- お役立ち記事
- Impact of production lot reduction and production discontinuation on costs
Impact of production lot reduction and production discontinuation on costs
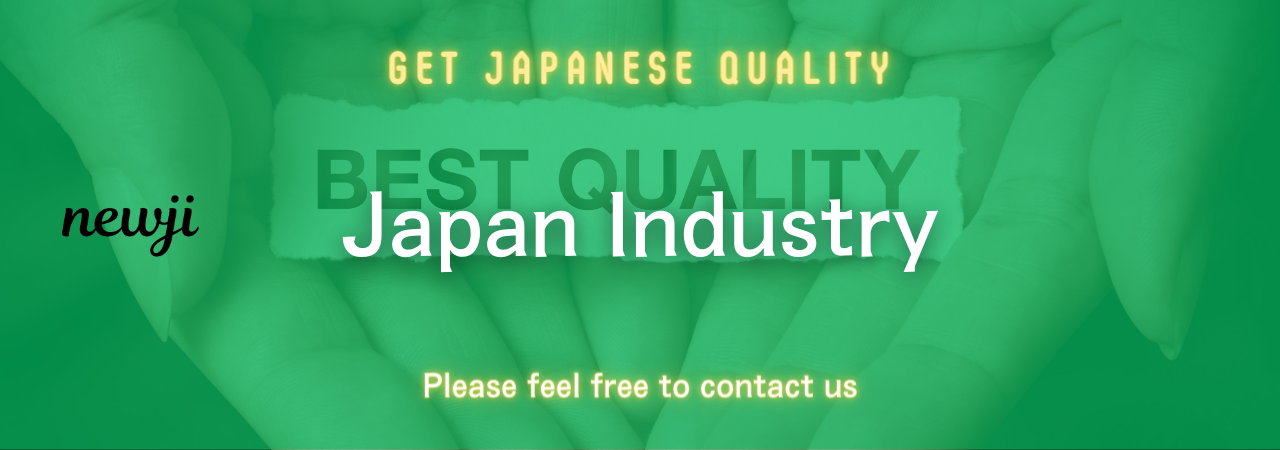
目次
Understanding Production Lot Reduction
Production lot reduction refers to the decreasing number of units produced in a single production run.
Traditionally, manufacturers aimed for large production lots.
This approach minimized costs per unit because of economies of scale—where the cost of production decreases as the quantity produced increases.
However, the shift towards lean manufacturing has changed this mindset.
Companies now focus on producing only what is needed to meet demand, which results in smaller production lots.
This shift minimizes waste, reduces inventory holding costs, and enhances product quality with quicker production cycles.
When a company decides to reduce production lots, it typically sees a direct impact on its production costs.
Smaller lots mean more frequent production runs, which can increase setup times and associated costs.
These costs include labor hours spent on configuring machinery for different products or parts, increasing operational expenses.
However, these increased setup costs might be offset by saving on storage and reduced capital tied up in unsold inventory.
Benefits of Smaller Production Lots
Reducing production lots can offer significant advantages despite the increased setup costs.
By producing smaller batches, manufacturers can respond more agilely to market changes.
This responsiveness means companies can closely match production with consumer demand, reducing the risk of overproduction.
Smaller production lots also encourage a more flexible manufacturing process.
Companies can quickly switch production lines to manufacture other products, catering to shifting demands and trends.
Such adaptability not only improves customer satisfaction but also allows businesses to capitalize on short-term market opportunities without delays.
Furthermore, producing smaller lots can enhance product quality.
With frequent turnovers, defects can be detected early, minimizing the risk of producing large quantities of faulty goods.
Overall, improved quality control leads to better end-products and a stronger brand reputation.
Impacts of Production Discontinuation
Production discontinuation occurs when a company ceases the manufacturing of a product.
This decision can stem from numerous factors, including declining demand, high production costs, or strategic business shifts.
While discontinuation can streamline operations and cut costs, it comes with its own set of challenges.
A significant issue faced by companies is the sunk costs associated with previously developed products.
These are often unrecoverable, meaning that any investments into research, development, or marketing for the discontinued product might result in a financial loss.
Another challenge with discontinuation is the impact on brand loyalty.
Customers who relied on a specific product might feel alienated, adversely affecting the brand’s reputation.
To mitigate such effects, businesses must effectively communicate discontinuation, offer alternatives, or compensate with new product developments that meet customer needs.
Cost Savings from Discontinuation
Nevertheless, discontinuing a product line can lead to significant cost savings.
For starters, direct cost reductions occur by eliminating expenses associated with manufacturing, materials, and labor dedicated to the product.
Moreover, companies can redirect resources to more profitable ventures.
This redirection might lead to improved efficiencies and better allocation of capital.
Additionally, discontinuation can streamline operations, aligning the company’s product offering with its core business strategy.
By doing so, manufacturers can optimize their inventory management and resource utilization, ultimately making their operations more efficient.
Furthermore, ceasing production of less profitable items allows companies to focus their innovation and development efforts on products with higher growth potential.
This focus can unlock new market opportunities and lead to long-term business success.
Balancing Act: Production Lot Reduction and Discontinuation
Weighing the cost benefits of production lot reductions against discontinuations involves a careful strategy alignment.
Businesses need comprehensive analyses to ensure that altering production strategies delivers more advantages than setbacks.
Risk assessments and market research can guide decision-making processes, enabling a smoother transition toward leaner operations.
It’s crucial for companies to adopt a balanced approach, continuously evaluating their production dynamics.
They should invest in robust data analytics to achieve real-time insights into market trends and consumer preferences.
These insights can guide strategic shifts, ensuring that any reduction or discontinuation decision enhances operational efficiencies without sacrificing customer satisfaction.
By remaining agile and open to strategic pivots, manufacturers can better manage costs, drive growth, and establish a competitive advantage in a rapidly changing market landscape.
This dynamic capability not only helps in coping with external pressures but also aligns with long-term business objectives.
Conclusion
In conclusion, both production lot reduction and production discontinuation impact costs in significant ways.
While smaller production lots can hike up operational expenses, their benefits of increased agility, less waste, and enhanced product quality can outweigh these costs.
On the other hand, discontinuation may lead to immediate cost reductions but can present challenges like potential brand reputation risks and sunk costs.
The key to mastering these strategies lies in striking a well-evaluated balance that aligns with the company’s overall business strategy.
By maintaining flexibility, leveraging data, and engaging in thoughtful planning, manufacturers can navigate these decisions effectively, ensuring sustainable success and competitiveness in their respective industries.
資料ダウンロード
QCD調達購買管理クラウド「newji」は、調達購買部門で必要なQCD管理全てを備えた、現場特化型兼クラウド型の今世紀最高の購買管理システムとなります。
ユーザー登録
調達購買業務の効率化だけでなく、システムを導入することで、コスト削減や製品・資材のステータス可視化のほか、属人化していた購買情報の共有化による内部不正防止や統制にも役立ちます。
NEWJI DX
製造業に特化したデジタルトランスフォーメーション(DX)の実現を目指す請負開発型のコンサルティングサービスです。AI、iPaaS、および先端の技術を駆使して、製造プロセスの効率化、業務効率化、チームワーク強化、コスト削減、品質向上を実現します。このサービスは、製造業の課題を深く理解し、それに対する最適なデジタルソリューションを提供することで、企業が持続的な成長とイノベーションを達成できるようサポートします。
オンライン講座
製造業、主に購買・調達部門にお勤めの方々に向けた情報を配信しております。
新任の方やベテランの方、管理職を対象とした幅広いコンテンツをご用意しております。
お問い合わせ
コストダウンが利益に直結する術だと理解していても、なかなか前に進めることができない状況。そんな時は、newjiのコストダウン自動化機能で大きく利益貢献しよう!
(Β版非公開)