- お役立ち記事
- How to Use Defect Analysis to Drive Supplier Improvement
How to Use Defect Analysis to Drive Supplier Improvement
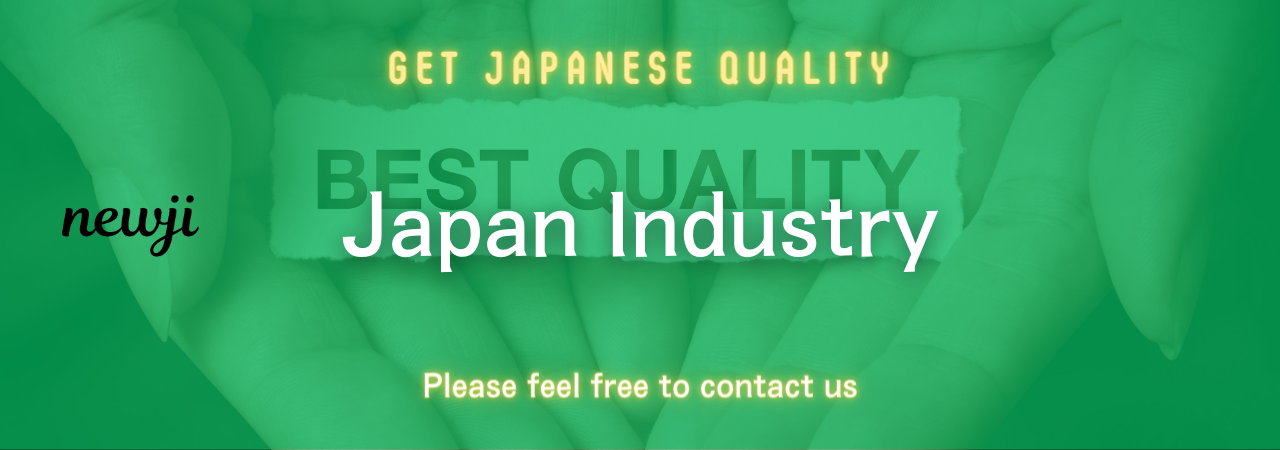
目次
Understanding Defect Analysis
Defect analysis is a vital process used to understand the root causes of product and service issues.
It’s a systematic examination of defects found in incoming materials or supplies that helps identify trends, patterns, and technical discrepancies.
This information drives improvement efforts and optimizes supplier performance.
By consistently analyzing defects, companies can reduce waste, improve quality, and foster stronger relationships with suppliers.
The ultimate goal is not just to fix problems but to prevent them from occurring in the first place, enhancing the overall supply chain efficiency.
The Importance of Supplier Improvement
Supplier improvement is an essential aspect of a successful business operation.
When suppliers provide high-quality materials, the end products are more likely to satisfy customer needs.
Improvements in supplier performance lead to cost savings, reduced waste, improved production times, and enhanced product reliability.
Additionally, well-performing suppliers tend to be more responsive and flexible in meeting the changing demands of the business, which can be a significant competitive advantage.
The Defect Analysis Process
Step 1: Data Collection
The initial step in defect analysis involves collecting data from various points in the supply chain.
This includes incoming inspections, production line checks, customer feedback, and returned goods analysis.
Accurate data collection is crucial for identifying defect trends and forming a basis for analysis.
Step 2: Identify Defect Types and Frequency
Once data is collected, the next step is to categorize the defects and quantify them by frequency.
This helps in understanding which defects are the most common and might require immediate attention.
Categories could include material defects, design flaws, or process failures.
Step 3: Root Cause Analysis
After categorizing, a root cause analysis (RCA) is conducted to find why defects are occurring.
Common methodologies used in RCA are the 5 Whys and Fishbone Diagrams.
These tools help trace the origin of a defect, delineating between superficial symptoms and underlying problems.
Utilizing the 5 Whys and Fishbone Diagram
The 5 Whys technique involves asking “why” multiple times until the fundamental cause is identified.
It’s effective in peeling away layers of symptoms to get to the root of a problem.
On the other hand, the Fishbone Diagram, also known as an Ishikawa or cause-and-effect diagram, is used to visualize potential causes of a defect, helping teams brainstorm issues across various categories like materials, methods, equipment, and personnel.
Developing Solutions and Action Plans
Step 1: Prioritize Issues
Once root causes are identified, it’s vital to prioritize the issues based on their impact on production, cost implications, and frequency.
Addressing the most significant problems first can lead to substantial improvements in supplier performance.
Step 2: Develop Solutions
For each prioritized issue, develop targeted solutions or improvements.
This could involve changes in processes, refining specifications, updating material requirements, or reassessing supplier manuals.
Effective solutions should be practical, cost-effective, and sustainable.
Step 3: Implement Changes
Implementing changes might require collaboration with suppliers, involving training sessions, workshops, and detailed feedback on identified defects and their causes.
The supplier needs to understand their role in the improvement process and be provided with the necessary tools and resources.
Step 4: Monitor and Review
After solutions are implemented, continuous monitoring is crucial.
Regular reviews ensure that changes are effective and sustained over time.
Data should be collected and analyzed consistently to spot any new trends or defects that need addressing.
Collaboration with Suppliers
Collaboration is key to successful defect analysis and supplier improvement.
Open communication and transparency strengthen the supplier-customer relationship.
Suppliers should be viewed as partners in the improvement process.
Involving them in identifying problems and creating solutions ensures both parties have aligned interests and goals.
Benefits of Effective Defect Analysis
Companies that invest in defect analysis enjoy numerous benefits.
These include improved product quality, reduced production costs, and enhanced customer satisfaction.
Preventive measures can significantly bring down the number of defects, leading to fewer returns and complaints.
Moreover, effective defect analysis contributes to developing a more robust and reliable supply chain.
Conclusion
Defect analysis is more than just an examination of faults in products and services.
It’s a powerful method to drive supplier improvement and elevate supply chain performance.
By understanding and addressing the root causes of defects, organizations can develop long-lasting solutions, leading to cost savings, increased efficiency, and better supplier partnerships.
Prioritizing defect analysis and collaboration with suppliers is a strategic move towards excellence in quality assurance and customer satisfaction.
資料ダウンロード
QCD調達購買管理クラウド「newji」は、調達購買部門で必要なQCD管理全てを備えた、現場特化型兼クラウド型の今世紀最高の購買管理システムとなります。
ユーザー登録
調達購買業務の効率化だけでなく、システムを導入することで、コスト削減や製品・資材のステータス可視化のほか、属人化していた購買情報の共有化による内部不正防止や統制にも役立ちます。
NEWJI DX
製造業に特化したデジタルトランスフォーメーション(DX)の実現を目指す請負開発型のコンサルティングサービスです。AI、iPaaS、および先端の技術を駆使して、製造プロセスの効率化、業務効率化、チームワーク強化、コスト削減、品質向上を実現します。このサービスは、製造業の課題を深く理解し、それに対する最適なデジタルソリューションを提供することで、企業が持続的な成長とイノベーションを達成できるようサポートします。
オンライン講座
製造業、主に購買・調達部門にお勤めの方々に向けた情報を配信しております。
新任の方やベテランの方、管理職を対象とした幅広いコンテンツをご用意しております。
お問い合わせ
コストダウンが利益に直結する術だと理解していても、なかなか前に進めることができない状況。そんな時は、newjiのコストダウン自動化機能で大きく利益貢献しよう!
(Β版非公開)