- お役立ち記事
- How to strengthen supplier collaboration to reduce transportation costs
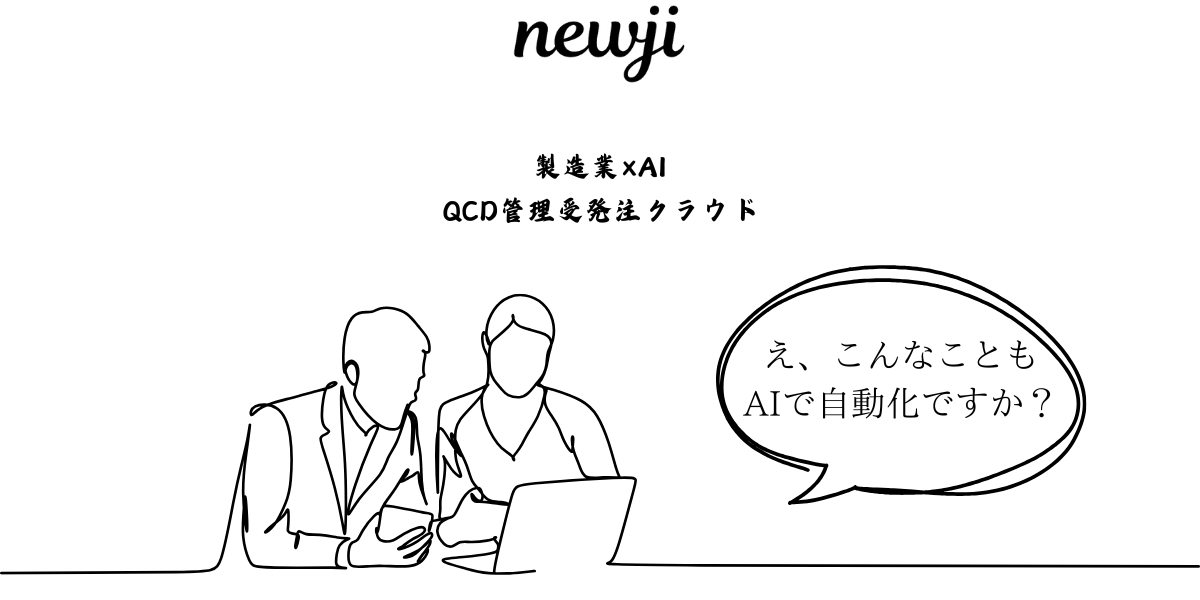
How to strengthen supplier collaboration to reduce transportation costs
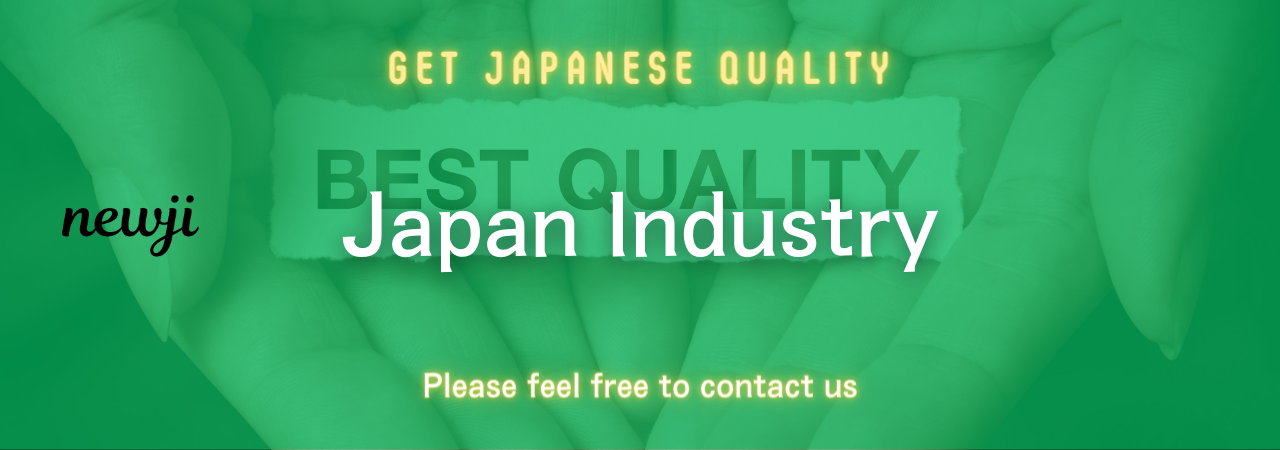
目次
Understanding Supplier Collaboration
Effective supplier collaboration has become a critical component in optimizing supply chain operations.
By establishing strong partnerships with suppliers, businesses can significantly reduce transportation costs, enhance operational efficiency, and promote mutual growth.
Supplier collaboration involves working closely with your suppliers to develop a synergy that benefits both parties, enabling shared goals and priorities.
Successful collaboration encompasses transparent communication, shared technologies, integrated planning, and aligned objectives.
Building trust and developing strong relationships are foundational elements that ensure seamless cooperation between businesses and their suppliers.
Such collaboration does not only involve exchanging information but extends to strategic planning and problem-solving, which are key to reducing transportation costs.
Key Strategies for Strengthening Supplier Collaboration
Fostering Open Communication
For effective collaboration, open and transparent communication is crucial.
Regular communication with suppliers helps in understanding their logistics capabilities, challenges, and opportunities.
It’s essential to establish channels through which both parties can share real-time information regarding demand forecasts, inventory levels, and transportation logistics.
Frequent meetings and updates can ensure that everyone is on the same page, which helps in aligning goals and expectations.
Streamlining Processes with Technology
Integrating technology into supply chain operations can significantly enhance collaboration with suppliers.
Using supply chain management software allows for better coordination and real-time tracking of shipments and inventory.
Tools such as Electronic Data Interchange (EDI) and cloud-based platforms facilitate efficient data sharing, reduce manual errors, and improve communication speed.
Automation of routine tasks can free up resources, allowing suppliers and businesses to focus on more strategic aspects of supply chain management.
Joint Planning and Forecasting
Coordinated planning and forecasting with suppliers can lead to significant reductions in transportation costs.
By sharing forecasts and demand data, both parties can plan better for future needs and optimize inventory management.
Collaborative planning involves jointly agreeing on delivery schedules, order quantities, and restocking timelines.
This ensures that transportation is efficiently managed, reducing the need for rushed, costlier shipping methods.
Negotiating Better Terms
Negotiating favorable terms with suppliers can directly impact transportation costs.
Businesses should seek to establish long-term contracts with suppliers that offer better rates for bulk purchases or frequent shipping.
Volume-based discounts, flexible payment terms, or shared-cost agreements for transportation can also be beneficial.
Engaging in regular reviews of contracts ensures they remain competitive and fair, adapting to any industry changes or new logistical needs.
Optimizing Transportation Networks
Working collaboratively to optimize transportation networks is another effective strategy.
This involves route optimization, load planning, and leveraging backhaul opportunities.
Engaging suppliers in discussions about logistics can uncover potential improvements in delivery routes or methods.
Shared transportation can minimize empty trips, thereby reducing overall transportation costs.
Advanced analytics and routing software can assist in choosing the most cost-efficient and environmentally friendly routes.
Supplier Performance Management
Monitoring supplier performance is essential to maintaining and improving collaboration.
Businesses should develop key performance indicators (KPIs) related to timely deliveries, transportation costs, and service quality.
Regular performance reviews with suppliers can help identify areas needing improvement and recognize success.
Rewarding top-performing suppliers encourages continued excellence and innovation in cost-reduction strategies.
Benefits of Strong Supplier Collaboration
Cost Savings and Efficiency
One of the primary advantages of robust supplier collaboration is the significant reduction in transportation costs.
Efficient planning, joint optimization, and bulk shipping discounts contribute directly to cost savings.
Furthermore, streamlined processes enhance overall supply chain efficiency, reducing lead times and minimizing disruptions.
Improved Supply Chain Resilience
Through strengthened collaboration, businesses and their suppliers can better anticipate and respond to potential disruptions.
Shared insights and combined resources help both parties navigate challenges such as sudden changes in demand or supply chain interruptions.
This resilience is critical, particularly in today’s dynamic market environment.
Enhanced Relationship and Trust
Building strong relationships and trust with suppliers leads to more reliable and dedicated partnerships.
When suppliers and businesses are aligned in their goals, there is a shared commitment to achieving success.
These improved relationships often result in greater flexibility and a willingness to innovate collaboratively.
Greater Competitive Advantage
Competitive advantage is achieved when businesses can offer improved services at a lower cost.
Strong supplier collaboration allows for more strategic supply chain decisions, better cost management, and adaptability, providing a notable edge over competitors.
Conclusion
Strengthening supplier collaboration requires deliberate strategy and effort but offers substantial rewards.
By focusing on open communication, technology integration, joint planning, and effective negotiation, businesses can reduce their transportation costs significantly.
The benefits of robust collaboration extend beyond financial savings; they include enhanced efficiency, agility, and stronger supplier relationships.
As the global market continues to evolve, businesses that excel in supplier collaboration will find themselves better equipped to compete and succeed.
資料ダウンロード
QCD調達購買管理クラウド「newji」は、調達購買部門で必要なQCD管理全てを備えた、現場特化型兼クラウド型の今世紀最高の購買管理システムとなります。
ユーザー登録
調達購買業務の効率化だけでなく、システムを導入することで、コスト削減や製品・資材のステータス可視化のほか、属人化していた購買情報の共有化による内部不正防止や統制にも役立ちます。
NEWJI DX
製造業に特化したデジタルトランスフォーメーション(DX)の実現を目指す請負開発型のコンサルティングサービスです。AI、iPaaS、および先端の技術を駆使して、製造プロセスの効率化、業務効率化、チームワーク強化、コスト削減、品質向上を実現します。このサービスは、製造業の課題を深く理解し、それに対する最適なデジタルソリューションを提供することで、企業が持続的な成長とイノベーションを達成できるようサポートします。
オンライン講座
製造業、主に購買・調達部門にお勤めの方々に向けた情報を配信しております。
新任の方やベテランの方、管理職を対象とした幅広いコンテンツをご用意しております。
お問い合わせ
コストダウンが利益に直結する術だと理解していても、なかなか前に進めることができない状況。そんな時は、newjiのコストダウン自動化機能で大きく利益貢献しよう!
(Β版非公開)