- お役立ち記事
- Improvement and management of material costs and processing costs
月間77,185名の
製造業ご担当者様が閲覧しています*
*2025年2月28日現在のGoogle Analyticsのデータより
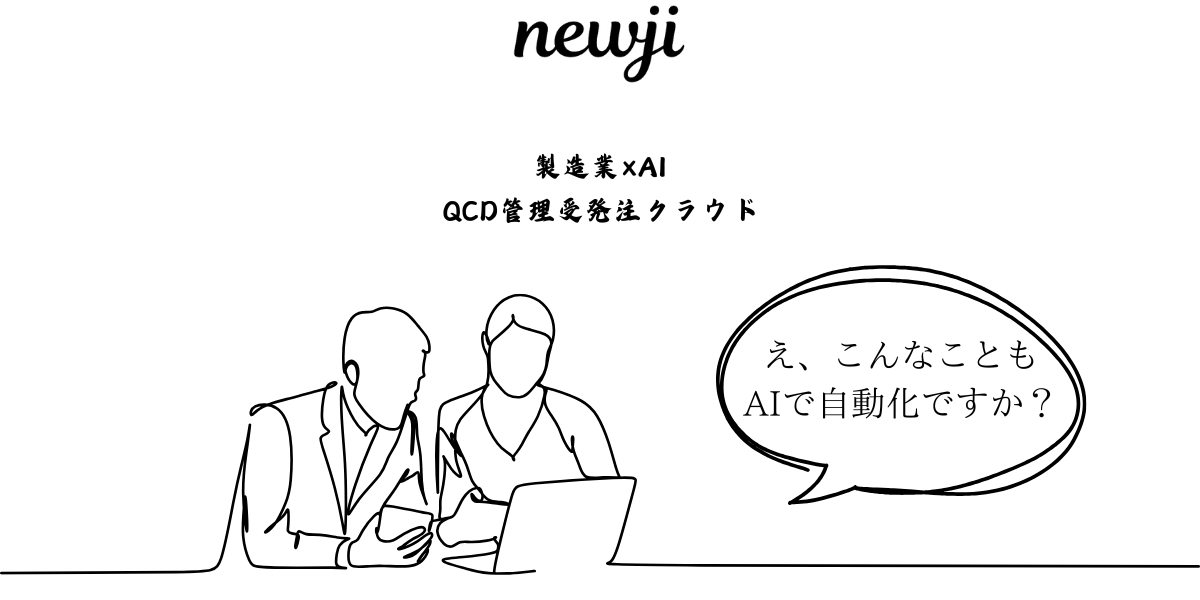
Improvement and management of material costs and processing costs
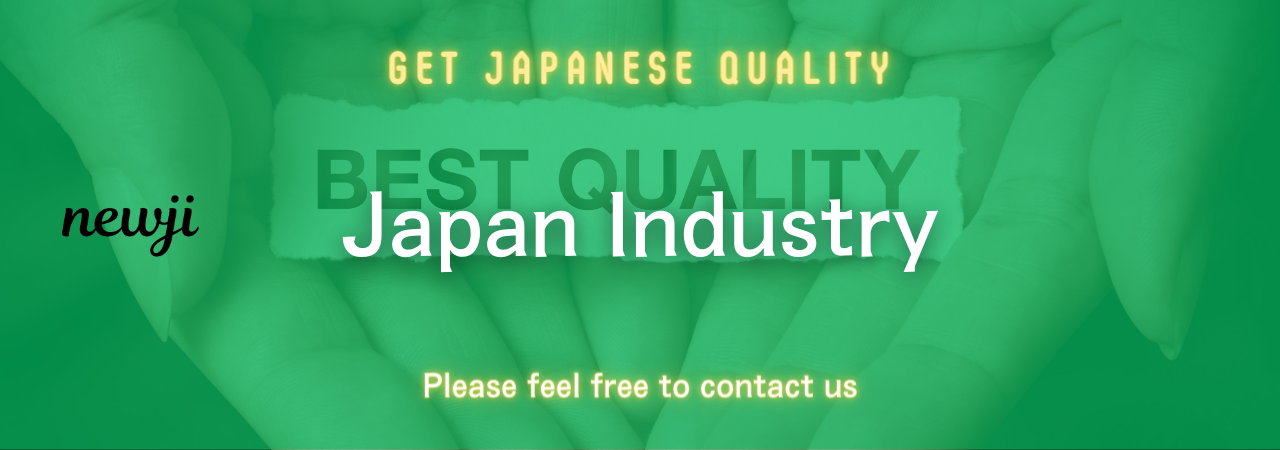
目次
Understanding Material Costs
Managing material costs is a crucial aspect of business operations, especially for manufacturing companies.
Material costs refer to the expenses incurred to acquire raw materials necessary for production.
These costs play a significant role in determining the overall expenses of a company.
Effective management of material costs can lead to improved profitability and competitive pricing.
There are different types of material costs, including direct and indirect costs.
Direct material costs are those directly related to the production of goods.
These include raw materials used in the manufacturing process.
Indirect material costs, on the other hand, are more ancillary expenses.
These might include tools, lubricants, and maintenance materials that support production.
Factors Influencing Material Costs
Several factors can influence material costs.
Supply and demand are significant determinants.
When demand for a particular raw material increases, prices often rise, impacting production costs.
Another factor is the geographical location of the supplier.
Transporting materials over long distances can add to the cost, making it essential for companies to find local suppliers when possible.
Additionally, currency exchange rates can affect the cost of importing materials from other countries.
Quality is another important factor.
Higher-quality materials may cost more, but they can lead to better products and fewer defects.
This can save money in the long run, despite a higher initial outlay.
Strategies for Managing Material Costs
To effectively manage material costs, businesses can adopt several strategies.
One such strategy is negotiating better terms with suppliers.
Building strong relationships with suppliers can lead to favorable pricing and discounts for bulk purchases.
Implementing a just-in-time inventory system can also help control material costs.
This approach ensures that materials are ordered and received as they are needed.
This reduces the need to store excess inventory and lowers storage expenses.
Investing in technology can streamline operations and improve material cost management.
Using software systems to track material usage and inventory levels can prevent overstocking and waste.
Another effective strategy is to evaluate and optimize the supply chain.
Identifying and eliminating bottlenecks and inefficiencies can lead to significant cost savings.
Understanding Processing Costs
Processing costs involve all the expenses related to transforming raw materials into finished products.
These costs can include labor, equipment maintenance, energy consumption, and overhead expenses.
Managing processing costs is essential to ensure the profitability of production activities.
Like material costs, processing costs can significantly affect a company’s bottom line.
Firms must understand and manage these costs effectively to remain competitive.
Factors Influencing Processing Costs
Labor costs are a major component of processing costs.
Skilled workers may demand higher wages, but their expertise can lead to higher quality and efficiency.
Conversely, unskilled or semi-skilled labor may reduce costs but could increase error rates and waste.
Technology plays a crucial role in processing costs.
Automation and advanced manufacturing technologies can decrease reliance on labor and increase production efficiency.
Energy costs also impact processing expenses.
The cost of electricity and other fuels can vary, affecting the total cost of production.
Strategies for Managing Processing Costs
One approach to managing processing costs is to invest in employee training.
Trained employees tend to be more efficient and make fewer mistakes.
This can lead to lower costs and improved product quality.
Regular maintenance of equipment is also vital.
Well-maintained machinery operates more efficiently, reducing downtime and preventing costly breakdowns.
Energy efficiency initiatives can reduce processing costs significantly.
For example, introducing energy-conserving practices or investing in energy-efficient equipment can decrease utility expenses.
Another effective strategy is to implement lean manufacturing principles.
This approach focuses on minimizing waste and improving workflow efficiency.
The Importance of Collaboration and Communication
Collaboration and communication within the organization are essential for optimizing material and processing costs.
Departments must work together to identify areas of waste and potential cost-saving opportunities.
Encouraging open communication between departments, such as procurement, production, and finance, can lead to more informed decisions.
By sharing information, companies can create more accurate forecasts and budgets, ultimately leading to better cost management.
Leveraging Technology for Better Cost Management
The use of technology can greatly enhance the management of material and processing costs.
Integrated software solutions and analytics can provide real-time data and insights.
This enables informed decision-making and proactive cost management.
Through automation, companies can streamline processes, reduce manual errors, and increase speed.
This results in cost reductions and improved operational efficiency.
Data analysis tools can help identify trends, forecast demand, and optimize inventory management.
These capabilities empower businesses to respond quickly to changes in market conditions and adjust their strategies accordingly.
Conclusion
Improving and managing material and processing costs is vital for a business’s sustainability and profitability.
By understanding the factors impacting these costs and implementing effective strategies, companies can achieve cost savings.
Efficient management of these costs also supports competitive pricing, better quality products, and improved customer satisfaction.
Emphasizing collaboration, continuous improvement, and embracing technology can further enhance a company’s ability to manage expenses.
In summary, diligently managing material and processing costs benefits not just the company, but also its stakeholders, employees, and customers.
This commitment to efficiency and improvement is a hallmark of successful businesses in the ever-evolving market landscape.
資料ダウンロード
QCD管理受発注クラウド「newji」は、受発注部門で必要なQCD管理全てを備えた、現場特化型兼クラウド型の今世紀最高の受発注管理システムとなります。
ユーザー登録
受発注業務の効率化だけでなく、システムを導入することで、コスト削減や製品・資材のステータス可視化のほか、属人化していた受発注情報の共有化による内部不正防止や統制にも役立ちます。
NEWJI DX
製造業に特化したデジタルトランスフォーメーション(DX)の実現を目指す請負開発型のコンサルティングサービスです。AI、iPaaS、および先端の技術を駆使して、製造プロセスの効率化、業務効率化、チームワーク強化、コスト削減、品質向上を実現します。このサービスは、製造業の課題を深く理解し、それに対する最適なデジタルソリューションを提供することで、企業が持続的な成長とイノベーションを達成できるようサポートします。
製造業ニュース解説
製造業、主に購買・調達部門にお勤めの方々に向けた情報を配信しております。
新任の方やベテランの方、管理職を対象とした幅広いコンテンツをご用意しております。
お問い合わせ
コストダウンが利益に直結する術だと理解していても、なかなか前に進めることができない状況。そんな時は、newjiのコストダウン自動化機能で大きく利益貢献しよう!
(β版非公開)