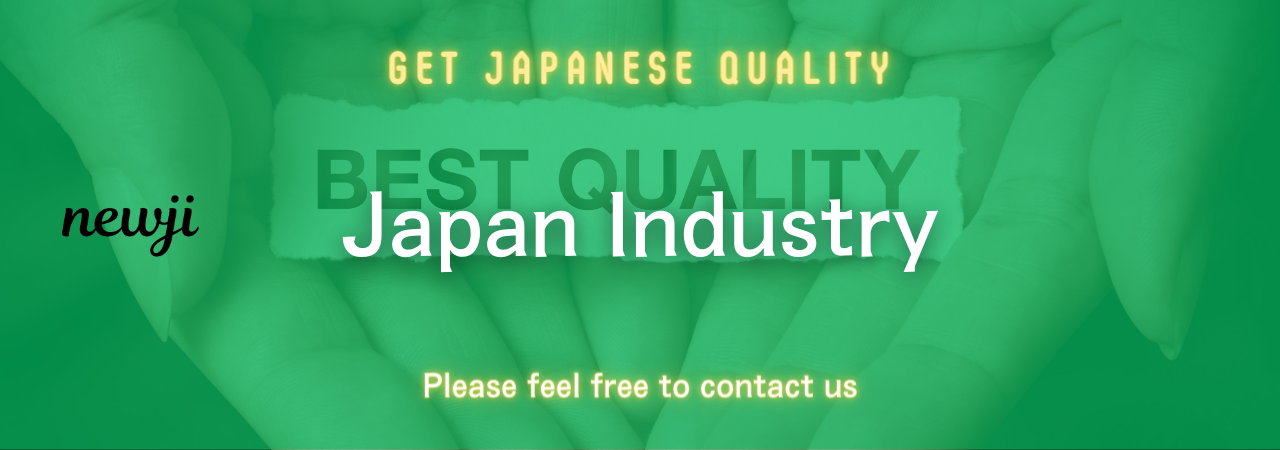
目次
Introduction to Custom Parts Procurement
The machinery industry is a complex and vibrant sector characterized by its need for precision, efficiency, and customization.
Custom parts procurement plays a vital role in ensuring that machinery functions correctly and meets specific operational requirements.
Yet, this process can be remarkably challenging, involving intricate specifications, rapid advancements, and fluctuating demand.
In this article, we’ll explore effective strategies to streamline custom parts procurement.
By doing so, businesses can enhance productivity, reduce expenses, and ensure a reliable supply chain.
Understanding the Challenges
Before considering procurement efficiency, it’s essential to recognize the inherent challenges within the custom parts procurement process.
Industries often face hurdles such as diverse supplier networks, varying quality standards, and unpredictable lead times.
These elements can complicate procurement efforts immensely.
Moreover, the task of aligning these challenges with a company’s unique needs can be daunting without a well-structured approach to procurement.
Diverse Supplier Network
Dealing with a wide array of suppliers can lead to complications.
Each supplier might have distinct processes, pricing structures, and delivery timelines.
Maintaining healthy relationships while ensuring consistent quality presents a notable challenge.
Inconsistent Quality Standards
When procuring custom parts, it is vital to maintain consistency in quality.
Variations can lead to significant delays and increased costs to rectify errors.
Ensuring that all suppliers adhere to stringent quality standards is imperative for seamless operations.
Fluctuating Lead Times
Unpredictable lead times can disrupt production schedules and lead to inefficiencies.
Without careful management, these fluctuations may affect the company’s ability to meet customer demands, ultimately impacting profitability.
Strategies to Streamline Procurement
With a clearer understanding of the challenges, businesses can implement strategies that simplify the custom parts procurement process.
These strategies center around optimizing supplier relationships, leveraging technology, and investing in resources.
Developing Strong Supplier Relationships
Building robust relationships with suppliers can transform the procurement process.
Open communication and collaboration ensure that both parties are aligned in terms of delivery schedules, quality, and cost expectations.
Create a clear and detailed contract that outlines the expectations and requirements.
Regularly review supplier performance, provide feedback, and encourage adherence to industry standards.
By fostering trust and mutual benefits, the procurement process becomes much smoother.
Leveraging Technology
Technology can play a crucial role in streamlining the procurement process.
Using modern tools and systems can help track, analyze, and optimize procurement activities, leading to improved efficiency.
Implementing Enterprise Resource Planning (ERP) systems allows companies to manage procurement activities in one centralized platform.
Such systems support inventory tracking, automate order processes, and provide real-time updates.
Additionally, e-procurement solutions can reduce administrative costs and minimize errors through digitization.
Embracing Data Analytics
Harnessing the power of data analytics offers valuable insights into procurement patterns.
This information assists in better forecasting demand, identifying cost-saving opportunities, and making informed decisions.
Custom parts procurement often involves fluctuating supply and demand.
Analytical tools can model different scenarios to prepare for potential disruptions, ensuring more resilient procurement practices.
Optimizing Inventory Management
Efficient inventory management goes hand-in-hand with effective procurement.
Balancing inventory levels to meet demand without overstocking can reduce carrying costs and free up capital.
Implementing Just-in-Time Inventory
Adopting Just-in-Time (JIT) inventory strategies helps in reducing waste and minimizing inventory holding costs.
This strategy involves receiving goods only as they are needed in the production process, thereby optimizing inventory levels.
Utilizing Vendor-Managed Inventory
Vendor-Managed Inventory (VMI) is another effective strategy where the supplier manages the inventory levels based on agreed standards.
This approach streamlines logistics and reduces the burden on the procurement team, ensuring a steady supply of necessary parts.
Enhancing Communication and Collaboration
Communication is the cornerstone of a successful procurement process.
Facilitating seamless collaboration between departments, suppliers, and stakeholders is crucial.
Promoting Interdepartmental Collaboration
Encouraging better communication between procurement, engineering, and production departments can lead to understanding requirements more precisely.
This ensures that all stakeholders are in agreement and reduces the chances of miscommunication affecting procurement.
Utilizing Collaborative Platforms
Utilizing collaborative digital platforms helps every team member stay informed and aligned.
These platforms provide a centralized hub where updates, changes, and critical information can be communicated swiftly and effectively.
Conclusion
Streamlining custom parts procurement requires a strategic approach focusing on supplier management, technology adoption, and enhanced communication.
Understanding the challenges and implementing targeted strategies can significantly improve the procurement process, resulting in cost savings and operational efficiency.
In the ever-evolving machinery industry, maintaining an agile and resilient procurement process is crucial to sustaining growth and competitive advantage.
By refining these processes, businesses can ensure the steady production of high-quality machinery and meet the demands of their customers effectively.
資料ダウンロード
QCD調達購買管理クラウド「newji」は、調達購買部門で必要なQCD管理全てを備えた、現場特化型兼クラウド型の今世紀最高の購買管理システムとなります。
ユーザー登録
調達購買業務の効率化だけでなく、システムを導入することで、コスト削減や製品・資材のステータス可視化のほか、属人化していた購買情報の共有化による内部不正防止や統制にも役立ちます。
NEWJI DX
製造業に特化したデジタルトランスフォーメーション(DX)の実現を目指す請負開発型のコンサルティングサービスです。AI、iPaaS、および先端の技術を駆使して、製造プロセスの効率化、業務効率化、チームワーク強化、コスト削減、品質向上を実現します。このサービスは、製造業の課題を深く理解し、それに対する最適なデジタルソリューションを提供することで、企業が持続的な成長とイノベーションを達成できるようサポートします。
オンライン講座
製造業、主に購買・調達部門にお勤めの方々に向けた情報を配信しております。
新任の方やベテランの方、管理職を対象とした幅広いコンテンツをご用意しております。
お問い合わせ
コストダウンが利益に直結する術だと理解していても、なかなか前に進めることができない状況。そんな時は、newjiのコストダウン自動化機能で大きく利益貢献しよう!
(Β版非公開)