- お役立ち記事
- How to use digital twins in the manufacturing industry to optimize maintenance plans
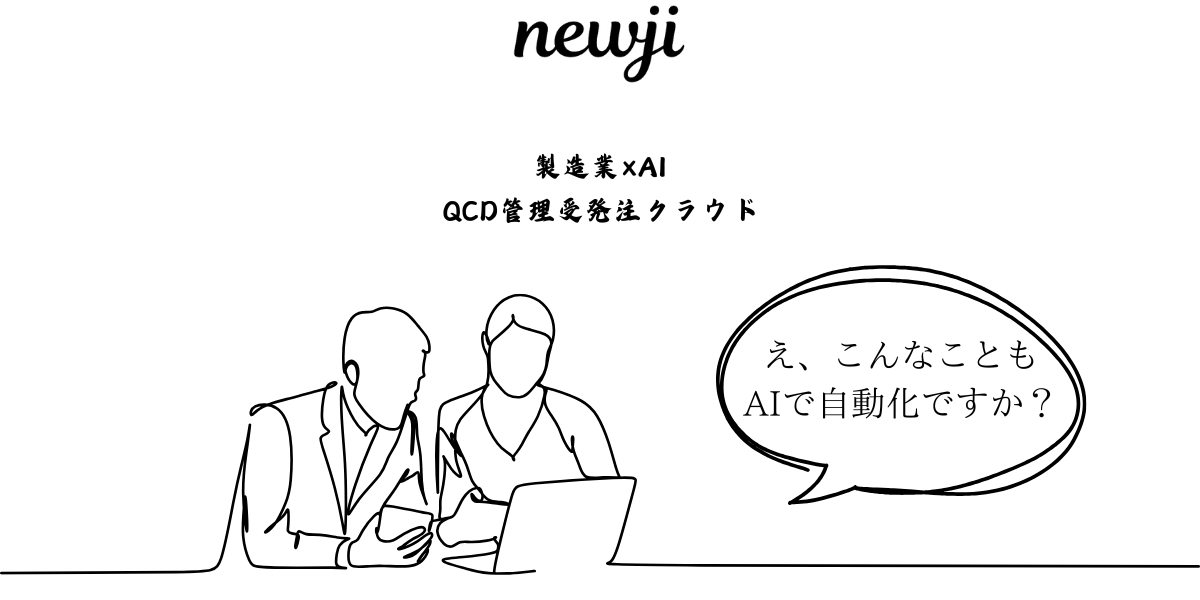
How to use digital twins in the manufacturing industry to optimize maintenance plans
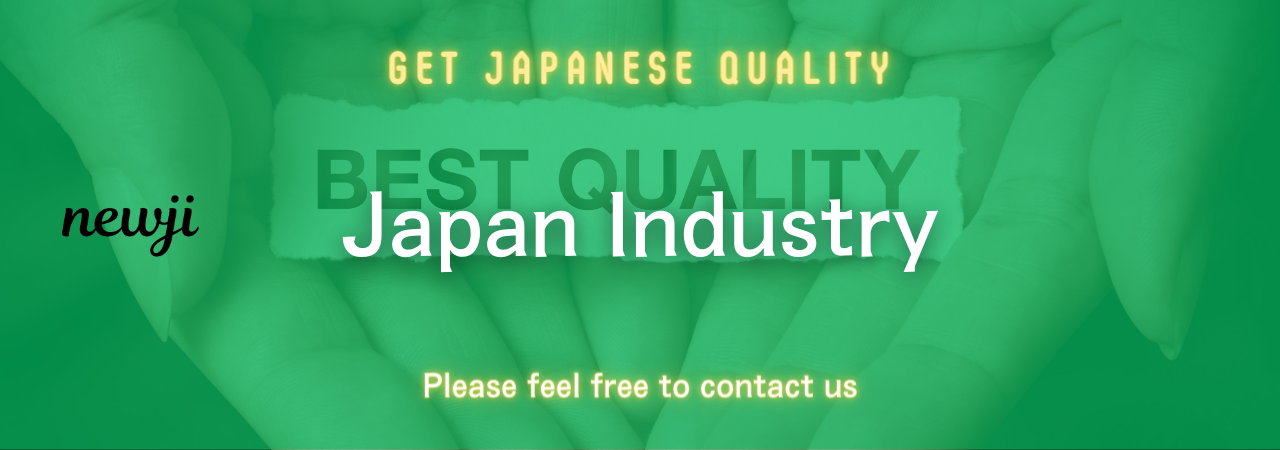
Digital twins have emerged as a transformative force in the manufacturing industry, offering new ways to optimize maintenance plans and improve overall efficiency.
If you’re curious about how digital twins work and how they can benefit your manufacturing processes, you’re in the right place.
Let’s dive into the world of digital twins and their application in manufacturing.
目次
What are Digital Twins?
Digital twins are virtual replicas of physical assets, processes, or systems that are used to simulate, predict, and optimize real-world outcomes.
These digital representations are created using data collected from sensors and other sources connected to the physical counterpart.
This data allows manufacturers to monitor operations in real-time and anticipate potential issues before they occur.
By providing insights into the functioning of machinery and systems, digital twins enable manufacturers to make data-driven decisions.
This helps in minimizing downtime, reducing maintenance costs, and increasing productivity.
The Role of Digital Twins in Manufacturing
Manufacturing is a complex industry that involves numerous processes, machines, and systems working together simultaneously.
It is crucial to maintain seamless operations to ensure high productivity and quality.
Digital twins play a significant role in achieving these objectives by providing real-time insights and predictive analytics.
Enhancing Predictive Maintenance
One of the primary applications of digital twins in manufacturing is predictive maintenance.
Predictive maintenance uses real-time data to predict when a machine or system is likely to fail, allowing manufacturers to schedule maintenance before a breakdown occurs.
With digital twins, manufacturers can create accurate models of their equipment to simulate and test different scenarios.
By analyzing data from these models, they can identify patterns and trends that indicate potential failures.
This proactive approach reduces unexpected downtimes and extends the lifespan of equipment.
As a result, manufacturers can save on maintenance costs and improve their overall operational efficiency.
Optimizing Maintenance Schedules
In traditional maintenance practices, equipment is often serviced based on fixed intervals, regardless of its actual condition.
This can lead to unnecessary downtime and increased operational costs.
Digital twins offer a more intelligent approach by helping manufacturers optimize maintenance schedules.
By continuously monitoring equipment and using data analytics, digital twins can determine the optimal time for maintenance tasks.
This ensures that machines are serviced only when necessary, improving resource allocation and minimizing disruptions to production schedules.
Improving Overall Equipment Effectiveness (OEE)
Overall Equipment Effectiveness (OEE) is a critical measure of a manufacturing system’s productivity.
It considers factors such as availability, performance, and quality to provide an accurate assessment of operational efficiency.
Digital twins contribute to improved OEE by providing valuable insights into machine performance and identifying areas that require improvement.
With accurate data and real-time monitoring, manufacturers can quickly address issues that affect productivity.
This continuous feedback loop allows for ongoing optimization, resulting in increased OEE and better utilization of resources.
Implementing Digital Twins in Manufacturing
Integrating digital twins into manufacturing processes requires a strategic approach.
Here are some key steps to consider for successful implementation:
Define Objectives and Use Cases
Before implementing digital twins, manufacturers must clearly define their objectives and identify specific use cases.
Determining the goals, such as reducing downtime or improving quality, helps in prioritizing efforts and resources.
Understanding the potential benefits of digital twins in particular areas of the manufacturing process ensures a focused approach.
Leverage Data and Analytics
Accurate data is the backbone of digital twins.
Manufacturers must ensure they collect data from reliable sources such as sensors, connected devices, and information systems.
Advanced analytics tools are also essential for processing and interpreting this data.
By leveraging data and analytics, manufacturers can gain actionable insights that guide decision-making.
Collaborate Across Teams
Implementing digital twins often requires collaboration between different teams, including IT, engineering, and operations.
It is crucial to foster effective communication and cooperation among stakeholders to ensure successful implementation.
By working together, teams can share insights and knowledge, streamlining the integration process and maximizing the benefits of digital twins.
Continuously Monitor and Improve
Digital twins are dynamic and require ongoing monitoring and improvements to remain effective.
Manufacturers should continuously evaluate the performance of their digital twins and make necessary adjustments.
By embracing a culture of continuous improvement, companies can stay ahead of the curve and fully leverage the power of digital twins for maintenance optimization.
Conclusion
Digital twins are revolutionizing the manufacturing industry by enhancing predictive maintenance, optimizing maintenance schedules, and improving overall equipment effectiveness.
Through strategic implementation and continuous improvement, manufacturers can harness the potential of digital twins to achieve operational excellence.
By providing real-time insights and data-driven decision-making capabilities, digital twins enable manufacturers to increase efficiency, reduce costs, and maintain a competitive edge.
As technology advances, the role of digital twins in manufacturing will continue to grow, offering new opportunities for innovation and success.
資料ダウンロード
QCD調達購買管理クラウド「newji」は、調達購買部門で必要なQCD管理全てを備えた、現場特化型兼クラウド型の今世紀最高の購買管理システムとなります。
ユーザー登録
調達購買業務の効率化だけでなく、システムを導入することで、コスト削減や製品・資材のステータス可視化のほか、属人化していた購買情報の共有化による内部不正防止や統制にも役立ちます。
NEWJI DX
製造業に特化したデジタルトランスフォーメーション(DX)の実現を目指す請負開発型のコンサルティングサービスです。AI、iPaaS、および先端の技術を駆使して、製造プロセスの効率化、業務効率化、チームワーク強化、コスト削減、品質向上を実現します。このサービスは、製造業の課題を深く理解し、それに対する最適なデジタルソリューションを提供することで、企業が持続的な成長とイノベーションを達成できるようサポートします。
オンライン講座
製造業、主に購買・調達部門にお勤めの方々に向けた情報を配信しております。
新任の方やベテランの方、管理職を対象とした幅広いコンテンツをご用意しております。
お問い合わせ
コストダウンが利益に直結する術だと理解していても、なかなか前に進めることができない状況。そんな時は、newjiのコストダウン自動化機能で大きく利益貢献しよう!
(Β版非公開)