- お役立ち記事
- Importance of supply chain quality control in manufacturing quality assurance and how to put it into practice
Importance of supply chain quality control in manufacturing quality assurance and how to put it into practice
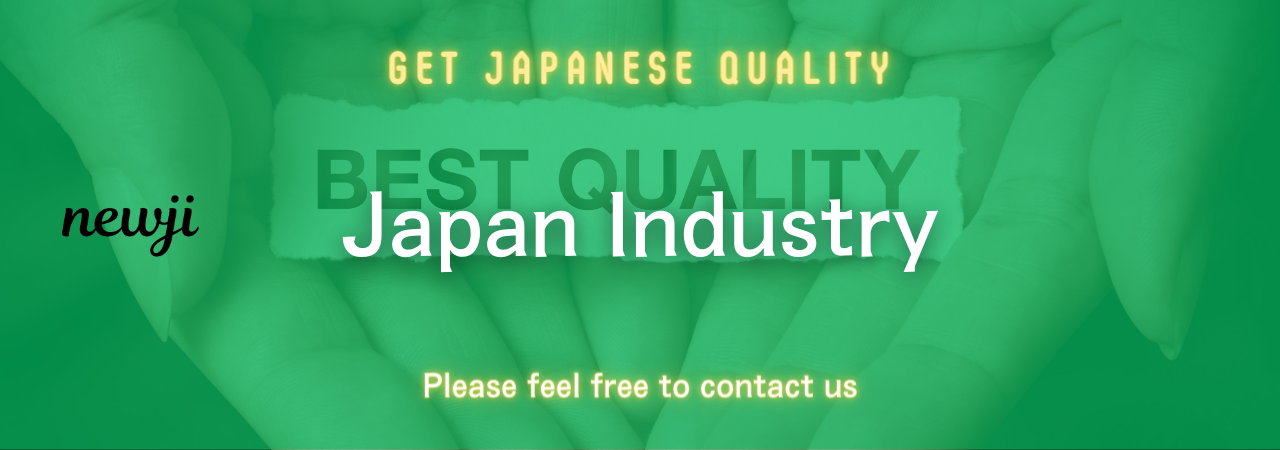
In today’s competitive market, the importance of supply chain quality control in manufacturing quality assurance cannot be overstated. Even the best-designed products can fail if the components sourced from suppliers are of poor quality. It’s essential to ensure that every part of the supply chain operates in harmony to produce the best possible products. This article will explore why supply chain quality control is crucial and how manufacturers can effectively implement it.
目次
What is Supply Chain Quality Control?
Supply chain quality control involves monitoring and managing the quality of products produced throughout the entire supply chain, from raw materials to finished goods. By maintaining high standards at every stage of production, manufacturers can ensure a consistent level of quality across their products.
Why Supply Chain Quality Control Matters
1. Consistency:Consistency is key in manufacturing. When each component of a product meets high standards, the final product is more likely to achieve consistent quality. Inconsistent components can lead to product failures, warranty claims, and customer dissatisfaction.
2. Cost Reduction:Poor quality control can result in wasted materials, production delays, and costly recalls. By implementing rigorous quality control measures, manufacturers can minimize these risks, streamline operations, and optimize costs.
3. Regulatory Compliance: Many industries are subject to stringent regulations regarding product quality and safety. Effective quality control ensures that all products meet these standards, reducing the risk of legal issues and ensuring customer safety.
4. Brand Reputation:High-quality products build a strong brand reputation, leading to customer loyalty and increased market share. On the contrary, a single defective product can significantly harm a brand’s image.
5. Supplier Relationships:Building strong relationships with suppliers who meet quality standards ensures a reliable supply chain. This mutual trust can lead to long-term partnerships and better negotiation terms.
How to Implement Supply Chain Quality Control
1. Identify Critical Control Points: The first step in implementing quality control is to identify critical points in the supply chain where errors are most likely to occur. These points can vary depending on the industry and product but typically include raw material sourcing, manufacturing processes, and final product assembly.
2. Set Quality Standards: Establishing clear quality standards is essential. These standards should be communicated to all suppliers and include specifications for materials, manufacturing processes, and finished products. Quality standards can be based on industry regulations, customer requirements, and company policies.
3. Supplier Audits: Regularly auditing suppliers ensures they adhere to quality standards. Audits can include on-site inspections, reviewing supplier documentation, and testing sample products. This process helps identify potential issues before they impact the final product.
4. Use Technology: Leveraging technology can streamline quality control processes. For example, implementing a robust Enterprise Resource Planning (ERP) system can provide real-time data on supplier performance, inventory levels, and production metrics. Additionally, quality management software can help track and analyze data, making it easier to identify trends and improvement areas.
5. Train Employees:Quality control is a team effort, and every employee must understand their role in maintaining quality standards. This includes training on quality control procedures, proper use of equipment, and recognizing potential quality issues. Regular training sessions can keep employees updated on best practices and industry standards.
6. Implement Statistical Process Control (SPC):SPC involves using statistical methods to monitor and control manufacturing processes. By analyzing data from production processes, manufacturers can identify variations and take corrective actions before issues arise. SPC tools like control charts and process capability analysis can help improve process stability and product quality.
7. Focus on Continuous Improvement: Quality control is not a one-time effort but a continuous process. Regularly reviewing quality performance, identifying areas for improvement, and implementing corrective actions is crucial for maintaining high standards. Techniques like Six Sigma and Lean Manufacturing can help identify inefficiencies and enhance quality.
8. Develop a Robust Supplier Management Program: Building strong relationships with suppliers is vital for effective quality control. This includes clear communication of quality standards, regular interactions with suppliers, and involving them in quality improvement initiatives. A robust supplier management program can ensure suppliers are aligned with the company’s quality goals.
9. Implement a Quality Control Team: Establishing a dedicated quality control team can help ensure rigorous adherence to quality standards. The team can conduct regular inspections, audits, and quality tests, providing an additional layer of oversight.
10. Monitor Customer Feedback: Customer feedback is a valuable source of information regarding product quality. Regularly monitoring reviews, complaints, and returns can provide insights into potential quality issues. Addressing these concerns promptly can improve customer satisfaction and product quality.
Case Study: Toyota’s Quality Control Approach
Toyota is renowned for its commitment to quality control. One key aspect of Toyota’s approach is its Supplier Partnership model, emphasizing long-term relationships and collaboration with suppliers. By involving suppliers in the quality control process and providing them with training and support, Toyota ensures consistency and high standards throughout its supply chain.
Toyota also uses Just-In-Time (JIT) manufacturing, which focuses on reducing waste and improving efficiency. This method ensures that components are produced and delivered exactly when needed, reducing inventory costs and potential quality issues.
Furthermore, Toyota’s culture of continuous improvement, known as Kaizen, encourages employees at all levels to identify and address quality issues. This proactive approach has helped Toyota maintain its reputation for producing reliable, high-quality vehicles.
The importance of supply chain quality control in manufacturing quality assurance cannot be overlooked. By implementing rigorous quality control measures, manufacturers can ensure consistent product quality, reduce costs, comply with regulations, and build strong supplier relationships. These efforts can lead to a stronger brand reputation, increased customer satisfaction, and a competitive edge in the market.
資料ダウンロード
QCD調達購買管理クラウド「newji」は、調達購買部門で必要なQCD管理全てを備えた、現場特化型兼クラウド型の今世紀最高の購買管理システムとなります。
ユーザー登録
調達購買業務の効率化だけでなく、システムを導入することで、コスト削減や製品・資材のステータス可視化のほか、属人化していた購買情報の共有化による内部不正防止や統制にも役立ちます。
NEWJI DX
製造業に特化したデジタルトランスフォーメーション(DX)の実現を目指す請負開発型のコンサルティングサービスです。AI、iPaaS、および先端の技術を駆使して、製造プロセスの効率化、業務効率化、チームワーク強化、コスト削減、品質向上を実現します。このサービスは、製造業の課題を深く理解し、それに対する最適なデジタルソリューションを提供することで、企業が持続的な成長とイノベーションを達成できるようサポートします。
オンライン講座
製造業、主に購買・調達部門にお勤めの方々に向けた情報を配信しております。
新任の方やベテランの方、管理職を対象とした幅広いコンテンツをご用意しております。
お問い合わせ
コストダウンが利益に直結する術だと理解していても、なかなか前に進めることができない状況。そんな時は、newjiのコストダウン自動化機能で大きく利益貢献しよう!
(Β版非公開)