- お役立ち記事
- IE Basics for Manufacturing Site Leaders and New Managers
IE Basics for Manufacturing Site Leaders and New Managers
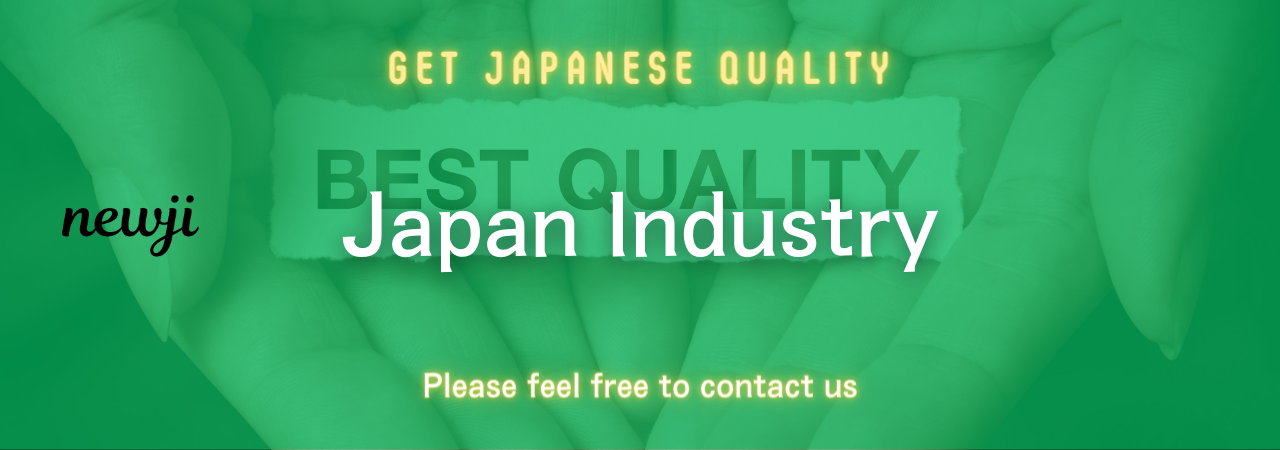
Industrial Engineering (IE) is a crucial field for improving processes, productivity, and efficiency in manufacturing sites.
For site leaders and new managers, understanding the fundamentals of IE can lay a solid foundation for making informed decisions and driving improvements.
This article will guide you through some of the essential concepts of IE and how they relate to your role in a manufacturing environment.
目次
What is Industrial Engineering?
Industrial Engineering is the discipline focused on optimizing processes, systems, or organizations by improving efficiency, productivity, and quality.
IE combines knowledge from mathematics, science, and engineering to design, monitor, and enhance complex systems.
Understanding IE enables site leaders and managers to better manage resources, maximize output, and ensure quality.
The Role of Industrial Engineering in Manufacturing
In the manufacturing sector, IE techniques are used to streamline production processes, reduce waste, improve safety, and cut costs.
By integrating IE principles, manufacturing sites can boost overall performance and maintain a competitive edge.
Process Optimization
Process optimization involves analyzing and improving the steps involved in manufacturing to make them more efficient.
IE tools such as time-motion studies and process mapping help identify bottlenecks and areas of opportunity.
By optimizing processes, leaders can reduce cycle times and increase throughput.
Lean Manufacturing
Lean manufacturing is a methodology that focuses on minimizing waste while maximizing value.
The main types of waste identified in lean are overproduction, waiting, transport, overprocessing, inventory, motion, and defects.
Implementing lean principles helps in creating more streamlined and efficient production processes.
Key Concepts and Techniques in Industrial Engineering
Several key concepts and techniques are vital for new managers and site leaders to understand and implement.
Here’s a closer look at some of these essential elements.
Six Sigma
Six Sigma is a set of techniques and tools used for process improvement, aiming for near-perfect quality.
It uses statistical methods to reduce variability and defects in processes.
Understanding Six Sigma allows leaders to lead projects that improve quality and efficiency.
5S System
The 5S system is a workplace organization method that stands for Sort, Set in order, Shine, Standardize, and Sustain.
Implementing the 5S approach helps keep the manufacturing floor organized, reduces waste, and enhances safety.
Total Quality Management (TQM)
TQM is a comprehensive approach to long-term success through customer satisfaction.
It involves all members of an organization in improving processes, products, services, and culture.
Understanding TQM can help managers foster a culture of continuous improvement.
Work Measurement
Work measurement involves the collection and analysis of data to establish time standards for performing specified tasks.
Techniques such as time studies and predetermined motion time systems (PMTS) are used to set accurate work standards.
These standards are essential for planning, costing, scheduling, and controlling production operations.
Value Stream Mapping (VSM)
VSM is a lean-management method used to analyze and design the flow of materials and information required to bring a product to a customer.
It helps identify waste and areas for improvement.
New managers can use VSM to gain a comprehensive view of the production process.
Ergonomics
Ergonomics focuses on designing workstations, tools, and practices that fit the capabilities and limitations of workers.
This reduces the risk of injury and enhances productivity.
Understanding ergonomics can lead to a healthier, more efficient workforce.
Implementing IE Principles
For site leaders and new managers, implementing IE principles can seem daunting.
However, breaking it down into manageable steps can simplify the process.
Identify Objectives
Before implementing changes, it’s critical to identify the specific objectives and goals.
Whether it’s reducing cycle time, improving quality, or increasing throughput, having clear objectives guides the entire process.
Data Collection and Analysis
Collecting accurate data is a cornerstone of IE.
Use various tools and techniques to gather data on current processes.
Analyzing this data helps identify bottlenecks, waste, and opportunities for improvement.
Develop and Test Solutions
Once areas for improvement are identified, develop potential solutions.
It’s essential to test these solutions on a small scale before full implementation.
This ensures they work as intended without causing disruption.
Implement and Monitor
After successful testing, implement the chosen solutions across the manufacturing site.
It’s crucial to continuously monitor the new processes to ensure they deliver the expected benefits and make adjustments as needed.
The Benefits of Industrial Engineering
Implementing IE principles in manufacturing brings numerous benefits.
Increased Efficiency
Optimized processes reduce cycle times and increase output.
This means more products can be manufactured in less time, improving overall efficiency.
Cost Reduction
By minimizing waste and improving processes, IE techniques help reduce operational costs.
This includes saving on materials, labor, and overhead.
Enhanced Quality
Techniques like Six Sigma and TQM focus on reducing defects and variability.
This leads to higher quality products, which enhances customer satisfaction.
Improved Safety
IE principles promote a safer work environment through better ergonomics and efficient processes.
This reduces workplace injuries and associated costs.
Conclusion
Industrial Engineering is vital for the success of manufacturing sites.
For site leaders and new managers, understanding and implementing IE principles can lead to significant improvements in efficiency, cost reduction, quality, and safety.
By adopting these techniques, managers can drive their teams towards continuous improvements and maintain a competitive edge in the industry.
This foundational knowledge will serve as a critical toolset in navigating the complex landscape of modern manufacturing.
資料ダウンロード
QCD調達購買管理クラウド「newji」は、調達購買部門で必要なQCD管理全てを備えた、現場特化型兼クラウド型の今世紀最高の購買管理システムとなります。
ユーザー登録
調達購買業務の効率化だけでなく、システムを導入することで、コスト削減や製品・資材のステータス可視化のほか、属人化していた購買情報の共有化による内部不正防止や統制にも役立ちます。
NEWJI DX
製造業に特化したデジタルトランスフォーメーション(DX)の実現を目指す請負開発型のコンサルティングサービスです。AI、iPaaS、および先端の技術を駆使して、製造プロセスの効率化、業務効率化、チームワーク強化、コスト削減、品質向上を実現します。このサービスは、製造業の課題を深く理解し、それに対する最適なデジタルソリューションを提供することで、企業が持続的な成長とイノベーションを達成できるようサポートします。
オンライン講座
製造業、主に購買・調達部門にお勤めの方々に向けた情報を配信しております。
新任の方やベテランの方、管理職を対象とした幅広いコンテンツをご用意しております。
お問い合わせ
コストダウンが利益に直結する術だと理解していても、なかなか前に進めることができない状況。そんな時は、newjiのコストダウン自動化機能で大きく利益貢献しよう!
(Β版非公開)