- お役立ち記事
- How to Utilize Statistical Quality Control (SQC) in Manufacturing Quality Assurance
How to Utilize Statistical Quality Control (SQC) in Manufacturing Quality Assurance
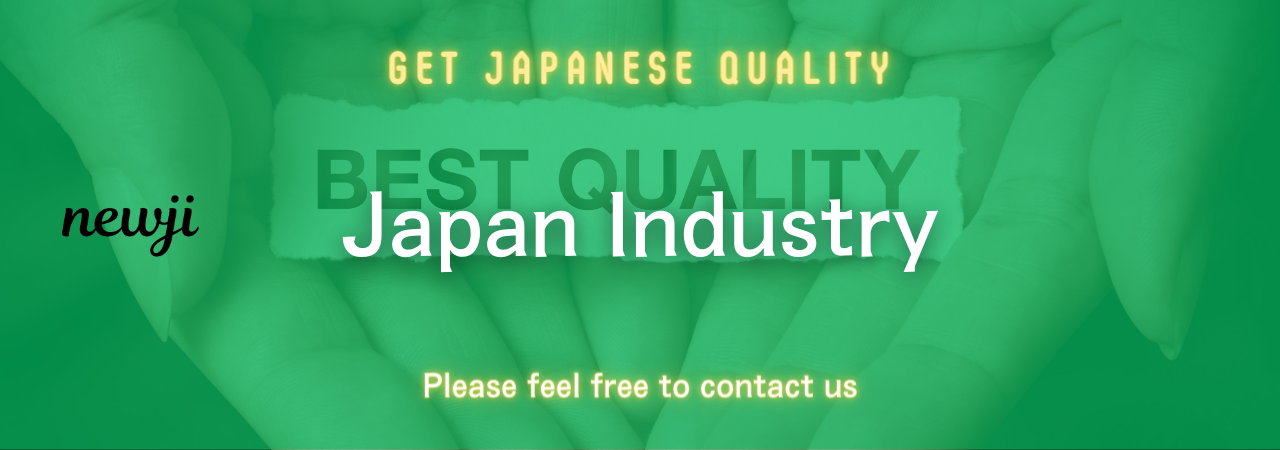
In the ever-evolving world of manufacturing, ensuring the highest level of product quality is essential.
Statistical Quality Control (SQC) provides a proactive approach to monitor and control the quality of products throughout the production process.
By understanding and implementing SQC, manufacturers can reduce defects, enhance productivity, and ultimately improve customer satisfaction.
This article will delve into the various aspects of SQC and how to effectively incorporate it into manufacturing quality assurance systems.
目次
Understanding Statistical Quality Control (SQC)
Statistical Quality Control is a set of statistical tools used in quality management for analyzing and improving processes.
These tools help identify variations in production processes that could lead to defects.
By analyzing data collected through various stages of the production process, manufacturers can make informed decisions to maintain or improve quality.
Key Components of SQC
SQC encompasses a range of statistical techniques, each serving a specific purpose in quality control.
Here are three primary components:
Descriptive Statistics
Descriptive statistics provide a summary of data collected from the production process.
These summaries include measures like mean (average), median, mode, standard deviation, and range.
By understanding these values, manufacturers can get an overview of the process behavior.
Statistical Process Control (SPC)
SPC involves using control charts to monitor production processes.
Control charts help distinguish between normal variations and variations that signal problems.
By plotting data points on control charts, manufacturers can spot trends and patterns that indicate potential quality issues.
Acceptance Sampling
Acceptance sampling is used to determine whether a batch of products meets quality standards.
Rather than inspecting every item, a sample is selected and tested.
Based on the results, the entire batch is either accepted or rejected.
This method saves time and resources while ensuring quality.
Benefits of Implementing SQC in Manufacturing
Incorporating SQC into manufacturing brings multiple benefits that contribute to a company’s overall success.
Here are some significant advantages:
Reduction in Defects
By identifying variations and implementing corrective actions in real-time, SQC helps minimize defects.
Continuous monitoring using control charts ensures quality issues are addressed before they escalate.
Improved Efficiency
SQC tools streamline the quality assurance process, enabling quicker decision-making.
Manufacturers can identify bottlenecks and areas of improvement, leading to increased efficiency and reduced waste.
Cost Savings
Efficiency gains and defect reduction translate to cost savings.
Manufacturers spend less on rework, scrap, and warranty claims, ultimately improving profitability.
Enhanced Customer Satisfaction
Consistently delivering high-quality products enhances customer trust and satisfaction.
With fewer defects, customers receive reliable products, resulting in repeat business and positive word-of-mouth.
Steps to Implement SQC in Manufacturing
Effective implementation of SQC requires a systematic approach.
Follow these steps to integrate SQC into your manufacturing process:
1. Define Objectives
Clearly outline the objectives of implementing SQC.
Identify the specific quality issues you aim to address and establish measurable goals.
2. Collect Data
Gather data from various stages of the production process.
Ensure data accuracy and relevance, as accurate data forms the foundation for effective SQC.
3. Analyze Data
Use descriptive statistics to analyze the collected data.
Gain insights into process behavior and identify areas that require improvement.
4. Implement Control Charts
Create control charts based on the analyzed data.
These charts will help monitor the production process in real-time and detect variations.
5. Train Staff
Ensure that employees are trained in SQC techniques.
They should be able to use control charts and understand how to interpret the data.
6. Monitor and Adjust
Continuously monitor the production process using control charts.
Make adjustments as needed to address variations and maintain quality standards.
7. Review and Improve
Regularly review the effectiveness of the SQC implementation.
Identify successes and areas for further improvement.
SQC is a continuous process that requires ongoing refinement.
SQC Tools and Techniques
Several tools and techniques are integral to SQC.
Below are some of the most commonly used ones:
Pareto Analysis
Pareto analysis helps identify the most significant factors contributing to quality issues.
By focusing on the vital few causes, manufacturers can address the most impactful problems first.
Fishbone Diagram
Also known as the cause-and-effect diagram, the fishbone diagram aids in identifying root causes of quality issues.
It visually maps out potential causes categorized into main groups like materials, methods, machines, and manpower.
Histogram
A histogram is a graphical representation of data distribution.
It shows the frequency of different data points, helping identify patterns and variations in the process.
Scatter Diagram
The scatter diagram plots data points on a graph to identify relationships between variables.
This tool is particularly useful in understanding correlations and the impact of one variable on another.
Control Charts
Control charts visually display process variations over time.
They include upper and lower control limits to differentiate between common cause variation and special cause variation.
Check Sheets
Check sheets are simple, structured forms for collecting data.
They ensure data is consistently gathered, making it easier to analyze and interpret.
Challenges in Implementing SQC
Despite its benefits, implementing SQC can present challenges.
Understanding these challenges can help manufacturers effectively address them:
Resistance to Change
Employees may be resistant to adopting new processes.
Clear communication and training can help overcome this resistance.
Data Quality
Accurate data is critical for SQC success.
Ensuring data integrity and consistency can be challenging but is essential for reliable analysis.
Resource Constraints
Implementing SQC requires investment in training, tools, and technology.
Manufacturers must allocate sufficient resources to support the implementation.
Continuous Improvement
SQC is an ongoing process that requires regular monitoring and adjustment.
Manufacturers need to commit to continuous improvement to achieve lasting benefits.
In conclusion, Statistical Quality Control (SQC) is a powerful tool for enhancing manufacturing quality assurance.
By understanding its key components, benefits, and implementation steps, manufacturers can significantly improve product quality and customer satisfaction.
Despite the challenges, the rewards of integrating SQC into manufacturing far outweigh the efforts required, paving the way for a more efficient and reliable production process.
資料ダウンロード
QCD調達購買管理クラウド「newji」は、調達購買部門で必要なQCD管理全てを備えた、現場特化型兼クラウド型の今世紀最高の購買管理システムとなります。
ユーザー登録
調達購買業務の効率化だけでなく、システムを導入することで、コスト削減や製品・資材のステータス可視化のほか、属人化していた購買情報の共有化による内部不正防止や統制にも役立ちます。
NEWJI DX
製造業に特化したデジタルトランスフォーメーション(DX)の実現を目指す請負開発型のコンサルティングサービスです。AI、iPaaS、および先端の技術を駆使して、製造プロセスの効率化、業務効率化、チームワーク強化、コスト削減、品質向上を実現します。このサービスは、製造業の課題を深く理解し、それに対する最適なデジタルソリューションを提供することで、企業が持続的な成長とイノベーションを達成できるようサポートします。
オンライン講座
製造業、主に購買・調達部門にお勤めの方々に向けた情報を配信しております。
新任の方やベテランの方、管理職を対象とした幅広いコンテンツをご用意しております。
お問い合わせ
コストダウンが利益に直結する術だと理解していても、なかなか前に進めることができない状況。そんな時は、newjiのコストダウン自動化機能で大きく利益貢献しよう!
(Β版非公開)