- お役立ち記事
- IC design and manufacturing considerations for ESD protection that quality assurance leaders in the semiconductor industry should know
IC design and manufacturing considerations for ESD protection that quality assurance leaders in the semiconductor industry should know
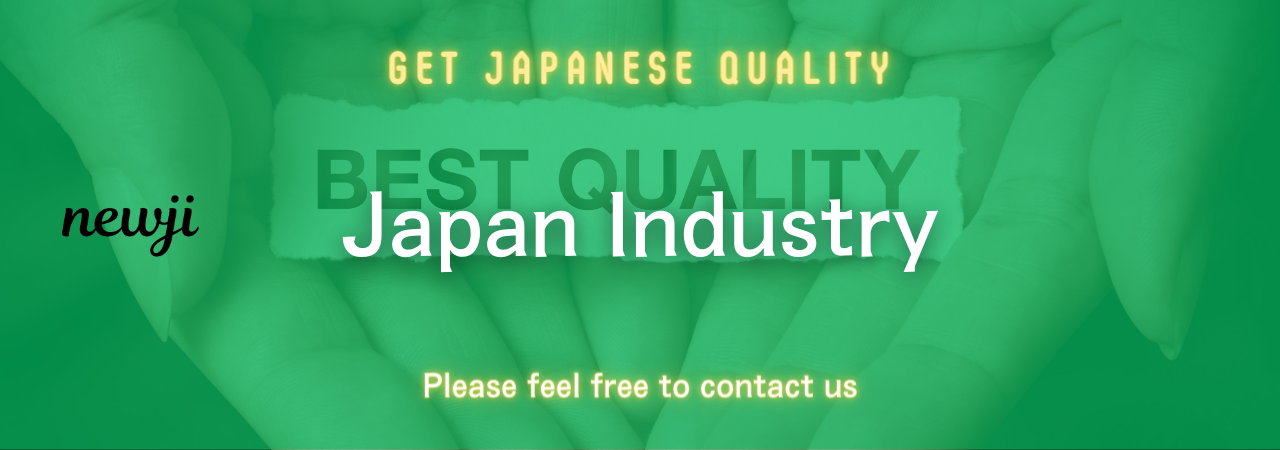
目次
Introduction to ESD Protection in IC Design
The importance of Electrostatic Discharge (ESD) protection in Integrated Circuit (IC) design cannot be overstated, particularly for quality assurance leaders in the semiconductor industry.
To ensure the reliability and functionality of ICs, it’s crucial to implement robust ESD protection measures during design and manufacturing.
By understanding key considerations and methodologies for ESD protection, teams can significantly improve the quality and longevity of their semiconductor products.
Understanding Electrostatic Discharge (ESD)
Electrostatic Discharge is a sudden flow of electricity between two electrically charged objects, caused by contact.
In the context of semiconductor manufacturing, ESD can lead to catastrophic failures or latent defects in ICs.
This makes it a critical area of concern for quality assurance leaders who are focused on ensuring the delivery of high-quality semiconductor products.
The Impact of ESD on ICs
When an IC is exposed to an ESD event, the influx of high voltage can cause permanent damage to the delicate structures within the chip.
This damage can manifest immediately, resulting in a non-functional product, or it may cause latent defects that become apparent later during operation.
Both situations can result in costly product recalls, damage to brand reputation, and significant financial losses.
Design Considerations for ESD Protection
Effective ESD protection begins with careful IC design.
There are several strategies and best practices that designers can employ to mitigate ESD risks.
Incorporating ESD Protection Devices
One of the primary methods for protecting ICs from ESD is the inclusion of dedicated ESD protection devices, such as diodes and resistors.
These components are designed to safely redirect the ESD current away from sensitive areas of the IC.
By integrating these devices into the circuit design, the overall resilience of the IC to ESD events is significantly enhanced.
Optimizing Circuit Layout
The physical layout of an IC also plays a crucial role in ESD protection.
Designers should aim to minimize parasitic inductance and resistance, which can exacerbate the effects of ESD.
Additionally, ensuring proper spacing between lines and integrating ground rings can help dissipate ESD energy more effectively.
Utilizing On-Chip Protection Strategies
On-chip protection strategies, such as the implementation of guard rings, are vital for isolating sensitive areas of the IC from potential ESD damage.
Guard rings act as barriers, directing ESD energy away from critical circuit components.
This method is particularly advantageous in mixed-signal devices, where digital and analog components coexist.
Manufacturing Considerations for ESD Protection
Beyond design, ESD protection must be a focus throughout the IC manufacturing process.
Ensuring that protective measures are maintained during production is essential for preserving the integrity of ESD safeguards.
Implementing ESD-Controlled Environments
To mitigate the risk of ESD damage during manufacturing, it is essential to maintain ESD-controlled environments.
This includes equipping production facilities with anti-static flooring, ESD-safe workstations, and proper grounding equipment.
Training staff in ESD safety protocols is also crucial to preventing incidents during handling and assembly.
Quality Assurance Testing and Validation
Comprehensive testing and validation processes should be a cornerstone of any ESD protection strategy in IC manufacturing.
This includes subjecting ICs to ESD stress tests that simulate real-world ESD events.
Through these tests, manufacturers can validate that the ESD protection measures are effective and adhere to industry standards.
Ongoing Monitoring and Improvement
Continuous monitoring of the manufacturing process is necessary to identify and mitigate potential ESD risks.
This involves regular audits of ESD control procedures and the implementation of corrective measures as needed.
Feedback from the monitoring process can drive ongoing improvements and ensure that the highest levels of product quality are maintained.
Conclusion: The Role of ESD Protection in Quality Assurance
For quality assurance leaders in the semiconductor industry, understanding and implementing effective ESD protection measures is paramount.
By focusing on both design and manufacturing considerations, ICs can be safeguarded against the adverse effects of ESD, ensuring reliable and high-quality semiconductor products.
Adhering to best practices for ESD protection not only protects the integrity of ICs but also reinforces trust in the products delivered to consumers, thereby safeguarding brand reputation and financial performance.
資料ダウンロード
QCD調達購買管理クラウド「newji」は、調達購買部門で必要なQCD管理全てを備えた、現場特化型兼クラウド型の今世紀最高の購買管理システムとなります。
ユーザー登録
調達購買業務の効率化だけでなく、システムを導入することで、コスト削減や製品・資材のステータス可視化のほか、属人化していた購買情報の共有化による内部不正防止や統制にも役立ちます。
NEWJI DX
製造業に特化したデジタルトランスフォーメーション(DX)の実現を目指す請負開発型のコンサルティングサービスです。AI、iPaaS、および先端の技術を駆使して、製造プロセスの効率化、業務効率化、チームワーク強化、コスト削減、品質向上を実現します。このサービスは、製造業の課題を深く理解し、それに対する最適なデジタルソリューションを提供することで、企業が持続的な成長とイノベーションを達成できるようサポートします。
オンライン講座
製造業、主に購買・調達部門にお勤めの方々に向けた情報を配信しております。
新任の方やベテランの方、管理職を対象とした幅広いコンテンツをご用意しております。
お問い合わせ
コストダウンが利益に直結する術だと理解していても、なかなか前に進めることができない状況。そんな時は、newjiのコストダウン自動化機能で大きく利益貢献しよう!
(Β版非公開)