- お役立ち記事
- Implementing 5S (Sort, Set in Order, Shine, Standardize, Sustain) in Manufacturing
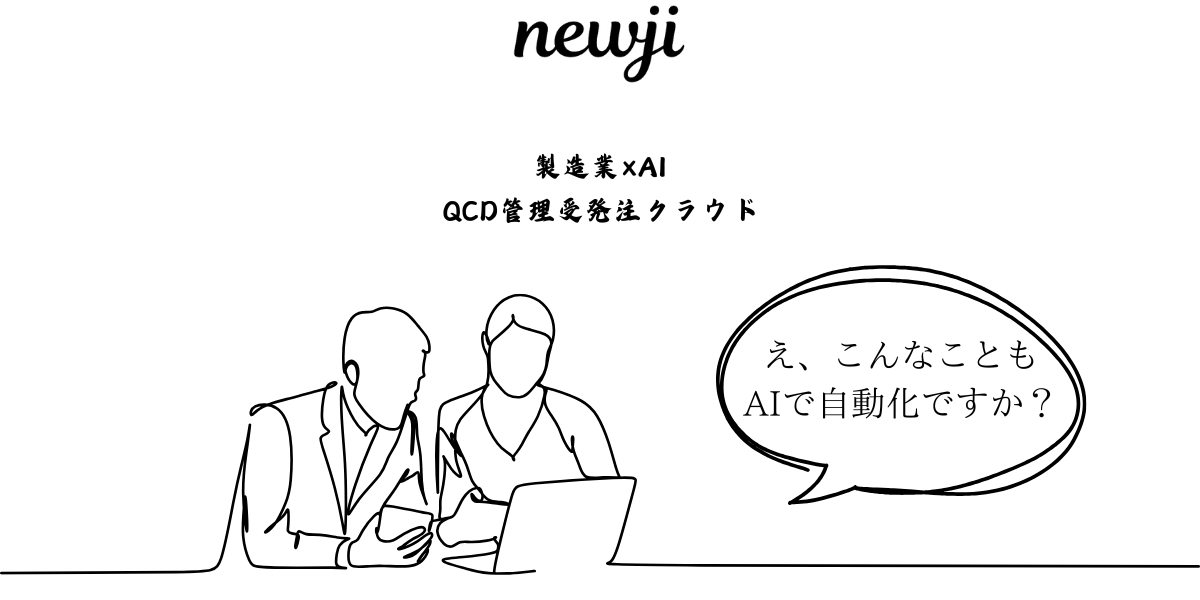
Implementing 5S (Sort, Set in Order, Shine, Standardize, Sustain) in Manufacturing
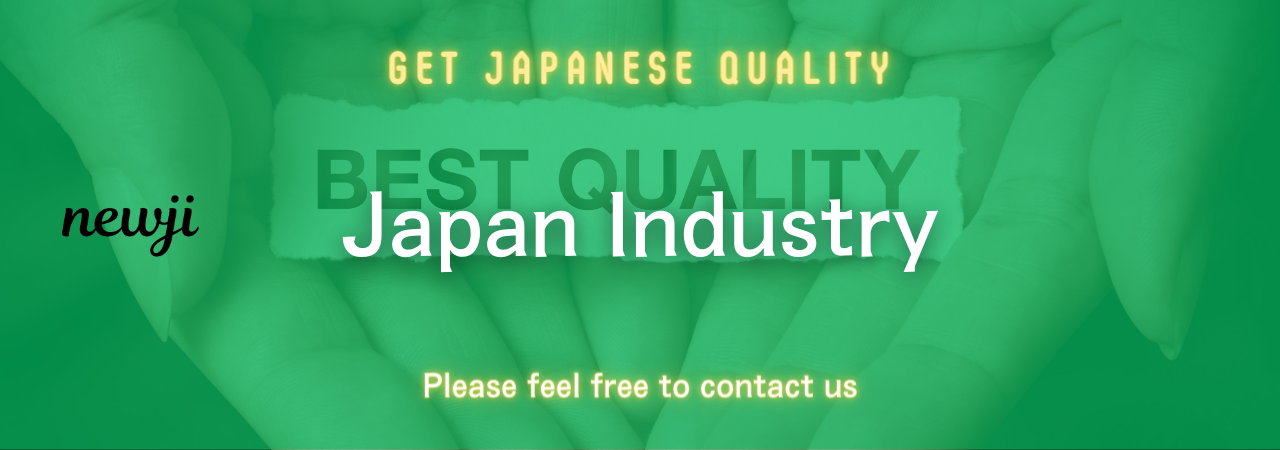
Implementing 5S (Sort, Set in Order, Shine, Standardize, Sustain) in Manufacturing
目次
What is 5S in Manufacturing?
The 5S methodology is a powerful tool used in lean manufacturing to improve workplace efficiency and safety.
It derives its name from five Japanese words that start with the letter “S”: Seiri (Sort), Seiton (Set in Order), Seiso (Shine), Seiketsu (Standardize), and Shitsuke (Sustain).
By following these five steps, your manufacturing process can run more smoothly, reduce waste, and create a more organized workspace.
Sort: Identifying and Removing Unnecessary Items
The first step in the 5S process is *Sort*.
This stage involves going through all the items in the workspace and classifying them as necessary or unnecessary.
Unnecessary items could be outdated tools, unused materials, or defective products.
Removing these items helps free up space and reduce clutter, making it easier to find what you need when you need it.
To implement the *Sort* phase effectively, involve the entire team in identifying what is essential for the job and what is not.
Mark the unnecessary items for disposal, recycling, or relocation.
Set in Order: Organize Your Workspace Efficiently
Once you’ve sorted out what you don’t need, the next step is to *Set in Order*.
This means organizing the remaining items in a way that minimizes wasted time and effort.
Designate specific places for all tools, materials, and products.
Label these places clearly so everyone in the team knows exactly where everything belongs.
Use techniques like color-coding and shadow boards to make it even easier to locate and return items.
By having a specific location for each item, you reduce the time spent searching for things, thus increasing productivity.
Shine: Keep the Workplace Clean and Tidy
The third step in the 5S methodology is *Shine*.
This involves keeping the workspace clean and free from dust, dirt, and clutter.
Regular cleaning should become a part of the daily routine to maintain a high standard of cleanliness.
When the workspace is clean, it’s easier to spot potential issues like leaks or equipment malfunctions.
A clean environment also promotes safety and can boost employee morale.
Set up daily, weekly, or monthly cleaning schedules and assign specific tasks to team members to ensure cleanliness is maintained consistently.
Standardize: Create Standard Operating Procedures
*Standardize* is the fourth step, and it focuses on creating standardized procedures to maintain the first three steps.
This means developing guidelines and routines to ensure that sorting, setting in order, and shining become regular practices.
Standard Operating Procedures (SOPs) should be documented and made easily accessible to all employees.
Training sessions and refresher courses can help reinforce these standards.
By making these practices a part of the company culture, you ensure that the improvements made are sustained over time.
Sustain: Make 5S a Long-Term Commitment
The final step in the 5S process is *Sustain*.
This step is about making a long-term commitment to maintaining the practices implemented in the first four steps.
Ongoing training and regular audits can help ensure that everyone continues to follow the 5S principles.
Encourage employee involvement by creating a sense of ownership and accountability.
Recognize and reward teams that consistently follow the 5S practices.
By doing so, you create a work culture that values organization, cleanliness, and efficiency.
Benefits of Implementing 5S in Manufacturing
Implementing the 5S methodology can bring numerous benefits to your manufacturing process.
One of the most significant advantages is increased efficiency.
When workers can easily find the tools and materials they need, they can complete their tasks more quickly and effectively.
Moreover, a clean and organized workspace reduces the risk of accidents and improves overall safety.
By removing unnecessary items and organizing the workspace, you also free up valuable floor space, making it easier to move around and increasing productivity.
Additionally, the 5S methodology fosters a sense of pride and ownership among employees, which can lead to a more motivated and engaged workforce.
Common Challenges and How to Overcome Them
While the benefits of 5S are clear, implementing it can come with its own set of challenges.
One of the most common challenges is resistance to change.
Employees may be accustomed to their old ways of working and may not see the immediate benefits of the new system.
To overcome this, it’s crucial to involve employees in the process from the beginning and provide adequate training.
Another challenge is maintaining the 5S practices over the long term.
Regular audits and continuous improvement initiatives can help ensure that the 5S principles are adhered to consistently.
Finally, management support is essential for the successful implementation of 5S.
Leaders should lead by example and show their commitment to the methodology.
Conclusion
Implementing the 5S methodology in your manufacturing process can lead to significant improvements in efficiency, safety, and productivity.
By following the five steps—Sort, Set in Order, Shine, Standardize, and Sustain—you can create a more organized and efficient workspace.
While there may be challenges along the way, involving employees and providing continuous support can help ensure the successful implementation of 5S.
In the long run, the 5S methodology can lead to a more motivated and engaged workforce, contributing to the overall success of your manufacturing operations.
So, are you ready to transform your manufacturing process with 5S?
資料ダウンロード
QCD調達購買管理クラウド「newji」は、調達購買部門で必要なQCD管理全てを備えた、現場特化型兼クラウド型の今世紀最高の購買管理システムとなります。
ユーザー登録
調達購買業務の効率化だけでなく、システムを導入することで、コスト削減や製品・資材のステータス可視化のほか、属人化していた購買情報の共有化による内部不正防止や統制にも役立ちます。
NEWJI DX
製造業に特化したデジタルトランスフォーメーション(DX)の実現を目指す請負開発型のコンサルティングサービスです。AI、iPaaS、および先端の技術を駆使して、製造プロセスの効率化、業務効率化、チームワーク強化、コスト削減、品質向上を実現します。このサービスは、製造業の課題を深く理解し、それに対する最適なデジタルソリューションを提供することで、企業が持続的な成長とイノベーションを達成できるようサポートします。
オンライン講座
製造業、主に購買・調達部門にお勤めの方々に向けた情報を配信しております。
新任の方やベテランの方、管理職を対象とした幅広いコンテンツをご用意しております。
お問い合わせ
コストダウンが利益に直結する術だと理解していても、なかなか前に進めることができない状況。そんな時は、newjiのコストダウン自動化機能で大きく利益貢献しよう!
(Β版非公開)