- お役立ち記事
- Ignition/smoke generation mechanisms of electrical/electronic components and countermeasure technology
Ignition/smoke generation mechanisms of electrical/electronic components and countermeasure technology
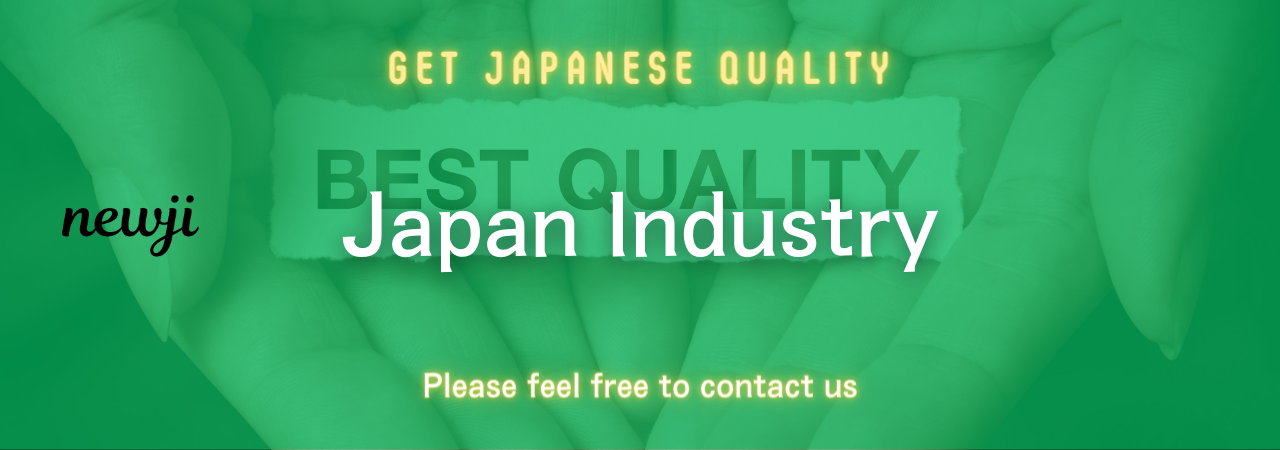
Understanding Ignition and Smoke Generation in Electronic Components
In our modern world, electrical and electronic devices have become indispensable.
From our homes to industries, these devices facilitate essential functions and improve efficiency.
However, with the increasing reliance on electronics, the risk of ignition and smoke generation has also become more prominent.
Understanding why and how these incidents occur is crucial for implementing effective countermeasures.
Electrical and electronic components may cause fires or smoke for various reasons.
Some occurrences are due to design flaws, while others are related to external factors or improper use.
By exploring these causes, we can better understand how to prevent such hazardous situations.
Causes of Ignition in Electrical Components
Ignition in electrical components can result from several sources.
One of the most common causes is an electrical short circuit.
This happens when an electrical path is unintentionally created, allowing currents to bypass the intended circuitry.
If the current is too high, the components can overheat and catch fire.
Another frequent cause is overloading.
When an electrical device is exposed to a current or voltage higher than what it is rated for, it can lead to excessive heating.
Materials like insulation and wiring can reach their ignition temperature, resulting in fires.
Improper component design can also be a major factor.
Mistakes in the selection of materials, poor thermal management, or lack of effective cooling solutions can lead to component failure and subsequent ignition.
Finally, physical damage to electrical devices, perhaps from impact or environmental exposure, can hamper the safe functioning of the components.
This damage can lead to ignitable conditions if not addressed correctly.
Smoke Generation in Electronic Devices
Smoke is often an early indicator of a looming fire risk.
In electronic components, smoke can result from overheating, poor insulation, or chemical reactions.
When a component overheats, it can cause the materials within to break down.
This breakdown can release hazardous gases and particles, evident as smoke.
Over time, components that are constantly under stress from heat may reach a point of failure, becoming smoke sources.
Poor insulation compromises a component’s ability to contain electrical energy or heat within designated paths.
Insulation breakdown can lead to arcing or sparks which might produce smoke.
Chemical reactions can occur as a result of component failings or external factors.
Instances include failures in lithium-ion batteries that might ignite due to dendrite formation, releasing harmful smoke.
Countermeasure Technologies to Prevent Ignition and Smoke
Addressing ignition and smoke generation in electronic components requires a multifaceted approach.
Technologies and best practices are continually evolving to manage and mitigate these risks effectively.
Design Optimization
A key preventive measure is ensuring robust design.
Engineers must use materials and components that can withstand the electrical loads they might face.
Proper thermal management, like heat sinks and thermal interface materials, helps dissipate excess heat, reducing the risk of overheating and ignition.
The use of fire-retardant materials in manufacturing can also limit the spread of fires should ignition occur.
Some designs include self-extinguishing features where electronic components contain flame-suppression systems.
Improved Testing and Quality Control
Stringent testing procedures can significantly reduce the risk of failure.
Before electronic components reach the market, they should undergo a series of rigorous tests to ensure they meet or exceed safety standards.
Quality control checks lessen the prospect of defects that could lead to ignition or smoke generation.
Applying techniques such as thermal imaging can help in the early identification of potential problem areas in electronic designs.
This proactive approach can prevent costly recalls and ensure devices operate safely for their intended lifespan.
Smart Monitoring and Detection Systems
Implementing advanced monitoring systems can detect anomalies in real time.
One such technology is current sensing, which monitors electrical flow and recognizes irregularities that might precede a failure.
These systems can automatically disconnect power, preventing overheating and reducing fire risks.
Smoke detectors specifically designed for electronics can provide early warnings.
These detectors identify subtle signs of smoke within an enclosed device, allowing for rapid interventions before a situation escalates.
Education and Awareness
It’s important for consumers and professionals alike to be aware of the potential hazards associated with electronic devices.
Training programs and informational resources can equip users with knowledge on best practices and emergency response strategies.
Regular maintenance and inspections are essential for keeping devices in working order.
Addressing small issues before they become major problems is key to ensuring safety.
The Role of Standards and Regulations
Compliance with established standards and regulations is essential for minimizing risks.
Agencies such as the International Electrotechnical Commission (IEC) and Underwriters Laboratories (UL) set guidelines for safety in electronic components.
Adhering to these standards ensures that manufacturers maintain a safety baseline.
These standards also evolve alongside technology, addressing new challenges as they arise.
They provide a framework for developing safer products and protecting consumers.
Conclusion
Electronic components are integral to modern life, but they come with inherent risks of ignition and smoke generation.
Understanding these risks and implementing effective countermeasures can prevent hazardous events and protect lives.
From optimized designs and materials to rigorous testing and proactive monitoring, various technologies and strategies work harmoniously to improve safety.
As technology advances, so too will our methods for mitigating risks, ensuring that electronic devices remain safe for users worldwide.
資料ダウンロード
QCD調達購買管理クラウド「newji」は、調達購買部門で必要なQCD管理全てを備えた、現場特化型兼クラウド型の今世紀最高の購買管理システムとなります。
ユーザー登録
調達購買業務の効率化だけでなく、システムを導入することで、コスト削減や製品・資材のステータス可視化のほか、属人化していた購買情報の共有化による内部不正防止や統制にも役立ちます。
NEWJI DX
製造業に特化したデジタルトランスフォーメーション(DX)の実現を目指す請負開発型のコンサルティングサービスです。AI、iPaaS、および先端の技術を駆使して、製造プロセスの効率化、業務効率化、チームワーク強化、コスト削減、品質向上を実現します。このサービスは、製造業の課題を深く理解し、それに対する最適なデジタルソリューションを提供することで、企業が持続的な成長とイノベーションを達成できるようサポートします。
オンライン講座
製造業、主に購買・調達部門にお勤めの方々に向けた情報を配信しております。
新任の方やベテランの方、管理職を対象とした幅広いコンテンツをご用意しております。
お問い合わせ
コストダウンが利益に直結する術だと理解していても、なかなか前に進めることができない状況。そんな時は、newjiのコストダウン自動化機能で大きく利益貢献しよう!
(Β版非公開)