- お役立ち記事
- “Ideas for reducing purchasing costs”—10 methods that can be implemented immediately on site
月間76,176名の
製造業ご担当者様が閲覧しています*
*2025年3月31日現在のGoogle Analyticsのデータより
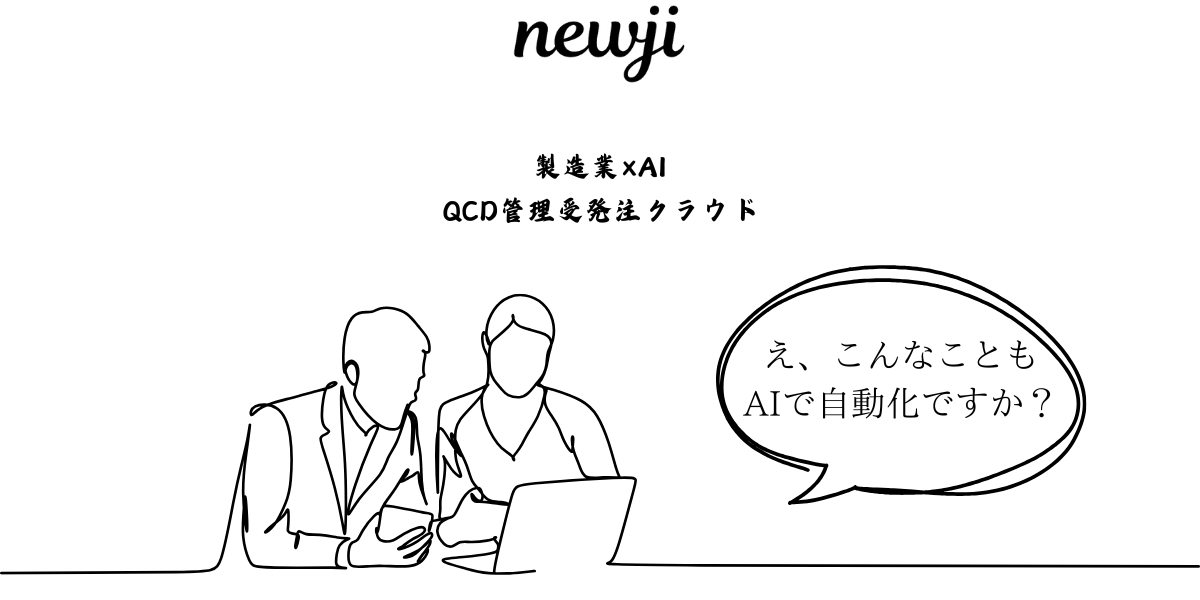
“Ideas for reducing purchasing costs”—10 methods that can be implemented immediately on site
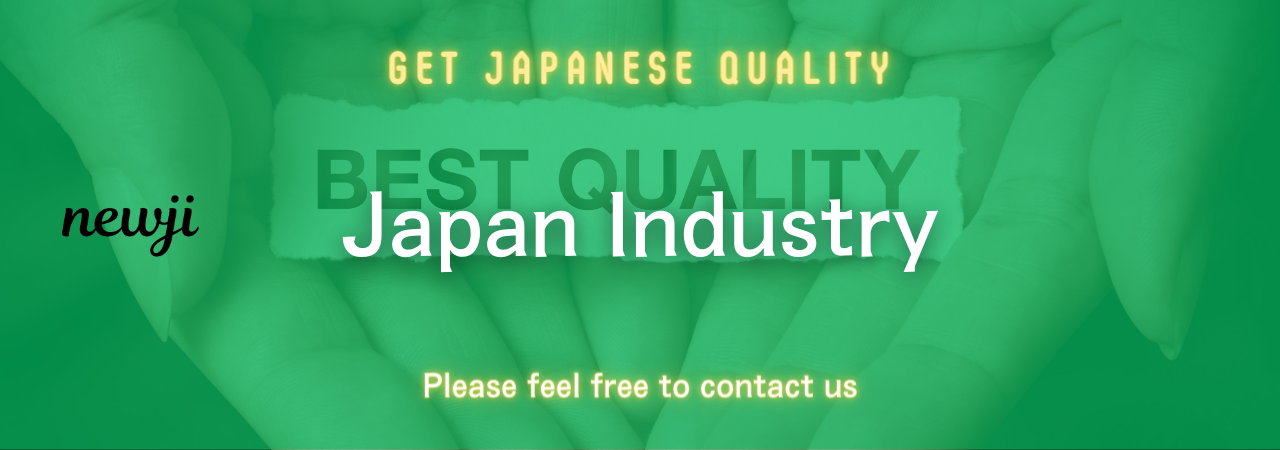
Reducing purchasing costs is a crucial aspect of financial management for any organization.
Whether you’re a small business owner or part of a large corporation, finding effective ways to cut down on expenses can lead to significant savings.
With a strategic approach, you can optimize procurement processes and maximize your budget.
Let’s explore ten actionable methods to reduce purchasing costs that you can put into action immediately.
目次
1. Analyze Current Spending
The first step in reducing purchasing costs is understanding where your money is currently going.
Conduct a thorough analysis of your spending patterns.
Identify areas where expenses are highest and evaluate whether they are necessary.
This analysis will help pinpoint inefficiencies and opportunities for cost reduction.
Review Supplier Contracts
Reviewing contracts with current suppliers can reveal opportunities for savings.
Negotiate better terms, discounts, or volume rebates to lower costs.
Ensure that all pricing structures are competitive and align with the current market trends.
2. Consolidate Suppliers
Working with too many suppliers can lead to inefficiencies and higher costs.
By consolidating suppliers, you can leverage better terms, streamline communication, and benefit from bulk purchasing.
Choose reliable suppliers that offer competitive pricing and high-quality products.
Evaluate Supplier Performance
Regularly assess supplier performance to ensure they meet expectations in terms of quality, delivery, and price.
Establish criteria for evaluating suppliers, and consider replacing those who do not meet standards.
3. Embrace Technology
Implementing technology solutions can dramatically reduce purchasing costs.
Use procurement software to automate processes, manage inventory, and analyze data for better decision-making.
Technology can streamline purchasing and identify cost-saving opportunities that may not be apparent through manual processes.
Leverage E-Procurement
E-procurement systems enable businesses to handle purchases online, improving efficiency and transparency.
This approach minimizes paperwork, reduces errors, and typically lowers transactional costs.
4. Negotiate Better Deals
Don’t settle for the first price offered by suppliers.
Negotiation is key to securing better deals.
Communicate your needs clearly and use your purchasing history as leverage to achieve discounts or more favorable payment terms.
Build Strategic Relationships
Develop strong relationships with key suppliers.
A strategic partnership can result in loyalty discounts and improved service levels.
Suppliers may be more willing to negotiate better terms if they see a long-term relationship.
5. Standardize Products
Standardizing products across the organization can help reduce purchasing costs by simplifying procurement processes.
By sticking to specific models or brands, you can negotiate bulk purchases with suppliers and achieve lower unit costs.
Streamline Product Specifications
Avoid excessive customization that can increase costs.
Instead, opt for standard specifications that meet your requirements without unnecessary enhancements.
6. Optimize Inventory Management
Effective inventory management is crucial for cost reduction.
Implement a system that tracks inventory levels in real time to avoid overstocking or stockouts.
By optimizing inventory, you can reduce storage costs and minimize waste.
Implement Just-in-Time (JIT) Inventory
JIT inventory management ensures that products are acquired only as they are needed.
This reduces the costs associated with holding and managing excess inventory.
7. Outsource Non-Core Activities
Consider outsourcing non-core purchasing activities to third-party providers.
This can allow your team to focus on strategic procurement while potentially reducing expenses related to staffing and operations.
Evaluate Cost Benefits
Carefully evaluate the cost benefits of outsourcing.
Sometimes, external providers can perform tasks more efficiently and at a lower cost than in-house teams.
8. Encourage Collaborative Purchasing
Collaborate with other businesses or departments to gain better purchasing power.
By pooling resources, organizations can achieve volume discounts and share best practices for further cost reductions.
Join Purchasing Consortia
Consider joining a purchasing consortium.
These groups combine the purchasing power of multiple organizations, leading to more favorable pricing.
9. Implement a Supplier Incentive Program
Encourage suppliers to offer competitive pricing through an incentive program.
Reward suppliers that deliver on time, meet quality standards, and offer competitive prices.
This can foster a competitive environment and drive cost savings.
Set Performance Targets
Establish clear performance targets tied to incentives.
This encourages suppliers to align their pricing strategies with your cost reduction goals.
10. Continuously Monitor and Review
Cost reduction is an ongoing process, not a one-time task.
Regularly monitor purchasing activities and review strategies to capture further savings.
Adopt a culture of continuous improvement, where cost-saving measures are constantly evaluated and adjusted.
Conduct Regular Audits
Conduct periodic audits of purchasing operations to ensure compliance with cost reduction strategies.
Audits can reveal areas where further efficiencies can be achieved.
In conclusion, reducing purchasing costs is a vital strategy for optimizing business resources and improving profitability.
By implementing these ten methods, you can achieve immediate savings and create a foundation for long-term financial stability.
The key is to remain proactive, continuously assess opportunities, and build strong supplier relationships for ongoing success.
資料ダウンロード
QCD管理受発注クラウド「newji」は、受発注部門で必要なQCD管理全てを備えた、現場特化型兼クラウド型の今世紀最高の受発注管理システムとなります。
ユーザー登録
受発注業務の効率化だけでなく、システムを導入することで、コスト削減や製品・資材のステータス可視化のほか、属人化していた受発注情報の共有化による内部不正防止や統制にも役立ちます。
NEWJI DX
製造業に特化したデジタルトランスフォーメーション(DX)の実現を目指す請負開発型のコンサルティングサービスです。AI、iPaaS、および先端の技術を駆使して、製造プロセスの効率化、業務効率化、チームワーク強化、コスト削減、品質向上を実現します。このサービスは、製造業の課題を深く理解し、それに対する最適なデジタルソリューションを提供することで、企業が持続的な成長とイノベーションを達成できるようサポートします。
製造業ニュース解説
製造業、主に購買・調達部門にお勤めの方々に向けた情報を配信しております。
新任の方やベテランの方、管理職を対象とした幅広いコンテンツをご用意しております。
お問い合わせ
コストダウンが利益に直結する術だと理解していても、なかなか前に進めることができない状況。そんな時は、newjiのコストダウン自動化機能で大きく利益貢献しよう!
(β版非公開)