- お役立ち記事
- How to visualize and build in design quality to eliminate recalls, customer complaints, and chronic manufacturing defects
月間76,176名の
製造業ご担当者様が閲覧しています*
*2025年3月31日現在のGoogle Analyticsのデータより
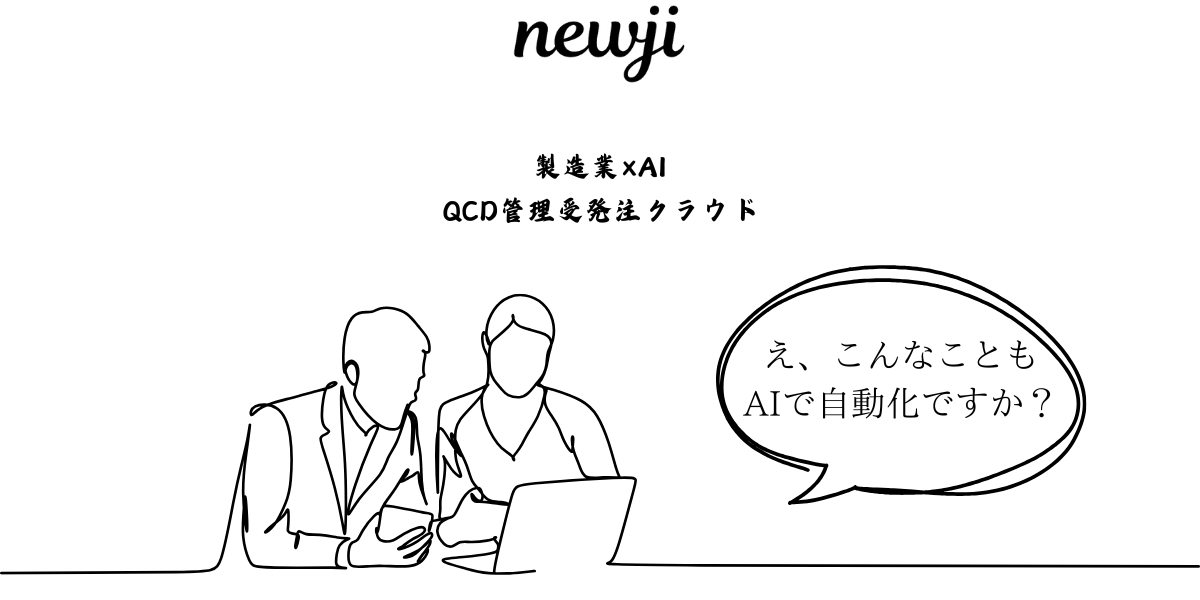
How to visualize and build in design quality to eliminate recalls, customer complaints, and chronic manufacturing defects
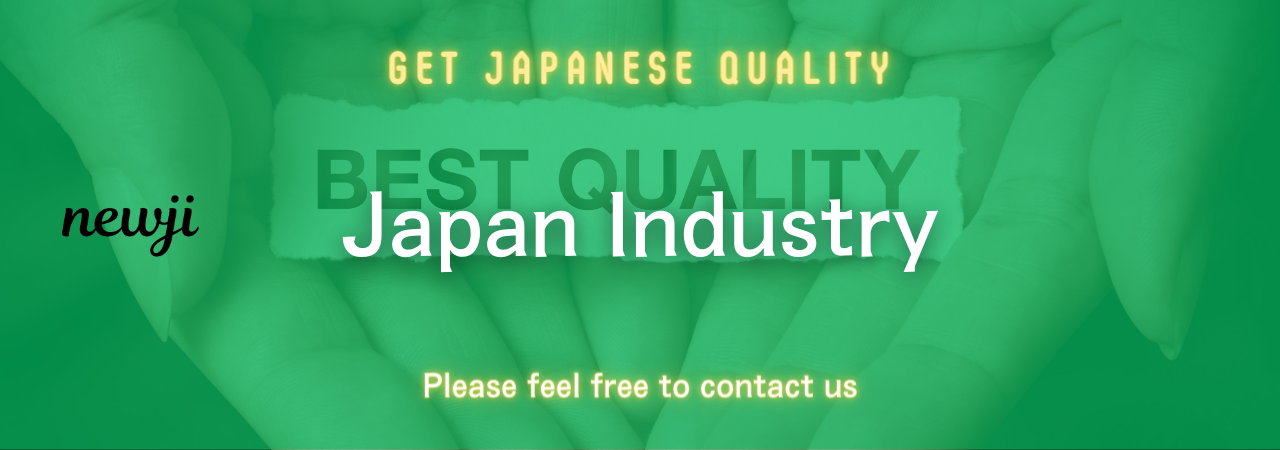
目次
Understanding Design Quality
Design quality is the foundation of any successful manufacturing process.
It involves creating a product that meets customer requirements and expectations while adhering to regulatory standards.
High design quality ensures that a product is not only functional but also reliable and safe.
By building design quality into your processes, you can prevent recalls, minimize customer complaints, and reduce chronic manufacturing defects.
The Importance of Design Quality in Manufacturing
Manufacturing products with poor design quality can lead to numerous complications.
These include safety hazards, increased costs due to returns or repairs, and damage to your brand’s reputation.
Recalls and customer complaints are often consequences of inadequate design quality.
Thus, prioritizing design quality can lead to numerous benefits, such as boosting customer satisfaction and reducing the likelihood of product recalls.
Visualizing Design Quality
One of the best ways to build design quality into your manufacturing process is to visualize it.
Visualization helps in identifying potential weaknesses in design early in the development phase.
Using Tools and Techniques for Visualization
1. Computer-Aided Design (CAD):
CAD software can be immensely helpful in visualizing a product’s design.
It allows designers to create detailed 3D models, helping to identify potential design flaws and facilitating better understanding among team members.
2. Prototyping:
Creating prototypes can help visualize the product’s functionality.
This enables manufacturers to test the product in real scenarios before mass production.
Prototypes provide a tangible way to assess a design’s quality, helping to spot and resolve issues early.
3. Design for Manufacturability (DFM):
DFM is a design approach that focuses on ease of manufacturing.
By using DFM principles, designers can visualize how their products will be manufactured, identifying potential issues that could lead to defects or recalls.
Strategies to Build Design Quality
Building design quality into your manufacturing process requires a strategic approach that involves all stakeholders.
Incorporating Design Reviews
Regular design reviews should be conducted throughout the development process.
These reviews should include team members from various departments such as engineering, quality assurance, and production.
Involving different perspectives helps identify potential issues that may not be apparent to designers alone.
Implementing Design Failure Mode and Effects Analysis (DFMEA)
DFMEA is a systematic method for evaluating a product design and identifying potential failure modes.
It assesses the potential impact of these failures and helps prioritize the implementation of preventive measures.
By using DFMEA, manufacturers can proactively manage design risks and prevent recalls or defects.
Ensuring Compliance with Industry Standards
Compliance with industry standards is crucial for maintaining design quality.
Adhering to these standards ensures that products meet legal requirements and safety guidelines.
Staying updated with the latest standards and integrating them into the design process is essential for maintaining high design quality.
Enhancing Quality Through Continuous Improvement
Continuous improvement is key to long-term success in design quality.
Manufacturers should regularly analyze their processes and products to identify areas for improvement.
Using techniques such as Lean Manufacturing and Six Sigma can help in optimizing design and production processes, ultimately leading to reduced defects and enhanced quality.
Reducing Recalls and Customer Complaints
The ultimate goal of building design quality is to minimize recalls and customer complaints, enhancing satisfaction and trust.
Effective Communication with Customers
Keeping open lines of communication with customers can provide valuable insights into product performance and areas for improvement.
Feedback mechanisms such as surveys, customer service channels, and social media can be used to gather customer opinions and experiences with the product.
Establishing a Robust Quality Management System (QMS)
A Quality Management System (QMS) provides a framework for consistent quality practices across the manufacturing process.
Implementing a QMS helps standardize procedures, monitor product quality, and implement corrective actions when necessary.
A robust QMS can significantly contribute to reducing defects and recalls.
Conclusion
Visualizing and building design quality in your manufacturing process is crucial for preventing recalls, customer complaints, and chronic manufacturing defects.
By employing tools like CAD, prototypes, and DFMEA, and involving stakeholders in design reviews, manufacturers can enhance design and production processes.
Prioritizing communication, compliance, and continuous improvement can lead to consistently high-quality products and satisfied customers.
資料ダウンロード
QCD管理受発注クラウド「newji」は、受発注部門で必要なQCD管理全てを備えた、現場特化型兼クラウド型の今世紀最高の受発注管理システムとなります。
ユーザー登録
受発注業務の効率化だけでなく、システムを導入することで、コスト削減や製品・資材のステータス可視化のほか、属人化していた受発注情報の共有化による内部不正防止や統制にも役立ちます。
NEWJI DX
製造業に特化したデジタルトランスフォーメーション(DX)の実現を目指す請負開発型のコンサルティングサービスです。AI、iPaaS、および先端の技術を駆使して、製造プロセスの効率化、業務効率化、チームワーク強化、コスト削減、品質向上を実現します。このサービスは、製造業の課題を深く理解し、それに対する最適なデジタルソリューションを提供することで、企業が持続的な成長とイノベーションを達成できるようサポートします。
製造業ニュース解説
製造業、主に購買・調達部門にお勤めの方々に向けた情報を配信しております。
新任の方やベテランの方、管理職を対象とした幅広いコンテンツをご用意しております。
お問い合わせ
コストダウンが利益に直結する術だと理解していても、なかなか前に進めることができない状況。そんな時は、newjiのコストダウン自動化機能で大きく利益貢献しよう!
(β版非公開)