- お役立ち記事
- How to successfully produce a heat-resistant metal injection molding prototype in Goshogawara City
月間76,176名の
製造業ご担当者様が閲覧しています*
*2025年3月31日現在のGoogle Analyticsのデータより
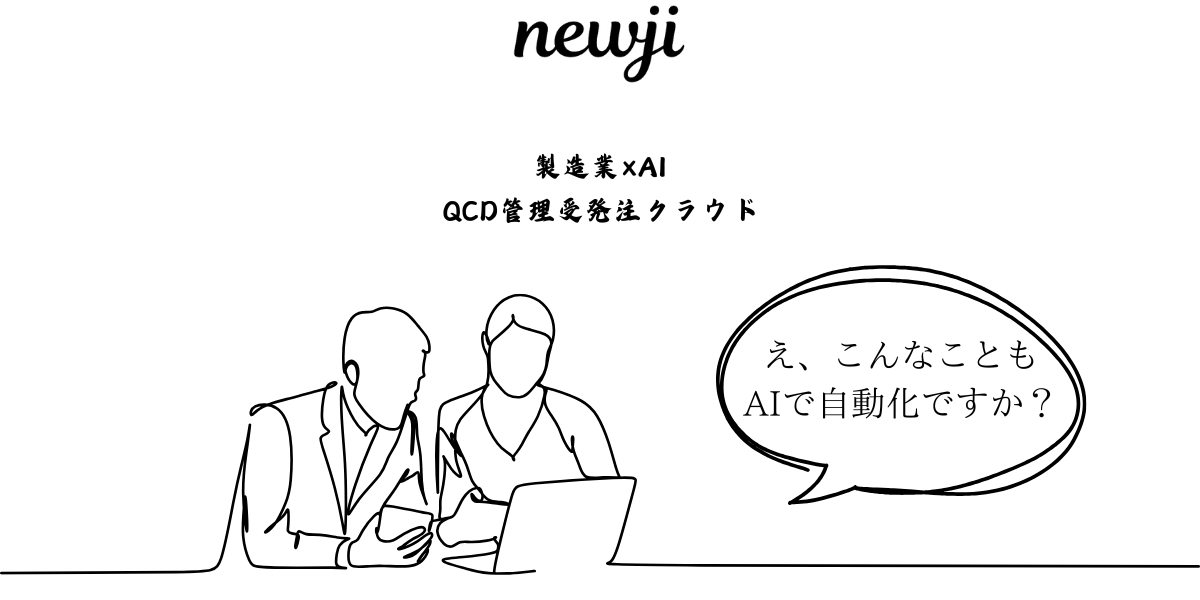
How to successfully produce a heat-resistant metal injection molding prototype in Goshogawara City
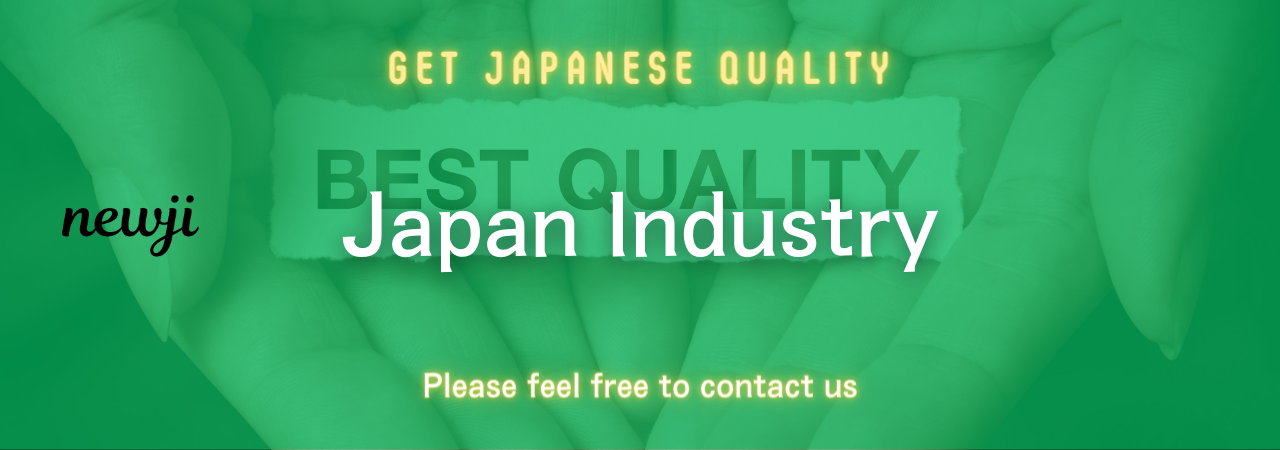
目次
Introduction to Metal Injection Molding
Metal injection molding (MIM) is a popular manufacturing process used to create intricate metal parts with high precision and consistency.
This process combines the benefits of plastic injection molding with the strength and durability of metal.
MIM is particularly useful for producing components with complex geometries and is widely used in industries such as automotive, aerospace, and medical devices.
Generating prototypes using metal injection molding is a vital step in the product development process.
In Goshogawara City, known for its expertise in advanced manufacturing techniques, creating a successful heat-resistant metal injection molding prototype requires understanding the nuances of this process.
Understanding the MIM Process
The metal injection molding process begins with a metal powder and a binding agent.
These materials are combined to form a feedstock that can be injected into a mold.
Once injected, the molded part, known as a “green part,” undergoes a series of debinding and sintering processes.
Debinding removes the binder, while sintering heats the part to a temperature where the metal particles bond together without melting.
This results in a dense and strong finished product.
The ability to achieve intricate designs with minimal material wastage makes MIM an attractive option for prototype production.
Why Heat-Resistance Matters
In various industries, components are often required to withstand high temperatures.
This demand is common in sectors like automotive, where engine parts are exposed to extreme heat, or in electronics, where components must endure elevated temperatures without degrading.
Producing a heat-resistant metal injection molding prototype ensures that the final product will perform reliably under harsh conditions without compromising structural integrity.
Choosing the Right Metal Powder
Selecting the appropriate metal powder is crucial when aiming for heat resistance.
Materials such as stainless steel, titanium, and certain metal alloys are commonly used for their ability to withstand high temperatures.
In Goshogawara City, manufacturers have access to state-of-the-art facilities and resources, enabling them to select the best materials for prototype development.
Understanding the specific requirements of your prototype, like the expected temperature range and mechanical stress, will guide you in choosing the right metal powder.
Partnering with Local Experts
Goshogawara City boasts a wealth of expertise in metalworking and mold design.
Collaborating with local experts can significantly enhance the success of your prototype project.
Experienced professionals can provide insights into the best practices for metal selection, mold design, and process optimization.
Moreover, they are familiar with the latest technological advancements, which can be incorporated into your prototype for improved performance.
Designing the Mold
The mold design plays a critical role in producing successful metal injection molded prototypes.
It determines the final shape, precision, and quality of the product.
Incorporating features like undercuts, complex geometries, or thin walls necessitates careful consideration during the design phase.
Advanced CAD software is typically used to create detailed mold designs tailored to the specific requirements of the prototype.
Focus on Mold Materials
The mold materials must withstand repeated use under high pressures and temperatures.
Typically, tool steel is used for mold construction due to its high strength and resistance to wear.
Selecting the correct mold material ensures longevity and dimensional accuracy across multiple prototype iterations, contributing to cost-effectiveness and efficiency in the long run.
Optimizing the Injection Molding Process
Controlling various parameters during the injection molding process is vital for a successful outcome.
Factors such as injection speed, pressure, and temperature must be meticulously adjusted to prevent defects like warping or shrinkage.
Implementing precise monitoring and control systems helps maintain these parameters within the desired range, ensuring high-quality prototypes.
Utilizing Advanced Technology
The use of advanced technologies, including simulation software and real-time monitoring systems, can dramatically enhance the efficiency and success of the metal injection molding process.
These tools help identify potential issues before they occur, allowing for adjustments that save time and resources.
Tech-savvy manufacturers in Goshogawara City often integrate such technologies into their operations, delivering superior prototype results.
Testing and Validation
Once the prototype is produced, rigorous testing and validation are necessary to ensure it meets all performance criteria.
Tests may include stress analysis, thermal resistance assessment, and quality inspections.
These evaluations verify that the prototype can perform as required under real-world conditions.
Incorporating feedback into subsequent prototype iterations can lead to improved performance and reliability.
Iterative Approach
Developing a successful heat-resistant prototype often involves an iterative approach.
This means multiple versions of the prototype may be produced and tested to refine performance.
Each iteration offers valuable data that informs enhancements in design and process parameters.
Adopting this approach increases the likelihood of achieving an optimal final product.
Conclusion
Producing a heat-resistant metal injection molding prototype in Goshogawara City requires a comprehensive understanding of the MIM process, careful material selection, and precise mold design.
Local expertise and advanced technologies play a significant role in optimizing production and ensuring successful prototype development.
By focusing on these areas and embracing an iterative approach, manufacturers can produce high-quality prototypes that meet stringent heat resistance requirements and pave the way for successful product launches.
資料ダウンロード
QCD管理受発注クラウド「newji」は、受発注部門で必要なQCD管理全てを備えた、現場特化型兼クラウド型の今世紀最高の受発注管理システムとなります。
ユーザー登録
受発注業務の効率化だけでなく、システムを導入することで、コスト削減や製品・資材のステータス可視化のほか、属人化していた受発注情報の共有化による内部不正防止や統制にも役立ちます。
NEWJI DX
製造業に特化したデジタルトランスフォーメーション(DX)の実現を目指す請負開発型のコンサルティングサービスです。AI、iPaaS、および先端の技術を駆使して、製造プロセスの効率化、業務効率化、チームワーク強化、コスト削減、品質向上を実現します。このサービスは、製造業の課題を深く理解し、それに対する最適なデジタルソリューションを提供することで、企業が持続的な成長とイノベーションを達成できるようサポートします。
製造業ニュース解説
製造業、主に購買・調達部門にお勤めの方々に向けた情報を配信しております。
新任の方やベテランの方、管理職を対象とした幅広いコンテンツをご用意しております。
お問い合わせ
コストダウンが利益に直結する術だと理解していても、なかなか前に進めることができない状況。そんな時は、newjiのコストダウン自動化機能で大きく利益貢献しよう!
(β版非公開)