- お役立ち記事
- How to use optimal ordering models to achieve inventory reduction goals for purchasing departments
月間76,176名の
製造業ご担当者様が閲覧しています*
*2025年3月31日現在のGoogle Analyticsのデータより
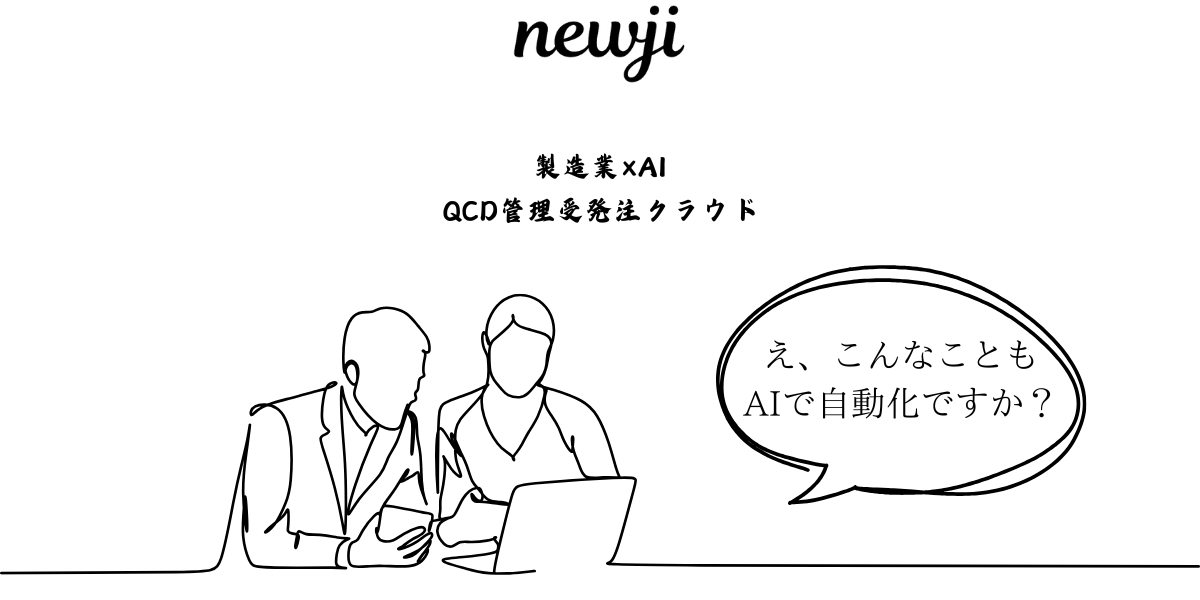
How to use optimal ordering models to achieve inventory reduction goals for purchasing departments
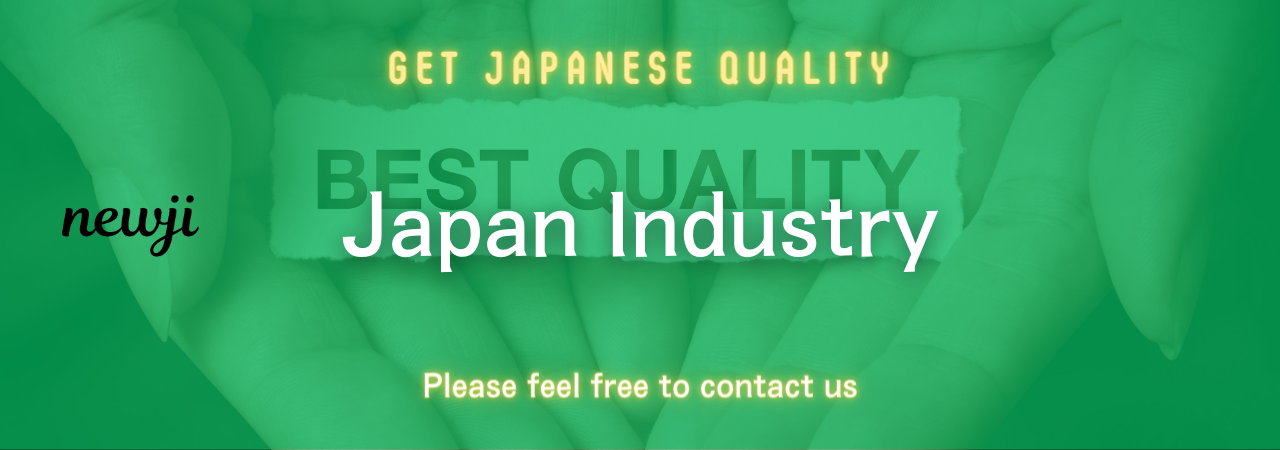
目次
Understanding Optimal Ordering Models
In today’s competitive business environment, managing inventory efficiently is crucial for success.
The purchasing department plays a pivotal role in maintaining the balance between supply and demand.
One of the significant goals of any purchasing department is inventory reduction, as excess inventory ties up capital and increases holding costs.
Optimal ordering models are mathematical and statistical tools designed to help businesses determine the most cost-effective way to manage and order inventory.
These models help in forecasting demand, minimizing costs, and achieving inventory reduction goals.
Let’s dive deeper into how these models work and how they can be implemented in purchasing departments.
Types of Optimal Ordering Models
There are several types of optimal ordering models, each suited to different business environments and inventory needs.
Understanding these models is the first step toward leveraging them for inventory reduction.
Economic Order Quantity (EOQ)
The Economic Order Quantity model is a fundamental tool for inventory management.
It calculates the optimal order quantity that minimizes the total inventory costs, which include holding costs, ordering costs, and stockout costs.
EOQ is particularly useful for companies with consistent demand patterns and steady sales.
Just-In-Time (JIT)
The Just-In-Time model focuses on reducing inefficiencies by ordering inventory only when there is an actual demand for it.
JIT minimizes the amount of stock held in inventory, which is beneficial in reducing storage costs and the risk of obsolescence.
This model requires a reliable supplier network and accurate demand forecasting.
ABC Analysis
ABC Analysis is a method for categorizing inventory into three groups (A, B, and C) based on their importance.
‘A’ items are the most valuable and require tight control and regular review, while ‘C’ items are the least critical.
This categorization helps manage resources effectively and focus efforts on inventory items that have the most impact on costs.
Reorder Point (ROP)
The Reorder Point model determines the specific point at which an order should be placed to replenish inventory before it reaches a critical low level.
ROP considers lead time and demand variability to ensure that there is always enough stock to meet customer demand without overstocking.
Implementing Optimal Ordering Models
To achieve inventory reduction goals using optimal ordering models, purchasing departments need a strategic approach.
Here’s how to implement these models effectively:
Analyze Historical Data
Start by analyzing historical sales and inventory data.
Understand patterns and trends that may affect demand forecasting.
This data is crucial for setting accurate baseline figures in models like EOQ and ROP.
Predict Future Demand
Use statistical forecasting techniques to predict future demand accurately.
Incorporate external factors such as market trends, seasonality, and economic indicators that could influence demand.
Accurate demand forecasting is vital for models like JIT and ROP to function effectively.
Collaborate with Suppliers
Establish strong relationships with reliable suppliers to improve lead times and inventory turnover.
For JIT models, supplier collaboration ensures that products are delivered promptly and with minimal delays.
Monitor Inventory Levels
Implement inventory tracking systems to monitor stock levels in real-time.
This real-time data helps in making informed decisions about when to reorder inventory, aligning perfectly with models like ROP.
Continuous Improvement
Regularly review and refine ordering processes and inventory policies.
Leverage data analytics to identify areas for improvement and make necessary adjustments to optimal ordering models.
Overcoming Challenges
While optimal ordering models can significantly streamline inventory management, they present certain challenges.
Data Accuracy
Inaccurate data can lead to flawed forecasts and suboptimal ordering decisions.
Ensure data integrity through regular audits and updates of information systems.
Complexity of Implementation
Implementing these models requires a comprehensive understanding of inventory dynamics and technology.
Invest in training staff and integrating advanced inventory management tools.
Changing Market Conditions
Rapid market changes can render forecasts obsolete.
Stay agile and be prepared to adapt models to shifting market conditions.
Benefits of Optimal Ordering Models
Utilizing optimal ordering models offers several benefits for purchasing departments aiming to reduce inventory levels:
Cost Efficiency
Reduce total inventory costs by optimizing order quantities and minimizing holding and ordering expenses.
Increased Cash Flow
Reduce excess inventory to free up capital, allowing for investment in other business areas.
Customer Satisfaction
Ensure product availability and timely delivery by maintaining optimal stock levels, thereby improving customer satisfaction and loyalty.
Reduction in Waste
Minimize overproduction and decrease waste by aligning orders closely with actual demand.
Conclusion
Optimal ordering models are essential tools for any purchasing department focused on inventory reduction.
By understanding and implementing these models, businesses can achieve efficient inventory management, cost savings, and improved operational performance.
The strategic use of these models not only reduces excess inventory but also enhances overall business competitiveness in a dynamic market landscape.
資料ダウンロード
QCD管理受発注クラウド「newji」は、受発注部門で必要なQCD管理全てを備えた、現場特化型兼クラウド型の今世紀最高の受発注管理システムとなります。
ユーザー登録
受発注業務の効率化だけでなく、システムを導入することで、コスト削減や製品・資材のステータス可視化のほか、属人化していた受発注情報の共有化による内部不正防止や統制にも役立ちます。
NEWJI DX
製造業に特化したデジタルトランスフォーメーション(DX)の実現を目指す請負開発型のコンサルティングサービスです。AI、iPaaS、および先端の技術を駆使して、製造プロセスの効率化、業務効率化、チームワーク強化、コスト削減、品質向上を実現します。このサービスは、製造業の課題を深く理解し、それに対する最適なデジタルソリューションを提供することで、企業が持続的な成長とイノベーションを達成できるようサポートします。
製造業ニュース解説
製造業、主に購買・調達部門にお勤めの方々に向けた情報を配信しております。
新任の方やベテランの方、管理職を対象とした幅広いコンテンツをご用意しております。
お問い合わせ
コストダウンが利益に直結する術だと理解していても、なかなか前に進めることができない状況。そんな時は、newjiのコストダウン自動化機能で大きく利益貢献しよう!
(β版非公開)