- お役立ち記事
- How to utilize international standard mechanical drawing geometric tolerances and maximum physical intersection
月間76,176名の
製造業ご担当者様が閲覧しています*
*2025年3月31日現在のGoogle Analyticsのデータより
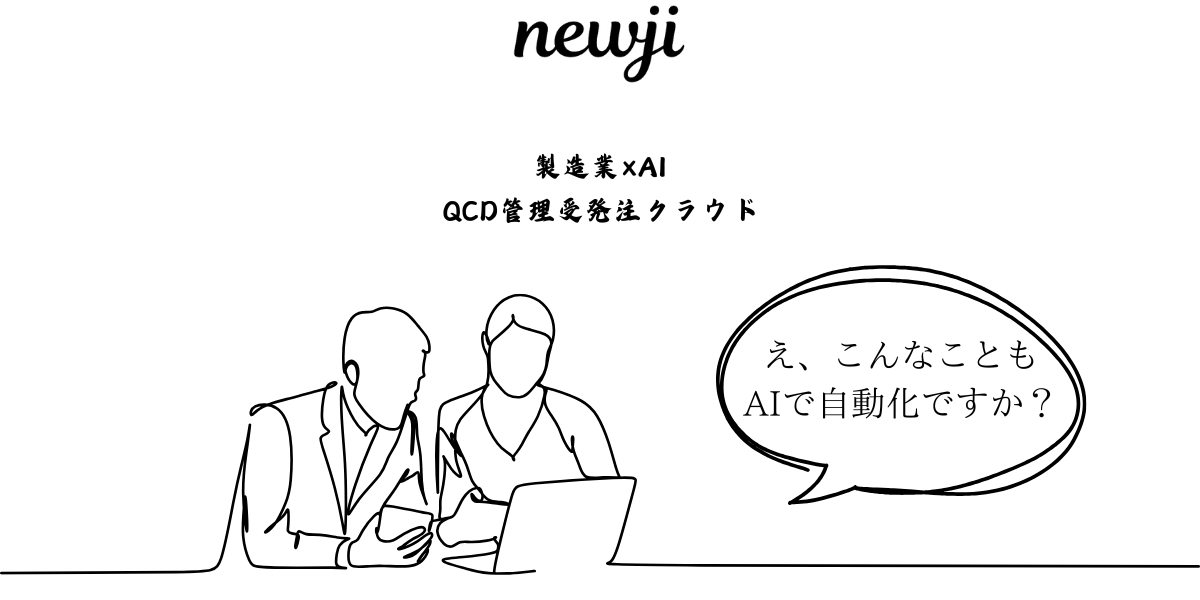
How to utilize international standard mechanical drawing geometric tolerances and maximum physical intersection
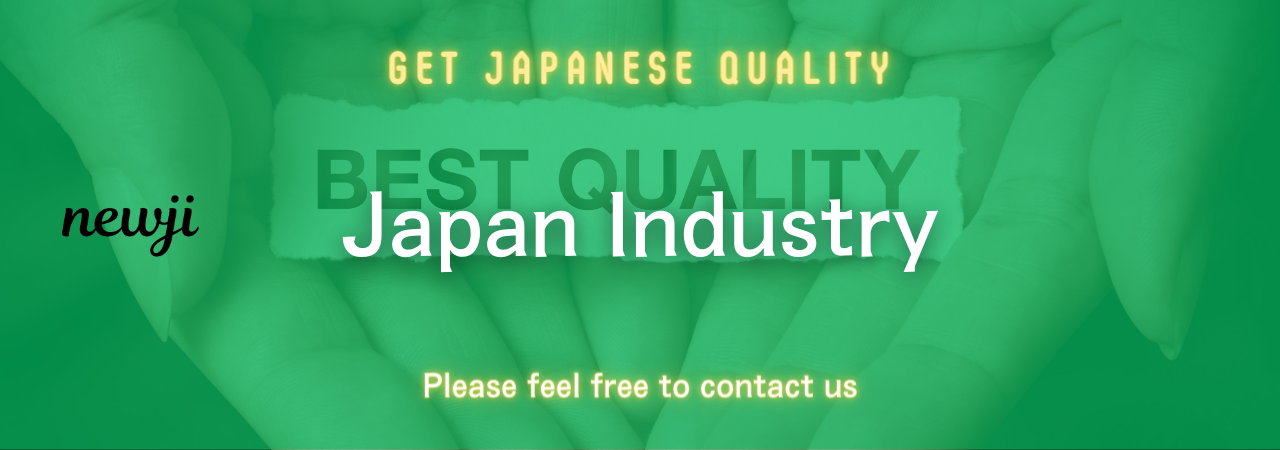
目次
Understanding Geometric Tolerances in Mechanical Drawings
In the world of mechanical engineering and design, precision and accuracy are crucial.
Geometric tolerances are a way to ensure that parts will fit and function as intended, even when there are small variances in manufacturing.
These tolerances help define the allowable deviation in the geometry of a part.
Geometric Dimensioning and Tolerancing (GD&T) is a system used to communicate these tolerances clearly and efficiently.
It’s standardized internationally, so engineers and manufacturers around the world can understand and use it.
The Basics of Geometric Tolerances
Geometric tolerances are used to define the permissible limits of variation for individual parts.
They specify the shape, orientation, location, and runout of features on a part.
This ensures that, even with some level of imperfection in manufacturing, the parts will still assemble correctly and function as planned.
There are several types of geometric tolerances, each conveying different information:
1. **Form Tolerances** – Control the shape of a feature, such as flatness or circularity.
2. **Orientation Tolerances** – Ensure features are aligned correctly, like perpendicularity or parallelism.
3. **Location Tolerances** – Dictate where features should be located within a certain range, including position and concentricity.
4. **Runout Tolerances** – Control how much a feature can wobble in relation to another feature, involving total runout and circular runout.
Understanding how to apply these tolerances effectively can improve both the quality and the manufacturability of a product.
Importance of Maximum Material Condition (MMC)
In tangent with geometric tolerances, Maximum Material Condition (MMC) is a critical concept.
It refers to the condition of a part when it contains the largest amount of material within the specified limits.
For example, when a hole is smallest in diameter or a shaft is largest in diameter, that is their MMC.
MMC is vital because it allows designers to optimize assemblies for tightest fits and accounts for the greatest potential interference or tolerance stack-up.
Why Use MMC?
The use of MMC is beneficial for various reasons:
– **Interchangeability**: MMC helps in ensuring that parts fit together even when manufactured by different suppliers.
This means a part can easily be swapped out without affecting the function of the assembled product.
– **Tight Control Over Assembly Dimensions**: By using MMC, engineers can maintain strict control over the size and position of a part.
This ensures precise alignment and fit in the assembly process.
– **Cost Efficiency**: With MMC, manufacturing processes can tolerate slight variations, reducing waste and lowering production costs.
For these reasons, MMC is an integral part of mechanical design and manufacturing.
Applying Geometric Tolerances and MMC in Designs
To make the most of geometric tolerances and MMC, it’s essential to apply them correctly in your mechanical drawings.
Here are some steps to guide you through this process:
1. Determine Key Features
Identify which features in your design are critical to the function and assembly of the part.
These could be holes, surfaces, or axes that need precise control for the part to effectively fit and function.
2. Apply Appropriate Tolerances
Select the correct types of geometric tolerances for each key feature.
Consider how each feature interacts with others in the assembly.
Assign tighter tolerances to essential features and more relaxed tolerances where precision is less critical.
3. Use MMC for Critical Features
Apply MMC to features that are significant in maintaining the integrity of the assembly.
This is particularly important when you need precise control over mating parts.
Using MMC ensures that even at extremes of allowable variation, the parts will still fit together as intended.
4. Communicate Clearly on Drawings
Ensure that all the geometric tolerances and MMC symbols are clearly shown on the drawings.
Standard symbols and notation should be used to facilitate universal understanding.
5. Verify Compatibility
Finally, use software tools or conduct manual checks to confirm that the geometric tolerances are compatible with manufacturing capabilities.
Always ensure that the assembly and functionality are maintained within the specified tolerances.
Benefits of Proper Implementation
Applying international standards for geometric tolerances and MMC can significantly improve the outcome of mechanical designs.
– **Improved Product Quality**: Geometric tolerances help in achieving high precision, enhancing the overall quality of the product.
– **Enhanced Performance**: Properly toleranced parts fit together seamlessly, leading to smooth operations and reduced wear and tear.
– **Reduced Production Costs**: By setting appropriate tolerances, you minimize rework and material waste, streamlining the production process.
– **Consistency Across Production Lines**: With standardized tolerances, it is easier to maintain consistency across different production runs and manufacturing locations.
Conclusion
Understanding and utilizing international standards for geometric tolerances and maximum material conditions are fundamental to the success of any mechanical design project.
By ensuring clear communication of tolerances and conditions, engineers can produce high-quality, reliable, and cost-effective products, suitable for global manufacturing and assembly.
Fostering these practices will lead to better performance, improved manufacturability, and more satisfied customers.
資料ダウンロード
QCD管理受発注クラウド「newji」は、受発注部門で必要なQCD管理全てを備えた、現場特化型兼クラウド型の今世紀最高の受発注管理システムとなります。
ユーザー登録
受発注業務の効率化だけでなく、システムを導入することで、コスト削減や製品・資材のステータス可視化のほか、属人化していた受発注情報の共有化による内部不正防止や統制にも役立ちます。
NEWJI DX
製造業に特化したデジタルトランスフォーメーション(DX)の実現を目指す請負開発型のコンサルティングサービスです。AI、iPaaS、および先端の技術を駆使して、製造プロセスの効率化、業務効率化、チームワーク強化、コスト削減、品質向上を実現します。このサービスは、製造業の課題を深く理解し、それに対する最適なデジタルソリューションを提供することで、企業が持続的な成長とイノベーションを達成できるようサポートします。
製造業ニュース解説
製造業、主に購買・調達部門にお勤めの方々に向けた情報を配信しております。
新任の方やベテランの方、管理職を対象とした幅広いコンテンツをご用意しております。
お問い合わせ
コストダウンが利益に直結する術だと理解していても、なかなか前に進めることができない状況。そんな時は、newjiのコストダウン自動化機能で大きく利益貢献しよう!
(β版非公開)