- お役立ち記事
- How to use data analysis tools to streamline inventory management in the manufacturing industry
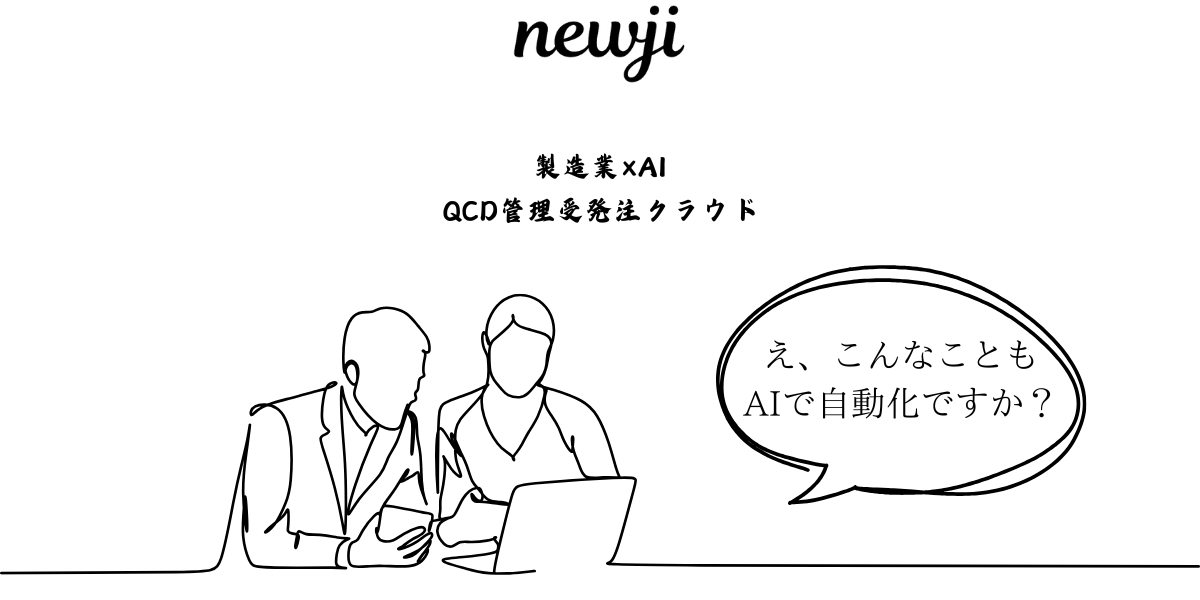
How to use data analysis tools to streamline inventory management in the manufacturing industry
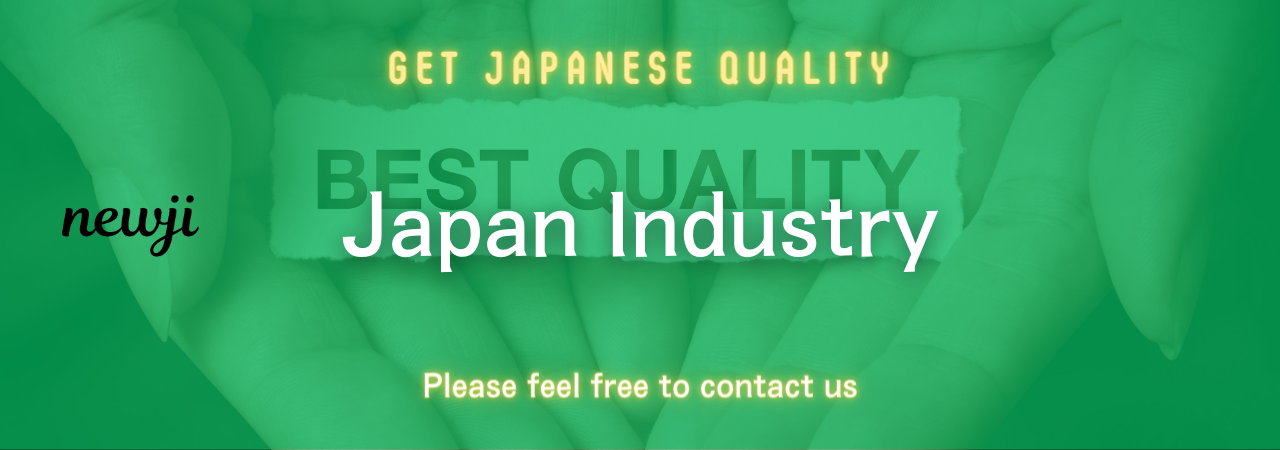
目次
Introduction to Data Analysis in Inventory Management
In the manufacturing industry, effective inventory management is crucial for maintaining production efficiency and meeting consumer demands.
Inventory management involves tracking the amount, location, and movement of stock items, which helps in minimizing excess stock and reducing storage costs.
With the advent of digital tools and data analysis, this process has become more streamlined and accurate.
Data analysis tools assist manufacturers in making informed decisions by organizing and interpreting inventory data.
By utilizing these tools, businesses can optimize inventory levels, forecast demand, and improve supply chain operations.
Understanding Data Analysis Tools
Data analysis tools come in various forms, each designed to process specific types of data and generate valuable insights.
Common tools include spreadsheets, business intelligence software, and specialized inventory management systems.
These tools enable businesses to visualize data through charts and graphs, making complex information accessible and understandable.
Spreadsheets, like Microsoft Excel and Google Sheets, offer basic data analysis capabilities.
They allow users to organize data in a tabular form, use formulas for calculations, and create simple visualizations.
Though they are widely used, they may not be ideal for complex analysis due to their limited processing power and functionality.
Business intelligence software, such as Tableau and Power BI, offers advanced data visualization and analytic abilities.
These tools facilitate the creation of dashboards that update in real-time, providing users with dynamic insights.
They are particularly useful for larger datasets as they can handle complex queries and integrate data from multiple sources.
Specialized inventory management systems, like SAP and Oracle Inventory Management, offer comprehensive solutions tailored for the manufacturing industry.
These systems automate various processes, such as order tracking, stock replenishment, and supplier management.
By integrating with other business systems, they provide a centralized platform for inventory management.
Benefits of Implementing Data Analysis in Inventory Management
Integrating data analysis tools into inventory management offers a host of benefits that can significantly improve operational efficiency and reduce costs.
Improved Demand Forecasting
One of the primary benefits is improved demand forecasting.
Accurate demand forecasts enable manufacturers to align their production schedules and inventory levels with market demands.
By analyzing historical data and market trends, data analysis tools help predict future sales, minimizing the risk of overstocking or stockouts.
Enhanced Supply Chain Efficiency
Data analysis improves supply chain efficiency by providing insights into supplier performance and lead times.
Manufacturers can use this information to select reliable suppliers and optimize their ordering processes.
With accurate data on supplier delivery times, manufacturers can adjust inventory levels accordingly, ensuring that materials are available when needed.
Reduced Inventory Costs
By streamlining inventory management, data analysis tools help reduce costs associated with excess stock and storage.
Maintaining optimal inventory levels minimizes the need for large storage spaces and reduces capital tied up in unsold goods.
Additionally, data-driven insights allow manufacturers to identify slow-moving items and take necessary actions, such as discounts or promotions, to clear them.
Enhanced Decision-Making
Data analysis empowers manufacturers to make data-driven decisions.
Through detailed reports and visualizations, businesses can identify trends, patterns, and anomalies that may impact operations.
This level of insight enables proactive decision-making, allowing companies to address potential issues before they escalate.
Steps to Streamline Inventory Management with Data Analysis
To effectively utilize data analysis tools for inventory management, manufacturers should follow a structured approach.
Data Collection
The first step involves collecting relevant data from various sources, such as sales records, supply chain information, and production data.
It’s essential to ensure that the data is accurate and up-to-date, as outdated or incorrect data can lead to flawed insights.
Data Integration
Once data is collected, it needs to be integrated into a centralized system for analysis.
This process may involve merging data from different sources, ensuring consistency and eliminating duplicates.
Integration allows for a comprehensive view of inventory, making it easier to analyze and interpret.
Data Analysis
With integrated data, manufacturers can perform data analysis to extract meaningful insights.
Utilizing data analysis tools, they can generate reports, visualizations, and forecasts to guide inventory management decisions.
This stage allows for the identification of trends, inefficiencies, and areas for improvement.
Implementation of Insights
The final step is to apply the insights gained from data analysis to improve inventory management practices.
This includes adjusting inventory levels, refining ordering processes, and enhancing supplier relationships.
Continuous monitoring ensures that the implemented changes are effective and sustainable.
Challenges and Considerations
While data analysis tools offer significant advantages, there are challenges that manufacturers must navigate.
Ensuring data accuracy is crucial, as errors can lead to misguided decisions.
Moreover, integrating new tools with existing systems may require technical expertise and time.
It’s also important to train employees on how to use these tools effectively.
Without proper training, the full potential of data analysis tools cannot be realized.
Continuous education and updates on new features and best practices are recommended.
Conclusion
Incorporating data analysis tools into inventory management provides the manufacturing industry with powerful capabilities to optimize operations and reduce costs.
By understanding and leveraging the insights these tools offer, manufacturers can significantly enhance their inventory management processes.
Through improved demand forecasting, enhanced supply chain efficiency, and data-driven decision-making, businesses stand to gain a competitive advantage in the ever-evolving market landscape.
資料ダウンロード
QCD調達購買管理クラウド「newji」は、調達購買部門で必要なQCD管理全てを備えた、現場特化型兼クラウド型の今世紀最高の購買管理システムとなります。
ユーザー登録
調達購買業務の効率化だけでなく、システムを導入することで、コスト削減や製品・資材のステータス可視化のほか、属人化していた購買情報の共有化による内部不正防止や統制にも役立ちます。
NEWJI DX
製造業に特化したデジタルトランスフォーメーション(DX)の実現を目指す請負開発型のコンサルティングサービスです。AI、iPaaS、および先端の技術を駆使して、製造プロセスの効率化、業務効率化、チームワーク強化、コスト削減、品質向上を実現します。このサービスは、製造業の課題を深く理解し、それに対する最適なデジタルソリューションを提供することで、企業が持続的な成長とイノベーションを達成できるようサポートします。
オンライン講座
製造業、主に購買・調達部門にお勤めの方々に向けた情報を配信しております。
新任の方やベテランの方、管理職を対象とした幅広いコンテンツをご用意しております。
お問い合わせ
コストダウンが利益に直結する術だと理解していても、なかなか前に進めることができない状況。そんな時は、newjiのコストダウン自動化機能で大きく利益貢献しよう!
(Β版非公開)