- お役立ち記事
- Improved Heat Dissipation Efficiency by Porous Mold Design in Injection Molding
月間76,176名の
製造業ご担当者様が閲覧しています*
*2025年3月31日現在のGoogle Analyticsのデータより
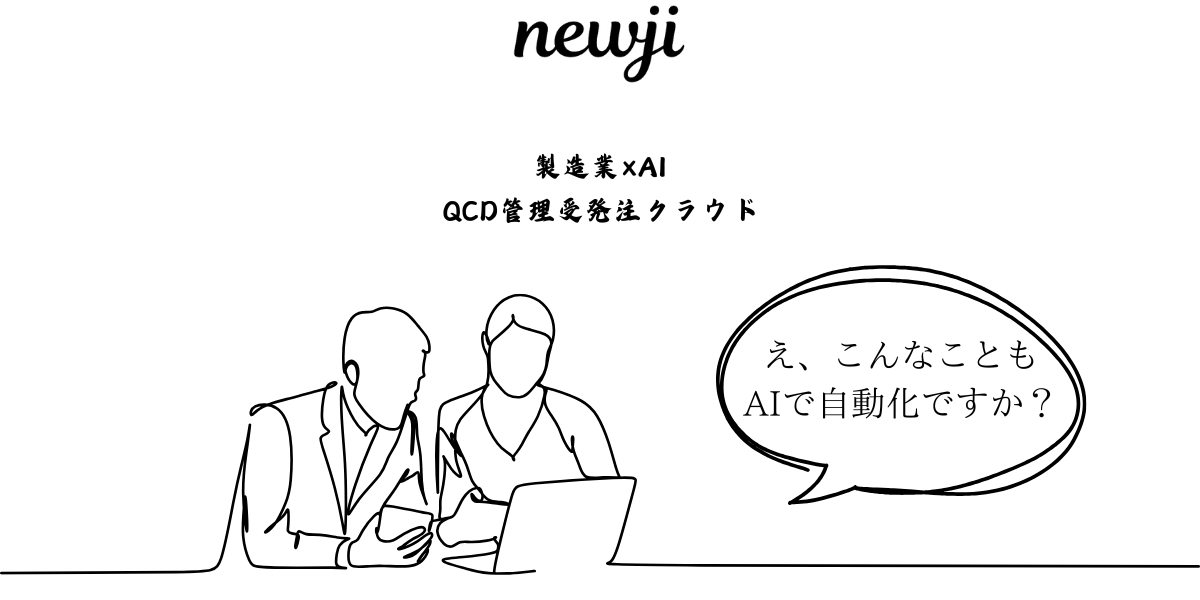
Improved Heat Dissipation Efficiency by Porous Mold Design in Injection Molding
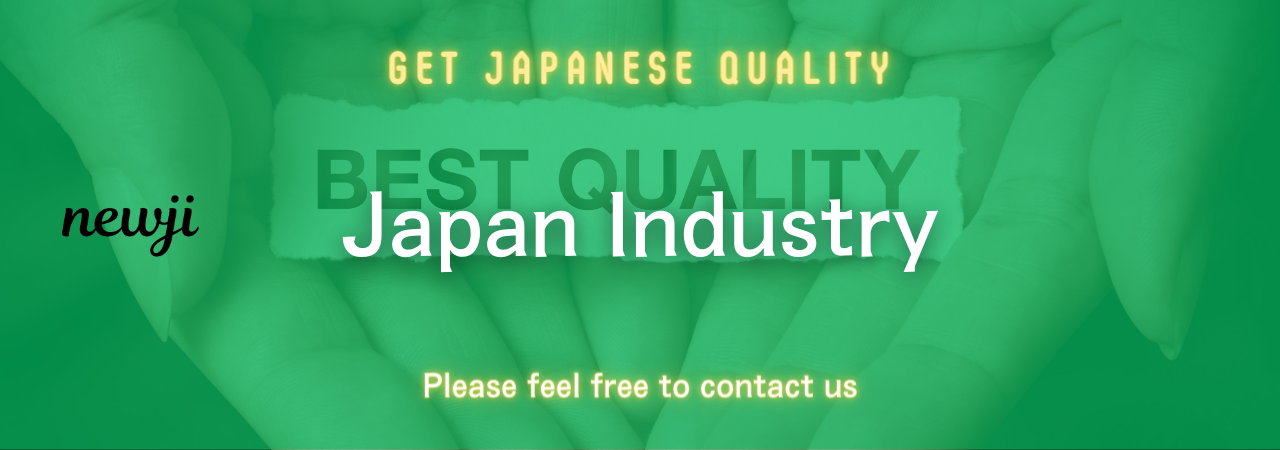
Injection molding is a popular manufacturing process used to create a wide variety of items, ranging from small plastic parts to entire car body panels.
One critical aspect of injection molding that can significantly influence the final product’s quality is heat dissipation.
Effective heat dissipation ensures that the molded part will have minimal defects, a smooth surface, and precise dimensions.
One innovative technique that has been gaining attention for improving heat dissipation is the use of porous mold designs.
目次
The Basics of Injection Molding
Before diving into porous mold designs, it’s essential to understand the fundamentals of injection molding.
In this process, molten plastic is injected into a mold, which is then cooled to allow the plastic to solidify.
Once it has cooled sufficiently, the mold is opened, and the final part is ejected.
Heat dissipation plays a crucial role during this cooling phase.
If the heat is not removed efficiently, it can lead to various problems such as warping, sink marks, and prolonged cycle times.
Why Heat Dissipation Matters
During injection molding, the mold’s ability to remove heat quickly and evenly is critical.
Uneven cooling can result in surface defects and structural weaknesses in the final product.
Furthermore, inefficient cooling can extend the cycle time for each part, reducing overall production efficiency.
Nevertheless, traditional molds often struggle with removing heat uniformly.
This is because materials like steel and aluminum, typically used for molds, have limited thermal conductivity.
The Concept of Porous Mold Design
Porous molds differ from traditional molds because they incorporate tiny holes or channels throughout the mold material.
These pores are designed to allow for greater airflow or fluid movement, thus significantly enhancing heat dissipation.
Materials traditionally used in porous molds include metals like sintered steel or specially engineered ceramics.
These materials undergo a manufacturing process that introduces micropores into the material, resulting in improved thermal properties.
How Porous Molds Improve Heat Dissipation
One of the main advantages of porous molds is their ability to distribute cooling more uniformly.
When the mold is porous, coolant can flow more freely through the material, reaching areas that would otherwise cool more slowly in a traditional mold.
This results in a more even temperature distribution across the mold surface and inside the mold cavities.
Moreover, porous molds can often utilize a larger surface area for heat exchange.
This is because the tiny pores increase the surface area within the mold, providing more opportunity for the coolant to absorb heat.
As a consequence, the overall heat removal process becomes more efficient.
Benefits of Improved Heat Dissipation
Enhanced heat dissipation brings numerous benefits to the injection molding process.
First, it can reduce cycles’ time significantly.
With efficient cooling, parts can solidify faster, allowing for quicker mold ejection and thus increasing production speeds.
Second, improved heat dissipation can considerably reduce defects.
Uniform cooling minimizes the risks of warping and shrinkage, resulting in higher-quality parts.
This means fewer rejects and rework, saving both time and resources.
Lastly, a more efficient cooling system often means that the mold’s lifespan is extended.
Since the mold doesn’t have to bear extreme temperature gradients, it is less likely to undergo thermal strain or fatigue, thereby lasting longer.
Case Studies and Real-World Applications
Real-world applications of porous mold designs have shown promising results.
For example, in the automotive industry, porous molds have been used to manufacture complex components with reduced cycle times and increased part consistency.
In electronics manufacturing, where precision is crucial, porous molds have demonstrated the ability to produce intricate parts with minimal defects and faster production rates.
These case studies underscore the significant impact that improved heat dissipation can have on various industries.
Challenges and Considerations
While porous mold designs offer numerous advantages, they are not without challenges.
One major consideration is the initial cost.
Producing porous molds is generally more expensive than traditional molds due to specialized materials and manufacturing processes.
However, the long-term savings in terms of reduced cycle times, fewer defects, and extended mold life often justify the initial investment.
Another challenge is maintenance.
Porous molds may require more frequent cleaning to prevent clogging of the pores, especially when using cooling fluids.
Regular maintenance is essential to ensure that the pores remain open and effective for optimal cooling.
Future Prospects
As technology advances, the prospects for porous mold designs continue to improve.
Innovations in materials science may lead to the development of new materials that offer even better thermal conductivity and durability.
Additionally, advancements in manufacturing techniques may make porous mold production more cost-effective and accessible to a broader range of industries.
Moreover, integrating smart technologies such as sensors and IoT devices into porous molds could provide real-time data on temperature and cooling efficiency.
This would allow for dynamic adjustments and further optimization of the injection molding process.
In summary, the use of porous mold designs in injection molding represents a significant step forward in improving heat dissipation efficiency.
While challenges remain, the benefits of quicker cycle times, higher part quality, and extended mold lifespan make it a worthwhile investment for many manufacturing processes.
As technology continues to evolve, the potential for even greater efficiencies and applications of porous molds is immense.
資料ダウンロード
QCD管理受発注クラウド「newji」は、受発注部門で必要なQCD管理全てを備えた、現場特化型兼クラウド型の今世紀最高の受発注管理システムとなります。
ユーザー登録
受発注業務の効率化だけでなく、システムを導入することで、コスト削減や製品・資材のステータス可視化のほか、属人化していた受発注情報の共有化による内部不正防止や統制にも役立ちます。
NEWJI DX
製造業に特化したデジタルトランスフォーメーション(DX)の実現を目指す請負開発型のコンサルティングサービスです。AI、iPaaS、および先端の技術を駆使して、製造プロセスの効率化、業務効率化、チームワーク強化、コスト削減、品質向上を実現します。このサービスは、製造業の課題を深く理解し、それに対する最適なデジタルソリューションを提供することで、企業が持続的な成長とイノベーションを達成できるようサポートします。
製造業ニュース解説
製造業、主に購買・調達部門にお勤めの方々に向けた情報を配信しております。
新任の方やベテランの方、管理職を対象とした幅広いコンテンツをご用意しております。
お問い合わせ
コストダウンが利益に直結する術だと理解していても、なかなか前に進めることができない状況。そんな時は、newjiのコストダウン自動化機能で大きく利益貢献しよう!
(β版非公開)