- お役立ち記事
- How to utilize the basics of mechanical elements, failure modes, and strength calculation/analysis methods for strength design
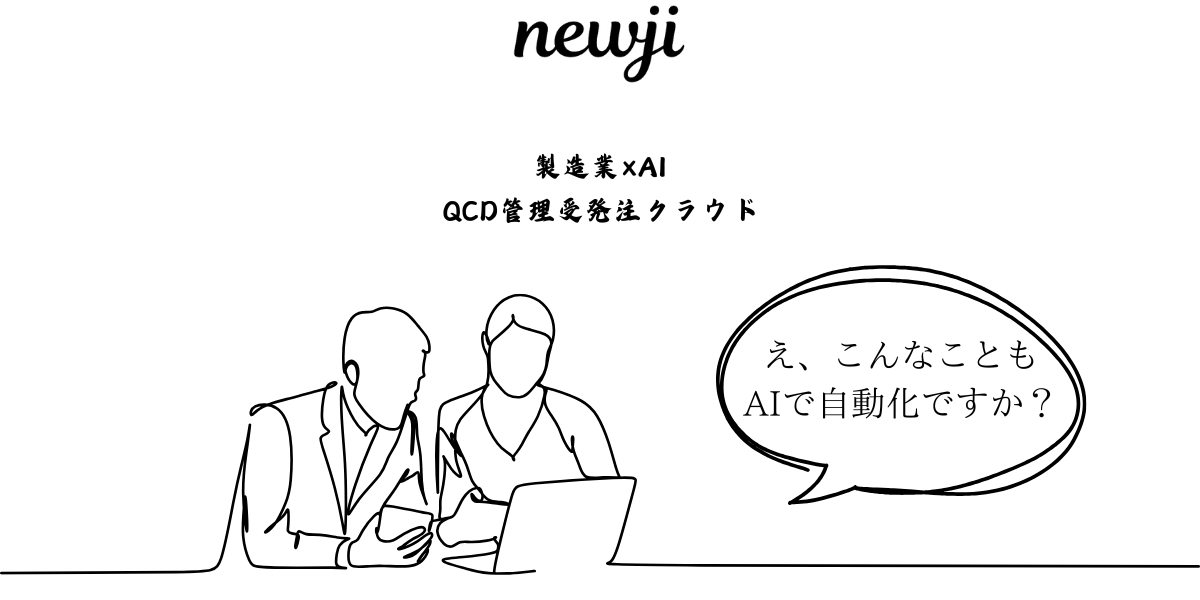
How to utilize the basics of mechanical elements, failure modes, and strength calculation/analysis methods for strength design
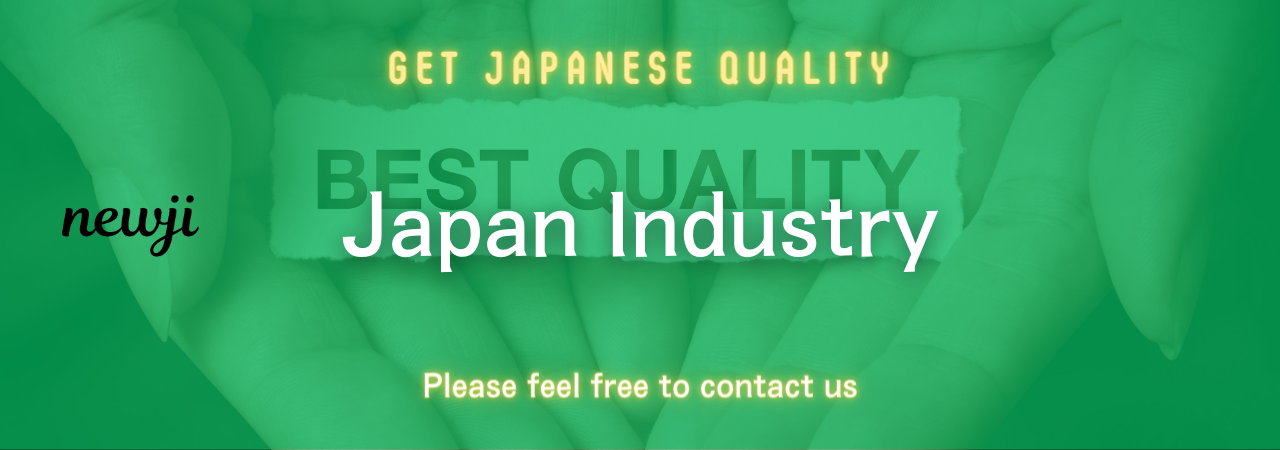
目次
Understanding Mechanical Elements
Mechanical elements are fundamental components used in various machines and structures.
Understanding these elements is vital for any aspiring engineer or designer as they play crucial roles in the functionality and reliability of systems.
Mechanical elements include gears, pulleys, springs, shafts, bearings, and fasteners.
Each of these has unique properties and applications.
By comprehending their functions, one can effectively incorporate them into designs to ensure optimal performance.
Mechanical elements often have specific roles, such as transmitting motion, supporting loads, or constraining movement within systems.
For instance, gears can change the direction of motion and alter speed and torque.
Springs can store energy and provide cushioning or load support.
Hence, understanding their basics allows for better integration and use in design.
Failure Modes in Mechanical Design
Careful consideration of failure modes is crucial in mechanical design.
Failure modes are the ways in which mechanical components might fail under certain conditions.
Understanding these can help in preventing potential issues during operation.
Common failure modes include fatigue, wear, corrosion, and fracture.
Fatigue occurs when a material is subjected to repeated cycles of stress and strain, leading to cracks and eventual failure.
Wear, on the other hand, happens due to friction and loss of material over time.
Understanding these failure modes can guide the choice of materials and design processes to mitigate risks.
To reduce the likelihood of failure, it is essential to test materials and components under various conditions.
Selecting appropriate materials with the right properties can also improve the longevity and performance of mechanical elements.
Strength Calculation and Analysis Methods
Strength calculation is a critical step in ensuring a mechanical design can withstand operational loads.
Calculating the strength involves determining how much stress a material can endure before it deforms or fractures.
Several methods are available for strength calculation.
These include static analysis, dynamic analysis, and fatigue analysis.
Static Analysis
Static analysis involves assessing the strength of materials under constant loads.
This method is used to evaluate structures and components under scenarios where the loads do not change significantly over time.
Static analysis helps in understanding the maximum stress a material can take without undergoing permanent deformation.
Dynamic Analysis
Dynamic analysis considers loads that vary with time.
This approach is essential for components subjected to changing forces and speeds, such as those in vehicles or machinery experiencing vibrations.
Dynamic analysis helps in predicting how a system will respond to different dynamic loads, ensuring it remains within safe operational limits.
Fatigue Analysis
Fatigue analysis is used to predict the lifespan of a component under repetitive stress cycles.
This analysis is crucial for parts like engine components or bridges, which experience loads repeatedly over their usage period.
By understanding fatigue, engineers can design parts that resist crack initiation and propagation, thus achieving safer designs.
Implementing Strength Design in Projects
Strength design integrates mechanical elements, failure modes, and calculation methods to create robust systems.
Designers and engineers use these principles to ensure safety, reliability, and cost-effectiveness in their projects.
The initial step in the strength design process involves understanding project requirements, such as load conditions and environmental factors.
Subsequent steps include selecting suitable materials and calculating how these materials will behave under anticipated loads.
Once calculations are complete and prototypes are developed, rigorous testing follows.
Testing is an essential part of strength design, offering a way to verify calculations and material performance.
Effective testing will uncover potential weaknesses before the product goes to market.
Moreover, computer-aided design (CAD) and finite element analysis (FEA) are powerful tools employed in strength design.
These technologies allow for modeling and simulating different conditions, which aids in refining designs and ensuring they meet specs without costly physical testing.
Balancing Cost and Safety
One of the challenges in mechanical design is balancing cost and safety.
Higher-quality materials and additional testing can lead to safer designs but also increase costs.
Therefore, finding an equilibrium is critical.
An effective way to balance cost and safety is through optimization.
This practice involves using algorithms and simulation tools to find the most efficient materials and production methods that do not compromise safety.
Additionally, ongoing monitoring and maintenance are important post-production.
These help in detecting any early signs of potential failure, extending the lifespan, and ensuring continued safety of products.
Conclusion
Understanding the basics of mechanical elements, failure modes, and strength calculation methods is imperative for robust design.
By integrating these elements into the design process, engineers and designers can produce systems that are not only effective but also reliable and safe.
Keeping abreast of advancements in technology and material science further enhances these designs, keeping them relevant in an ever-evolving landscape.
資料ダウンロード
QCD調達購買管理クラウド「newji」は、調達購買部門で必要なQCD管理全てを備えた、現場特化型兼クラウド型の今世紀最高の購買管理システムとなります。
ユーザー登録
調達購買業務の効率化だけでなく、システムを導入することで、コスト削減や製品・資材のステータス可視化のほか、属人化していた購買情報の共有化による内部不正防止や統制にも役立ちます。
NEWJI DX
製造業に特化したデジタルトランスフォーメーション(DX)の実現を目指す請負開発型のコンサルティングサービスです。AI、iPaaS、および先端の技術を駆使して、製造プロセスの効率化、業務効率化、チームワーク強化、コスト削減、品質向上を実現します。このサービスは、製造業の課題を深く理解し、それに対する最適なデジタルソリューションを提供することで、企業が持続的な成長とイノベーションを達成できるようサポートします。
オンライン講座
製造業、主に購買・調達部門にお勤めの方々に向けた情報を配信しております。
新任の方やベテランの方、管理職を対象とした幅広いコンテンツをご用意しております。
お問い合わせ
コストダウンが利益に直結する術だと理解していても、なかなか前に進めることができない状況。そんな時は、newjiのコストダウン自動化機能で大きく利益貢献しよう!
(Β版非公開)