- お役立ち記事
- Implementing PLCs for Automation in Manufacturing
Implementing PLCs for Automation in Manufacturing
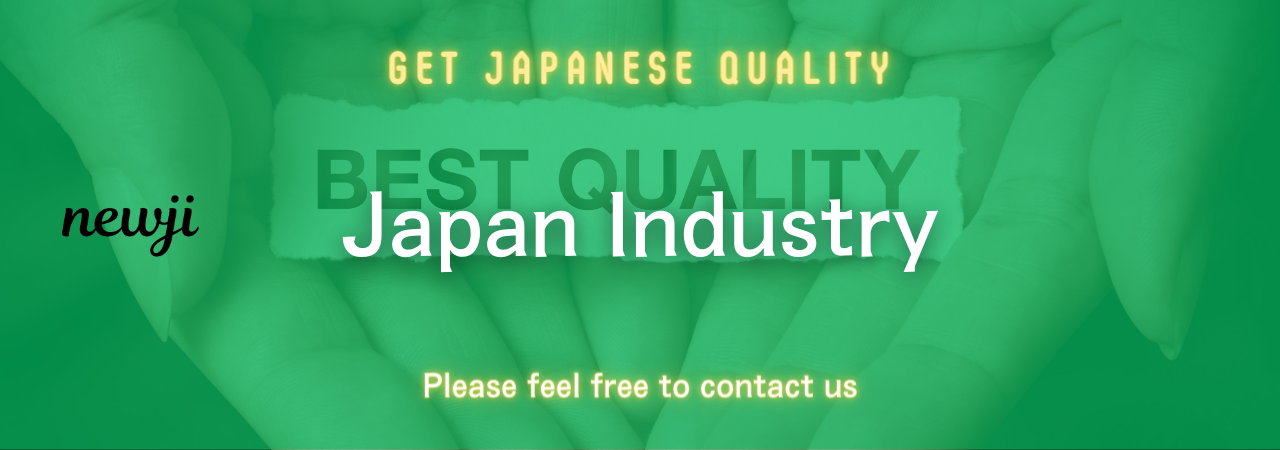
In today’s fast-paced manufacturing world, efficiency and precision are key.
To keep up with this demand, many manufacturers are turning to programmable logic controllers (PLCs) for automation.
PLCs are computer-based systems used to control machinery on factory assembly lines, amusement rides, or even light fixtures.
They play a crucial role in making the manufacturing process more efficient and reliable.
目次
What is a PLC?
A PLC, or Programmable Logic Controller, is a type of digital computer used for automation of electromechanical processes.
Unlike regular computers, PLCs are designed to withstand harsh industrial environments, making them perfect for factory settings.
Their primary function is to monitor inputs from various sensors and devices and then make decisions based on a programmed set of instructions to control outputs.
PLCs are designed to be highly versatile and can be used for a wide variety of applications, making them a popular choice for manufacturing automation.
They can manage tasks like monitoring temperature, controlling robotic arms, and even tracking product movement on an assembly line.
Benefits of Using PLCs in Manufacturing
Increased Efficiency
One of the main advantages of using PLCs in manufacturing is the increase in efficiency they provide.
PLCs can perform tasks much faster and more accurately than human workers.
By automating repetitive and time-consuming tasks, manufacturers can produce more goods in less time while reducing errors.
This leads to higher productivity and lower operating costs.
Improved Quality Control
PLCs help ensure that products are manufactured to the highest quality standards by providing consistent and precise control over the production process.
Their ability to monitor and adjust various parameters in real-time means that any deviations from the desired specifications can be quickly identified and corrected.
This helps to minimize defects and maintain the quality of the final products.
Enhanced Safety
Safety is a key concern in any manufacturing environment.
PLCs can help enhance safety by monitoring and controlling various safety systems.
For example, they can detect when a piece of equipment is malfunctioning and shut it down to prevent accidents.
They can also ensure that machinery operates within safe parameters, reducing the risk of injuries to workers.
How PLCs Work
Understanding how PLCs work is essential for implementing them successfully in a manufacturing setting.
A PLC system consists of three main components: the processor, input/output (I/O) modules, and a programming device.
The Processor
The processor, also known as the central processing unit (CPU), is the brain of the PLC.
It interprets the program instructions and processes data from the input devices.
The processor then sends control signals to the output devices to execute specific actions.
It operates in a continuous loop, constantly checking the inputs and adjusting the outputs as necessary.
Input/Output Modules
Input and output modules are the components that allow the PLC to interact with the external environment.
Input modules receive signals from various sensors and devices, such as temperature sensors, pressure switches, and limit switches.
These signals are then sent to the processor for analysis.
Output modules send control signals from the processor to devices like motors, valves, and lights to perform the desired actions.
Programming Device
Programming the PLC is a crucial step in the implementation process.
A programming device, such as a computer or handheld programmer, is used to write the instructions that the PLC will follow.
These instructions are usually written in a specialized programming language, such as ladder logic, which resembles electrical relay logic diagrams.
Steps to Implement PLCs in Manufacturing
Successfully implementing PLCs in manufacturing requires careful planning and execution.
Here are the essential steps to follow:
1. Assess Your Needs
The first step is to assess your specific needs and determine how PLCs can help improve your manufacturing process.
Identify the tasks and processes that can benefit from automation and create a list of requirements for your PLC system.
Consider factors such as the number of inputs and outputs needed, the complexity of the control tasks, and the environmental conditions the PLC will operate in.
2. Choose the Right PLC
Once you have a clear understanding of your needs, it’s time to choose the right PLC for your application.
There are many different types and models of PLCs available, each with its own set of features and capabilities.
Look for a PLC that meets your requirements in terms of input/output capacity, processing power, and durability.
Also, consider factors such as ease of programming and compatibility with your existing equipment.
3. Develop the Program
With the right PLC selected, you can begin developing the program that will control your manufacturing process.
This involves writing a set of instructions in a programming language supported by your PLC.
It is important to thoroughly test the program in a simulated environment to ensure it performs as expected before deploying it in your actual manufacturing process.
4. Install and Connect the PLC
Next, install the PLC and connect it to the necessary input and output devices.
Ensure that all wiring is done correctly and that the PLC is securely mounted in a location where it is protected from potential hazards.
Follow the manufacturer’s guidelines for installation to avoid any issues.
5. Conduct a System Test
Before fully integrating the PLC into your manufacturing process, conduct a comprehensive system test.
Check all the inputs and outputs to ensure they are functioning correctly and that the PLC is controlling the process as intended.
Make any necessary adjustments to the program and hardware configuration based on the test results.
6. Train Your Staff
Implementing a new PLC system may require training for your staff to ensure they can operate and maintain it effectively.
Provide comprehensive training on how to use the programming tools, troubleshoot common issues, and perform routine maintenance.
This will help minimize downtime and ensure the system runs smoothly.
Conclusion
Implementing PLCs for automation in manufacturing offers numerous benefits, including increased efficiency, improved quality control, and enhanced safety.
By understanding how PLCs work and following a structured implementation process, manufacturers can successfully integrate these powerful tools into their operations.
With the right PLC system in place, manufacturers can achieve greater productivity, maintain high-quality standards, and create a safer work environment.
Make the move towards automation today and unlock the full potential of your manufacturing process.
資料ダウンロード
QCD調達購買管理クラウド「newji」は、調達購買部門で必要なQCD管理全てを備えた、現場特化型兼クラウド型の今世紀最高の購買管理システムとなります。
ユーザー登録
調達購買業務の効率化だけでなく、システムを導入することで、コスト削減や製品・資材のステータス可視化のほか、属人化していた購買情報の共有化による内部不正防止や統制にも役立ちます。
NEWJI DX
製造業に特化したデジタルトランスフォーメーション(DX)の実現を目指す請負開発型のコンサルティングサービスです。AI、iPaaS、および先端の技術を駆使して、製造プロセスの効率化、業務効率化、チームワーク強化、コスト削減、品質向上を実現します。このサービスは、製造業の課題を深く理解し、それに対する最適なデジタルソリューションを提供することで、企業が持続的な成長とイノベーションを達成できるようサポートします。
オンライン講座
製造業、主に購買・調達部門にお勤めの方々に向けた情報を配信しております。
新任の方やベテランの方、管理職を対象とした幅広いコンテンツをご用意しております。
お問い合わせ
コストダウンが利益に直結する術だと理解していても、なかなか前に進めることができない状況。そんな時は、newjiのコストダウン自動化機能で大きく利益貢献しよう!
(Β版非公開)