- お役立ち記事
- Implement and benefit from Smart Maintenance: condition monitoring and maintenance prediction for manufacturing equipment
Implement and benefit from Smart Maintenance: condition monitoring and maintenance prediction for manufacturing equipment
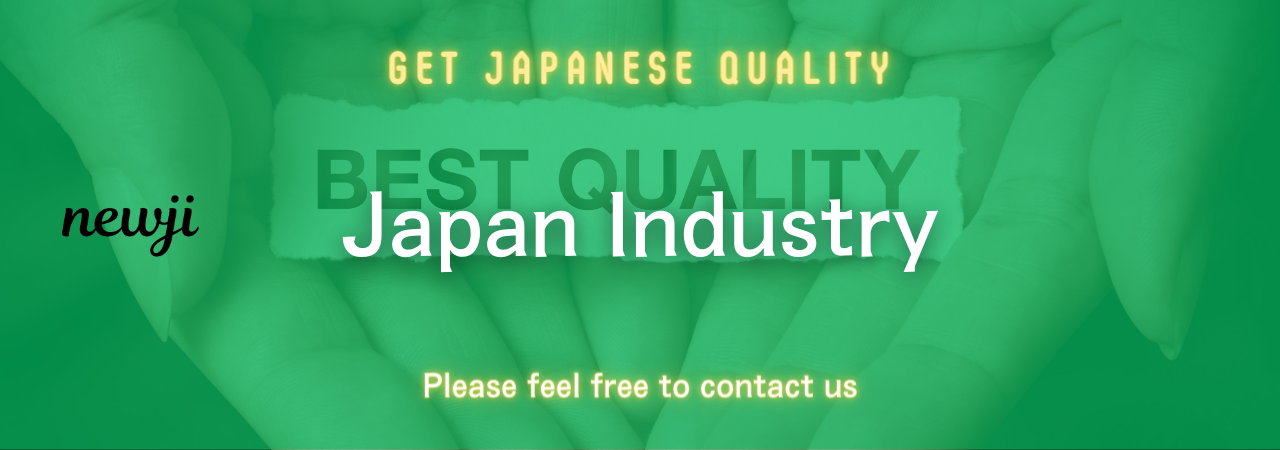
In today’s fast-paced manufacturing environment, ensuring that equipment operates efficiently is crucial.
Implementing smart maintenance techniques like condition monitoring and maintenance prediction can help achieve this goal.
Let’s explore what smart maintenance is, how it works, and the benefits it brings to manufacturing operations.
目次
Understanding Smart Maintenance
Smart maintenance combines advanced technologies with traditional maintenance practices to keep equipment in optimal condition.
It uses sensors and data analytics to monitor machinery in real-time, predict failures, and schedule maintenance activities proactively.
Condition Monitoring
Condition monitoring is a key component of smart maintenance.
It involves the continuous tracking of equipment performance using sensors and other devices.
These sensors measure various parameters like temperature, vibration, pressure, and more.
By analyzing this data, it becomes possible to detect any deviations from normal operating conditions.
For instance, an increase in vibration might indicate an imbalance or wear in a machine part.
With timely detection, maintenance can be done before a minor issue becomes a major problem.
Maintenance Prediction
Using the data collected from condition monitoring, maintenance prediction takes it a step further.
Advanced algorithms and machine learning models analyze historical and real-time data to forecast when equipment might fail.
This predictive approach allows maintenance teams to schedule repairs or part replacements at the most convenient times, minimizing downtime.
How Smart Maintenance Works
Data Collection
Smart maintenance starts with data collection.
Sensors placed on manufacturing equipment gather data on various performance metrics.
This data is then transmitted to a centralized system for analysis.
Data Analysis
The collected data is analyzed using sophisticated algorithms and machine learning models.
These models are trained to recognize patterns and predict potential failures.
For example, they can identify trends that precede equipment malfunctions, providing valuable insights for maintenance planning.
Maintenance Scheduling
Based on the analysis, maintenance activities are scheduled proactively.
Instead of waiting for equipment to break down, maintenance can be performed when it is most needed.
This approach helps in reducing unexpected downtime and extending the lifespan of machinery.
Benefits of Smart Maintenance
Reduced Downtime
One of the biggest advantages of smart maintenance is reduced downtime.
By predicting and addressing potential issues before they cause equipment failure, production interruptions are minimized.
This leads to higher productivity and cost savings.
Increased Equipment Lifespan
Regular monitoring and timely maintenance improve the overall health of machinery.
Fixing minor issues early prevents them from escalating into major problems, thereby extending the lifespan of the equipment.
This means fewer replacements and better return on investment.
Cost Savings
Predictive maintenance is cost-efficient compared to reactive maintenance.
Unexpected breakdowns can be expensive, both in terms of repair costs and lost production time.
Smart maintenance reduces these expenses by ensuring that maintenance is done proactively.
Improved Safety
By keeping equipment in optimal condition, the risk of accidents caused by machinery failure is significantly reduced.
This promotes a safer working environment for employees.
Implementing Smart Maintenance
Choosing the Right Sensors
The first step in implementing smart maintenance is selecting the appropriate sensors for your equipment.
The choice depends on the type of machinery and the parameters you need to monitor.
Common types of sensors include temperature sensors, vibration sensors, and pressure sensors.
Setting Up Data Collection Systems
Once you have the sensors, set up a system to collect and transmit the data.
This could involve integrating with existing industrial Internet of Things (IIoT) platforms or developing a new system tailored to your needs.
Analyzing the Data
With data collection in place, the next step is data analysis.
Invest in advanced analytics software that can process the data and provide actionable insights.
Machine learning models are particularly effective for predictive maintenance, as they can learn from historical data and improve over time.
Training Maintenance Teams
Your maintenance teams need to be trained to interpret the data and act accordingly.
This might involve learning new software tools or understanding how to respond to the insights generated by the analytics.
Challenges and Solutions
Data Management
One challenge is managing the large volumes of data generated by sensors.
Investing in robust data storage and processing solutions can help ensure smooth operations.
Integration with Existing Systems
Another challenge is integrating smart maintenance systems with existing machinery and processes.
Working with experienced vendors or consulting experts can facilitate a seamless integration.
Initial Investment
While the initial investment in smart maintenance technology might be significant, the long-term benefits in terms of reduced downtime, cost savings, and enhanced equipment lifespan make it worthwhile.
Embracing smart maintenance through condition monitoring and maintenance prediction can revolutionize how manufacturing equipment is maintained.
By proactively addressing potential issues, manufacturers can enjoy improved efficiency, cost savings, and a safer work environment.
So, start exploring smart maintenance solutions today and take a step towards a more productive future.
資料ダウンロード
QCD調達購買管理クラウド「newji」は、調達購買部門で必要なQCD管理全てを備えた、現場特化型兼クラウド型の今世紀最高の購買管理システムとなります。
ユーザー登録
調達購買業務の効率化だけでなく、システムを導入することで、コスト削減や製品・資材のステータス可視化のほか、属人化していた購買情報の共有化による内部不正防止や統制にも役立ちます。
NEWJI DX
製造業に特化したデジタルトランスフォーメーション(DX)の実現を目指す請負開発型のコンサルティングサービスです。AI、iPaaS、および先端の技術を駆使して、製造プロセスの効率化、業務効率化、チームワーク強化、コスト削減、品質向上を実現します。このサービスは、製造業の課題を深く理解し、それに対する最適なデジタルソリューションを提供することで、企業が持続的な成長とイノベーションを達成できるようサポートします。
オンライン講座
製造業、主に購買・調達部門にお勤めの方々に向けた情報を配信しております。
新任の方やベテランの方、管理職を対象とした幅広いコンテンツをご用意しております。
お問い合わせ
コストダウンが利益に直結する術だと理解していても、なかなか前に進めることができない状況。そんな時は、newjiのコストダウン自動化機能で大きく利益貢献しよう!
(Β版非公開)