- お役立ち記事
- Importance and Methods of Deburring: Deburring Processes to Improve Part Finish and Safety
月間76,176名の
製造業ご担当者様が閲覧しています*
*2025年3月31日現在のGoogle Analyticsのデータより
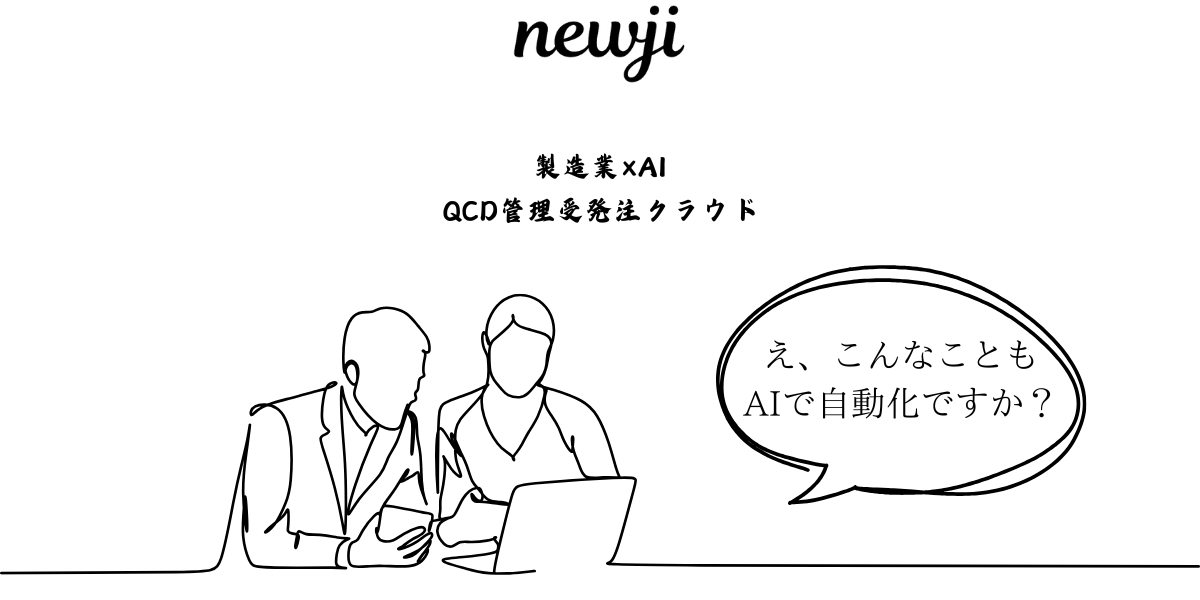
Importance and Methods of Deburring: Deburring Processes to Improve Part Finish and Safety
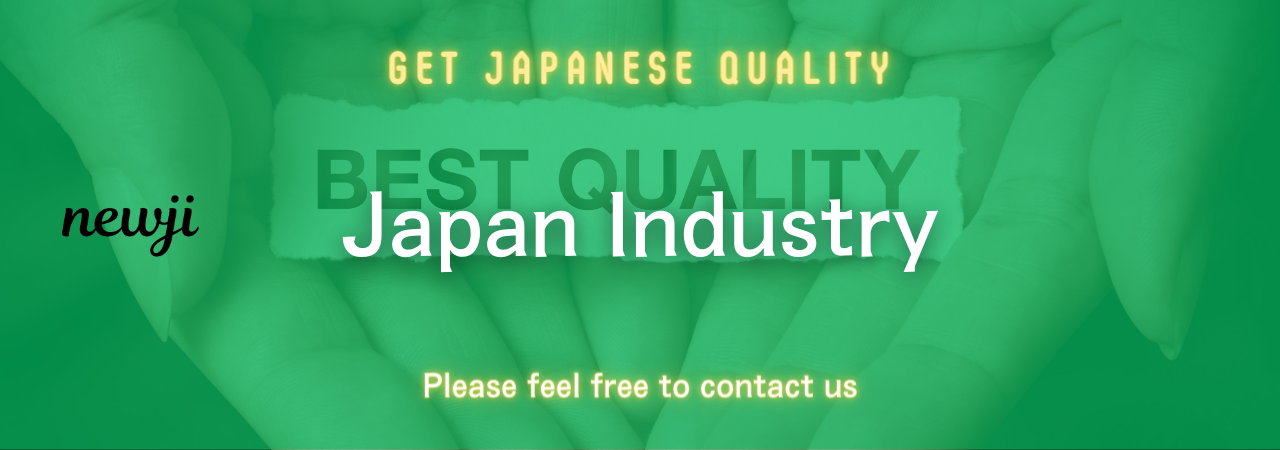
When working on manufacturing processes, the importance of deburring cannot be overstated.
Deburring is the process of removing small imperfections or burrs from the edges of parts or components after they have been machined, cast, or otherwise manufactured.
These tiny, raised edges can affect the functionality and aesthetics of the parts and even pose significant safety risks.
Understanding the importance of deburring and the methods used to achieve it can lead to better quality control, improved safety, and enhanced overall product integrity.
目次
What is Deburring?
Deburring refers to removing unwanted material from the surface of a manufactured part.
These unwanted materials, called burrs, are often sharp and dangerous.
They can result from various machining processes such as drilling, milling, grinding, or turning.
Burrs can be small metal fragments, shavings, or rough edges left on a part from machining operations.
The goal of deburring is to produce a clean, smooth surface that is free from any remaining burrs, making the part safer and more visually appealing.
This process is vital in many industries, including automotive, aerospace, electronics, and medical devices, where precision and safety are paramount.
Why is Deburring Important?
Safety Concerns
Sharp burrs can pose a significant safety hazard.
They can cause injuries like cuts and scrapes to workers handling the parts or end-users.
By removing these burrs, manufacturers can ensure that their products are safe to handle and use.
Improved Functionality
Burrs can interfere with the proper functioning of mechanical parts.
They can cause misalignment, interfere with assembly, or even result in parts failing to fit together correctly.
By removing burrs, manufacturers can ensure that their products function as intended.
Enhanced Aesthetic Appeal
Aesthetics can be essential for customer satisfaction in consumer products.
Rough, jagged edges can make a product look unfinished or of poor quality.
Deburring smoothens these edges, contributing to a more professional and polished final product.
Increased Lifetime of Parts
Burrs can create stress concentrations in a part, which can lead to premature failure.
By eliminating these imperfections, manufacturers can produce more durable components that last longer.
Quality Control
Deburring is often a critical part of the quality control process.
It ensures that each part meets the required specifications and standards, improving the overall consistency and reliability of the products.
Common Deburring Methods
There are several methods used to remove burrs from manufactured parts, each with its advantages and applications.
Manual Deburring
Manual deburring involves using hand tools to remove burrs.
Tools like files, sandpaper, or deburring knives are typically used.
This method is suitable for small-scale operations or situations where precision is crucial.
Although labor-intensive, it allows for detailed and accurate removal of burrs from complex parts.
Mechanical Deburring
Mechanical deburring uses machines to remove burrs.
This method includes techniques like tumbling, vibratory finishing, or abrasive blasting.
Tumbling involves placing parts in a drum with abrasive media and rotating them to smooth the surface.
Vibratory finishing uses a vibrating container to achieve similar results.
Abrasive blasting, on the other hand, uses high-pressure streams of abrasive materials to remove burrs.
Thermal Deburring
Thermal deburring, also known as combustion deburring, uses high-temperature gas to burn away residual material.
Parts are placed in a chamber, and a mixture of gases is ignited to burn off the burrs.
This method is highly effective for removing burrs from hard-to-reach areas, but it can be costly and is typically used for high-value parts.
Electrochemical Deburring
Electrochemical deburring utilizes electrical energy to remove burrs.
Parts are submerged in an electrolyte solution and subjected to an electrical current, which dissolves the unwanted material.
This method is particularly suitable for burrs located in difficult-to-reach areas and provides a high degree of precision.
Ultrasonic Deburring
Ultrasonic deburring uses high-frequency sound waves to remove burrs.
Parts are immersed in a liquid, and ultrasonic vibrations create microscopic bubbles that scrub the parts’ surface.
This technique is non-abrasive and is often used for delicate or intricate components.
How to Choose the Right Deburring Method
Selecting the appropriate deburring method depends on various factors, including the material, shape, size, and application of the parts.
Material
The type of material being deburred plays a significant role in determining the appropriate method.
For instance, materials like steel may require more robust deburring techniques like abrasive blasting, while softer materials like aluminum may be suitable for manual or mechanical deburring.
Part Complexity
The complexity of the part’s shape and design also influences the choice of deburring method.
Intricate parts with hard-to-reach areas may benefit from thermal or electrochemical deburring, whereas simpler shapes might be effectively deburred using manual or mechanical methods.
Production Volume
For high-volume production, automated deburring methods like mechanical or thermal deburring are more efficient and cost-effective.
In contrast, low-volume or custom parts might be better suited for manual deburring due to its flexibility.
Tolerances and Specifications
Parts with tight tolerances or specific surface finish requirements may necessitate more precise deburring methods such as ultrasonic or electrochemical deburring.
Ensuring that the chosen method meets these criteria is essential for maintaining quality control.
Conclusion
In the manufacturing world, deburring is an essential process that enhances the safety, functionality, aesthetics, and longevity of parts.
With several deburring methods available, choosing the right technique depends on the material, complexity, production volume, and specific requirements of the parts.
Manufacturers can achieve better quality control and produce safer, more reliable products by removing burrs effectively.
Understanding the importance and methods of deburring allows industries to maintain a high standard of workmanship, ensuring that each part meets the demands of today’s competitive market.
資料ダウンロード
QCD管理受発注クラウド「newji」は、受発注部門で必要なQCD管理全てを備えた、現場特化型兼クラウド型の今世紀最高の受発注管理システムとなります。
ユーザー登録
受発注業務の効率化だけでなく、システムを導入することで、コスト削減や製品・資材のステータス可視化のほか、属人化していた受発注情報の共有化による内部不正防止や統制にも役立ちます。
NEWJI DX
製造業に特化したデジタルトランスフォーメーション(DX)の実現を目指す請負開発型のコンサルティングサービスです。AI、iPaaS、および先端の技術を駆使して、製造プロセスの効率化、業務効率化、チームワーク強化、コスト削減、品質向上を実現します。このサービスは、製造業の課題を深く理解し、それに対する最適なデジタルソリューションを提供することで、企業が持続的な成長とイノベーションを達成できるようサポートします。
製造業ニュース解説
製造業、主に購買・調達部門にお勤めの方々に向けた情報を配信しております。
新任の方やベテランの方、管理職を対象とした幅広いコンテンツをご用意しております。
お問い合わせ
コストダウンが利益に直結する術だと理解していても、なかなか前に進めることができない状況。そんな時は、newjiのコストダウン自動化機能で大きく利益貢献しよう!
(β版非公開)