- お役立ち記事
- Improvement measures that can be used in the purchasing department to shorten lead times and reduce inventory costs
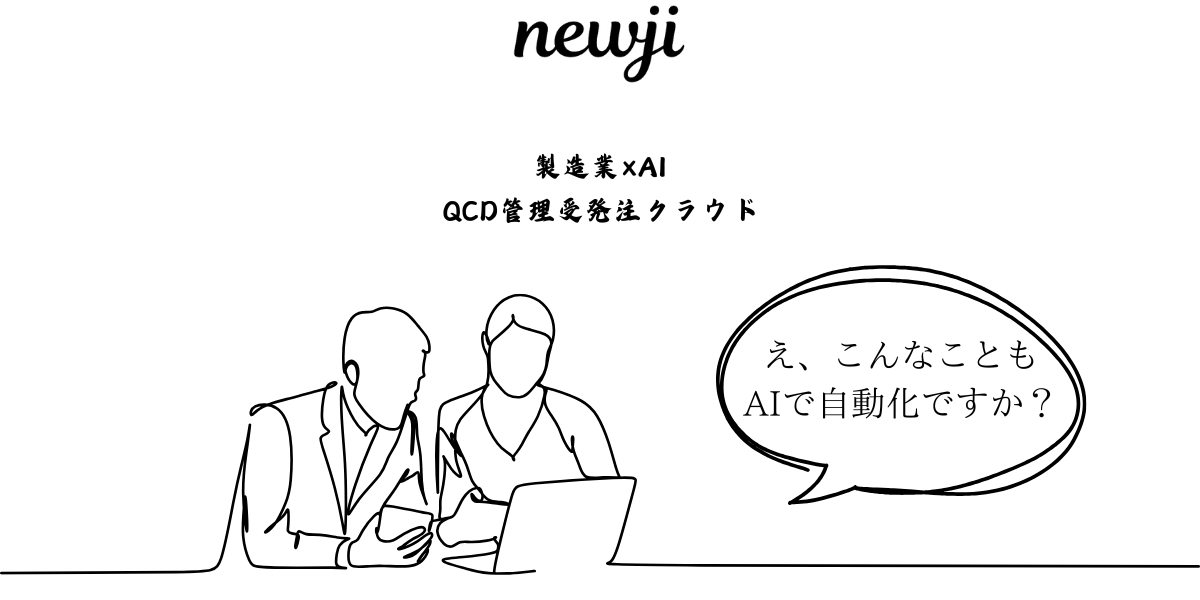
Improvement measures that can be used in the purchasing department to shorten lead times and reduce inventory costs
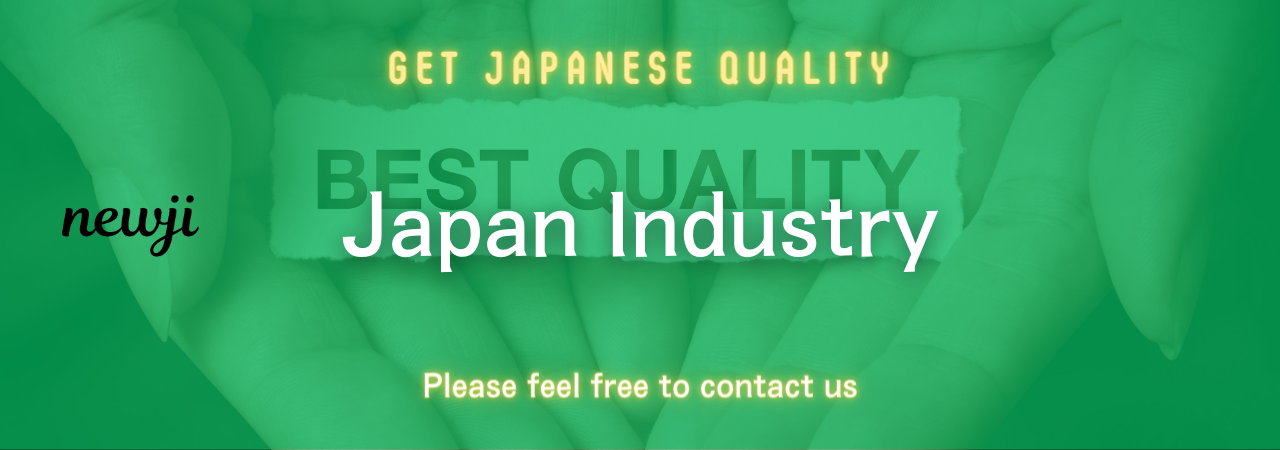
In today’s fast-paced business environment, companies are constantly looking for ways to improve efficiency and cut costs.
One area where significant improvements can be made is in the purchasing department.
By focusing on strategies to shorten lead times and reduce inventory costs, organizations can boost their bottom line and enhance overall productivity.
This article explores effective measures that can be implemented within the purchasing department to achieve these goals.
目次
Understanding Lead Times and Inventory Costs
Before implementing improvement measures, it’s crucial to understand what lead times and inventory costs entail.
Lead time refers to the period from when an order is placed until it is received and available for use.
It includes the time taken for processing an order, manufacturing, and transporting goods.
On the other hand, inventory costs include the expenses associated with storing and managing stock, such as warehousing, insurance, and depreciation.
The Importance of Reducing Lead Times
Reducing lead times is essential for several reasons.
Firstly, it allows companies to respond more swiftly to market demand, ensuring that products are available when customers need them.
Secondly, shorter lead times result in better customer service and satisfaction, as orders are fulfilled more promptly.
Lastly, reducing lead times can decrease the risk of stockouts and overstock situations, leading to more efficient inventory management.
The Impact of Lowering Inventory Costs
Lowering inventory costs are equally important in improving a company’s profitability.
High inventory costs can tie up capital that could otherwise be used for growth opportunities.
By reducing these expenses, businesses can free up resources for innovation, expansion, or other strategic initiatives.
Moreover, managing inventory costs effectively can lead to better cash flow and financial stability.
Strategies to Shorten Lead Times
Enhancing lead times involves a combination of process improvement, supplier collaboration, and technological advancements.
Let’s explore some actionable strategies to achieve quicker lead times.
Streamlining Internal Processes
One of the first steps in reducing lead times is to streamline internal processes.
Evaluate the current purchase order processing system to identify any bottlenecks or inefficiencies.
Implementing an automated purchase order system can significantly speed up the procedure by minimizing manual tasks and reducing the likelihood of human errors.
Additionally, adopting lean principles can optimize operations by eliminating waste and enhancing productivity.
For instance, revising approval workflows and reducing unnecessary documentation can expedite the purchasing process.
Enhancing Supplier Relationships
Building strong relationships with suppliers is crucial in reducing lead times.
Engage in open communication and regular meetings with suppliers to discuss expectations and any potential challenges.
Collaborate closely to develop mutually beneficial solutions that can speed up delivery times.
Furthermore, consider working with suppliers that are geographically closer or have a proven track record of quick turnaround times.
Negotiating favorable terms and establishing flexible delivery schedules can also play a significant role in achieving shorter lead times.
Leveraging Technology
Incorporating technology solutions can make a substantial difference in reducing lead times.
Implementing an integrated inventory management system can facilitate real-time tracking of orders, inventory levels, and supplier performance.
This visibility allows for proactive adjustments and quicker decision-making, ultimately leading to faster lead times.
Furthermore, businesses can benefit from utilizing advanced forecasting tools that help predict demand patterns accurately.
With better demand forecasting, purchasing departments can plan orders more effectively and avoid unnecessary delays.
Strategies to Reduce Inventory Costs
Reducing inventory costs requires a proactive approach and a focus on optimizing inventory management practices.
Here are some strategies to achieve cost-effective inventory control.
Implementing Just-in-Time Inventory
Just-in-Time (JIT) inventory is a method aimed at minimizing waste and reducing excess inventory by ensuring that materials are ordered only when needed.
This approach not only lowers storage costs but also minimizes the risk of obsolete or expired stock.
JIT can be particularly beneficial for companies dealing with fast-moving goods or perishable items.
Conducting Regular Inventory Audits
Conducting regular inventory audits is crucial for maintaining accurate stock levels and preventing discrepancies.
Identify slow-moving or obsolete items that can be eliminated to free up storage space and reduce holding costs.
Establishing a systematic review schedule and employing barcode or RFID technology can enhance inventory tracking accuracy.
Forecasting Demand Accurately
Accurate demand forecasting plays a pivotal role in optimizing inventory levels.
By analyzing historical data and market trends, businesses can predict future demand more precisely.
This knowledge enables the purchasing department to order the right quantity of products, avoiding both overstock and stockouts.
Centralizing Supplier Management
Centralizing supplier management involves consolidating supplier information and transaction history in one location.
This centralized approach enables better negotiation power with suppliers and provides insights into supplier performance.
By having a comprehensive view of suppliers’ capabilities and reliability, purchasing departments can make informed decisions that lead to cost savings.
In conclusion, improving lead times and reducing inventory costs are critical objectives for any purchasing department seeking to enhance business performance.
By implementing strategies such as streamlining internal processes, enhancing supplier relationships, leveraging technology, and optimizing inventory management, companies can achieve substantial benefits.
These improvements translate to increased efficiency, better customer satisfaction, and a healthier bottom line.
Continuously evaluating and refining these strategies will ensure that the purchasing department remains a valuable asset in driving organizational success.
資料ダウンロード
QCD調達購買管理クラウド「newji」は、調達購買部門で必要なQCD管理全てを備えた、現場特化型兼クラウド型の今世紀最高の購買管理システムとなります。
ユーザー登録
調達購買業務の効率化だけでなく、システムを導入することで、コスト削減や製品・資材のステータス可視化のほか、属人化していた購買情報の共有化による内部不正防止や統制にも役立ちます。
NEWJI DX
製造業に特化したデジタルトランスフォーメーション(DX)の実現を目指す請負開発型のコンサルティングサービスです。AI、iPaaS、および先端の技術を駆使して、製造プロセスの効率化、業務効率化、チームワーク強化、コスト削減、品質向上を実現します。このサービスは、製造業の課題を深く理解し、それに対する最適なデジタルソリューションを提供することで、企業が持続的な成長とイノベーションを達成できるようサポートします。
オンライン講座
製造業、主に購買・調達部門にお勤めの方々に向けた情報を配信しております。
新任の方やベテランの方、管理職を対象とした幅広いコンテンツをご用意しております。
お問い合わせ
コストダウンが利益に直結する術だと理解していても、なかなか前に進めることができない状況。そんな時は、newjiのコストダウン自動化機能で大きく利益貢献しよう!
(Β版非公開)