- お役立ち記事
- Hydrogen Embrittlement Countermeasures and Durability Improvement for Metals
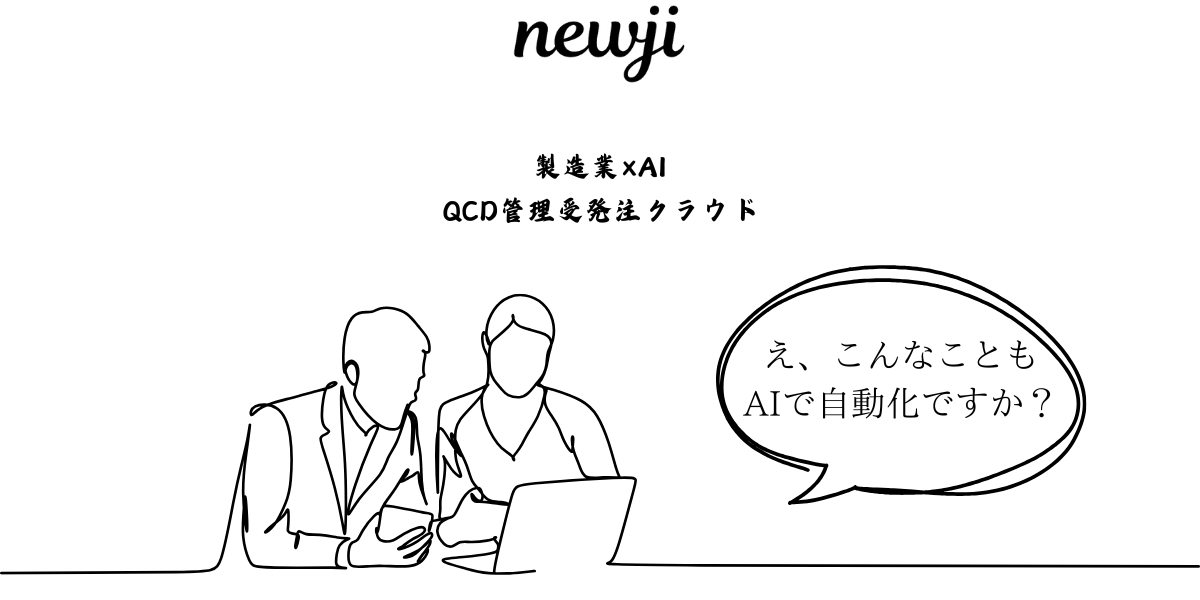
Hydrogen Embrittlement Countermeasures and Durability Improvement for Metals
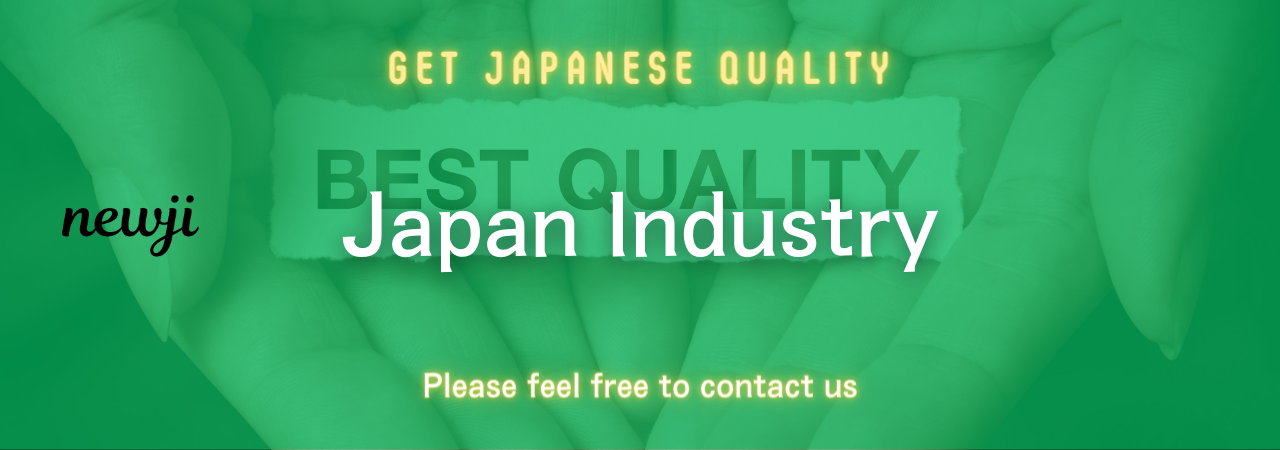
目次
Understanding Hydrogen Embrittlement
Hydrogen embrittlement is a phenomenon where metals become brittle and crack due to the infiltration and diffusion of hydrogen into their structure.
This issue is particularly concerning in industries that rely heavily on metal components, such as automotive, aerospace, and energy production.
The degradation of metal integrity can lead to unexpected failures and costly repairs, making it crucial to address this problem effectively.
The process begins when hydrogen atoms enter the metal lattice, usually during processes like electroplating, welding, or simply through environmental exposure.
Once inside, these atoms can form bubbles or combine with other elements present, such as carbon, to form brittle compounds.
Eventually, the presence of hydrogen causes microfractures, which may lead to catastrophic failures if not mitigated.
To combat hydrogen embrittlement, it’s important first to understand the environments and processes that predispose metals to this condition.
Identifying Susceptible Materials
Not all metals are equally affected by hydrogen embrittlement.
High-strength steels, titanium alloys, and certain nickel-based alloys are particularly susceptible.
These materials are often chosen for their superior mechanical properties, but their affinity for hydrogen makes them vulnerable.
Lower-strength alloys or metals like stainless steel and aluminum are generally more resistant.
Understanding which materials are prone to embrittlement is the first step in developing effective countermeasures.
Engineers and designers must choose materials not just based on strength and weight but also on their environment of use and exposure to hydrogen.
Environmental Considerations
Hydrogen can be introduced into metals through several environmental factors.
These include exposure to hydrogen gas, liquid hydrogen, or environments where hydrogen is generated, such as electrochemical reactions and moisture.
For instance, metals used in oil and gas pipelines are often exposed to conditions that generate hydrogen.
Thus, identifying and controlling these environmental factors is critical in preventing hydrogen ingress.
Preventive Measures
Preventing hydrogen embrittlement involves a combination of material choice, protective coatings, and process optimization.
Material Selection
Selecting the right materials for the intended application is the simplest and often the most effective way to prevent hydrogen embrittlement.
Whenever possible, choose metals less susceptible to hydrogen infiltration.
Design considerations should also take into account the service conditions, selecting materials with inherent resistance to hydrogen effects.
Protective Coatings
Applying coatings to susceptible metals is another effective method to prevent embrittlement.
Barrier coatings can prevent hydrogen from interacting with the metal surface.
Electroless nickel plating, phosphate coatings, or using polymer-based coatings can significantly reduce hydrogen ingress.
Regular maintenance and inspection of these coatings are essential to ensure their effectiveness over time.
Process Optimization
Processes that expose metals to hydrogen, such as electroplating, should be carefully controlled to minimize exposure.
Optimizing process parameters, such as temperature and duration, can reduce the introduction of hydrogen.
Heat treatments, such as baking, immediately after processes suspected of introducing hydrogen, can help in diffusing hydrogen out of the metal structure.
Testing and Detection
Detecting hydrogen embrittlement early can prevent significant failures.
A variety of techniques can be used to assess the integrity of metals exposed to hydrogen.
Non-destructive Testing
Techniques such as ultrasonic testing, magnetic particle inspection, and eddy current testing can identify subsurface cracks and flaws without compromising the component.
These methods are crucial for continuous monitoring of structural components in industries.
Destructive Testing
Destructive testing, although compromising some materials, provides valuable data about material performance under load.
Tests such as tensile and impact testing can be used to evaluate the extent of embrittlement in a controlled manner.
This data is invaluable for understanding the effects of hydrogen on specific materials and environments.
Long-term Durability Improvement
Incorporating long-term strategies to improve the durability of metals involves not only addressing current hydrogen embrittlement issues but also future-proofing against new challenges.
Research and Development
Continuous R&D is essential for developing new materials and coatings with improved resistance to hydrogen.
Recent advancements in nanotechnology and material science are paving the way for the development of alloys with better resilience to embrittlement.
Research in the field of hydrogen embrittlement is dynamic, and staying informed about the latest developments can lead to better solutions.
Design Adjustments
Designing components with built-in safety margins and designing for easy inspection and maintenance access can significantly improve the durability of metal structures.
By anticipating potential embrittlement points, engineers can adjust designs to accommodate occasional hydrogen-related stresses.
Conclusion
Hydrogen embrittlement presents a significant challenge for various industries, but with appropriate countermeasures and a proactive approach, its impact can be minimized.
At its core, overcoming hydrogen embrittlement requires a thorough understanding of material properties, environmental conditions, and effective technological solutions.
Implementing preventive strategies, continuous testing, and long-term durability improvements are vital for maintaining the integrity of metal structures exposed to potential hydrogen infiltration.
Through consistent innovation and vigilance, industries can significantly reduce the risks associated with hydrogen embrittlement, ensuring safer and more reliable operations.
資料ダウンロード
QCD調達購買管理クラウド「newji」は、調達購買部門で必要なQCD管理全てを備えた、現場特化型兼クラウド型の今世紀最高の購買管理システムとなります。
ユーザー登録
調達購買業務の効率化だけでなく、システムを導入することで、コスト削減や製品・資材のステータス可視化のほか、属人化していた購買情報の共有化による内部不正防止や統制にも役立ちます。
NEWJI DX
製造業に特化したデジタルトランスフォーメーション(DX)の実現を目指す請負開発型のコンサルティングサービスです。AI、iPaaS、および先端の技術を駆使して、製造プロセスの効率化、業務効率化、チームワーク強化、コスト削減、品質向上を実現します。このサービスは、製造業の課題を深く理解し、それに対する最適なデジタルソリューションを提供することで、企業が持続的な成長とイノベーションを達成できるようサポートします。
オンライン講座
製造業、主に購買・調達部門にお勤めの方々に向けた情報を配信しております。
新任の方やベテランの方、管理職を対象とした幅広いコンテンツをご用意しております。
お問い合わせ
コストダウンが利益に直結する術だと理解していても、なかなか前に進めることができない状況。そんな時は、newjiのコストダウン自動化機能で大きく利益貢献しよう!
(Β版非公開)