- お役立ち記事
- How to use experimental design to optimize tire manufacturing processes
月間76,176名の
製造業ご担当者様が閲覧しています*
*2025年3月31日現在のGoogle Analyticsのデータより
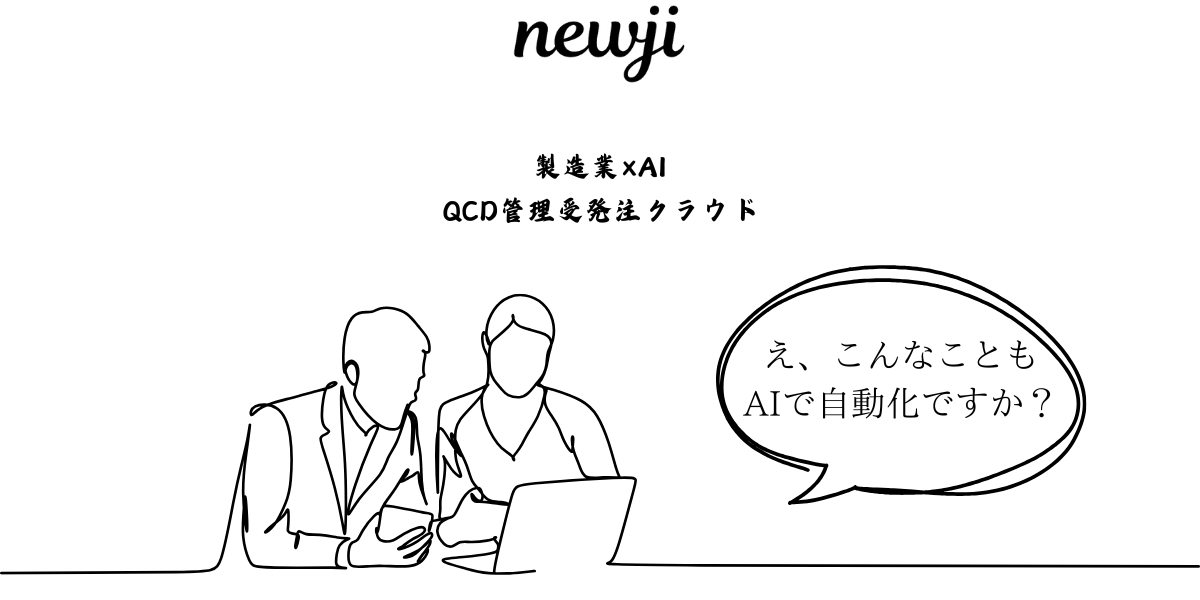
How to use experimental design to optimize tire manufacturing processes
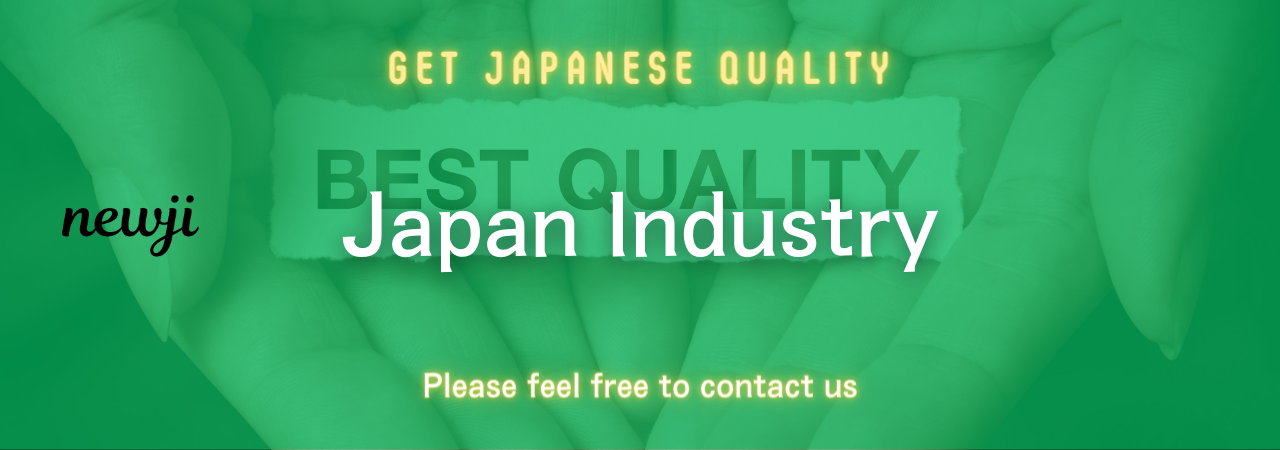
目次
Understanding Experimental Design
Before diving into the application of experimental design in tire manufacturing, it is essential to understand what experimental design entails.
Experimental design is a systematic approach to conducting experiments that aims to identify the effects of various factors on a particular outcome.
By organizing experiments effectively, manufacturers can isolate variables and determine the optimal conditions for their processes.
In tire manufacturing, this means improving quality, reducing production costs, and enhancing performance.
The Importance of Experimental Design in Tire Manufacturing
Tire manufacturing is a complex process involving multiple materials and steps.
Various factors, such as temperature, pressure, and mixing time, can influence tire durability, fuel efficiency, and safety.
Applying experimental design helps manufacturers identify the optimal combination of these factors to produce the best possible tire.
This not only ensures a superior product but can also streamline production processes.
By experimenting with different parameters, manufacturers can reduce material waste, minimize energy consumption, and shorten production cycles.
Steps to Implement Experimental Design
To optimize tire manufacturing processes using experimental design, follow these structured steps:
1. Define the Objectives
The first step is to clearly define the objectives of the experiment.
What aspects of the tire manufacturing process need optimization?
Is the focus on improving tread durability, rolling resistance, or reducing production time?
Defining precise objectives ensures that the experimental design is tailored to meet these goals.
2. Identify Key Factors and Levels
Once objectives are set, identify the key factors influencing the manufacturing process.
These could include raw material composition, curing time, and temperature settings.
For each factor, determine the levels or variations that will be tested.
For example, if temperature is a factor, the levels might include low, medium, and high settings.
3. Choose an Experimental Design Method
Several experimental design methods can be applied, such as factorial designs, response surface methodology, or Taguchi methods.
Each has its advantages and is suited for different types of experiments.
Factorial designs allow for the examination of interactions between multiple factors, while Taguchi methods help with robust designs that can handle variability.
Selecting the appropriate method depends on the complexity and nature of the manufacturing process.
4. Conduct the Experiment
With the experimental setup in place, proceed by conducting the experiment according to the chosen design method.
Ensure that all variables are controlled precisely and that data is recorded meticulously.
Consistency is critical in obtaining reliable results.
5. Analyze the Results
Once the data is collected, analyze it using statistical software or methods to identify patterns and relationships.
ANOVA (Analysis of Variance) is commonly used to determine if there are statistically significant differences between the factor levels.
Such analysis helps pinpoint which factors and settings yield the best results.
6. Implement the Optimal Settings
Based on the analysis, implement the optimal factor settings in the tire manufacturing process.
This may involve adjusting temperatures, modifying material compositions, or altering curing times.
Such changes should reflect the best practices identified through the experiment.
7. Continuously Monitor and Improve
Even after implementing changes, continuous monitoring is crucial.
This ensures that any variation in materials or external conditions is swiftly addressed.
Continuous improvement should be an ongoing goal, with new experiments being conducted regularly as technology and materials evolve.
Challenges and Considerations in Tire Manufacturing
While experimental design is powerful, there are challenges in its application to tire manufacturing.
One major challenge is the cost associated with conducting experiments, especially if they require significant alterations to the production process.
Time constraints can also limit the extent and number of experiments conducted.
Manufacturers must balance between thorough experimentation and maintaining production schedules.
Moreover, the quality of input data can heavily influence the outcomes of the experiments.
Ensuring accurate and consistent data is a must to achieve reliable results.
Conclusion
Experimental design offers a methodical way to optimize tire manufacturing processes, enhancing product quality while reducing costs.
By defining objectives, identifying key factors, and analyzing results, manufacturers can significantly improve their processes.
Even though there are challenges, the benefits far outweigh the costs, providing a clear pathway to innovation and efficiency in tire production.
With continuous improvement and adaptation, tire manufacturers can remain competitive in a dynamic market.
資料ダウンロード
QCD管理受発注クラウド「newji」は、受発注部門で必要なQCD管理全てを備えた、現場特化型兼クラウド型の今世紀最高の受発注管理システムとなります。
ユーザー登録
受発注業務の効率化だけでなく、システムを導入することで、コスト削減や製品・資材のステータス可視化のほか、属人化していた受発注情報の共有化による内部不正防止や統制にも役立ちます。
NEWJI DX
製造業に特化したデジタルトランスフォーメーション(DX)の実現を目指す請負開発型のコンサルティングサービスです。AI、iPaaS、および先端の技術を駆使して、製造プロセスの効率化、業務効率化、チームワーク強化、コスト削減、品質向上を実現します。このサービスは、製造業の課題を深く理解し、それに対する最適なデジタルソリューションを提供することで、企業が持続的な成長とイノベーションを達成できるようサポートします。
製造業ニュース解説
製造業、主に購買・調達部門にお勤めの方々に向けた情報を配信しております。
新任の方やベテランの方、管理職を対象とした幅広いコンテンツをご用意しております。
お問い合わせ
コストダウンが利益に直結する術だと理解していても、なかなか前に進めることができない状況。そんな時は、newjiのコストダウン自動化機能で大きく利益貢献しよう!
(β版非公開)