- お役立ち記事
- How to use alternative suppliers to help purchasing departments reduce the risk of material shortages
How to use alternative suppliers to help purchasing departments reduce the risk of material shortages
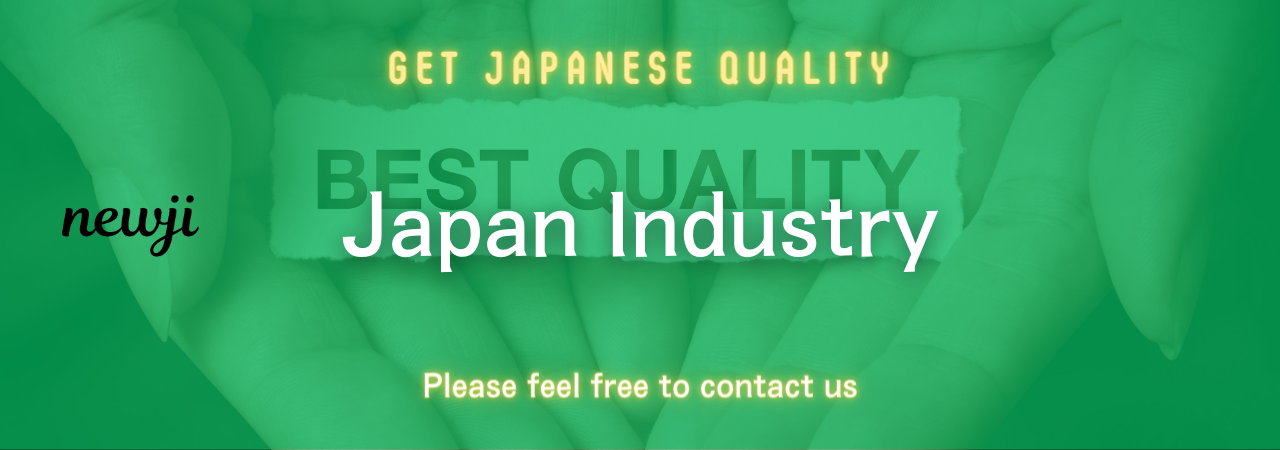
目次
Understanding the Role of Alternative Suppliers
In the ever-evolving landscape of global supply chains, purchasing departments face a significant challenge: material shortages.
These shortages can disrupt production, leading to delays and increased costs.
One effective strategy to mitigate this risk is leveraging alternative suppliers.
Alternative suppliers are secondary or backup sources for purchasing goods and materials.
They provide flexibility and security by ensuring that a company is not solely reliant on a single supplier.
In doing so, they help maintain a steady flow of necessary materials, even when unforeseen circumstances arise with primary suppliers.
The Benefits of Using Alternative Suppliers
The key benefit of utilizing alternative suppliers is the reduction of dependency.
When a company relies solely on one supplier, any disruption on the supplier’s end—be it due to politics, natural disasters, or financial issues—can severely impact the company’s operations.
By having alternative suppliers, businesses can quickly pivot to another source, minimizing negative impacts.
Another advantage is cost optimization.
With multiple suppliers, a company can engage in competitive bidding, ensuring that they get the best deal possible.
It also encourages primary suppliers to maintain competitive pricing and quality, knowing that alternatives are readily available.
Alternative suppliers can also offer diversification of risks.
If one supplier experiences a bottleneck due to region-specific issues, a company can shift its requirements to a supplier in a unaffected area.
This geographic diversification spreads risk and can safeguard against region-specific disruptions.
Implementing a Strategy for Alternative Suppliers
Establishing a network of alternative suppliers requires careful planning and execution.
Here are some steps purchasing departments should consider:
Assess Current Supplier Dependencies
The first step is to conduct a thorough analysis of current supplier relationships.
Identify which materials or services are being purchased from single sources and evaluate the potential risks associated with them.
This assessment will help in determining which areas require alternative suppliers the most.
Research and Vet Potential Suppliers
Once dependencies are identified, the next step is to research potential suppliers.
Look for suppliers who can meet quality standards and have the capacity to deliver the necessary quantities.
It is crucial to vet these suppliers thoroughly to avoid replacing one risky supplier with another.
Consider factors such as reputation, financial health, and delivery timelines.
Establish Relationships with Alternatives
Developing strong relationships with alternative suppliers is vital.
Regular communication and engagement help build trust and ensure that the supplier understands your business needs.
It’s beneficial to foster these relationships even if they are not used frequently.
Strong alliances can be invaluable in times of emergency.
Negotiate Contracts and Terms
Once suitable suppliers are identified, negotiate terms that offer flexibility, such as price locking for a certain period or guaranteed delivery times.
Having robust contracts in place ensures that when a shift to an alternative supplier is necessary, the transition is smooth and operations remain unaffected.
Developing a Contingency Plan
Having alternative suppliers is part of a broader contingency plan.
Purchasing departments should work closely with financial and risk management teams to develop a comprehensive plan.
This plan should outline scenarios that would necessitate switching suppliers, detail procedures for doing so, and assign responsibilities to team members.
Perform regular drills to ensure that the contingency plan is actionable and that all team members are familiar with their roles.
Maintaining a Balance
While having alternative suppliers is crucial, it is also important to maintain strong partnerships with primary suppliers.
Ensure fair treatment and cultivate relationships that benefit all parties involved.
This balance aids in maintaining quality and competitive pricing, as primary suppliers are aware of the presence of competition.
Challenges and Considerations
Implementing a network of alternative suppliers is not without challenges.
There can be initial time investment and costs in researching and engaging with new suppliers.
Additionally, differing quality standards and geographic distances may pose challenges.
To address these, a strategic approach that includes thorough vetting, comparisons, and pilot testing of suppliers can mitigate potential issues.
Technology and Automation in Sourcing
Modern technology can facilitate the management of multiple suppliers.
Supply chain management software can help track supplier performance, manage orders, and predict potential risks based on real-time data.
Automation tools can streamline the ordering process, reducing errors and improving efficiency.
Conclusion
Utilizing alternative suppliers is a strategic move for purchasing departments to reduce the risk of material shortages.
By diversifying supply sources, companies can safeguard against disruptions, optimize costs, and ensure continuous production.
While there are challenges in implementing a network of alternative suppliers, the long-term benefits significantly outweigh the initial efforts.
By maintaining flexibility and adaptability through alternative suppliers, businesses can remain resilient in the face of supply chain uncertainties.
資料ダウンロード
QCD調達購買管理クラウド「newji」は、調達購買部門で必要なQCD管理全てを備えた、現場特化型兼クラウド型の今世紀最高の購買管理システムとなります。
ユーザー登録
調達購買業務の効率化だけでなく、システムを導入することで、コスト削減や製品・資材のステータス可視化のほか、属人化していた購買情報の共有化による内部不正防止や統制にも役立ちます。
NEWJI DX
製造業に特化したデジタルトランスフォーメーション(DX)の実現を目指す請負開発型のコンサルティングサービスです。AI、iPaaS、および先端の技術を駆使して、製造プロセスの効率化、業務効率化、チームワーク強化、コスト削減、品質向上を実現します。このサービスは、製造業の課題を深く理解し、それに対する最適なデジタルソリューションを提供することで、企業が持続的な成長とイノベーションを達成できるようサポートします。
オンライン講座
製造業、主に購買・調達部門にお勤めの方々に向けた情報を配信しております。
新任の方やベテランの方、管理職を対象とした幅広いコンテンツをご用意しております。
お問い合わせ
コストダウンが利益に直結する術だと理解していても、なかなか前に進めることができない状況。そんな時は、newjiのコストダウン自動化機能で大きく利益貢献しよう!
(Β版非公開)