- お役立ち記事
- Importance of Supplier Cooperation for Six Sigma Implementation
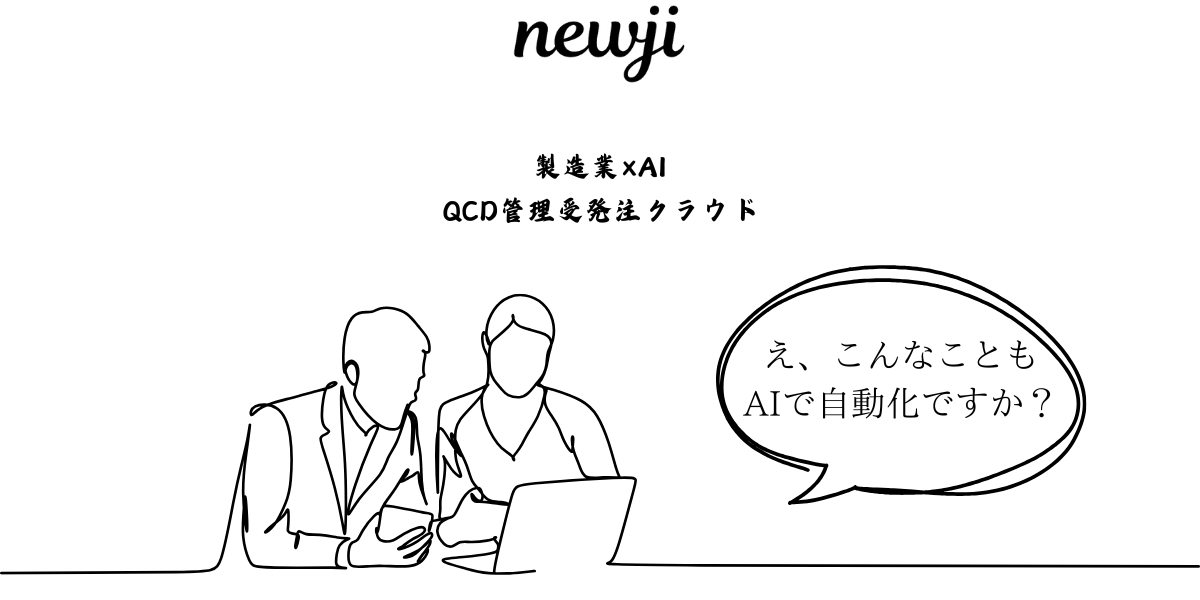
Importance of Supplier Cooperation for Six Sigma Implementation
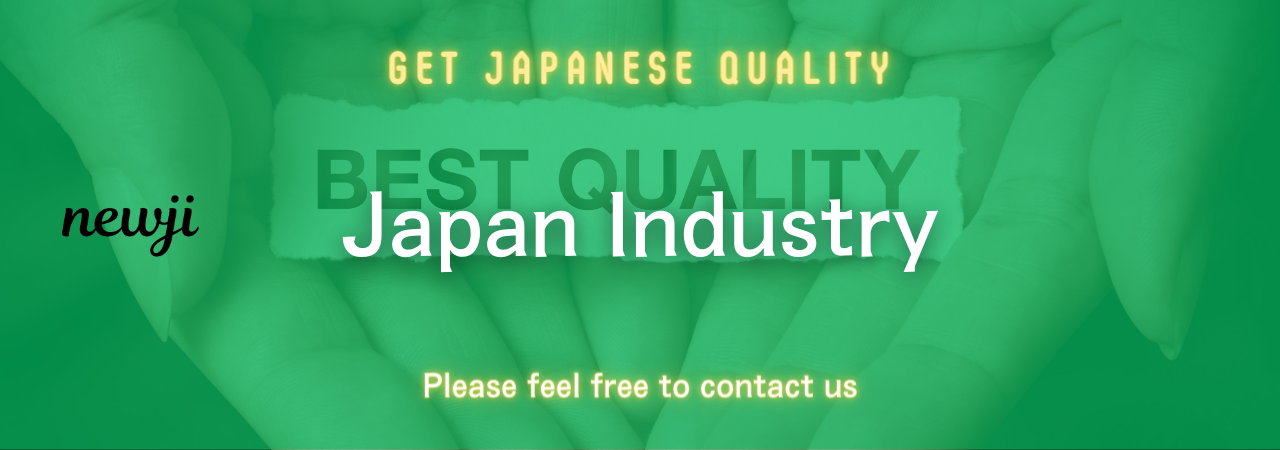
Implementing Six Sigma within an organization is no small feat. It requires meticulous planning, robust methods, and a deep commitment to quality control.
While the focus is often on internal processes, the role of suppliers should never be overlooked. Supplier cooperation is a cornerstone for successful Six Sigma implementation, contributing significantly to the overall quality and efficiency of the process.
Let’s delve into why supplier cooperation is crucial and how businesses can foster these essential partnerships.
目次
The Role of Suppliers in Six Sigma
Suppliers play a pivotal role in the supply chain. They provide the raw materials, components, and services that organizations need to function. In a Six Sigma framework, the quality of these supplies directly impacts the quality of the final product.
Poorly sourced materials can derail even the best Six Sigma initiatives, causing defects, inefficiencies, and customer dissatisfaction.
Hence, suppliers must be aligned with the company’s Six Sigma goals to ensure seamless implementation and consistent quality.
Quality Control and Consistency
Six Sigma is all about reducing variation and ensuring consistency. This principle extends beyond internal processes to include supplier inputs.
When suppliers adhere to Six Sigma principles, they provide consistent, high-quality materials or services. This uniformity helps the organization maintain its quality standards, minimize defects, and reduce the need for rework.
By working closely with suppliers, organizations can ensure that the supply chain upholds the same level of rigor as their internal operations.
Fostering Collaborative Relationships
Building a partnership with suppliers that supports Six Sigma starts with fostering collaborative relationships. This involves open communication, mutual trust, and shared objectives.
When suppliers understand an organization’s Six Sigma goals, they are more likely to align their processes and quality standards to meet these expectations.
Engaging in Continuous Improvement
Continuous improvement is a core tenet of Six Sigma. Organizations should encourage suppliers to adopt this mindset by involving them in Six Sigma training and development programs.
Collaborative efforts like joint workshops, regular feedback sessions, and performance evaluations can lead to shared learning and improvement.
This collaborative approach ensures that both parties are committed to reducing defects and enhancing quality over time.
Setting Clear Expectations
To achieve successful supplier cooperation, companies need to set clear expectations regarding quality standards and performance metrics.
These expectations should be communicated explicitly through detailed contracts, service level agreements (SLAs), and regular performance reviews.
By defining what constitutes acceptable quality and performance levels, organizations can hold suppliers accountable and foster a culture of excellence.
Implementing Supplier Audits
Periodic supplier audits are crucial for ensuring compliance with Six Sigma standards. These audits help in assessing the supplier’s processes, quality controls, and overall alignment with the organization’s objectives.
Regularly scheduled audits create an environment of accountability and continuous improvement. They also provide valuable insights into areas where suppliers may need additional support or training.
Leveraging Technology for Better Integration
Technology plays a vital role in integrating suppliers into an organization’s Six Sigma framework. Advanced tools and software can streamline communication, enhance data sharing, and improve process transparency.
For instance, integrated supply chain management systems can provide real-time updates on inventory levels, order statuses, and quality metrics.
Such systems ensure that both the organization and its suppliers have access to accurate, up-to-date information, facilitating proactive problem-solving and decision-making.
Utilizing Data Analytics
Data analytics can provide deep insights into supplier performance and quality trends. By leveraging data, organizations can identify patterns, anticipate issues, and implement corrective actions swiftly.
Predictive analytics, for example, can forecast potential supply chain disruptions, allowing companies to take preventive measures.
This data-driven approach enhances collaboration and ensures that the supply chain contributes positively to the Six Sigma goals.
Building Long-term Partnerships
The relationship between an organization and its suppliers should be seen as a long-term partnership rather than a transactional interaction. Long-term partnerships foster deeper understanding, trust, and mutual commitment to quality.
Incentivizing Performance
Organizations can incentivize suppliers to meet or exceed Six Sigma standards by offering performance-based incentives. These could include financial rewards, extended contracts, or preferred supplier status.
Recognizing and rewarding suppliers for their contributions to quality encourages them to maintain high standards and continue improving their processes.
Conclusion
Leveraging supplier cooperation for Six Sigma implementation is not just beneficial; it’s essential. Suppliers are an integral part of the supply chain, and their alignment with Six Sigma principles ensures consistent quality and efficiency.
Organizations that invest in building strong, collaborative relationships with their suppliers are better positioned to achieve their Six Sigma goals.
By setting clear expectations, fostering continuous improvement, leveraging technology, and building long-term partnerships, companies can create a supply chain that is resilient, efficient, and committed to excellence.
資料ダウンロード
QCD調達購買管理クラウド「newji」は、調達購買部門で必要なQCD管理全てを備えた、現場特化型兼クラウド型の今世紀最高の購買管理システムとなります。
ユーザー登録
調達購買業務の効率化だけでなく、システムを導入することで、コスト削減や製品・資材のステータス可視化のほか、属人化していた購買情報の共有化による内部不正防止や統制にも役立ちます。
NEWJI DX
製造業に特化したデジタルトランスフォーメーション(DX)の実現を目指す請負開発型のコンサルティングサービスです。AI、iPaaS、および先端の技術を駆使して、製造プロセスの効率化、業務効率化、チームワーク強化、コスト削減、品質向上を実現します。このサービスは、製造業の課題を深く理解し、それに対する最適なデジタルソリューションを提供することで、企業が持続的な成長とイノベーションを達成できるようサポートします。
オンライン講座
製造業、主に購買・調達部門にお勤めの方々に向けた情報を配信しております。
新任の方やベテランの方、管理職を対象とした幅広いコンテンツをご用意しております。
お問い合わせ
コストダウンが利益に直結する術だと理解していても、なかなか前に進めることができない状況。そんな時は、newjiのコストダウン自動化機能で大きく利益貢献しよう!
(Β版非公開)